Market Research Insights: Choosing the Right Orbital Wrapping Machine
- Market Research Insights: Choosing the Right Orbital Wrapping Machine
- 1. Understanding the Purpose of an Orbital Wrapping Machine
- 2. Key Considerations in Choosing the Right Orbital Wrapping Machine
- 3. Market Trends in Orbital Wrapping Machines
- 4. Comparing Top Orbital Wrapping Machine Models
- 5. Cost Considerations: Total Cost of Ownership
- 6. Key Industries Benefiting from Orbital Wrapping Machines
- 7. How to Choose the Best Supplier for Orbital Wrapping Machines
- 8. Conclusion
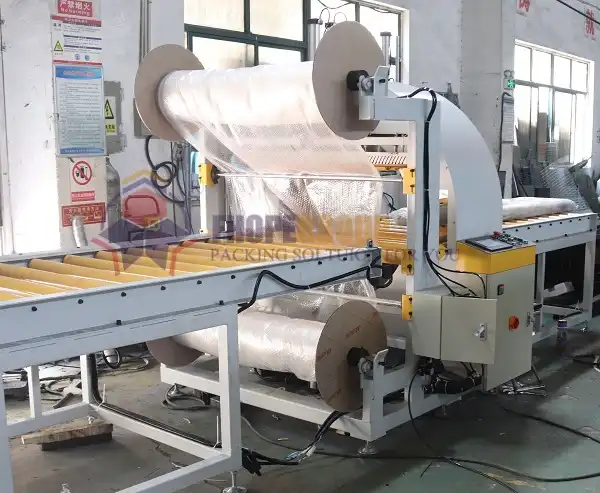
Choosing the right orbital wrapping machine is a strategic decision that can significantly impact your packaging efficiency, product protection, and overall operational costs. With a variety of models and technologies available on the market, it’s crucial to understand the specific factors that will guide you toward the most suitable option for your needs. This market research insight aims to provide a comprehensive guide to help you make an informed choice, ensuring your investment aligns with your business objectives.
1. Understanding the Purpose of an Orbital Wrapping Machine
An orbital wrapping machine is designed to secure products using stretch film by wrapping it around the items in a circular or orbital motion. This technology is particularly beneficial for packaging long, bulky, or irregularly shaped items such as pipes, profiles, wooden planks, or even doors. The machine ensures that products are fully enclosed in protective wrapping, safeguarding them from environmental elements, handling damage, and other potential risks during storage or transportation.
This type of packaging machinery is a game-changer for industries looking to boost efficiency, minimize labor, and enhance the durability of their packaging solutions.
2. Key Considerations in Choosing the Right Orbital Wrapping Machine
When selecting the right orbital wrapping machine, it’s important to evaluate your specific business needs, packaging requirements, and long-term goals. Here are the essential factors to consider:
2.1 Product Size and Shape Compatibility
Your product dimensions, particularly their length, width, and height, play a crucial role in determining which machine will suit your needs. Orbital wrapping machines come in different sizes and capacities, so it’s essential to choose a model that can accommodate your largest products. For example, businesses dealing with metal pipes or aluminum profiles should prioritize machines with larger orbital diameters.
2.2 Production Volume
The volume of products you need to package daily is another critical factor. High-production environments benefit from machines with faster wrapping speeds and automated features. Fully automatic orbital wrapping machines are best suited for continuous production lines, whereas semi-automatic models are ideal for smaller-scale operations.
2.3 Level of Automation
Orbital wrapping machines are available in manual, semi-automatic, and fully automatic models. The level of automation required largely depends on your operational needs and the volume of packaging. Fully automated machines offer higher efficiency and require minimal human intervention, while semi-automatic models provide a balance between cost-effectiveness and productivity for businesses with moderate packaging needs.
2.4 Film Type and Cost
The type of stretch film used is another important consideration. Different machines are compatible with various types of films, from standard polyethylene stretch film to high-performance films designed for specific protection needs. Additionally, the cost of film over time can add up, so finding a machine that optimizes film usage and reduces waste is crucial for cost savings in the long run.
2.5 Durability and Maintenance Requirements
Investing in an orbital wrapping machine is a long-term decision. Therefore, evaluating the durability of the machine and its maintenance requirements is essential. Machines constructed from high-quality materials and with fewer complex components generally offer a longer lifespan and require less frequent maintenance.
3. Market Trends in Orbital Wrapping Machines
As industries continue to focus on optimizing their packaging lines, several key trends have emerged in the orbital wrapping machine market. Staying ahead of these trends can help you choose a machine that not only meets your current needs but also positions your business for future growth.
3.1 Increased Automation and Smart Technology Integration
The demand for automation has been on the rise across industries, with packaging being no exception. Many modern orbital wrapping machines now come equipped with smart technology, including programmable logic controllers (PLCs), touch-screen interfaces, and remote monitoring capabilities. These advancements allow for greater control over the wrapping process, enhanced efficiency, and better data-driven decision-making.
3.2 Sustainability and Eco-Friendly Packaging
Sustainability is an increasingly important factor for businesses worldwide. Companies are looking for machines that reduce film usage and offer more eco-friendly packaging options. This is driving the development of machines that can handle thinner, more environmentally friendly films while still providing robust protection for products.
3.3 Customization and Modular Design
Customization is becoming more prevalent as businesses look for machines that can be tailored to their specific needs. Modular design features allow companies to add or remove features based on their production requirements. Whether it’s upgrading to a fully automatic system or adding a pallet wrapping function, these machines can grow and evolve with your business.

Get Your Best Solution !
4. Comparing Top Orbital Wrapping Machine Models
The market is filled with various models of orbital wrapping machines, each offering different features and benefits. Here are some key differences to look for when comparing different models:
4.1 Entry-Level vs. High-End Models
Entry-level orbital wrappers are typically more affordable and have fewer features, making them suitable for small or medium-sized businesses with lower packaging needs. They are often semi-automatic, requiring some operator intervention. On the other hand, high-end models are fully automated, feature advanced control systems, and are designed for high-volume production lines. These models offer faster wrapping speeds, better film tension control, and enhanced product protection.
4.2 Manual vs. Automatic Tension Control
Tension control is a critical feature that ensures the film is applied tightly enough to secure the product but not so tight that it causes damage. Manual tension control requires the operator to adjust the tension settings, while automatic tension control allows the machine to adjust based on the product’s size and weight, ensuring consistent wrapping quality.
4.3 Film Efficiency Features
Some machines are designed with advanced film-saving technologies that minimize waste by optimizing how much film is used. Look for models that offer pre-stretch mechanisms, which stretch the film before it is applied, resulting in greater film coverage with less material.
5. Cost Considerations: Total Cost of Ownership
When evaluating the cost of an orbital wrapping machine, it’s important to go beyond the initial purchase price and consider the total cost of ownership (TCO). This includes factors like energy consumption, film costs, maintenance requirements, and potential downtime.
5.1 Initial Purchase Price
While entry-level models are more affordable upfront, they may not offer the same level of efficiency or durability as higher-end machines. It’s important to balance your budget with long-term operational needs.
5.2 Operational Costs
The cost of running an orbital wrapping machine includes film usage, energy consumption, and labor (if the machine is not fully automated). Look for machines that optimize these factors to minimize ongoing expenses.
5.3 Maintenance and Spare Parts
Routine maintenance is necessary to ensure long-term functionality and minimize downtime. When selecting a machine, inquire about the availability and cost of spare parts, as well as the ease of maintenance. Machines from reputable manufacturers often come with robust service contracts and easy access to OEM parts.
6. Key Industries Benefiting from Orbital Wrapping Machines
Several industries have found significant benefits in adopting orbital wrapping machines as part of their packaging lines. Here are some of the leading sectors that use these machines:
6.1 Construction Materials Industry
For companies that deal with long, heavy items like pipes, beams, or tubing, orbital wrapping machines offer a perfect solution for protecting products during transport and storage.
6.2 Furniture and Wood Products Industry
The furniture and wood industry requires secure and tight packaging for delicate or large items. Orbital wrappers ensure products are wrapped without damage and protected from environmental elements.
6.3 Metal and Fabrication Industry
Metal rods, profiles, and sheets often require tight, secure packaging to prevent corrosion and damage. Orbital wrapping machines are ideal for applying durable protective film to these products.
7. How to Choose the Best Supplier for Orbital Wrapping Machines
Choosing the right supplier is just as important as selecting the right machine. Here are some tips to ensure you work with a reputable supplier:
7.1 Reputation and Reviews
Look for suppliers with a proven track record of delivering high-quality machines and excellent customer service. Online reviews, industry referrals, and case studies are good indicators of a supplier’s reliability.
7.2 Service Contracts and Support
Make sure the supplier offers comprehensive after-sales support, including service contracts, technical support, and training for your staff. A supplier that provides OEM parts and has a local service presence is often the best choice for long-term maintenance.
7.3 Customization Options
If your business requires specific features or modifications, look for suppliers that offer customization options or modular designs. A flexible approach to machine design can help you future-proof your investment.
8. Conclusion
Choosing the right orbital wrapping machine requires a thorough understanding of your packaging needs, the latest market trends, and the available technology. By carefully assessing factors like product size, production volume, and automation requirements, you can make an informed decision that improves your packaging efficiency and lowers your operational costs. As the market continues to evolve, staying ahead of trends such as increased automation, sustainability, and modular designs will ensure your business remains competitive.
By partnering with the right supplier and investing in a machine tailored to your specific needs, your business can reap the benefits of enhanced packaging efficiency, reduced material waste, and improved product protection.

Get Your Best Solution !