Minimizing Manufacturing Downtime: Why Investing in Mold Handling Equipment is a Smart Choice
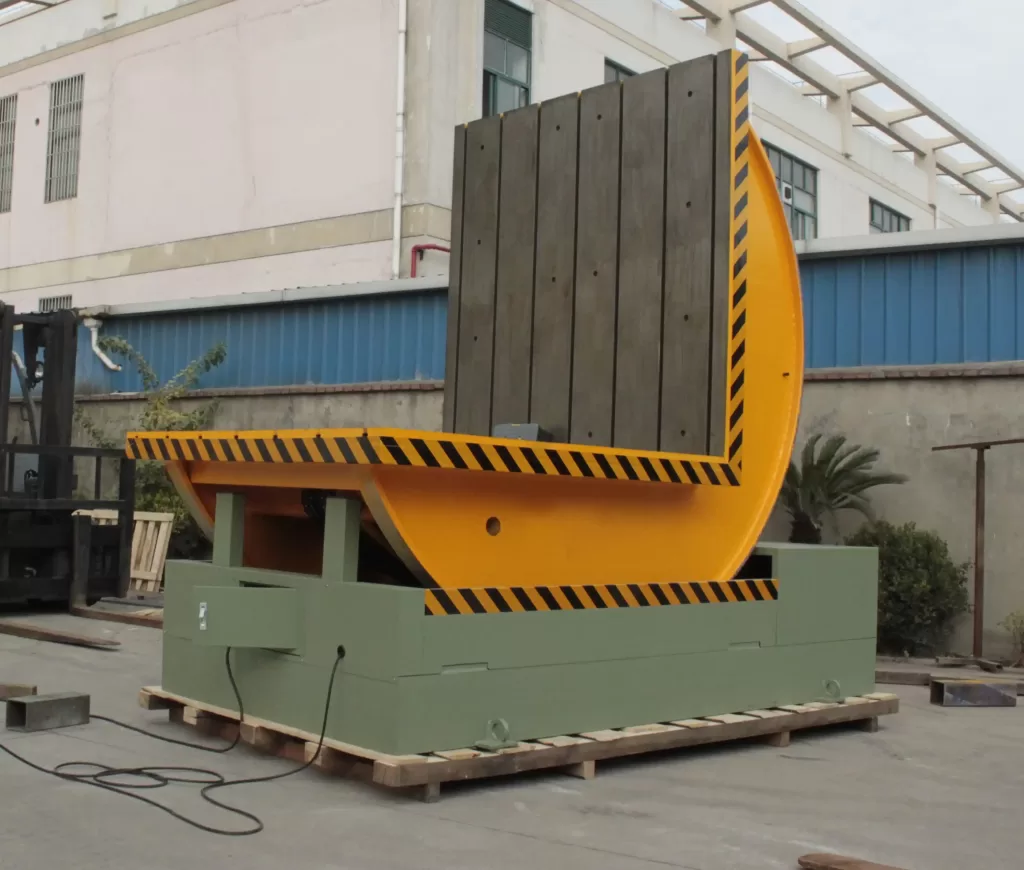
In any manufacturing operation, from small job shops to large-scale industrial facilities, downtime represents a significant drain on resources and productivity. Unplanned stops halt production, delay deliveries, and inflate operational costs. Minimizing this downtime is paramount. One effective strategy gaining traction involves specialized mold handling equipment, specifically the mold rotator (also known as a mold tilter or die rotator). This equipment is designed for the safe and efficient turning and positioning of heavy molds and dies. This article delves into why investing in a mold rotator is a prudent decision for minimizing downtime, enhancing workplace safety, and boosting overall operational efficiency.
1. Understanding Manufacturing Downtime and Its Financial Impact
Before exploring the solutions, it's crucial to grasp the significant impact of downtime. Downtime refers to any period when production machinery or a line is not operational. Common causes include equipment breakdowns, scheduled maintenance, tooling changeovers, and inefficient material handling – such as manually rotating heavy molds.
In industries reliant on molds and dies (e.g., plastic injection molding, die casting, stamping, forging), manipulating these heavy tools is often a bottleneck. Manual methods involving cranes, forklifts, and multiple personnel are inherently slow and pose risks. Every minute spent wrestling a mold is a minute lost from value-added production. Industry studies suggest unplanned downtime can cost manufacturers significantly, potentially reaching thousands or even hundreds of thousands of dollars per hour depending on the scale and sector ([Authoritative Source on Downtime Costs - e.g., Link to Industry Report or Study]). Automating repetitive, time-consuming tasks like mold turning with dedicated mold handling equipment directly addresses this challenge, saving valuable production time and mitigating risks.
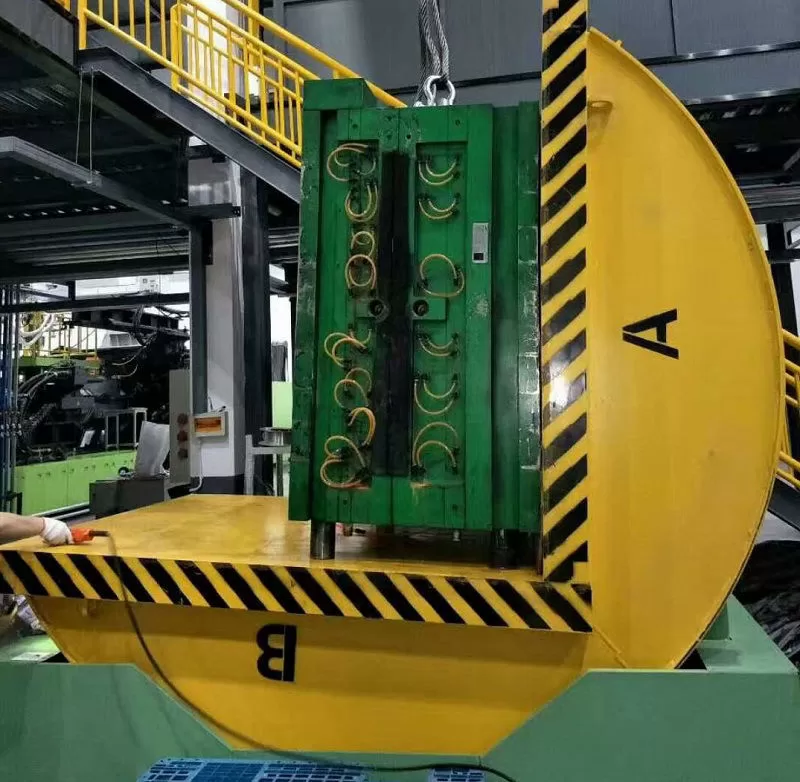
2. The Role of Mold Rotators in Modern Manufacturing Operations
A mold rotator is purpose-built mechanical or hydraulic equipment designed to safely and efficiently rotate, tilt, or invert large, heavy molds and dies with minimal manual intervention. This specialized machinery is essential for tasks like mold maintenance, cleaning, inspection, and setup, reducing reliance on general-purpose lifting equipment and manual labor.
Key characteristics and capabilities of modern mold rotators often include:
- High Load Capacity: Engineered to handle substantial weights, often ranging from a few tons to over 50 tons, accommodating a wide variety of mold sizes.
- Precise Rotation Control: Typically offer controlled rotation (e.g., 90°, 180°, or custom angles) powered electrically or hydraulically, ensuring accurate positioning for maintenance access or press insertion.
- Robust Construction: Built for industrial environments with heavy-duty frames and reliable drive systems.
- Enhanced Safety Features: Incorporate mechanisms like locking systems, controlled speed, and remote operation to prevent accidents associated with manual handling or less stable methods.
- Versatile Designs: Available in various configurations (e.g., C-frame, pit-mounted, mobile) to suit different facility layouts and workflow requirements.
Investing in the right mold handling equipment yields numerous advantages, with the most immediate being a quantifiable reduction in downtime during mold changeovers and maintenance cycles.
3. How Mold Rotators Directly Minimize Production Downtime
The primary driver for adopting mold rotators is their ability to drastically cut down the time associated with mold handling tasks. Traditional methods often involve:
- Securing the mold with slings or chains.
- Using an overhead crane or forklift for lifting and turning.
- Requiring multiple personnel for spotting and maneuvering.
- Significant risk of delays due to balancing issues or needing repositioning.
This entire process can take hours and introduces considerable variability.
A mold rotator streamlines this workflow dramatically. Consider this comparison:
- Manual/Crane Method: Rotating a 10-ton mold might take 2-3 workers 1-2 hours, including setup and safety checks.
- Mold Rotator Method: The same task can often be completed by a single operator in 10-20 minutes.
This time saving directly translates to reduced machine downtime during changeovers. This efficiency aligns with Lean Manufacturing principles like Single-Minute Exchange of Die (SMED), aiming to reduce setup times to mere minutes. Faster, more predictable mold handling means less time waiting and more time producing. Furthermore, the precision control minimizes errors during rotation that could necessitate rework or cause further delays.
4. Enhancing Workplace Safety with Automated Mold Handling
Handling heavy, cumbersome molds manually or with makeshift setups is inherently risky. Potential hazards include:
- Musculoskeletal injuries from lifting, pushing, or pulling.
- Crushing injuries if a mold slips or falls.
- Damage to the expensive mold itself due to impacts or improper support.
OSHA and other safety bodies emphasize engineered controls to mitigate such risks ([Authoritative Source - e.g., Link to OSHA Ergonomics or Material Handling Guidelines]). A mold rotator serves as a prime example of such an engineering control.
Key Safety Benefits:
- Reduces Manual Handling: Minimizes direct physical contact and exertion by workers.
- Controlled Movement: Ensures smooth, stable rotation, preventing sudden shifts or drops.
- Secure Clamping: Holds the mold firmly in place during the entire process.
- Reduced Operator Proximity: Often allows operation from a safe distance via pendants or remote controls.
By automating this hazardous task, manufacturers significantly lower the risk of workplace injuries, potentially reducing workers' compensation claims and improving overall facility safety culture. A safer environment also boosts employee morale and can contribute to better retention rates.
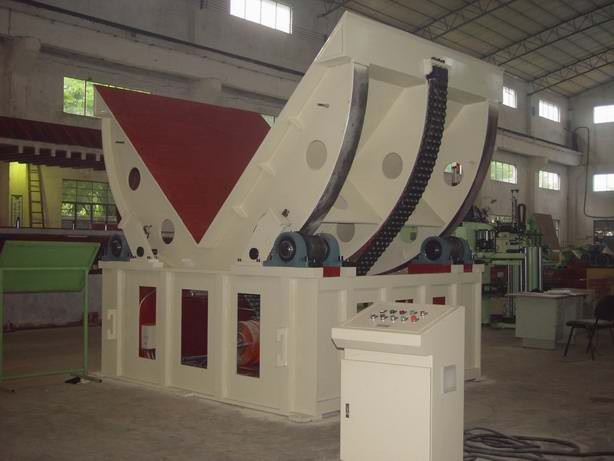
5. Improving Overall Production Efficiency and Throughput
Operational efficiency is critical for competitiveness. Faster, safer mold handling directly contributes to higher efficiency and throughput.
- Quicker Changeovers: Reduced setup time means production lines restart faster, increasing machine utilization and overall output.
- Optimized Labor Allocation: Frees up skilled workers previously tied up in manual mold handling, allowing them to focus on other value-added tasks like machine operation, quality control, or preventive maintenance.
- Improved Workflow: Creates a more predictable and streamlined process for mold maintenance and changeovers.
- Enhanced Mold Care: Proper handling reduces the chance of accidental damage, ensuring molds are ready for production runs without unexpected repair delays.
The precision offered by mold rotators also ensures molds are correctly oriented for maintenance or installation, preventing misalignment issues that could lead to production defects or further stoppages. These cumulative effects significantly boost overall operational efficiency (OEE).
6. Reducing Mold Maintenance Costs and Equipment Wear
Molds and dies represent substantial capital investments. Protecting these assets is crucial. Manual handling or using inappropriate equipment like forklifts for turning increases the risk of:
- Scratches, dents, or cracks on mold surfaces.
- Damage to delicate components like slides, lifters, or cooling channels.
- Misalignment of mold halves.
Such damage necessitates costly repairs and leads to extended, unplanned downtime.
A mold rotator provides a controlled, secure, and gentle method for handling. The even support and smooth rotation minimize stress on the mold structure, significantly reducing the risk of accidental damage. This translates directly to:
- Lower repair costs.
- Extended mold lifespan.
- Reduced need for premature replacement.
Additionally, relying less on overhead cranes or forklifts for this specific task reduces wear and tear on that equipment, potentially lowering their maintenance costs and freeing them for tasks they are better suited for.
7. Calculating the Long-Term Return on Investment (ROI) for Mold Rotators
While a mold rotator requires an initial capital investment, evaluating its long-term ROI reveals its financial viability. The benefits accumulate over time, often resulting in a payback period of just a few years.
Factors contributing to a positive ROI include:
- Increased Production Output: Direct result of reduced downtime during changeovers.
- Reduced Labor Costs: Fewer personnel needed for mold handling tasks.
- Lower Mold Repair/Replacement Costs: Due to safer, damage-free handling.
- Reduced Injury-Related Costs: Savings on workers' compensation and lost time due to accidents.
- Improved Product Quality: Fewer production issues caused by mold damage or misalignment.
Manufacturers performing frequent mold changes or dealing with particularly large/heavy molds typically see the fastest ROI. A thorough cost-benefit analysis, considering current handling times, labor rates, downtime costs, and potential safety incident costs, will typically demonstrate the compelling financial case for investing in a mold rotator.
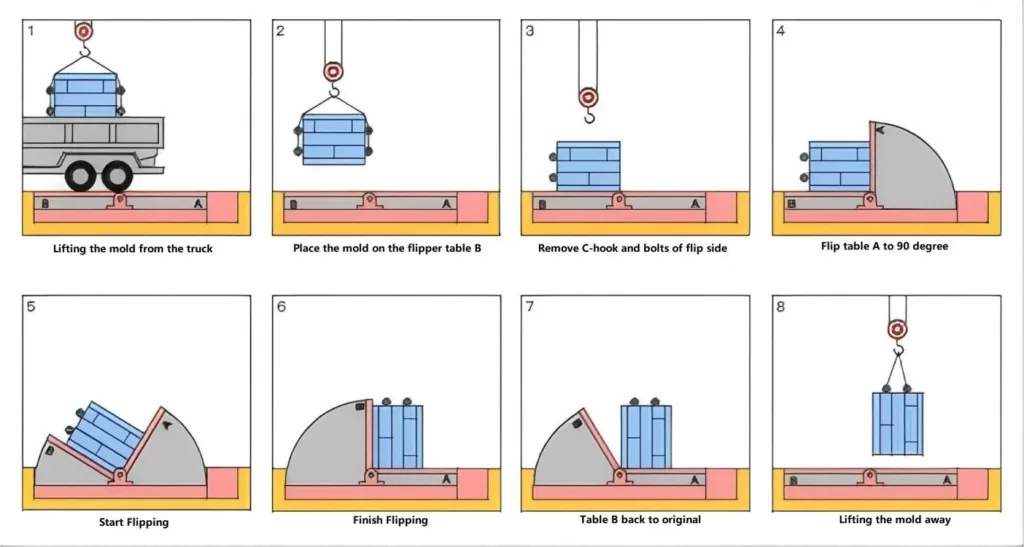
8. Conclusion: A Smart Investment for Forward-Thinking Manufacturers
In a competitive global market, optimizing every aspect of the manufacturing process is essential. Reducing non-value-added time, enhancing safety, and protecting expensive tooling are critical objectives. Investing in specialized mold handling equipment like a mold rotator addresses all these points effectively.
It provides a safer, faster, and more reliable method for handling molds and dies compared to traditional techniques. The resulting benefits – minimized downtime, improved worker safety, increased production efficiency, reduced maintenance costs, and a strong long-term ROI – make it a strategically sound investment.
For manufacturers looking to streamline operations, boost productivity, and foster a safer working environment, adopting automated mold handling solutions is no longer a luxury but a necessity for sustained success and competitiveness.

Get Your Best Solution !