Optimizing Door Packaging: The Role of Orbital Stretch Wrappers
Ensuring doors arrive at their destination undamaged is paramount in the manufacturing and distribution industry. Scratches, dents, and moisture exposure during transit can lead to costly returns and dissatisfied customers. An effective packaging strategy is crucial, and for long, bulky items like doors, orbital stretch wrappers offer a robust and efficient solution. Often referred to generally as a door packaging machine, this technology automates the protective wrapping process.
This article explores the function, benefits, and key considerations of using orbital stretch wrappers for door packaging, aligning with best practices for operational efficiency and product protection.
What is an Orbital Stretch Wrapper?
Unlike traditional turntable stretch wrappers where the load rotates on a platform, an orbital stretch wrapper features a vertical ring or rotating carriage. The door passes horizontally through the center of this ring, which dispenses stretch film, wrapping it securely around the product's profile. This method is particularly well-suited for long, heavy, or irregularly shaped items that are difficult or unstable to rotate.
The core components typically include:
- Infeed and Outfeed Conveyors: To transport the door through the wrapping zone.
- Rotating Ring/Carriage: Holds and dispenses the stretch film roll.
- Film Delivery System: Controls film tension and pre-stretch (if applicable).
- Clamping and Cutting Mechanism: Automatically grips the film at the start and cuts it upon cycle completion.
- Control Panel: Allows operators to set parameters like wrap patterns, tension, and conveyor speed.
(Placeholder for Image: Diagram showing the orbital stretch wrapping process for a door)
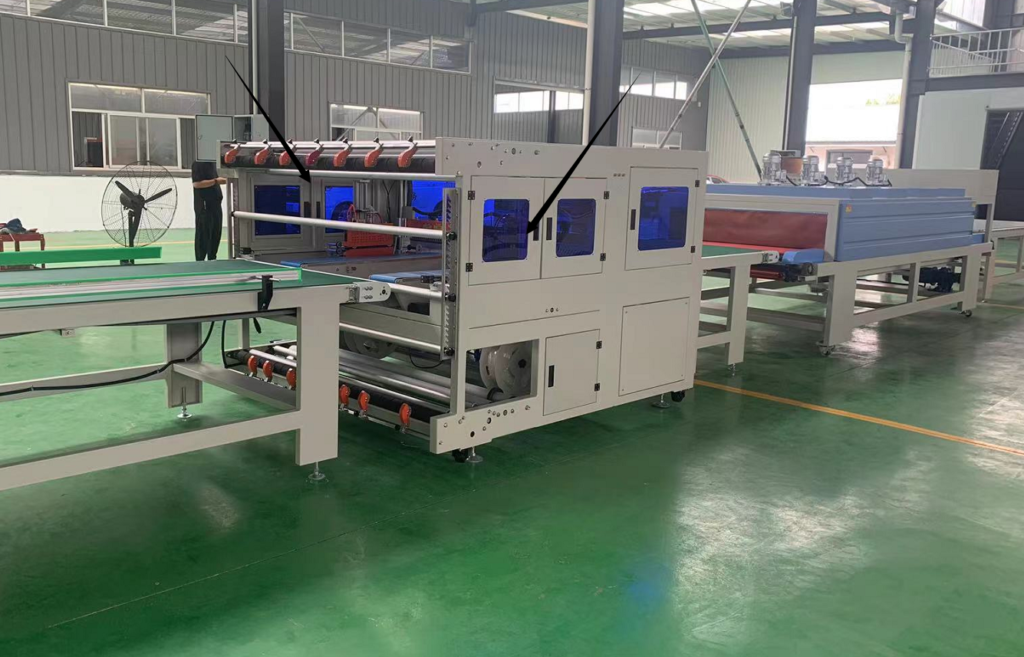
How Orbital Wrappers Enhance Door Packaging
Implementing an automated horizontal wrapping machine system offers significant advantages over manual or semi-automated methods:
1. Superior Product Protection
The primary benefit is consistent, high-quality protection. Orbital wrappers apply stretch film with controlled tension, creating a tight cocoon around the door.
- Full Encapsulation: Wraps all sides (except potentially the very ends, depending on setup), safeguarding vulnerable edges and corners.
- Damage Prevention: Creates a barrier against scratches, scuffs, dust, and moisture during handling and shipping.
- Load Stabilization: Unitizes the door, making it more stable for transport and reducing the risk of shifting.
2. Increased Operational Efficiency
Automation drastically speeds up the packaging process compared to manual wrapping.
- Higher Throughput: Machines can wrap doors significantly faster than human operators, boosting overall productivity.
- Reduced Labor Costs: Frees up personnel previously dedicated to tedious manual wrapping for more value-added tasks.
- Consistency: Ensures every door is wrapped to the same standard, eliminating variability common in manual processes.
3. Material Optimization and Cost Savings
Modern orbital wrappers often incorporate pre-stretch capabilities.
- Film Pre-Stretch: Stretches the film before application (often up to 250-300%), maximizing yield per roll and significantly reducing film consumption compared to manual application.
- Controlled Usage: Applies only the necessary amount of film based on programmed settings, minimizing waste.
- Lower Material Costs: Although the initial investment is higher, reduced film usage leads to ongoing savings.
4. Improved Handling and Safety
Properly wrapped doors are easier and safer to manage.
- Easier Handling: The film provides a uniform surface, facilitating handling with forklifts or other equipment.
- Reduced Injury Risk: Automating the wrapping process minimizes manual lifting and awkward movements associated with wrapping large items.
- Stable Stacking: Wrapped doors can often be stacked more securely (within structural limits), optimizing warehouse space and transport loads.
(Placeholder for Video: Showing an orbital wrapper in action packaging doors)
Key Considerations for Implementation
Selecting the right orbital stretch wrapper involves evaluating several factors:
- Product Dimensions: Ensure the machine's ring diameter and conveyor system can accommodate the full range of door sizes (height, width, length) your facility handles.
- Throughput Requirements: Match the machine's wrapping speed (doors per hour) to your production output.
- Film Specifications: Consider the type, gauge, and pre-stretch capabilities required for adequate protection. Consult film suppliers for recommendations based on product weight and shipping conditions. ([External Link Placeholder: Link to a reputable packaging film guide or standard, e.g., from ASTM or a packaging association])
- Automation Level: Determine the need for integration with existing production lines, automatic top sheet dispensers, or corner protection applicators.
- Footprint and Layout: Ensure sufficient space for the machine, conveyors, and safe operator access within your facility.
- Safety Features: Verify compliance with safety standards, including emergency stops, safety guarding, and light curtains. ([External Link Placeholder: Link to OSHA or relevant safety standard body])
(Placeholder for Image: A finished door securely wrapped in stretch film, ready for shipping)
![Finished door securely wrapped in clear stretch film by an orbital wrapper, highlighting edge protection]
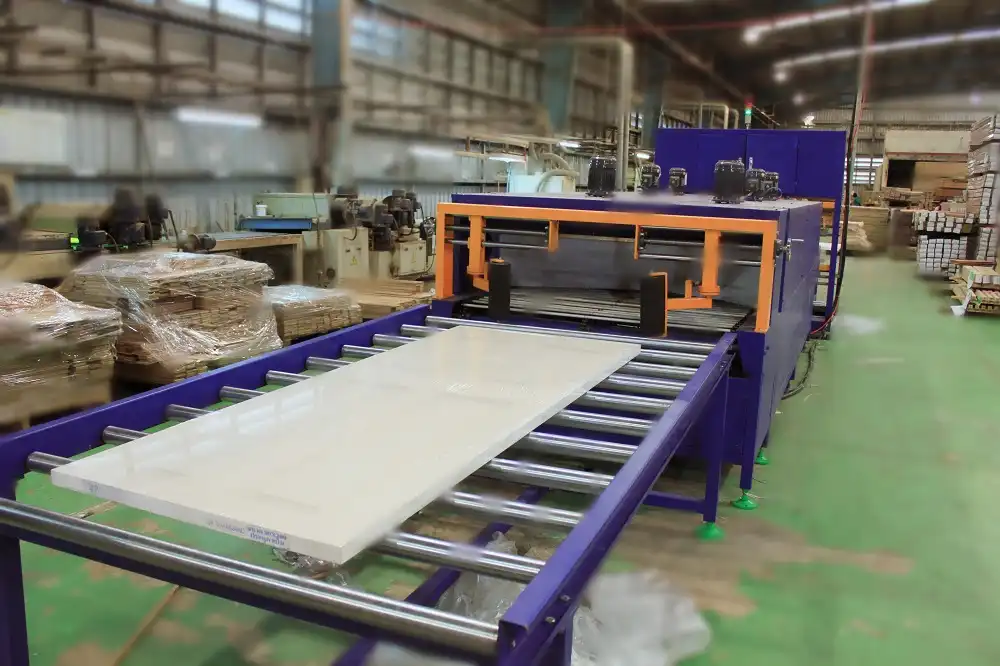
Conclusion
For door manufacturers seeking to improve packaging quality, increase efficiency, and reduce costs associated with shipping damage and labor, orbital stretch wrappers present a compelling solution. By automating the application of stretch film, these machines provide consistent, robust protection tailored to the unique challenges of handling long and bulky products. Careful consideration of operational needs and machine specifications will ensure the chosen system delivers optimal performance and a strong return on investment, ultimately contributing to greater customer satisfaction and a more streamlined logistics process.