Optimizing End-of-Line Packaging: A Guide to Automatic Pallet Wrapping Machines
Manual pallet wrapping is often time-consuming, inconsistent, and physically demanding. As throughput demands increase and consistent load containment becomes critical for reducing shipping damage, many fabrication and manufacturing facilities turn to automation. An automatic pallet wrapping machine offers a robust solution for efficiently securing palletized goods using stretch film.
These machines automate the process of applying stretch film, significantly improving speed, consistency, and safety compared to manual or semi-automatic methods. Understanding their features and benefits is key to selecting the right system for your operation.
Key Operational Features of Automatic Pallet Wrappers
Modern automatic stretch wrappers incorporate several advanced features designed for performance and flexibility:
Automation and Control Systems
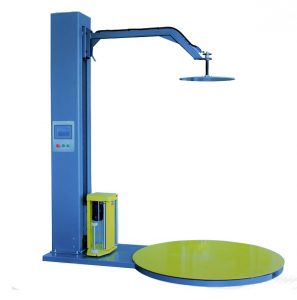
- Fully Automatic Operation: Once initiated, the machine handles the entire wrap cycle without operator intervention, from film attachment to cutting and sealing.
- Programmable Logic Controller (PLC): Allows for precise control over wrapping parameters, including rotation speed, film carriage speed (up/down), number of top/bottom wraps, and film tension.
- Adjustable Wrapping Parameters: Settings can be easily customized and saved as recipes for different load types, sizes, and stability requirements via a Human-Machine Interface (HMI), often a touchscreen.
- Multiple Wrapping Modes: Programs can accommodate various needs, such as applying a top sheet for dust/moisture protection (requiring an integrated top sheet dispenser) or reinforcing specific load sections.
Material Handling and Film Management
- Integrated Conveyor Systems: Power conveyors automatically transport pallets into, through, and out of the wrapping zone, enabling seamless integration into automated production lines. Conveyor types (roller, chain) can be specified based on pallet type and weight.
- Powered Film Pre-Stretch: This critical feature stretches the film before application (often up to 250-300%), maximizing film yield, reducing material costs, and ensuring tighter, more secure loads.
- Automatic Film Clamp, Cut, and Wipe System: Securely captures the film tail at the start of the cycle, cleanly cuts the film upon completion, and often includes a wipe-down mechanism to press the film tail against the load, preventing unraveling.
Safety Mechanisms
- Perimeter Guarding: Physical fencing or barriers prevent personnel from entering the wrapping zone during operation.
- Light Curtains: Safety sensors create an invisible barrier; if interrupted, they immediately halt machine motion.
- Load Height Sensing: Photo-eyes automatically detect the top of the pallet, ensuring the machine wraps to the correct height without manual adjustment.
- Emergency Stops: Easily accessible E-stop buttons are strategically placed to quickly stop all machine functions.
Benefits for Fabrication and Manufacturing Operations
Investing in an automatic pallet wrapper provides tangible advantages:
- Enhanced Throughput and Efficiency: Significantly faster cycle times compared to manual wrapping, reducing bottlenecks at the end of the packaging line.
- Improved Load Containment and Product Protection: Consistent wrap patterns and controlled film tension provide superior load stability, drastically reducing product damage during transit and handling.
- Labor Optimization and Ergonomics: Frees up personnel previously assigned to manual wrapping for more value-added tasks. Eliminates the physically demanding and repetitive motions associated with hand wrapping, improving workplace safety.
- Material Cost Savings: Film pre-stretching significantly reduces the amount of stretch film consumed per pallet compared to manual wrapping, leading to substantial cost reductions.
- Consistency: Every pallet is wrapped according to pre-set parameters, ensuring uniformity critical for automated storage and retrieval systems (AS/RS) and customer satisfaction.
Considerations When Selecting an Automatic Pallet Wrapper
Choosing the right machine involves evaluating several factors:
- Load Characteristics: Consider the typical size, weight, shape, and stability of your palletized goods.
- Required Throughput: Determine the number of pallets per hour the machine needs to handle to keep pace with production.
- Integration Needs: Assess how the wrapper will connect with upstream and downstream equipment (conveyors, AGVs, etc.).
- Film Type and Pre-Stretch: Ensure the machine is compatible with your desired film specifications and offers the appropriate pre-stretch level for optimal performance and savings.
- Operating Environment: Factor in space constraints, temperature, and cleanliness of the installation area.
- Maintenance and Support: Evaluate the manufacturer's reputation for reliability, service availability, and spare parts accessibility.
Conclusion
An automatic pallet wrapping machine is a cornerstone of efficient and reliable end-of-line packaging. By automating the stretch wrapping process, businesses can achieve higher throughput, better load protection, significant cost savings, and improved worker safety. Carefully evaluating operational needs against machine capabilities ensures the selection of a system that delivers long-term value and performance. For businesses looking to scale operations and enhance packaging quality, exploring options like a Multipurpose, Automatic Pallet Wrapping Machine is a crucial step towards modernization.