Key Steps to Enhance Safety in Operating Orbital Stretch Wrapper for Pallet Load
In the fast-paced world of logistics and warehousing, efficiency and safety go hand in hand. One of the most crucial pieces of equipment in this industry is the orbital stretch wrapper, a machine designed to secure pallet loads quickly and effectively. While these machines are invaluable for streamlining operations, they also present potential safety hazards if not operated correctly. In this comprehensive guide, we’ll explore the key steps to enhance safety when operating an orbital stretch wrapper for pallet loads, ensuring that your workplace remains both productive and secure.
Understanding the Orbital Stretch Wrapper
Before diving into safety measures, it’s essential to understand what an orbital stretch wrapper is and how it functions. An orbital stretch wrapper is a machine designed to wrap stretch film around a pallet load in a horizontal motion. Unlike traditional turntable or rotary arm wrappers, orbital wrappers move around the load, making them ideal for unstable or oddly-shaped items.
Key components of an orbital stretch wrapper include:
- The film delivery system
- The orbital ring that moves around the load
- The conveyor system that moves pallets through the wrapping area
- Control panels for operation and adjustment
Understanding these components is crucial for implementing effective safety measures.
The Importance of Safety in Pallet Wrapping Operations
Ensuring safety in pallet wrapping operations is not just about compliance with regulations; it’s about protecting your most valuable asset – your workforce. Accidents involving orbital stretch wrappers can lead to:
- Serious injuries to operators and nearby workers
- Damage to valuable inventory
- Costly downtime and repairs
- Negative impact on company morale and reputation
By prioritizing safety, you’re not only protecting your employees but also enhancing overall operational efficiency and productivity.
Key Step 1: Proper Training and Certification
The foundation of safety in operating orbital stretch wrappers lies in comprehensive training. Here’s what an effective training program should include:
Theoretical Knowledge
- Basic principles of stretch wrapping
- Understanding of machine components and functions
- Safety features and their importance
- Potential hazards and risk assessment
Hands-on Training
- Practical operation of the machine under supervision
- Troubleshooting common issues
- Emergency shut-off procedures
Certification Process
- Written and practical tests to ensure competency
- Regular refresher courses to keep skills up-to-date
Remember, only certified operators should be allowed to use the orbital stretch wrapper. This is not an area where on-the-job learning is appropriate.
Key Step 2: Pre-Operation Safety Checks
Before starting any wrapping operation, it’s crucial to perform a thorough safety check. This should become a habitual part of the operator’s routine.
Machine Inspection
- Check for any visible damage or wear on the machine
- Ensure all guards and safety devices are in place and functioning
- Verify that emergency stop buttons are accessible and operational
Area Inspection
- Clear the wrapping area of any obstacles or debris
- Ensure adequate lighting in the operational area
- Check that warning signs and safety markings are visible and in good condition
Film and Pallet Inspection
- Verify that the correct type and size of stretch film is loaded
- Check that pallets are stable and properly assembled
By consistently performing these checks, you can prevent many potential accidents before they occur.
Key Step 3: Proper Machine Setup and Adjustment
Correct setup of the orbital stretch wrapper is crucial for both safety and efficiency. Here are the key areas to focus on:
Film Tension Adjustment
- Set the proper film tension to ensure secure wrapping without damaging products
- Regularly check and adjust tension as needed, especially when changing load types
Speed Settings
- Adjust the orbital speed based on the stability and weight of the load
- Start with slower speeds for unfamiliar or unstable loads
Height and Width Settings
- Ensure the machine is properly adjusted to accommodate the size of the load
- Double-check settings when switching between different pallet sizes
Remember, improper setup can lead to unstable loads, which are a major safety hazard during transportation and storage.
Key Step 4: Safe Loading and Unloading Procedures
The process of getting pallets in and out of the wrapping area is a critical safety point. Here’s how to do it safely:
Loading Procedures
- Use proper lifting equipment (forklifts, pallet jacks) to move loads into position
- Ensure the load is centered on the conveyor or wrapping area
- Verify that the load is stable before initiating the wrapping process
Unloading Procedures
- Wait for the wrapping cycle to complete fully before approaching the load
- Use caution when removing the wrapped pallet, as it may be heavier than before wrapping
- Inspect the wrapped load for stability before transporting
Key Step 5: Implementing a Safe Operating Zone
Creating and maintaining a safe operating zone around the orbital stretch wrapper is crucial for preventing accidents.
Defining the Zone
- Use floor markings or barriers to clearly delineate the operating area
- Ensure the zone includes enough space for safe loading and unloading
Access Control
- Restrict access to the operating zone to authorized personnel only
- Use signage to warn others about the potential hazards
Traffic Management
- Implement clear traffic patterns for forklifts and pedestrians around the wrapping area
- Use mirrors or sensors to improve visibility in blind spots
By controlling access and movement around the machine, you significantly reduce the risk of collisions and other accidents.

Key Step 6: Personal Protective Equipment (PPE)
While proper machine operation is crucial, personal protective equipment provides an additional layer of safety for operators.
Essential PPE for Orbital Stretch Wrapper Operators
- Safety glasses to protect against film debris or snapping
- Steel-toed boots to guard against falling objects
- High-visibility vests to ensure operators are easily seen
- Gloves to protect hands during film loading and minor adjustments
PPE Maintenance
- Regularly inspect PPE for wear and damage
- Replace PPE as needed to ensure continued protection
- Train employees on the proper use and care of their PPE
Remember, PPE is only effective if it’s worn consistently and correctly.
Key Step 7: Emergency Procedures and Equipment
Even with the best preventive measures, emergencies can still occur. Being prepared for these situations is crucial.
Emergency Stop Procedures
- Train all operators on the location and use of emergency stop buttons
- Conduct regular drills to ensure quick response times
First Aid and Fire Safety
- Maintain well-stocked first aid kits in easily accessible locations
- Ensure fire extinguishers are available and operators know how to use them
Emergency Response Plan
- Develop a clear plan for various emergency scenarios
- Regularly review and practice the emergency response plan with all staff
Having a well-prepared team can make a significant difference in minimizing the impact of any emergency situation.
Key Step 8: Regular Maintenance and Inspections
A well-maintained machine is a safer machine. Implementing a robust maintenance program is essential for long-term safety.
Daily Checks
- Perform visual inspections at the start of each shift
- Check for any unusual noises or vibrations during operation
Scheduled Maintenance
- Follow the manufacturer’s recommended maintenance schedule
- Keep detailed records of all maintenance activities
Professional Inspections
- Schedule regular inspections by qualified technicians
- Address any issues identified during inspections promptly
Remember, preventive maintenance is not just about keeping the machine running; it’s about ensuring it runs safely.
Key Step 9: Proper Film Handling and Storage
The stretch film itself can be a source of safety hazards if not handled correctly.
Safe Film Loading
- Train operators on the correct technique for loading film rolls
- Use mechanical aids for heavy rolls to prevent strain injuries
Film Storage
- Store film rolls in a cool, dry area away from direct sunlight
- Implement a first-in, first-out system to ensure film quality
Waste Management
- Dispose of used film and cores properly to prevent tripping hazards
- Consider recycling options for used stretch film
Proper film management not only enhances safety but also contributes to a more organized and efficient workplace.
Key Step 10: Continuous Improvement and Feedback
Safety is not a one-time implementation but an ongoing process of improvement.
Safety Meetings
- Hold regular safety meetings to discuss any issues or near-misses
- Encourage open communication about safety concerns
Operator Feedback
- Create a system for operators to report safety issues or suggest improvements
- Act on valuable feedback to show that safety input is taken seriously
Safety Audits
- Conduct periodic safety audits of the wrapping operation
- Use audit results to identify areas for improvement and track progress over time
By fostering a culture of continuous improvement, you can ensure that your safety measures evolve with your operations.
Conclusion: Prioritizing Safety for Optimal Performance
Operating an orbital stretch wrapper for pallet loads is a critical task in many warehouses and distribution centers. While these machines offer significant benefits in terms of efficiency and load stability, they also present potential safety risks that must be carefully managed.
By implementing the key steps outlined in this guide – from comprehensive training and pre-operation checks to regular maintenance and continuous improvement – you can create a safer working environment around your orbital stretch wrapper. Remember, safety is not just about avoiding accidents; it’s about creating a culture where every employee feels valued and protected.
A safe operation is ultimately a more productive operation. When employees feel secure in their work environment, they can focus on performing their tasks efficiently and effectively. Moreover, a strong safety record can enhance your company’s reputation, potentially leading to new business opportunities and reduced insurance costs.
As technology continues to evolve, stay informed about new safety features and best practices in the industry. Regularly review and update your safety protocols to ensure they remain effective and relevant. By making safety a top priority in your orbital stretch wrapper operations, you’re not just protecting your workforce – you’re investing in the long-term success and sustainability of your business.
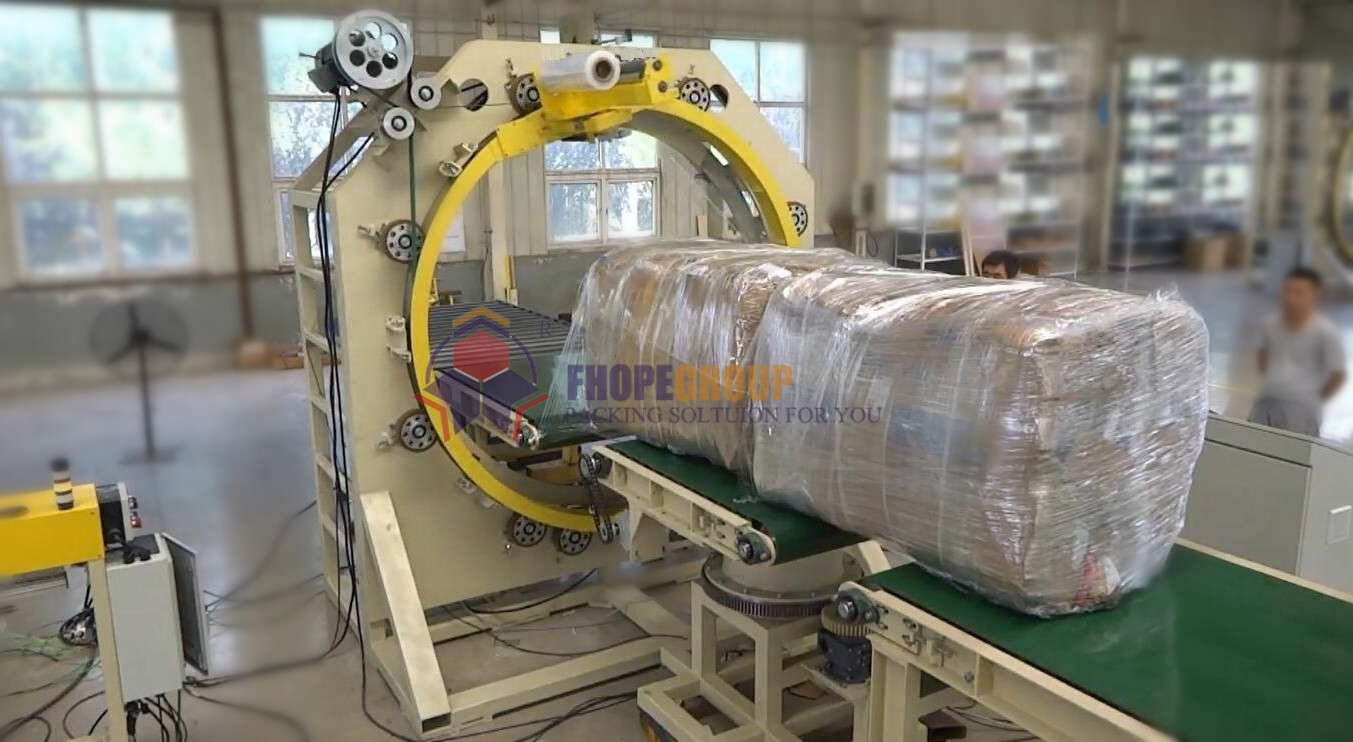