Optimizing Packaging for Different Coil Sizes with a Flexible Steel Coil Packing Line
- Optimizing Packaging for Different Coil Sizes with a Flexible Steel Coil Packing Line
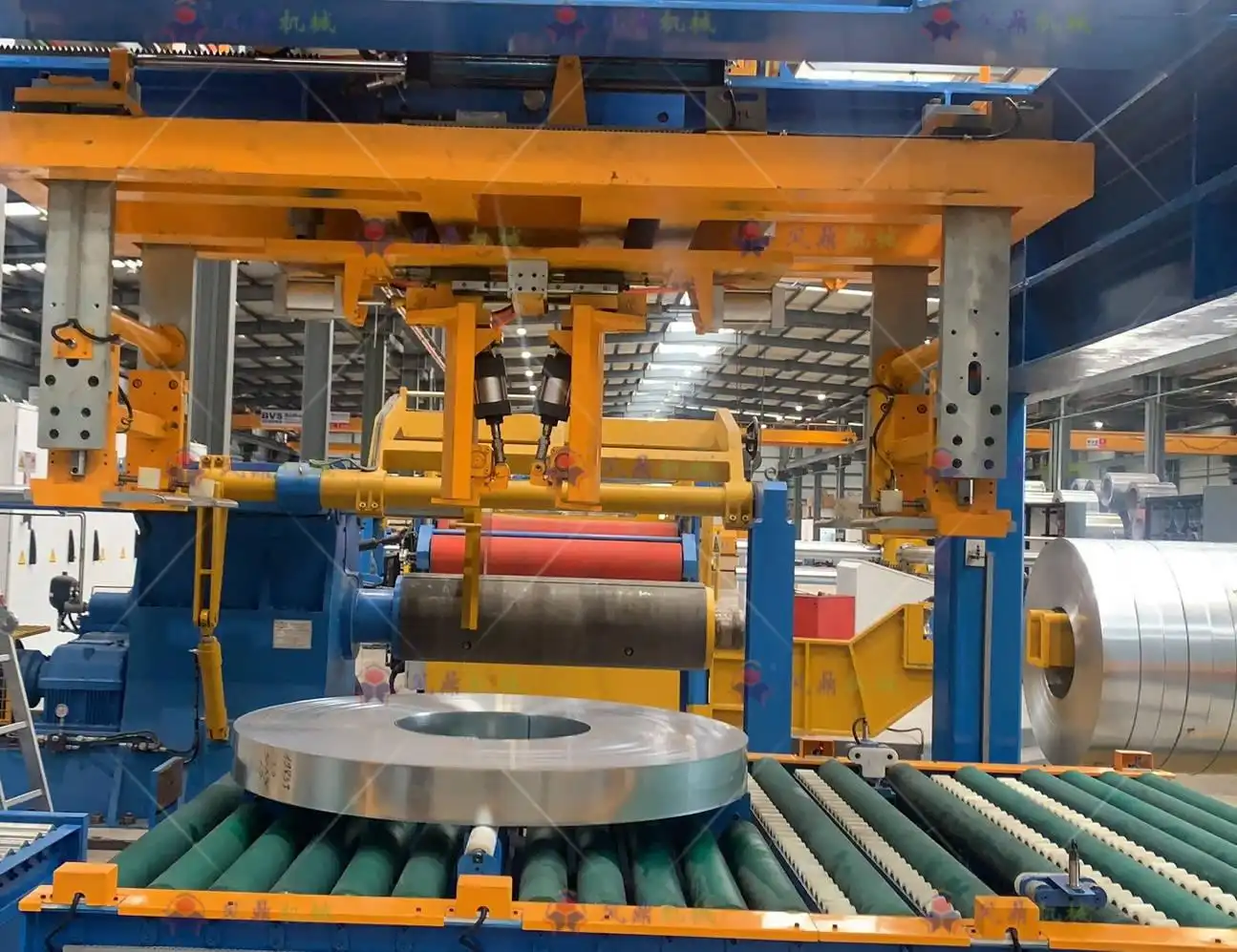
Introduction
In the steel industry, coil packaging plays a vital role in protecting products during transportation and storage. However, not all coils are the same. Coils vary in size, weight, and material, and this variation requires a flexible steel coil packing line to ensure optimal packaging for each type of coil. A one-size-fits-all approach can lead to inefficiencies, material wastage, and even damaged goods. To overcome these challenges, companies are increasingly adopting flexible packaging solutions that can handle a wide range of coil sizes, from small to extra-large, without compromising on quality or efficiency.
This article will explore how a flexible steel coil packing line can be optimized to accommodate different coil sizes, ensuring that each coil is packaged correctly and efficiently. We will look at the benefits of flexibility in a packing line, the challenges associated with packaging various coil sizes, and the customization options available to optimize performance.
1. The Importance of Flexibility in Steel Coil Packing Lines
Adapting to Varied Coil Sizes
Steel coils can range widely in size, from smaller coils used in specialized applications to massive coils used in heavy industries. A flexible packing line is essential for facilities that process different coil sizes on a daily basis. Without flexibility, the packing line may require manual adjustments, which can slow down operations and lead to inconsistencies in packaging quality.
By designing a system that can automatically adjust to different coil dimensions, companies can optimize packaging performance and ensure that each coil is securely packed, regardless of its size.
Reducing Downtime and Increasing Efficiency
One of the key benefits of a flexible steel coil packing line is the reduction in downtime. In traditional systems, switching between different coil sizes often requires manual intervention to adjust machine settings, which can lead to delays and increased labor costs. A flexible system eliminates the need for manual adjustments by allowing operators to quickly switch between different coil sizes without disrupting the flow of production. This increases overall efficiency and keeps the production line running smoothly.
2. Challenges of Packaging Different Coil Sizes
Handling Variations in Weight and Diameter
One of the primary challenges in packaging different coil sizes is the variation in weight and diameter. Larger coils may require more robust packaging materials and equipment to ensure they are securely strapped and protected, while smaller coils may need lighter, more flexible materials to avoid over-packaging. Additionally, the difference in weight between coils can affect the performance of conveyor systems and other automated equipment.
Maintaining Consistent Packaging Quality
When handling various coil sizes, maintaining consistent packaging quality can be difficult. Without proper adjustments, larger coils may be under-wrapped, leaving them vulnerable to damage during transport, while smaller coils may be over-wrapped, leading to unnecessary material waste. A flexible packing line must be able to ensure that each coil is wrapped and strapped with the right amount of material, regardless of its size.
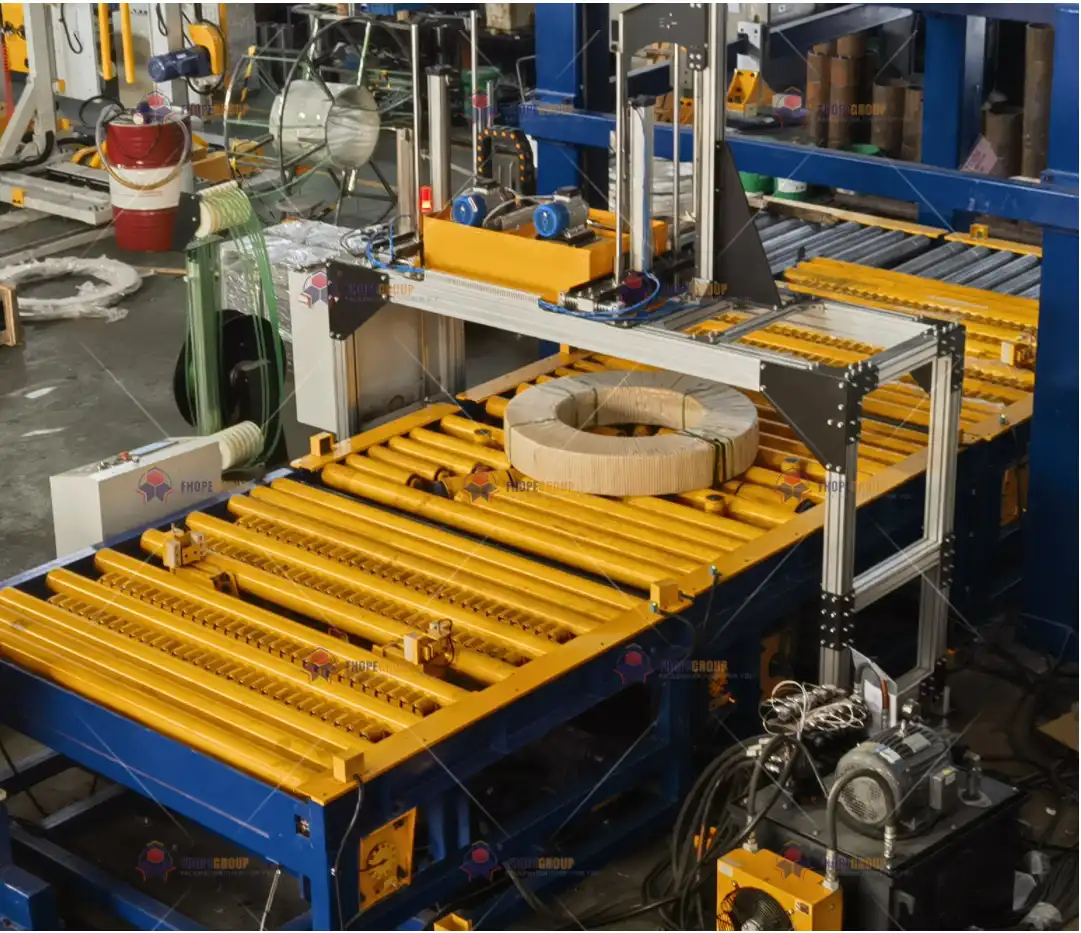
3. Core Features of a Flexible Steel Coil Packing Line
Adjustable Conveyor Systems
To accommodate coils of different sizes, the conveyor system in a steel coil packing line must be adjustable. This includes the ability to change the width, speed, and weight tolerance of the conveyor belts. Automated systems that adjust these settings in real time are particularly valuable, as they allow the packing line to handle different coils without needing to pause for manual adjustments.
- Width Adjustment: Ensures that both large and small coils are securely transported through the packaging line.
- Speed Control: The system adjusts the conveyor speed based on coil weight, preventing heavy coils from moving too quickly and light coils from moving too slowly.
- Weight Sensors: Integrated weight sensors ensure that the system can handle coils of varying weights without overloading the machinery.
Automated Wrapping Systems
One of the most critical components of a flexible steel coil packing line is the automated wrapping system. This system must be able to adjust to different coil sizes, ensuring that each coil receives the appropriate level of protection. Automated wrapping machines are equipped with sensors that detect the coil’s dimensions and adjust the tension and amount of wrapping material accordingly.
For instance, large coils may require multiple layers of stretch film or protective paper, while smaller coils may only need a single layer. By customizing the wrapping process based on coil size, the system can prevent overuse of materials and ensure that each coil is adequately protected.
4. Customizing Packaging Materials for Different Coil Sizes
Material Selection for Large Coils
Large steel coils require durable packaging materials that can withstand the weight and pressure exerted during transport. Common materials for large coils include:
- Heavy-duty stretch film: Provides a high level of protection and ensures that the coil remains intact during long-distance transport.
- VCI (Vapor Corrosion Inhibitor) paper: Prevents rust and corrosion, especially in high-humidity environments.
- Steel or reinforced plastic straps: Securely hold the coil in place, preventing shifting during movement.
The strength and durability of the packaging materials used for large coils are critical to ensuring that the product arrives at its destination without damage.
Material Selection for Small Coils
For smaller coils, the focus is on using lightweight packaging materials that provide sufficient protection without adding unnecessary bulk or cost. These may include:
- Lightweight stretch film: Protects against dirt, dust, and moisture while keeping the package light and easy to handle.
- Plastic straps: Suitable for lighter coils that don’t require heavy-duty strapping.
By customizing the packaging materials based on coil size, companies can ensure that each coil is packaged efficiently without wasting resources.
5. Automation Levels for Packaging Different Coil Sizes
Semi-Automated vs. Fully Automated Systems
When optimizing a steel coil packing line for flexibility, companies must consider the level of automation that best suits their needs. Both semi-automated and fully automated systems offer unique benefits:
- Semi-Automated Systems: Semi-automated systems require human operators to load and position the coils, but the actual wrapping and strapping processes are automated. This option is suitable for facilities that handle a moderate variety of coil sizes and don’t require frequent changes in the packaging setup.
- Fully Automated Systems: Fully automated systems can handle the entire packaging process without human intervention. These systems are ideal for facilities with high production volumes and frequent changes in coil size. They can automatically adjust to different coil dimensions, minimizing downtime and maximizing efficiency.
Benefits of Fully Automated Systems for Flexibility
Fully automated systems offer the highest level of flexibility because they can quickly adapt to changes in coil size without requiring manual intervention. With sensors and programmable logic controllers (PLCs), fully automated systems can automatically detect coil size and adjust the wrapping and strapping parameters in real time. This ensures that each coil is packaged efficiently, regardless of its size or weight.
This concludes the first half of the article. Please review this portion and let me know if you would like any changes or adjustments before I proceed with the second half.

Get Your Best Solution !