In the fast-paced world of logistics and warehousing, the tools and machinery we use can make or break our operational efficiency. Among these tools, pallet inverters—machines designed to flip or rotate pallets for various purposes—have become essential. However, a crucial decision arises when choosing the right type: should you opt for a mobile pallet inverter or a stationary pallet inverter? This question is not just about the equipment but about how it integrates into your workflow and enhances your overall productivity.
At first glance, both mobile and stationary pallet inverters might seem to perform the same task—flipping pallets. But the reality is far more nuanced. These machines differ significantly in terms of design, functionality, and application. A mobile pallet inverter offers flexibility and adaptability, while a stationary one provides stability and high throughput. Understanding these distinctions is vital for making an informed decision that aligns with your business operations.
To make the best choice between a mobile and a stationary pallet inverter, you need to consider factors such as your factory layout, the frequency of pallet rotation, and the specific handling requirements of your products. By diving deeper into their features, advantages, and limitations, we can uncover which option suits your needs best. Let’s explore this decision-making process step by step.
[claim] Choosing the right pallet inverter is not just about the machine itself; it’s about how it fits into your workflow and adapts to the unique demands of your operation. Only by evaluating both options thoroughly can you maximize your efficiency and ROI.
Table of Contents
- What are the key differences between mobile and stationary pallet inverters?
1.1 Versatility and mobility: How mobile pallet inverters adapt to dynamic operations
1.2 Stability and scalability: The stationary pallet inverter advantage
1.3 Comparing use-case scenarios: Which is better for your operation? - How do space and layout impact pallet inverter selection?
2.1 Mobile inverters in tight spaces: A compact solution
2.2 Stationary systems in large facilities: Optimizing workflow
2.3 Navigating layout challenges: Tips for seamless integration - Which factors influence the cost-effectiveness of pallet inverters?
3.1 Initial investment vs. long-term value
3.2 Maintenance and operational costs
3.3 ROI considerations: Ensuring your choice pays off
1. What are the key differences between mobile and stationary pallet inverters?
1.1 Versatility and mobility: How mobile pallet inverters adapt to dynamic operations
When it comes to versatility, mobile pallet inverters shine as champions of adaptability. These machines are designed to move freely across your facility, enabling you to bring the pallet inverter to the product rather than the other way around. For businesses with dynamic operations or multiple workstations, this flexibility can be a game changer.
Imagine a warehouse where products are constantly being shuffled between loading docks, storage areas, and production lines. In such an environment, a mobile pallet inverter allows you to handle pallet rotation at various locations, reducing downtime and streamlining workflows. Unlike stationary systems, which are fixed in one place, mobile inverters give you the freedom to adapt to changing needs without reconfiguring your facility.
However, mobility comes with its own set of challenges. Mobile pallet inverters typically have a smaller capacity compared to their stationary counterparts. Additionally, they require operators to navigate them through the facility, which might not be ideal in spaces with heavy traffic or narrow aisles. Despite these limitations, their ability to adapt to diverse tasks makes them a preferred choice for operations that value flexibility above all else.
1.2 Stability and scalability: The stationary pallet inverter advantage
Stationary pallet inverters, on the other hand, are all about delivering consistent performance in high-volume operations. These machines are installed at fixed locations, often integrated into production lines or designated pallet-handling areas. Their robust design allows them to handle heavier loads and larger volumes, making them indispensable for industries that require high throughput.
One of the key advantages of stationary pallet inverters is their stability. Since they are not designed to move, these machines can be built to accommodate a wide range of pallet sizes and weights. This scalability is particularly beneficial for businesses dealing with bulk goods or heavy materials that require frequent pallet rotation. Furthermore, stationary systems often come with customizable features, such as automated controls and conveyor integrations, which can further enhance their efficiency.
That said, the fixed nature of stationary pallet inverters can be a drawback in certain scenarios. If your facility lacks the space to dedicate a permanent area to pallet handling, or if your operations are spread across multiple locations, a stationary system may feel restrictive. In such cases, the flexibility of a mobile inverter might outweigh the stability of a stationary one.
1.3 Comparing use-case scenarios: Which is better for your operation?
To truly understand the difference between mobile and stationary pallet inverters, it helps to compare their performance in specific scenarios. For instance, a mobile pallet inverter is ideal for smaller warehouses with limited space or businesses that handle a variety of products requiring occasional pallet rotation. Its ability to move between stations ensures that you’re not tied down to a single location, making it a versatile choice for dynamic environments.
Conversely, a stationary pallet inverter excels in large-scale operations where efficiency and consistency are paramount. If your business involves frequent pallet exchanges, heavy loads, or integration with automated systems, a stationary inverter is likely the better option. Its high capacity and customizability make it a reliable workhorse for demanding applications.
Ultimately, the choice between mobile and stationary pallet inverters boils down to your specific needs. By carefully evaluating your workflow, product requirements, and facility layout, you can identify which machine offers the best balance of flexibility, stability, and performance.
[claim] Whether you prioritize adaptability or efficiency, understanding the strengths and limitations of mobile and stationary pallet inverters is key to making the right decision for your business.
2. How do space and layout impact pallet inverter selection?
2.1 Mobile inverters in tight spaces: A compact solution
Space is one of the most critical factors when choosing between a mobile and stationary pallet inverter. For facilities with tight layouts or limited floor space, mobile pallet inverters provide a distinct advantage. Their compact design and portability allow operators to navigate narrow aisles and crowded storage areas with ease. Unlike stationary systems, which require a dedicated area for installation, mobile inverters can operate wherever they’re needed, making them a practical choice for smaller warehouses.
Picture a bustling warehouse where every square foot is maximized. In such an environment, dedicating a fixed spot for a stationary inverter could disrupt the flow of operations. A mobile inverter eliminates this constraint by offering on-demand functionality. Whether it’s flipping a damaged pallet or replacing a load for shipping, the mobility of these machines ensures that tasks can be completed without rearranging your workspace.
However, the compact nature of mobile pallet inverters comes with some compromises. For example, their smaller size may limit their load capacity, and their reliance on manual operation might not suit facilities with high automation levels. Still, in environments where flexibility and space efficiency are priorities, mobile inverters excel.
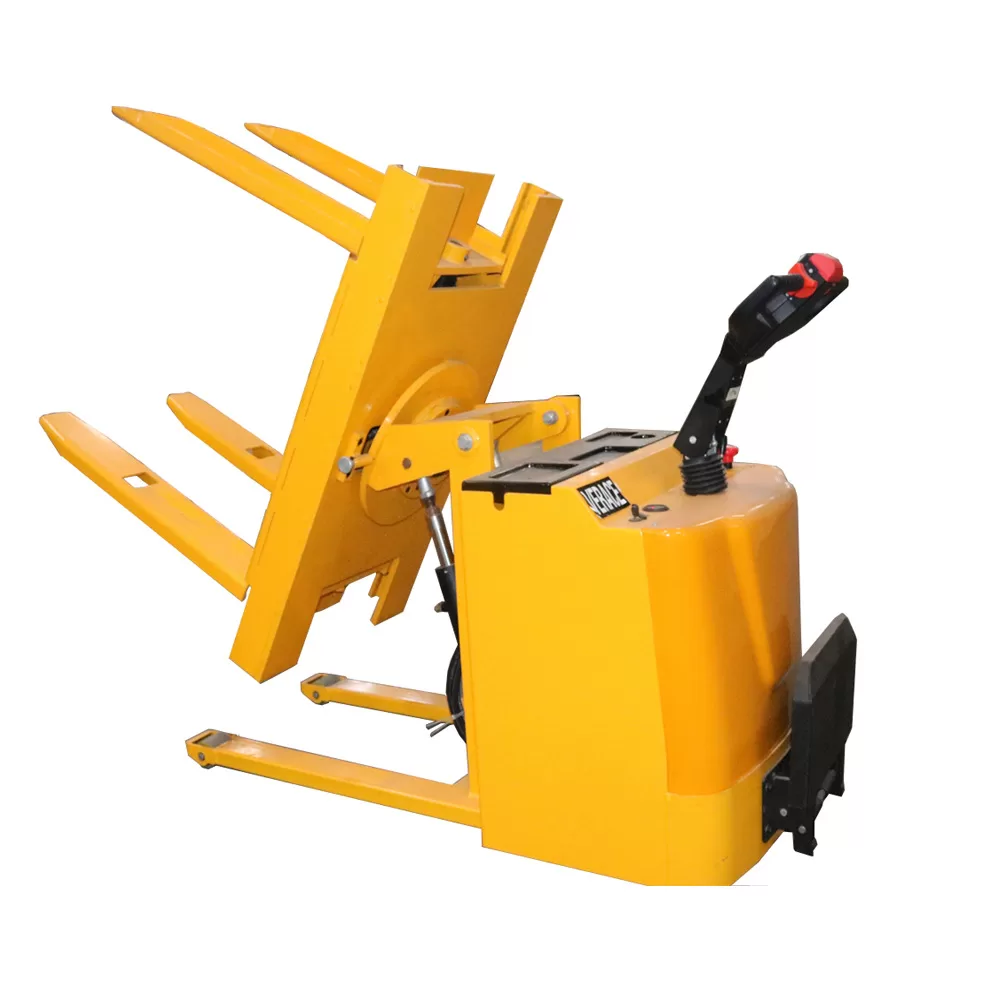
2.2 Stationary systems in large facilities: Optimizing workflow
For large facilities with ample space, stationary pallet inverters are often the preferred choice. These machines are typically installed in strategic locations, such as near loading docks, production lines, or storage zones, where they can handle high volumes of pallet turnover. Their fixed position and robust construction make them ideal for businesses that prioritize efficiency and consistency over mobility.
In large-scale operations, stationary inverters can be integrated into automated systems to create seamless workflows. For instance, a stationary inverter positioned at the end of a production line can automatically rotate pallets as part of the packaging process, reducing the need for manual intervention. Additionally, their ability to handle heavier loads and larger pallets makes them indispensable for industries such as manufacturing, food processing, and pharmaceuticals.
While stationary systems excel in spacious facilities, they are not without their limitations. Their fixed nature means they can’t be relocated easily, and installing them may require significant modifications to your layout. Moreover, if your operations are spread across multiple areas, relying solely on stationary inverters could lead to inefficiencies. In such cases, combining stationary systems with mobile inverters might offer the best of both worlds.
2.3 Navigating layout challenges: Tips for seamless integration
Selecting the right pallet inverter also involves addressing layout challenges unique to your facility. For instance, a warehouse with narrow aisles and dense shelving may benefit more from the flexibility of mobile inverters, while a facility with designated processing zones might favor stationary systems. Regardless of your choice, careful planning is essential for ensuring seamless integration.
Start by mapping out your workflow to identify bottlenecks and high-traffic areas. If space is limited, consider how a mobile inverter can be maneuvered without disrupting other operations. For stationary systems, evaluate whether your facility has enough room for installation and whether the placement aligns with your operational flow. In some cases, combining the two types of inverters can strike the perfect balance between flexibility and efficiency.
Space and layout are not just physical constraints; they are integral to the effectiveness of your pallet inverter. By carefully assessing your facility’s unique characteristics, you can choose a solution that enhances productivity without compromising your workflow.
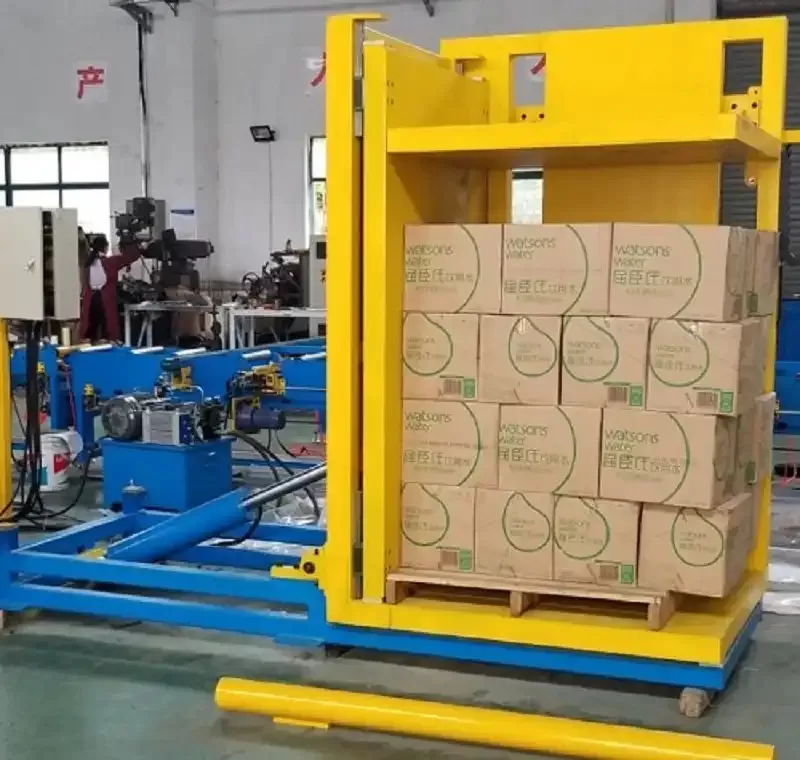
3. Which factors influence the cost-effectiveness of pallet inverters?
3.1 Initial investment vs. long-term value
When evaluating the cost-effectiveness of pallet inverters, it’s important to consider not only the initial purchase price but also the long-term value they bring to your operations. Mobile pallet inverters tend to have a lower upfront cost compared to stationary systems, making them an attractive option for businesses with limited budgets. However, their smaller capacity and reliance on manual operation might lead to higher labor costs over time.
On the other hand, stationary pallet inverters often come with a higher price tag due to their robust construction and additional features, such as automation capabilities. While the initial investment may seem steep, these machines can deliver significant cost savings in the long run by reducing labor requirements and increasing throughput. For businesses that handle high volumes of pallet rotation, the scalability and efficiency of stationary systems can quickly offset their higher upfront cost.
3.2 Maintenance and operational costs
In addition to the purchase price, it’s crucial to factor in maintenance and operational costs when choosing a pallet inverter. Mobile inverters typically have lower maintenance requirements due to their simpler design, but their frequent movement across the facility can lead to wear and tear, especially in demanding environments. Regular checks and repairs may be needed to keep them in optimal condition.
Stationary systems, while more durable, often require specialized maintenance due to their complex components and integration with other machinery. Additionally, their fixed installation means that any repairs or upgrades may cause temporary disruptions to your operations. Balancing these costs against the machine’s performance and lifespan is key to determining its overall cost-effectiveness.
3.3 ROI considerations: Ensuring your choice pays off
Ultimately, the return on investment (ROI) of a pallet inverter depends on how well it aligns with your operational needs. A mobile pallet inverter may offer quicker ROI for businesses with smaller-scale operations or those that require flexibility. Its ability to adapt to various tasks and locations can provide immediate benefits, such as reduced downtime and increased productivity.
For larger facilities, a stationary pallet inverter may take longer to pay off, but its higher capacity and integration capabilities can lead to substantial long-term savings. By automating repetitive tasks and minimizing labor costs, stationary systems can enhance efficiency and profitability over time. To maximize your ROI, it’s essential to evaluate your current and future needs, as well as the potential benefits each type of inverter can offer.
[claim] Cost-effectiveness is not just about the price tag; it’s about the value a pallet inverter brings to your operations. By analyzing both upfront and ongoing costs, you can make a decision that delivers maximum ROI.