Optimizing Wood Product Packaging with Orbital Stretch Wrappers
Protecting wooden materials and products during storage and transit presents unique challenges. Wood is susceptible to moisture absorption, scratches, dust accumulation, and physical damage. Effectively securing diverse shapes and sizes, from long lumber and panels to assembled furniture, requires a specialized approach. Orbital stretch wrappers provide an efficient and reliable solution tailored specifically for the wood industry.
This automated packaging technology utilizes a rotating ring mechanism to encircle wooden items with stretch film, creating a tight, protective layer. This method ensures consistent, comprehensive coverage crucial for maintaining product integrity from the factory to the final destination.
How Orbital Stretch Wrapping Works for Wood Products
Unlike traditional turntable wrappers, orbital wrappers pass a ring carrying the stretch film around the stationary product or allow the product to pass through the rotating ring. This process is particularly advantageous for long or irregularly shaped wooden items:
- Product Infeed: Wooden items are conveyed into the wrapping zone.
- Film Application: A rotating ring dispenses the stretch film, orbiting around the product.
- Consistent Overlap: The machine ensures precise film overlap, creating a secure and sealed wrap.
- Cutting and Sealing: Once wrapping is complete, the film is automatically cut and secured.
- Product Outfeed: The fully wrapped product is conveyed out, ready for storage or shipping.
This mechanism provides 360-degree protection quickly and efficiently.
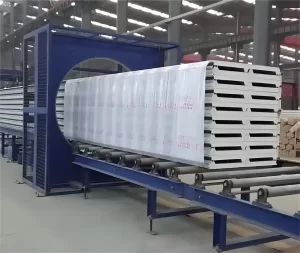
Key Benefits of Using Orbital Stretch Wrappers for Wood
Implementing orbital stretch wrapping offers significant advantages for businesses handling wooden goods:
- Enhanced Protection: Creates a robust barrier against moisture, dust, dirt, and surface damage like scratches or dents.
- Improved Load Stability: Tightly wraps individual pieces or bundles, preventing shifting during transport and reducing the risk of damage.
- Increased Efficiency: Automates the wrapping process, significantly faster than manual methods, boosting throughput.
- Material Savings: Optimized film usage with adjustable tension and overlap controls reduces waste compared to less precise methods.
- Versatility: Capable of handling a wide range of wood product dimensions, from narrow planks to wide panels and bulky furniture.
- Reduced Labor Costs: Automation minimizes the need for manual labor in the wrapping process.
Typical Technical Specifications
While specific configurations vary, typical parameters for an automatic orbital stretch wrapper suitable for wood products include:
- Machine Type: Automatic Orbital Stretch Wrapper
- Applicable Product Height: Up to 1000mm (Variable based on model)
- Maximum Load Weight: Typically around 1000kg (Can be customized)
- Compatible Film Types: PE, PVC, LLDPE stretch film
- Film Roll Dimensions:
- Outer Diameter: e.g., 300mm
- Inner Diameter: e.g., 76mm (Standard core)
- Width: e.g., 500mm (Adaptable)
- Power Requirements: Often 220V, 50Hz, single phase (Confirm based on region/model)
- Approximate Machine Weight: ~800kg (Varies significantly)
- Operational Speed: Up to 20 cycles per minute (Dependent on product size and wrap settings)
- Control System: PLC (Programmable Logic Controller) with HMI (Human-Machine Interface) and variable frequency drive for speed control.
- Wrapping Efficiency: Features like adjustable film overlap and tension control optimize material use.
- Safety: Includes safety shields, interlocks, and emergency stop functionalities.
- Maintenance: Designed for accessible routine maintenance.
Note: The parameters listed above are illustrative. For exact specifications matching your application needs, direct consultation is recommended. info@fhopepack.com
Common Applications in the Wood Industry
Orbital stretch wrappers are invaluable across various sectors dealing with wood:

1. Furniture Manufacturing
Protecting finished items like tables, chairs, and cabinetry is paramount. Orbital wrappers envelop furniture of diverse shapes, shielding wooden surfaces from scratches, dust, and moisture during handling and shipping, ensuring products arrive in showroom condition. This minimizes returns and upholds brand quality perception.
2. Building Materials Supply
Suppliers of lumber, beams, panels, and flooring benefit greatly. The wrapper accommodates long and bulky items (e.g., up to 1000mm height or more), securing them tightly. This prevents moisture absorption, contamination, and physical damage during transit, preserving material quality for construction use and ensuring load stability.
3. Wooden Craft and Décor Production
Items with intricate designs or delicate finishes require careful handling. Orbital wrappers offer adjustable film tension, providing a secure wrap without damaging ornate details. This maintains the aesthetic appeal and structural integrity of valuable craft items, enhancing marketability.
Choosing the Right Orbital Wrapper
Selecting the appropriate machine involves considering:
- Product Dimensions: Maximum and minimum length, width, and height of items to be wrapped.
- Product Weight: Ensure the machine's load capacity is sufficient.
- Throughput Needs: Required wrapping speed (cycles per minute or products per hour).
- Level of Automation: Options range from semi-automatic to fully integrated lines.
- Film Specifications: Compatibility with desired film types and thicknesses.
Conclusion
Orbital stretch wrappers represent a significant advancement in protective packaging for the wood industry. By providing efficient, consistent, and versatile wrapping, they help preserve the quality and integrity of wooden products, from raw materials to finished goods. Implementing this technology can lead to reduced damage, lower costs, and improved operational efficiency.
For detailed specifications or consultation on the best orbital wrapping solution for your wooden products, please reach out: info@fhopepack.com