Streamline Your Logistics: How Pallet Wrappers Cut Costs and Boost Efficiency
Are rising labor costs and inconsistent load containment impacting your warehouse operations? Manual pallet wrapping, while traditional, often presents challenges in efficiency, material usage, and worker safety. Investing in an automated or semi-automated pallet wrapper can be a strategic move to significantly reduce costs and enhance your overall logistics process.
Let's explore how implementing a pallet wrapping machine can benefit your business:
The Challenges of Manual Pallet Wrapping
Before diving into the benefits of automation, it's helpful to understand the limitations of manual wrapping:
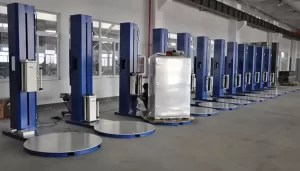
- Labor Intensity & Cost: Manual wrapping is physically demanding and time-consuming, directly impacting labor costs per pallet.
- Inconsistent Wrap Quality: Achieving consistent tension and overlap manually is difficult, potentially leading to unstable loads and product damage during transit.
- Material Waste: Without precise control, manual wrapping often uses more stretch film than necessary, increasing material costs.
- Safety Concerns: The repetitive bending, twisting, and walking backward involved in manual wrapping can lead to worker fatigue and increase the risk of musculoskeletal injuries.
Unpacking the Financial Benefits of Pallet Wrappers
Investing in a pallet wrapper offers tangible returns by addressing the inefficiencies of manual processes:
1. Significant Labor Cost Reduction
Automating or semi-automating the wrapping process drastically cuts down on the manual labor required per pallet. Operators can often manage the wrapping process alongside other tasks, optimizing workforce allocation and reducing direct labor expenses associated with wrapping.
2. Optimized Stretch Film Consumption
Modern pallet wrappers apply stretch film with consistent tension and pre-stretch capabilities (stretching the film before application). This ensures optimal load containment while using significantly less film compared to manual methods – often reducing film usage by 30-50% or more, leading to direct material savings.
3. Reduced Product Damage During Transit
Consistent and secure wrapping minimizes load shifting during handling and transportation. This translates to less product damage, fewer customer complaints, and reduced costs associated with returns or replacements.
Enhancing Operational Efficiency and Safety
Beyond direct cost savings, pallet wrappers improve workflow and create a safer working environment:
4. Increased Throughput
Pallet wrapping machines work quickly and consistently. A typical wrap cycle can often be completed in 60-90 seconds, significantly faster than manual wrapping. This speed helps products move out of the warehouse faster, improving overall operational velocity. Getting products shipped efficiently is crucial, and automated wrapping removes a common bottleneck.
5. Improved Load Containment & Stability
Machine wrapping provides uniform tension and placement, creating a more secure and stable load. This is critical for protecting goods, ensuring stackability, and meeting shipping requirements.
6. Enhanced Workplace Safety
Automating the wrapping process removes operators from the physically demanding and potentially hazardous task of circling a pallet with heavy film rolls. This reduces risks associated with back strain, trips, and falls. Many machines incorporate safety features like shielded moving parts to further protect operators. Safety is paramount, and transitioning away from manual wrapping significantly mitigates injury risks.
Choosing the Right Pallet Wrapper for Your Needs
Selecting the appropriate machine depends on your specific operational requirements:
- Volume: How many pallets do you wrap per day or hour?
- Load Types: Are your loads uniform or variable in size and weight? Are they stable or unstable?
- Automation Level: Do you need a fully automated system integrated into a conveyor line, or is a machine requiring operator initiation suitable?
- Budget and Space: Consider the initial investment, ongoing maintenance, and the physical footprint of the machine.
Options generally include:
- Semi-automatic stretch wrappers: Require an operator to attach the film tail, start the cycle, and cut the film at the end. Ideal for low-to-medium volume operations.
- Automatic stretch wrap machine systems: Handle the entire process automatically, often integrated with conveyors for high-volume environments. (Note: The linked example is a horizontal wrapper, typically used for long items, while standard pallet wrappers are vertical).
Conclusion: A Strategic Investment for Growth
In conclusion, integrating a pallet wrapper into your operations offers a clear path to reduced expenses, heightened efficiency, improved load security, and a safer work environment. By optimizing labor, materials, and processes, these machines provide a strong return on investment for businesses looking to streamline their end-of-line packaging and stay competitive in today's demanding logistics landscape. Analyzing your specific needs will help determine the best type of pallet wrapper to unlock these significant benefits for your business.