Understanding Orbital Stretch Wrappers for Efficient Panel and Profile Packaging
Wrapping long, unwieldy items like metal panels, extrusions, lumber, or pipes presents unique packaging challenges compared to standard palletized goods. For fabricators and manufacturers dealing with these types of products, ensuring load stability and protection during handling and transport is critical. Orbital stretch wrappers offer an effective and efficient method specifically designed for these applications.
What is an Orbital Stretch Wrapper?
Unlike traditional turntable wrappers where the load rotates on a platform, an orbital stretch wrapper (also commonly referred to as a horizontal wrapper) typically keeps the load stationary or moves it linearly on a conveyor. The key feature is a rotating ring or eyelet through which the product passes. This ring carries the roll of stretch film, applying it circumferentially as the product moves through the wrapping zone.
The Wrapping Process for Panels and Profiles
The operation of an orbital wrapper for items like panels and profiles generally follows these steps:
- Infeed: The panel, profile bundle, or other long product is placed onto the infeed conveyor system, either manually or automatically.
- Conveyance: The conveyor moves the product horizontally towards and through the wrapping ring.
- Wrapping: As the product passes through the ring's opening, the ring rotates around the product, dispensing the stretch film and wrapping it securely. The conveyor speed and ring speed are synchronized to ensure consistent overlap and film coverage.
- Film Application: The film carriage mechanism on the ring maintains consistent tension on the stretch film, ensuring a tight, stable wrap that conforms to the product's shape.
- Outfeed: Once the entire length of the product has passed through the ring and is wrapped, it moves onto the outfeed conveyor for removal or further processing. Automatic systems often include film clamping, cutting, and wiping mechanisms for a fully automated cycle.
panel shrink packing machine Key Advantages for Long and Bulky Loads
Orbital wrappers provide distinct benefits when packaging panels, profiles, and similar items:
- Handling Long and Awkward Loads: Because the product moves linearly through the machine, there's theoretically no limit to the length of the product that can be wrapped (unlike the diagonal limitations of a turntable). This makes them ideal for extrusions, pipes, lumber, and long panels.
- Consistent Load Containment: The wrapping action applies film evenly along the entire length, providing uniform containment and protection against shifting, scratches, and environmental factors like dust or moisture.
- Versatility for Various Shapes: They can effectively wrap bundles or individual items with regular or somewhat irregular cross-sections, securing them tightly.
See an Orbital Stretch Wrapper in Action:
Critical Consideration: Film Roll Mounting Options
The method used to supply stretch film to the wrapping ring significantly impacts machine design and operation, particularly concerning the size of the film roll that can be used:
Option 1: Film Roll Rotates Through the Ring Center
- Mechanism: In some designs, the entire roll of stretch film is mounted directly onto the rotating ring assembly.
- Limitation: This method requires the film roll itself to pass through the machine's ring or 'coil' center along with the product. Consequently, the maximum outer diameter of the film roll is limited by the minimum inner diameter (ID) of the ring.
- Example: If a machine's ring has a minimum ID of 340mm, the usable film roll diameter might be restricted to around 200mm or less, accounting for necessary clearances.
- Implication: Smaller film rolls deplete faster, potentially leading to more frequent roll changes and increased machine downtime, which can impact overall throughput.
Option 2: Film Roll Mounted on an External Supporter/Stand
- Mechanism: This configuration places the film roll on a separate, often stationary or articulating, stand or supporter. The film is then fed to the rotating ring assembly rather than being carried on it.
- Advantage: This design effectively removes the limitation on the film roll's outer diameter imposed by the ring's ID.
- Capability: Larger diameter film rolls (e.g., 250mm, 400mm, or even larger industrial sizes) can be readily used.
- Implication: Utilizing larger rolls significantly extends the operating time between film changes, thereby reducing downtime and improving overall operational efficiency, especially in higher volume settings.
Understanding this difference is crucial when selecting a machine, as it directly affects material replenishment frequency and line productivity.
Operational Parameters and Customization
Modern orbital stretch wrappers often allow for adjustments to optimize the wrap for specific products and requirements:
- Film Tension: Controls how tightly the film is applied.
- Ring Speed: Affects the wrapping speed and throughput.
- Conveyor Speed: Works in conjunction with ring speed to determine film overlap.
- Film Overlap: Adjustable percentage to ensure complete coverage and desired containment force.
Beyond basic wrapping, systems can be customized or integrated with features like:
- Top sheet applicators for added protection against dust and moisture.
- Automatic corner protection applicators.
- Integrated weighing systems.
- Bundling capabilities before wrapping.
Orbital vs. Turntable Wrappers: Key Distinction
While turntable wrappers are the standard for palletized loads that can be rotated, orbital wrappers are the specialized solution for long products that are impractical or impossible to rotate effectively on a turntable platform.
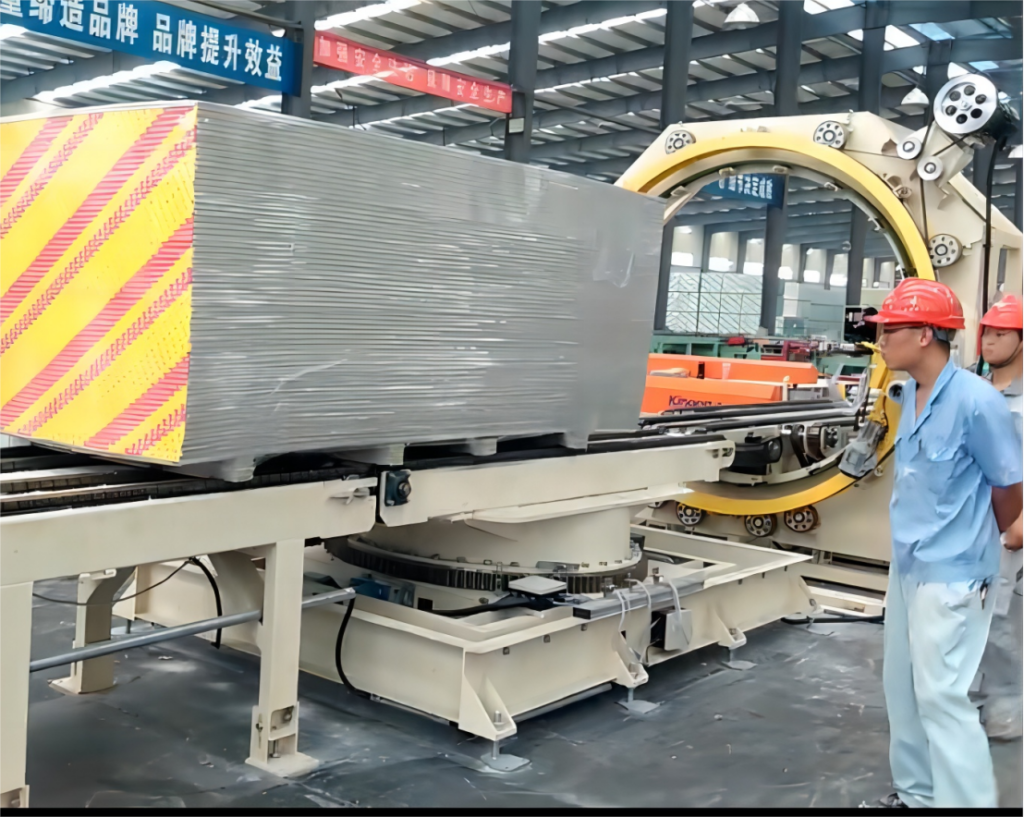
Conclusion
For operations handling panels, profiles, extrusions, lumber, tubing, or similar elongated materials, orbital stretch wrappers provide a robust, efficient, and protective packaging solution. By moving the product linearly through a rotating film application ring, they overcome the limitations of turntable systems for long items. Careful consideration of factors like film roll mounting options and required customization will ensure the selected system meets specific operational needs and enhances packaging productivity within the fabrication environment.