Orbital Stretch Wrapper: Identifying Packaging Needs for Improved Efficiency
- Orbital Stretch Wrapper: Identifying Packaging Needs for Improved Efficiency
- 1. What is an Orbital Stretch Wrapper?
- 2. Key Features to Consider When Choosing an Orbital Stretch Wrapper
- 3. Matching Your Packaging Needs with the Right Orbital Stretch Wrapper
- 4. How Orbital Stretch Wrappers Improve Efficiency
- 5. Industries That Benefit Most from Orbital Stretch Wrappers
- 6. Innovative Technologies in Orbital Stretch Wrappers
- 7. Maintenance and Durability: Maximizing Your ROI
- 8. Conclusion
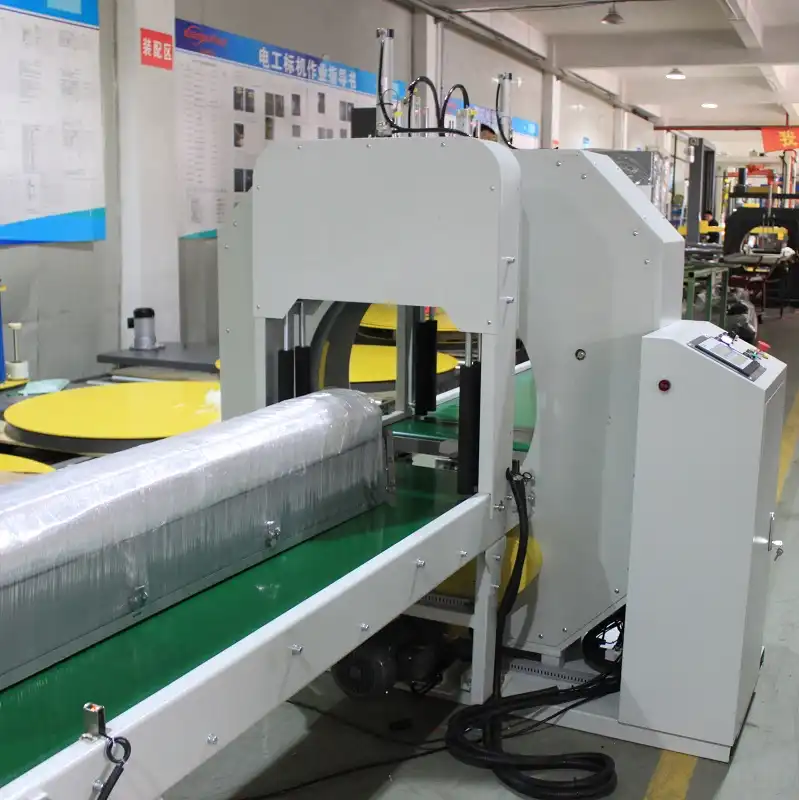
The packaging process is a crucial aspect of manufacturing and logistics, directly impacting efficiency, product protection, and overall operational costs. As companies aim to optimize their production lines, the orbital stretch wrapper has emerged as a valuable solution for improving packaging processes, particularly for products that are long, bulky, or oddly shaped. Identifying your packaging needs is essential when considering this advanced technology to maximize your investment. In this article, we will explore the key features of orbital stretch wrappers, how to match them with specific packaging needs, and how they can significantly enhance efficiency across industries.
1. What is an Orbital Stretch Wrapper?
An orbital stretch wrapper is a specialized machine designed to wrap products by rotating them through a circular, or orbital, motion. This packaging solution is widely used for items that are not easily packaged using traditional methods, such as long pipes, profiles, boards, and irregularly shaped goods. The orbital motion ensures that every part of the product is securely wrapped in stretch film, providing protection from dust, moisture, and physical damage during storage or transportation.
Unlike conventional stretch wrapping machines that wrap around stationary pallets, orbital stretch wrappers move the wrapping material around the product while it remains stationary. This feature allows for a more versatile and adaptable wrapping solution for uniquely shaped goods.
2. Key Features to Consider When Choosing an Orbital Stretch Wrapper
Before investing in an orbital stretch wrapper, it is important to understand the key features that can impact your packaging process. Each model comes with its own set of specifications, and aligning these with your specific needs will ensure you make the right choice. Here are some essential features to consider:
2.1 Wrapper Diameter
The diameter of the orbital wrapper plays a critical role in determining what size of product it can handle. Machines are available in various sizes, with wrapper diameters ranging from small to large. It is important to measure the largest product you need to wrap and choose a machine with a wrapper diameter that can comfortably accommodate it.
2.2 Wrapping Speed
The speed at which the machine wraps your product will significantly affect your overall packaging efficiency. Higher wrapping speeds are particularly beneficial for high-volume production lines where time savings directly contribute to greater productivity. Adjustable speed settings also offer flexibility, allowing operators to slow down the wrapping process for more delicate or irregularly shaped items.
2.3 Film Roll Capacity
The size and capacity of the stretch film roll that the machine can handle determine how frequently the film will need to be replaced. Larger film rolls mean less frequent changes, contributing to continuous operation and improved efficiency.
2.4 Tension Control
Different products require varying levels of tension during the wrapping process to avoid damage or shifting. Adjustable tension control is a vital feature that allows you to fine-tune the amount of force applied to the stretch film, ensuring the right balance between securing the load and protecting the product from unnecessary pressure.
2.5 Automation Level
Orbital stretch wrappers come in manual, semi-automatic, and fully automatic versions. The automation level you choose will depend on your operational needs, budget, and the volume of products you need to wrap. Fully automated machines offer the greatest efficiency, requiring minimal operator involvement, while semi-automatic machines provide a more affordable option for lower-volume operations.
3. Matching Your Packaging Needs with the Right Orbital Stretch Wrapper
Choosing the right orbital stretch wrapper involves a careful assessment of your packaging requirements. Not every business needs a fully automated, high-speed machine, while others might require one that can handle high output volumes. Here are some factors to consider when matching your packaging needs with the appropriate machine:
3.1 Product Size and Shape
One of the primary considerations is the size and shape of the products you need to package. Orbital stretch wrappers are particularly effective for long or irregularly shaped products such as aluminum profiles, pipes, or wooden planks. For companies that frequently deal with these types of items, a machine with a larger diameter and customizable tension control will be beneficial.
3.2 Production Volume
The volume of products that need to be wrapped each day will dictate the speed and level of automation required. High-volume operations, such as manufacturing plants, will benefit from fully automated models with fast wrapping speeds and large film roll capacities. On the other hand, smaller businesses with lower production volumes may find semi-automatic or manual models more cost-effective.
3.3 Protection Requirements
If your products are sensitive to dust, moisture, or damage, it is important to choose a machine with adjustable tension control and a reliable wrapping method. The stretch film should be tightly applied without compromising the integrity of the product. For fragile items, slower wrapping speeds and more control over the wrapping process can help prevent damage.

Get Your Best Solution !
4. How Orbital Stretch Wrappers Improve Efficiency
One of the primary reasons companies invest in orbital stretch wrappers is to enhance efficiency in their packaging lines. The automated or semi-automated nature of these machines offers a number of advantages over manual wrapping processes, including:
4.1 Speed and Consistency
Manual wrapping can be time-consuming and inconsistent, leading to variations in the quality of the packaging. An orbital stretch wrapper eliminates these issues by providing a consistent, high-speed wrapping solution. This is particularly beneficial for large production lines that require the same level of packaging for every product.
4.2 Labor Savings
By automating the wrapping process, businesses can significantly reduce the amount of labor required for packaging tasks. This not only reduces labor costs but also minimizes the risk of injuries that often occur with manual wrapping methods, such as repetitive strain injuries.
4.3 Material Savings
The precision of an orbital stretch wrapper ensures that only the necessary amount of film is used for each product, reducing waste and cutting down on material costs over time.
4.4 Enhanced Product Protection
Consistency in wrapping tension and coverage ensures that each product is securely packaged, reducing the likelihood of damage during handling, shipping, or storage. This can help prevent costly returns and improve customer satisfaction.
5. Industries That Benefit Most from Orbital Stretch Wrappers
The versatility of orbital stretch wrappers makes them a valuable asset across various industries. Some of the key industries that benefit the most from this technology include:
5.1 Construction Materials
Companies that deal with long and heavy materials like pipes, tubes, and beams require a wrapping solution that can handle irregular shapes. Orbital stretch wrappers are ideal for protecting these materials during transportation and storage.
5.2 Wood and Furniture Industry
Furniture, planks, and other wooden products need secure packaging to protect them from scratches and dents. The customizable wrapping options of an orbital stretch wrapper ensure that these delicate products are handled with care.
5.3 Metal and Aluminum Products
Metal and aluminum profiles can be challenging to package due to their length and weight. Orbital stretch wrappers provide a reliable method for securing these products, ensuring they remain free from damage.
6. Innovative Technologies in Orbital Stretch Wrappers
With advancements in technology, modern orbital stretch wrappers come equipped with a range of innovative features designed to improve packaging efficiency. These include:
6.1 Programmable Logic Controllers (PLC)
Many high-end orbital stretch wrappers are equipped with PLC systems, allowing operators to program the machine for specific product types, adjust speed and tension settings, and monitor the wrapping process for increased precision.
6.2 Remote Monitoring
Remote monitoring capabilities allow companies to track the performance of their machines in real-time. This helps in identifying any issues before they cause downtime and ensures that the machine is operating at peak efficiency.
6.3 Energy Efficiency
Newer models of orbital stretch wrappers are designed to be energy-efficient, reducing power consumption and lowering operational costs while maintaining high performance.
7. Maintenance and Durability: Maximizing Your ROI
Investing in an orbital stretch wrapper is a long-term decision, and ensuring its proper maintenance is essential for maximizing your return on investment. Regular maintenance and proper care of the machine will not only prolong its lifespan but also ensure consistent performance.
7.1 Routine Checks
Conducting routine checks on components such as the wrapping ring, film carriage, and drive system can help identify wear and tear before it leads to more serious issues. Regular lubrication and cleaning will ensure the machine continues to operate smoothly.
7.2 Training for Operators
Proper training for machine operators is essential to ensure that they understand how to use the machine correctly. This will minimize the risk of user errors that could lead to damage or reduced efficiency.
7.3 OEM Parts and Service Contracts
Working with the original equipment manufacturer (OEM) for replacement parts and service contracts ensures that your machine remains in top condition and that repairs are handled by professionals who are familiar with the equipment.
8. Conclusion
The orbital stretch wrapper is a powerful tool for businesses looking to improve their packaging efficiency and protect their products during transport and storage. By carefully assessing your packaging needs and matching them with the right features, you can make an informed investment that delivers significant returns in terms of time savings, labor reductions, and enhanced product protection. With technological advancements, these machines are becoming even more versatile and efficient, making them an essential addition to modern production lines across various industries.
Incorporating an orbital stretch wrapper into your operations is not just about speed and convenience – it’s about safeguarding your products, reducing waste, and maximizing profitability in the long term. By choosing the right machine and maintaining it properly, you can ensure your investment pays off for years to come.

Get Your Best Solution !