Minimizing Downtime: Why Investing in a Coil Upender is a Smart Choice
In industries handling heavy materials like steel, aluminum, or wire coils, maintaining operational efficiency and ensuring workplace safety are paramount. A significant challenge is minimizing downtime – any period where production stops due to equipment issues, process inefficiencies, or safety incidents. This is where specialized material handling equipment, such as a coil upender, becomes a crucial asset in the manufacturing workflow.
A coil upender, also known as a coil tilter, is engineered to safely and efficiently rotate or flip heavy coils between horizontal ("eye-to-sky") and vertical ("eye-to-the-wall") orientations. Investing in this equipment delivers substantial benefits, including drastically reduced downtime, enhanced worker safety, and increased overall productivity. This article delves into the vital role of a coil upender in modern industrial settings, outlines the operational challenges it overcomes, and clarifies why it represents a strategic investment for optimizing manufacturing operations.
1. What is a Coil Upender and Its Function?
A coil upender is a purpose-built machine designed to tilt or rotate cylindrical coils, typically made of metal, from a horizontal to a vertical position, or vice versa. This repositioning is essential for various stages in the production cycle, including storage, transportation, loading onto machinery (like slitters or presses), or preparing for packaging processes.
Traditionally, manual or makeshift methods for handling coils are not only labor-intensive and slow but also inherently risky. A coil upender automates this critical task, facilitating faster, safer, and more controlled coil movements. Whether dealing with steel, aluminum, copper, or paper coils, this equipment significantly streamlines handling logistics and minimizes the need for manual intervention.
By employing a coil upender, manufacturers ensure precise coil positioning, which is crucial for subsequent operations such as automated wrapping, strapping, slitting, or efficient loading/unloading. This automated tilting process reduces the potential for human error, drastically lowers the risk of injuries associated with manual handling, and accelerates the overall material flow, directly contributing to minimized production downtime.
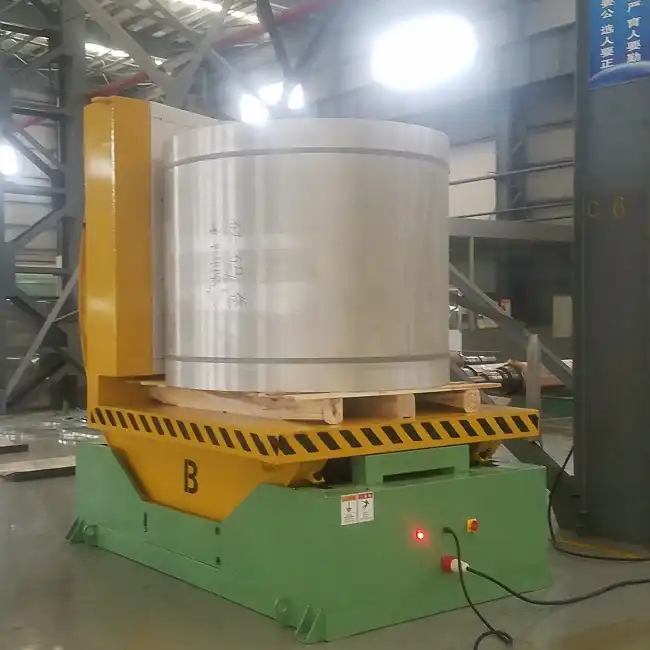
2. The High Cost of Downtime in Coil Processing
In the competitive landscape of manufacturing, downtime is a direct drain on productivity and profitability. It represents any time a machine, process, or production line is idle or non-operational. This directly impacts output, hinders the ability to meet production schedules, and ultimately erodes the bottom line.
Several factors related to coil handling frequently contribute to costly downtime:
- Manual Handling Inefficiencies: Without automated solutions like a coil upender, repositioning heavy coils requires significant time, manpower, and often involves cumbersome equipment like cranes or forklifts, leading to delays and bottlenecks.
- Safety Incidents and Injuries: Manually manipulating multi-ton coils poses severe risks to workers, including strains, crush injuries, and falls. Accidents result in immediate production halts, potential regulatory fines, increased insurance premiums, and significant worker compensation costs.
- Equipment Damage and Material Waste: Improper handling can damage both the coil material (e.g., edge damage, telescoping) and the handling equipment itself, leading to costly repairs, material scrap, and unplanned maintenance interruptions.
- Inefficient Changeovers: Slow coil repositioning between processes (e.g., moving from storage to a slitting line) extends changeover times, further reducing valuable production uptime.
Investing in a coil upender directly mitigates these issues. The machine's ability to perform the heavy lifting and precise tilting in a controlled, automated manner significantly reduces the time required for coil manipulation, allowing production lines to operate more continuously and efficiently.
3. Key Advantages of Integrating a Coil Upender
A coil upender offers several compelling advantages that make it a strategic investment for businesses aiming to optimize operations and slash downtime:
- Increased Efficiency and Throughput: By automating the tilting process, a coil upender dramatically cuts down the time and labor needed to handle heavy coils. This acceleration in material flow allows production lines to run faster and smoother, boosting overall throughput and capacity. This is especially critical in high-volume environments where minimizing non-value-added time is essential for competitiveness.
- Improved Workplace Safety and Ergonomics: Safety is arguably the most significant benefit. A coil upender eliminates the need for direct manual handling of potentially hazardous heavy coils, substantially reducing the risk of severe worker injuries. The controlled, mechanical rotation prevents accidents associated with load instability or operator error. This focus on safety not only protects employees but also reduces costs related to injuries, insurance, and lost workdays, fostering a safer work environment.
- Enhanced Consistency and Precision: Manual coil handling often leads to inconsistent positioning, which can cause problems in downstream processes (e.g., misalignment on a payoff reel) or even damage the coil. A coil upender ensures repeatable, precise positioning every time, contributing to process stability and quality control. This consistency minimizes errors, reduces material waste from handling damage, and prevents disruptions in the production flow, helping maintain steady and predictable output rates.
- Protection of Coil Material: Gentle and controlled rotation minimizes the risk of damage to the coil edges or surfaces, which can occur with less sophisticated handling methods. This is particularly important for sensitive materials like aluminum or coated steel, preserving material integrity and reducing scrap rates.
4. Essential Features and Customization Options for Coil Upenders
Coil upenders are highly effective partly because they can be tailored with specific features to match diverse industrial applications and coil types. Customization ensures the equipment performs optimally within a specific operational context.
Common customizable features and considerations include:
- Load Capacity: Available in various capacities, from models handling lighter coils (e.g., under 5 tons) to heavy-duty units capable of manipulating coils weighing 30 tons or more. Selecting the correct capacity is crucial for safety and longevity.
- Platform Size and Configuration: The platform (or cradle) that supports the coil can be designed to accommodate specific coil diameters and widths. Options like V-saddles or flat platforms, sometimes with protective padding (e.g., polyurethane), ensure secure and damage-free handling.
- Rotation Angle: Most upenders provide 90-degree rotation, but some applications might require different angles or even full 180-degree inversion capabilities.
- Automation and Control Systems: Options range from simple pendant controls for semi-automated operation to fully integrated automated systems that interface with conveyors, AGVs, or production line controls, requiring minimal operator intervention. PLC controls allow for programmable operation sequences.
- Safety Features: Essential features include robust structural design, limit switches, emergency stop buttons, hydraulic or electromechanical locking mechanisms, safety barriers or light curtains, and load detection sensors to prevent overloading or unsafe operation.
- Power Source: Typically powered by electro-hydraulic systems, though fully electromechanical designs are also available, offering choices based on facility infrastructure and maintenance preferences.
Choosing the right configuration ensures the coil upender seamlessly integrates into the workflow and delivers maximum efficiency and safety benefits.
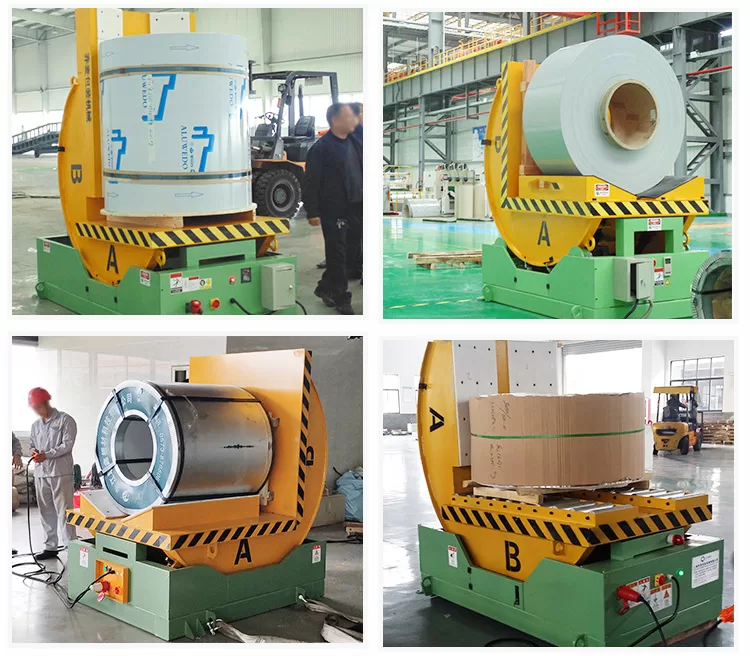
5. Calculating the Return on Investment (ROI) for a Coil Upender
While the initial capital expenditure for a coil upender can be substantial, the long-term cost savings and quantifiable return on investment (ROI) often justify the purchase. The ROI stems from multiple areas:
- Reduced Labor Costs: Automating coil tilting reduces the manual labor required for this task, freeing up personnel for more value-added activities and potentially lowering overall labor expenses.
- Minimized Downtime Costs: Faster and more reliable coil handling directly translates to increased production uptime. Calculating the cost of downtime per hour and comparing it to the efficiency gains provides a clear picture of savings.
- Lower Maintenance and Repair Costs: Controlled handling reduces wear and tear on both the coils and other production equipment (e.g., preventing damage to processing lines from poorly positioned coils), leading to lower maintenance costs over time.
- Reduced Costs Associated with Accidents: Fewer workplace injuries mean lower insurance premiums, reduced worker compensation claims, and avoidance of potential fines and litigation costs.
- Decreased Material Scrap: Protecting coils from handling damage reduces material waste and the associated costs.
By quantifying these savings relative to the initial investment, businesses often find that a coil upender delivers a compelling ROI through improved productivity, safety, and reduced operational expenditures (OPEX).
6. Selecting the Right Coil Upender for Your Operations
Choosing the most suitable coil upender requires careful consideration of your specific operational needs. Key factors to evaluate include:
- Coil Specifications: Document the range of materials (steel, aluminum, copper, paper, etc.), minimum and maximum weights, diameters, and widths of the coils you handle. This determines the required capacity and platform design.
- Production Volume and Frequency: Assess how often coils need to be repositioned. High-volume operations benefit significantly from fully automated, high-speed models, while lower-frequency needs might be met by semi-automated units.
- Facility Layout and Space Constraints: Measure the available footprint for the machine and consider how it will integrate with existing material flow paths, conveyors, cranes, or forklift traffic patterns.
- Integration Requirements: Determine if the upender needs to communicate with other automated systems or production line controls (e.g., signaling readiness, receiving commands).
- Safety Standards: Ensure the chosen equipment complies with relevant industry and regional safety regulations (e.g., OSHA, CE marking).
- Budget vs. Long-Term Value: Balance the initial purchase price against the anticipated long-term cost savings (ROI) from reduced downtime, labor, and accidents. Consider the total cost of ownership, including maintenance and energy consumption.
Thoroughly assessing these factors will guide you toward selecting a coil upender that provides optimal performance, safety, and value for your unique manufacturing environment.
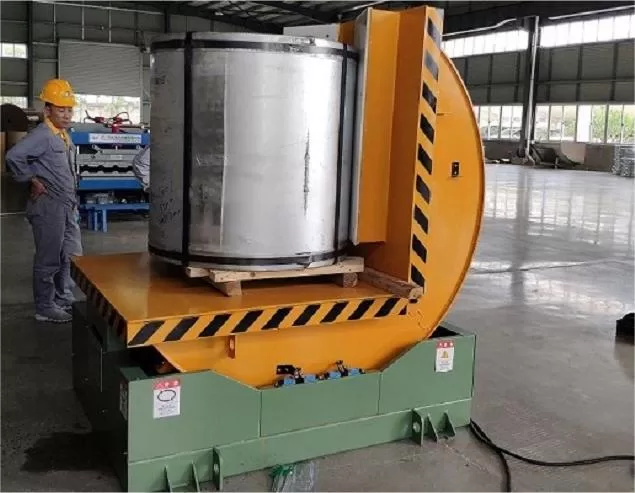
Conclusion: Boost Efficiency and Safety by Investing in a Coil Upender
In today's demanding manufacturing climate, minimizing downtime and ensuring worker safety are not just goals but operational necessities for maintaining competitiveness and profitability. A coil upender provides a robust solution to the challenges of handling heavy coils, offering tangible benefits ranging from increased operational efficiency and throughput to significantly improved worker safety and reduced labor dependency.
By automating the critical process of tilting and rotating heavy coils, businesses can achieve smoother, faster, and more reliable production flows with fewer costly disruptions. Investing in a coil upender is a strategic decision to optimize material handling operations, protect valuable assets (both personnel and materials), and enhance the overall resilience of the production line. With customizable options available to meet specific industrial needs, a well-chosen coil upender represents an investment that delivers substantial returns through enhanced productivity, minimized downtime, and long-term operational cost savings.