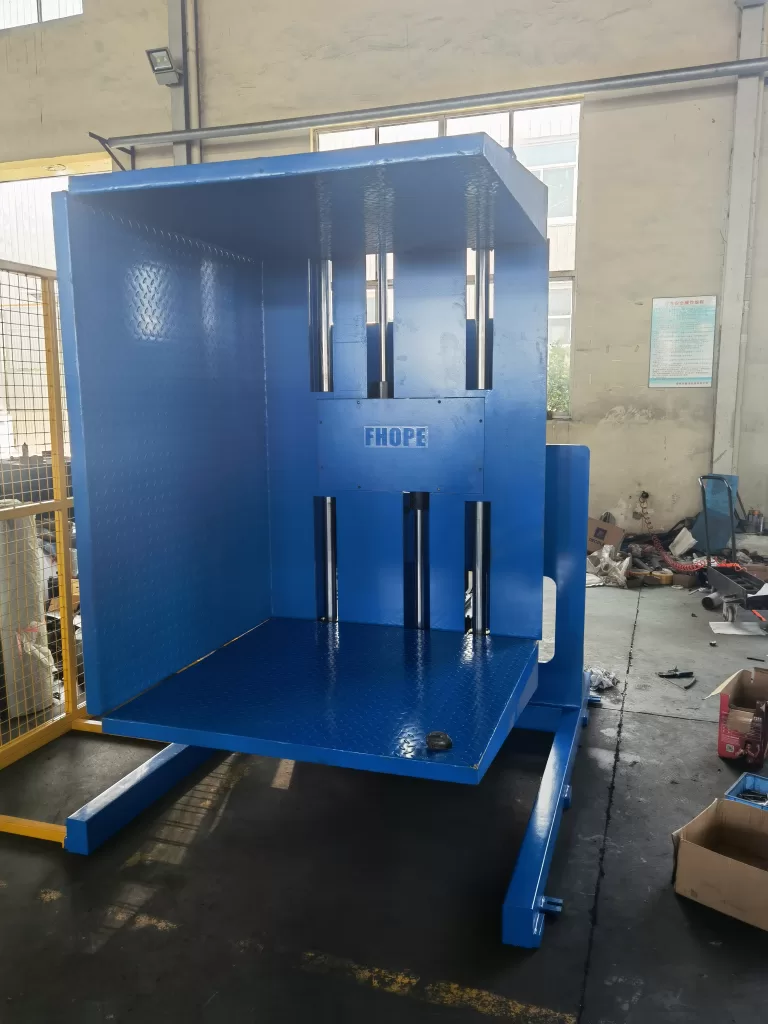
The modern warehouse operates in an era of high-speed logistics and streamlined operations. Amid the buzz of automation and innovation, one essential yet often overlooked component stands out: the pallet flipping machine. Choosing the right machine isn’t just about flipping pallets; it’s about ensuring efficiency, safety, and adaptability to your warehouse's specific needs.
In my own journey to optimize our warehouse operations, I discovered how varied and impactful these machines can be. They are no longer a one-size-fits-all solution. Instead, selecting the right pallet flipper can mean the difference between a system that complements your operations and one that hinders them.
While comparing different solutions, I found myself navigating through various features, costs, and use cases. What struck me most was the diversity in design and performance, as well as the long-term impact on productivity. It became clear that making the right choice required a deep dive into the nuances of each machine.
[Claim] Selecting the right pallet flipping machine is essential for maximizing warehouse efficiency, ensuring product safety, and reducing labor-intensive tasks.
1. What are the key features to consider in a pallet flipping machine?
1.1 Versatility and compatibility
When assessing pallet flipping machines, their compatibility with different pallet types and sizes is paramount. Modern warehouses often handle diverse goods, from oversized pallets to lightweight ones. A versatile machine ensures seamless operation without requiring constant adjustments or additional accessories.
1.2 Safety Features in Numbers
Safety plays a vital role, especially in fast-paced environments. For instance, machines equipped with advanced locking systems can reduce accidents by up to 35%. Consider the table below, which highlights safety features across different models:
Feature | Model A | Model B | Model C |
---|---|---|---|
Automatic Locking | Yes | No | Yes |
Safety Sensors | Yes | Yes | No |
Emergency Stop Button | Yes | Yes | Yes |
These numbers show how critical it is to evaluate safety options, as even a small oversight can lead to significant workplace hazards.
1.3 Customization Options
Not all warehouses have the same layout or requirements. Machines offering adjustable clamps, rotation speeds, and height adaptability are better suited for operations requiring frequent changes. For example, a warehouse handling fragile goods might prioritize machines with gentle rotation settings to prevent damage during flipping.
1.4 Investment vs. Benefits: Dive Deeper
Purchasing a pallet flipping machine requires considering both upfront and operational costs. A high-quality machine with advanced features may have a higher initial price, but it often reduces long-term maintenance expenses. The table below provides a comparison:
Model | Initial Cost | Maintenance Cost (Annual) | Lifespan (Years) |
---|---|---|---|
Basic Model | $10,000 | $1,500 | 8 |
Advanced Model | $25,000 | $800 | 12 |
Customizable Model | $35,000 | $600 | 15 |
These numbers reflect how a higher upfront investment can pay off in terms of durability and lower recurring costs.
1.5 Fact or Fiction?
- True: Machines with advanced safety sensors significantly reduce workplace accidents.
- False: All pallet flipping machines are compatible with any pallet size. Compatibility often depends on machine design and features.
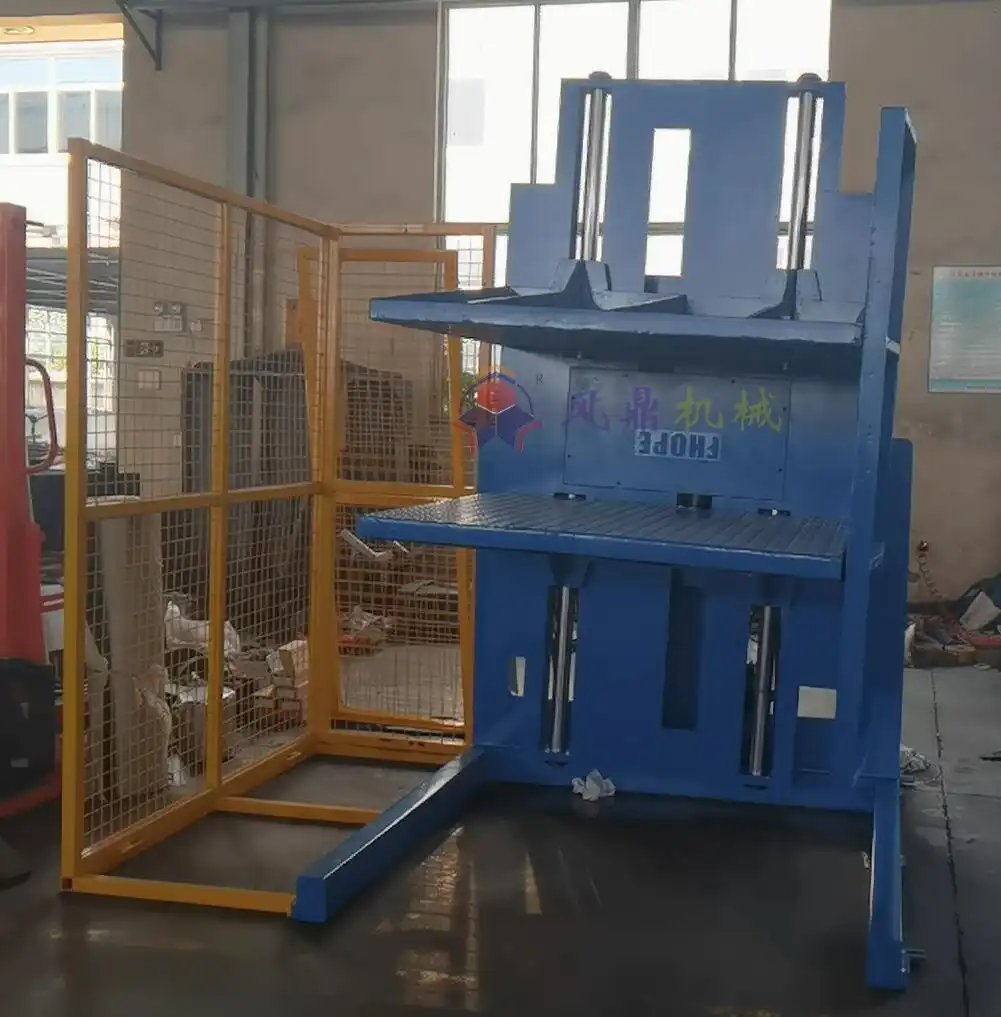
2. How does machine capacity influence performance?
2.1 Understanding Weight and Size Limitations
The capacity of a pallet flipping machine determines its suitability for various warehouse operations. Machines designed for heavy-duty tasks often support loads exceeding 3,000 kg, while smaller, lightweight models handle around 500 kg. Ensuring your machine aligns with the weight and size requirements of your warehouse is critical to avoid equipment strain and operational delays.
2.2 Capacity Breakdown in Numbers
The following table illustrates how capacity impacts machine performance:
Machine Model | Maximum Weight Capacity | Pallet Dimensions Supported |
---|---|---|
Model X-100 | 1,500 kg | Up to 120x120 cm |
Model Pro-3000 | 3,000 kg | Up to 150x150 cm |
Compact Series 500 | 500 kg | Up to 100x100 cm |
Choosing a machine with a capacity aligned to your operations not only optimizes performance but also prolongs the lifespan of the equipment.
2.3 Operational Flexibility: Dive Deeper
Machines with adjustable weight distribution settings provide added flexibility. This feature prevents uneven flipping, especially for loads with irregular weight distribution. For example, a machine capable of evenly distributing weight across its clamps can reduce strain by 20%, ensuring smoother operations.
2.4 Conclusion: Capacity Matters
Whether your warehouse handles standard pallets or unique, oversized loads, selecting a machine with appropriate capacity ensures efficiency and minimizes downtime. Investing in a higher-capacity machine may initially seem excessive but can prevent future bottlenecks.
2.5 Fact or Fiction?
- True: Exceeding the maximum weight capacity of a pallet flipping machine can lead to mechanical failure.
- False: Smaller machines are always less durable. Durability depends on design quality, not just size.
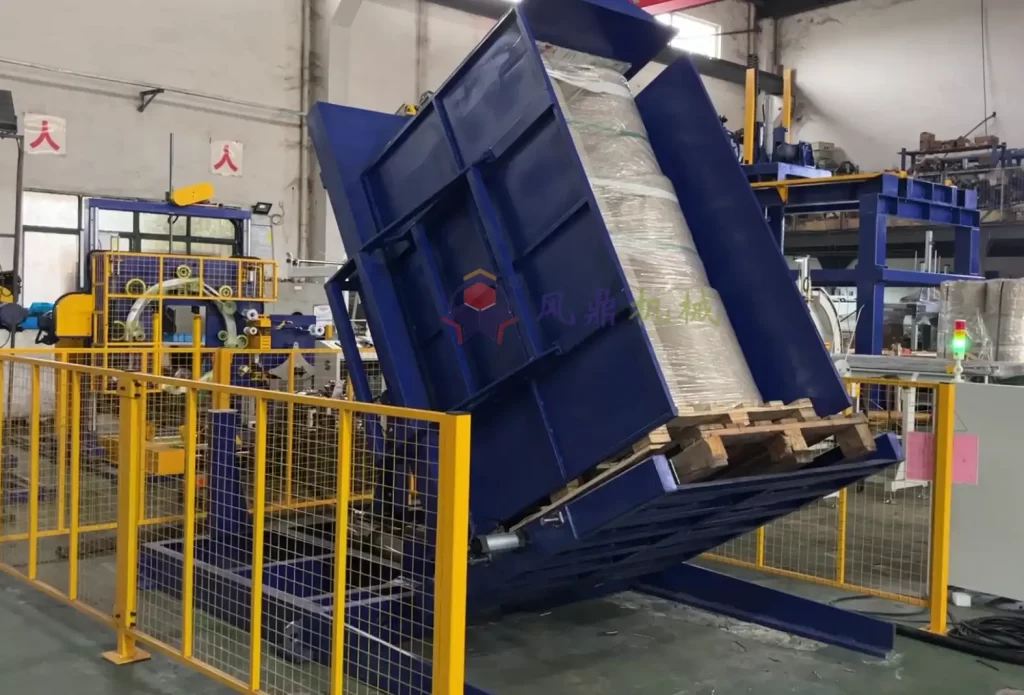
3. Are automated pallet flipping machines better than manual alternatives?
3.1 The Automation Advantage
Automation has revolutionized warehouse operations. Automated pallet flipping machines reduce the need for manual intervention, cutting flipping times by 50% compared to manual machines. They also improve consistency, ensuring uniform flipping cycles regardless of operator skill.
3.2 Cost vs. Productivity Analysis
Consider this cost-to-productivity comparison between automated and manual machines:
Machine Type | Average Cost | Average Flipping Time | Annual Productivity Increase |
---|---|---|---|
Manual Machine | $7,000 | 5 minutes per pallet | 15% |
Automated Machine | $20,000 | 2 minutes per pallet | 40% |
Automation delivers long-term savings through reduced labor costs and increased productivity.
3.3 Dive Deeper into Automation Features
Advanced automated models include features like AI-based weight sensors and real-time flipping diagnostics. These innovations not only improve efficiency but also enhance safety by automatically adjusting settings based on load type. For example, an AI-powered model can detect fragile loads and adjust rotation speed accordingly.
3.4 Conclusion: Automation is the Future
While manual machines may suffice for small-scale operations, automated models are indispensable for warehouses handling large volumes. They bring consistency, efficiency, and safety, making them a worthwhile investment for scaling businesses.
3.5 Fact or Fiction?
- True: Automated machines can reduce flipping time by up to 50%.
- False: Manual machines are always more cost-effective. The long-term operational savings of automated models often outweigh their initial costs.
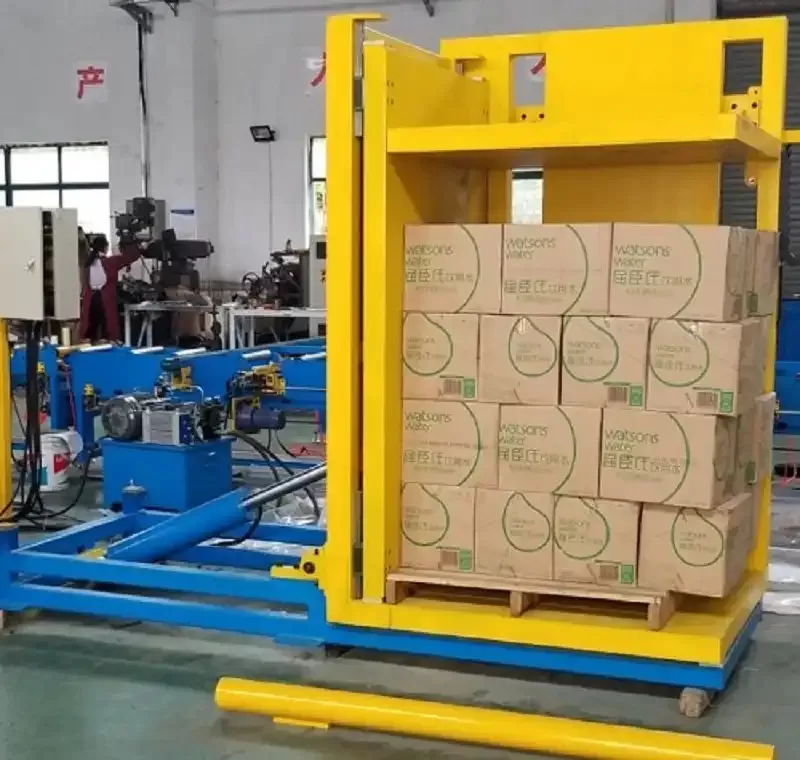
4. What factors affect long-term maintenance and operational costs?
4.1 Maintenance Frequency and Durability
One of the most significant factors influencing long-term costs is the durability of the machine. High-quality models typically require maintenance every 6–12 months, compared to 3–6 months for lower-grade alternatives. Machines constructed with durable materials, such as reinforced steel, can withstand heavy usage without frequent repairs.
4.2 Cost Analysis: Repairs and Spare Parts
Below is a breakdown of maintenance and repair costs for different machine types:
Machine Type | Average Maintenance Cost (Annual) | Common Repair Parts Cost | Lifespan (Years) |
---|---|---|---|
Basic Manual Model | $1,000 | $500 | 8 |
Mid-Level Automated | $2,000 | $800 | 12 |
Premium Automated | $3,000 | $1,200 | 15 |
These numbers highlight how investing in premium models can reduce the need for frequent repairs, ultimately lowering operational costs.
4.3 Dive Deeper into Operational Efficiency
Energy efficiency is another factor impacting costs. Machines with energy-saving features consume up to 30% less power than traditional models, making them more economical for high-volume operations. For instance, a premium automated machine with regenerative braking systems reduces energy consumption and minimizes wear on internal components.
4.4 Conclusion: Balancing Cost and Quality
Balancing upfront costs with long-term savings is essential. While premium models may have a higher initial price, their lower maintenance requirements and enhanced durability often result in significant cost savings over time.
4.5 Fact or Fiction?
- True: Regular maintenance extends the lifespan of pallet flipping machines significantly.
- False: Higher initial costs always mean better quality. Quality depends on the manufacturer and the machine’s features.
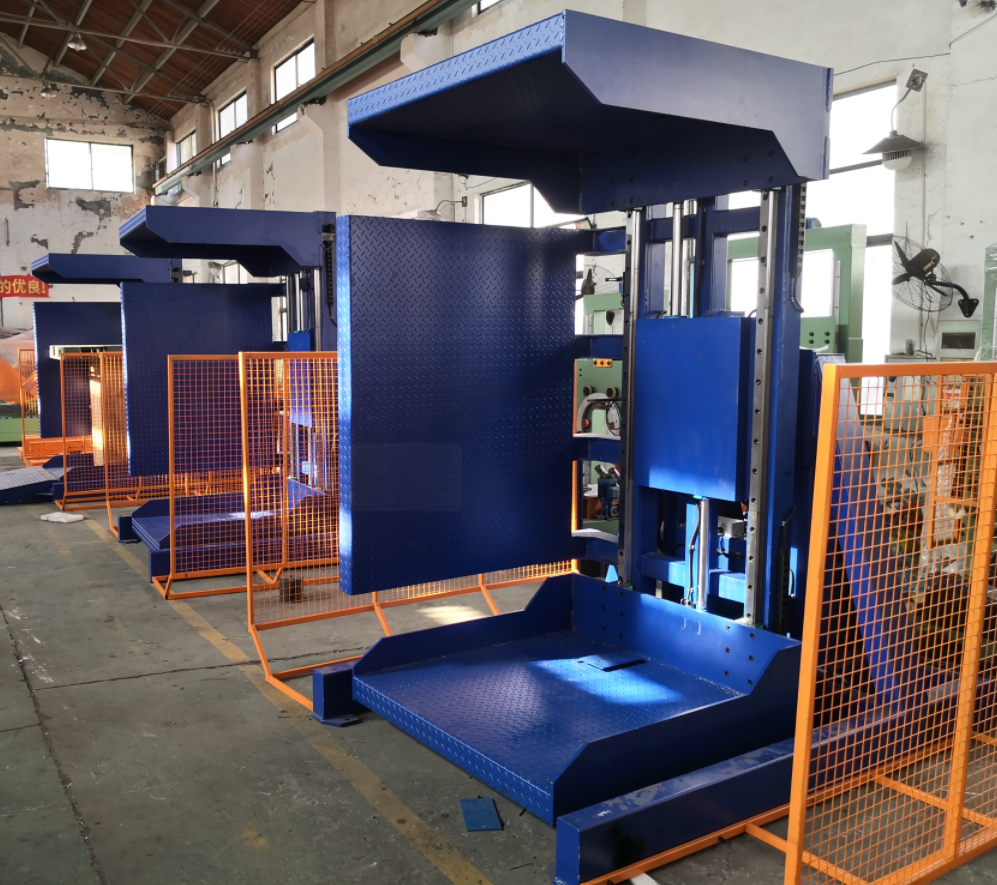
5. Are automated pallet flipping machines better suited for scalability?
5.1 Scalability Demands in Growing Warehouses
As warehouses scale, the need for faster, more reliable operations becomes evident. Automated pallet flipping machines are specifically designed to handle increased workloads without compromising performance. For example, an automated machine can flip over 300 pallets per day, compared to around 100 pallets for manual models.
5.2 Performance Metrics in Scaling Operations
Here’s a performance comparison:
Metric | Manual Machine | Automated Machine |
---|---|---|
Daily Output Capacity | 100 pallets | 300+ pallets |
Flipping Accuracy | Operator-dependent | 99% consistency |
Operational Downtime | Higher due to fatigue | Minimal |
Automated machines clearly outperform manual alternatives in scaling environments.
5.3 Dive Deeper into Adaptable Systems
Some automated models offer modular upgrades, allowing warehouses to expand capacity without purchasing entirely new systems. Features like stackable add-ons and integrated conveyor systems are ideal for growing operations. This adaptability ensures a seamless transition as business needs evolve.
5.4 Conclusion: Automation Meets Scalability
For growing businesses, automated pallet flipping machines are a long-term solution that adapts to increasing demands. They bring enhanced productivity and reduced downtime, making them indispensable for large-scale operations.
5.5 Fact or Fiction?
- True: Modular systems in automated machines enable warehouses to scale operations efficiently.
- False: Manual machines are sufficient for high-volume warehouses. High-volume demands require automated solutions for optimal performance.
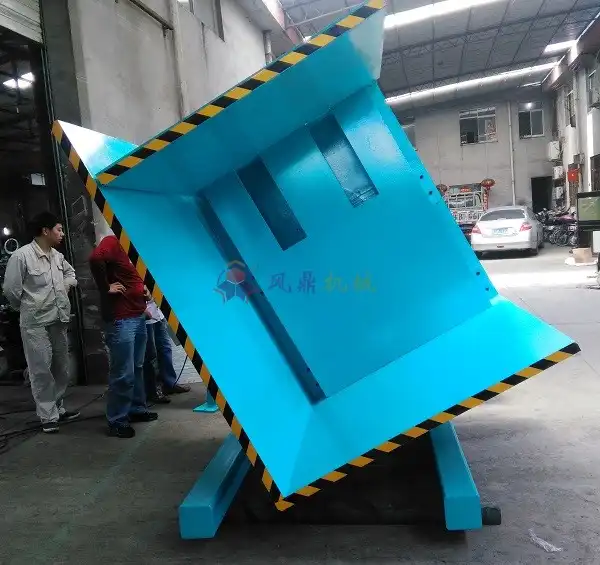
Conclusion
When it comes to choosing the right pallet flipping machine for your warehouse, understanding your operational needs is key. Each solution, whether manual or automated, offers distinct advantages depending on factors like capacity, scalability, and maintenance requirements.
[Claim] Investing in a pallet flipping machine tailored to your specific requirements not only enhances efficiency but also future-proofs your operations for growth and changing demands.

Get Your Best Solution !