Market Analysis: Choosing the Right Horizontal Wrapping Machine for Efficiency
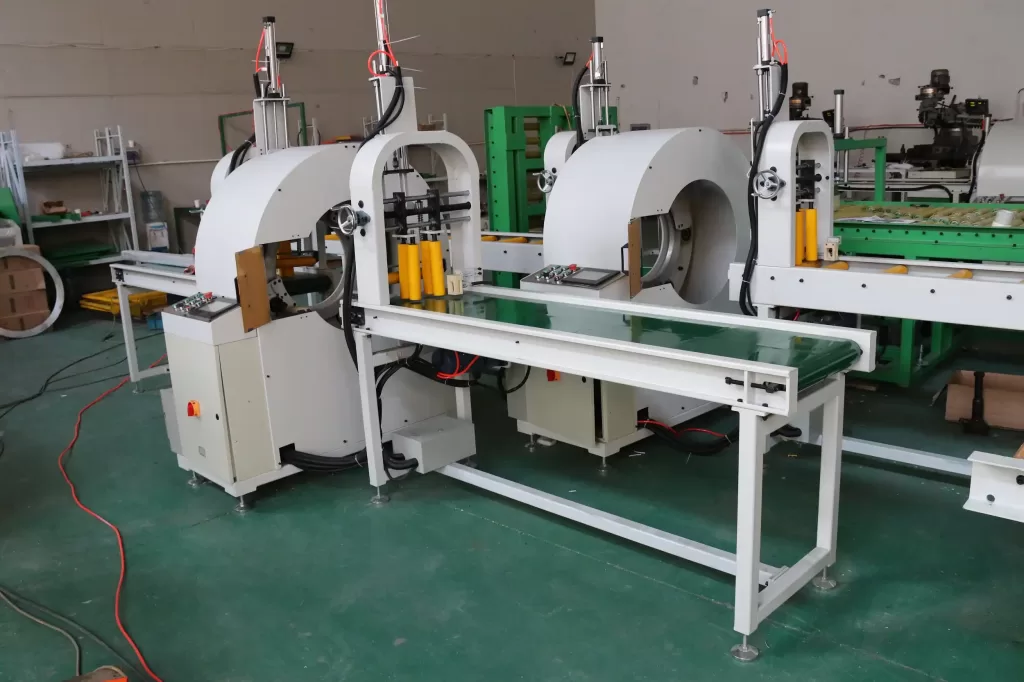
Introduction
In today’s competitive industrial landscape, maximizing efficiency is paramount. For businesses involved in packaging and shipping, selecting the right equipment significantly impacts operational flow, labor costs, and product protection during transit. A horizontal wrapping machine, also known as a horizontal stretch wrapper, is a vital piece of equipment that can dramatically enhance productivity, especially for long or bulky items. However, choosing the most suitable model requires careful consideration of machine capabilities, product characteristics, production volume, and specific business needs.
This guide provides a comprehensive analysis to help you select the optimal horizontal wrapping machine, ensuring you invest in a solution that boosts efficiency and delivers long-term value for your operations.
1. Understanding Horizontal Wrapping Machines: Types and Functions
Before evaluating specific models, it's essential to grasp the fundamentals of horizontal wrapping machines. These automated or semi-automated systems are engineered to apply stretch film or other wrapping materials around products positioned horizontally. The primary wrapping process secures items for storage or shipment and shields them from dust, moisture, potential damage, and other environmental factors. Horizontal wrappers are particularly effective for packaging long items such as pipes, lumber, extrusions, profiles, textiles, and bundled goods, though their versatility extends to various product types across different industries.
Key Types of Horizontal Wrapping Machines:
Understanding the different types available is the first step in narrowing down your options:
- Semi-automatic Horizontal Wrapping Machines: These require an operator to initiate the wrapping cycle, position the product, and cut the film. They are well-suited for low to medium production volumes where flexibility is needed, offering a balance between automation and manual control.
- Fully Automatic Horizontal Wrapping Machines: Designed for high-volume operations, these machines integrate seamlessly into production lines. They automate the entire process, including product feeding, wrapping, film cutting, and sealing, minimizing labor requirements and maximizing throughput.
- Orbital Horizontal Wrapping Machines: These specialized wrappers use a ring that orbits around the product, applying film tightly and securely. They are ideal for wrapping long, bulky, or irregularly shaped items, ensuring complete coverage and stability.
The best choice depends critically on your production scale, product dimensions and shape, required wrapping speed, and desired level of automation.

2. Essential Features: What Defines a High-Efficiency Horizontal Wrapper?
When comparing horizontal wrapping machines, prioritize these key features to ensure the equipment aligns with your operational demands for optimal efficiency and reliability:
- Wrapping Speed and Throughput: Evaluate the machine's cycles per minute or hour. Ensure it can meet or exceed your current and anticipated future production demands. High throughput is crucial for fast-paced environments.
- Machine Durability and Construction: Look for machines built with high-quality materials and robust construction. Industrial environments demand equipment that can withstand continuous operation with minimal wear and tear.
- Level of Automation: Consider the degree of automation needed. Fully automatic systems offer the highest efficiency and reduce labor costs, contributing to a faster return on investment (ROI), while semi-automatic models provide more flexibility for varied tasks.
- Product Size Capacity: Verify the machine's specifications regarding minimum and maximum product length, width, and height (or diameter for orbital wrappers) it can handle. Ensure it accommodates your entire product range.
- Wrapping Material Compatibility: Check if the machine works efficiently with different types and thicknesses of stretch film or other wrapping materials (e.g., VCI film, paper). Flexibility in material choice can be advantageous.
- Control System and Ease of Use: An intuitive interface, programmable logic controller (PLC), and easy-to-adjust settings reduce operator training time and minimize errors. Touchscreen controls are increasingly standard.
- Safety Features: Essential for any automated machinery. Look for features like emergency stops, safety guards, light curtains, and clear warning indicators to protect operators and comply with safety regulations.
3. Current Market Trends: Automation, Sustainability, and IoT
The horizontal wrapping machine market is continually evolving, driven by industry demands for greater efficiency, flexibility, and intelligence:
- Increased Automation: Automation trends remain dominant, with fully automatic wrappers becoming more sophisticated and accessible. Robotic integration for loading and unloading is also gaining traction in high-volume settings.
- Focus on Sustainability: There's a growing demand for machines compatible with thinner gauge films and eco-friendly packaging materials, such as recyclable or biodegradable options. Efficient film usage (pre-stretch capabilities) also reduces waste.
- IoT Integration: The adoption of IoT (Internet of Things) technology is rising. Smart wrappers can provide real-time data on performance, material consumption, and maintenance needs. This enables predictive maintenance, remote diagnostics, and better operational oversight.
- Customization and Modularity: Manufacturers increasingly offer modular designs and customization options to tailor machines precisely to specific application requirements.
Staying informed about these trends helps ensure your investment is future-proof and aligns with modern manufacturing practices.
4. Tailoring the Choice: Industry-Specific Wrapping Needs
The ideal horizontal wrapping machine varies significantly depending on the industry and the products being handled:
- Construction, Timber, and Metals: These sectors frequently handle long, heavy products like lumber, pipes, steel profiles, and aluminum extrusions. They require heavy-duty, robust orbital wrappers capable of managing significant weight and length, often with specialized infeed and outfeed conveyors.
- Manufacturing (General): Manufacturers of items like cables, hoses, textiles, furniture components, or assembled goods need versatile machines. Depending on volume, semi-automatic or fully automatic systems might be appropriate. Orbital wrappers are often used for coiled products.
- Logistics and Distribution: Warehouses and fulfillment centers use horizontal wrappers to prepare diverse products for shipping. Key priorities include speed, reliability, and the ability to handle various product sizes efficiently to minimize packaging time and ensure load security during transit.
- Windows and Doors: This industry requires careful handling to protect surfaces. Wrappers often need features like top pressure plates or specialized conveyors to stabilize products and ensure a secure, damage-free wrap.
Understanding the specific challenges and requirements of your industry is crucial for selecting a machine that truly enhances efficiency.
5. Key Factors Driving Wrapping Machine Efficiency
Beyond basic features, several factors directly influence the day-to-day operational efficiency of a horizontal wrapping machine:
- Machine Speed and Cycle Time: As mentioned, higher speeds directly translate to increased throughput. However, ensure the speed doesn't compromise wrap quality or stability. Consistent, reliable speed is key.
- Ease of Use and Operator Training: Intuitive controls and clear operating procedures reduce the learning curve and minimize potential errors. Quick setup and changeover between different product sizes also boost efficiency.
- Maintenance Requirements and Downtime: Choose machines known for reliability and minimal maintenance needs. Easy access to components for routine checks and readily available spare parts are critical for reducing downtime. Consider maintenance service agreements.
- Film Pre-Stretch Capability: Machines with powered pre-stretch systems can stretch the film significantly (e.g., 200-300%) before application. This maximizes film yield, reduces material costs per wrap, and provides a more secure load containment.
- Product Handling and Versatility: The ability to easily adjust guides, conveyors, and wrapping parameters to accommodate a wide range of product sizes and shapes provides operational flexibility and maximizes machine utilization, especially if your product mix varies.
The most efficient machine is often the one that optimally balances speed, reliability, ease of use, material efficiency, and versatility for your specific application.
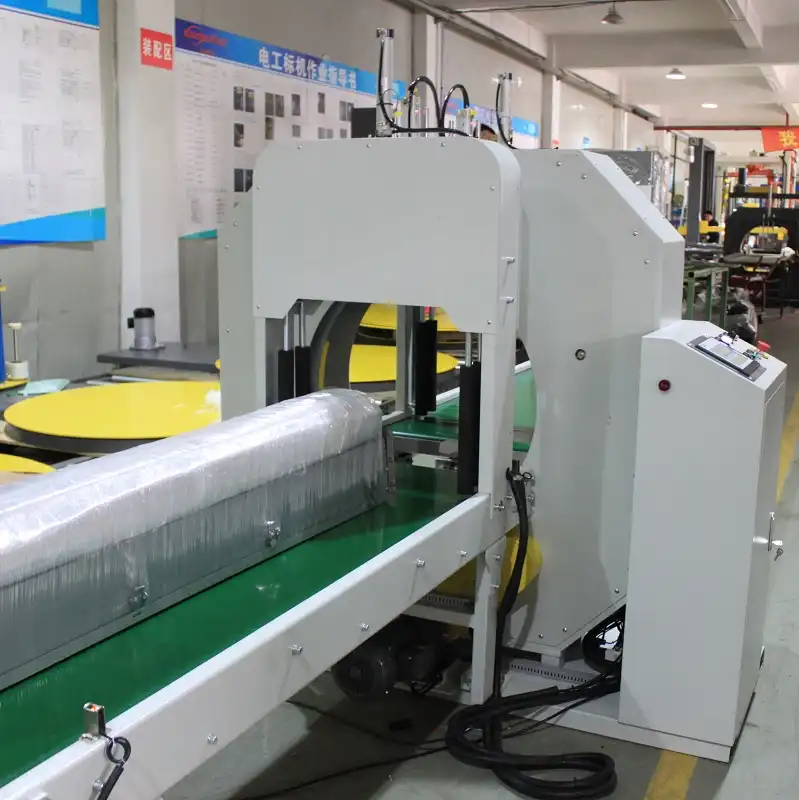
6. Balancing Cost and Efficiency: Calculating True ROI
While operational efficiency is a primary goal, the investment cost is always a key consideration. Cost-effectiveness extends beyond the initial purchase price; evaluate the Total Cost of Ownership (TCO):
- Initial Purchase Cost: Fully automatic, high-speed, or highly customized machines have a higher upfront cost but often yield better long-term ROI through labor savings, increased throughput, and material efficiency.
- Operating Costs: Factor in energy consumption (look for energy-efficient motors and drives), compressed air usage (if applicable), and wrapping material costs. High pre-stretch ratios significantly lower film costs over time.
- Labor Costs: Automation level directly impacts labor requirements. Calculate the savings from reduced manual handling and operator time.
- Maintenance Costs: Consider the cost of routine maintenance, spare parts, and potential downtime. Reliable machines with good manufacturer support minimize these costs.
Analyze the expected payback period and long-term ROI by comparing the TCO against the anticipated efficiency gains and cost savings.
7. Avoiding Pitfalls: Common Mistakes in Machine Selection
Selecting the wrong horizontal wrapping machine can lead to inefficiency, higher costs, and operational headaches. Avoid these common mistakes:
- Ignoring Future Scalability: Choosing a machine that only meets current needs without considering potential business growth can lead to needing a replacement sooner than expected. Opt for models with some capacity for increased volume or size variations.
- Underestimating Maintenance and Support: Neglecting to investigate the ease of maintenance, availability of parts, and quality of manufacturer support can result in prolonged downtime and lost productivity.
- Focusing Solely on Price: The cheapest machine isn't always the best value. Lower-priced models might lack durability, efficiency features (like pre-stretch), or adequate safety measures, leading to higher operating costs and potential safety risks.
- Insufficient Product Testing: Failing to test the machine with your specific products (especially challenging ones) can lead to unpleasant surprises regarding wrap quality, stability, or handling issues. Request demonstrations or trial runs if possible.
- Overlooking Integration Needs: If the wrapper needs to connect with existing conveyors or production lines, ensure compatibility and seamless integration capabilities are considered from the start.

Get Your Best Solution !
8. Enhancing Performance: The Role of Customization
Modern horizontal wrapping machines often offer customization options to precisely match specific operational needs, further boosting efficiency:
- Adjustable Wrapping Tension and Overlap: Fine-tuning film tension and the amount of overlap ensures optimal load containment for different product weights and types without damaging the product or wasting film.
- Custom Infeed/Outfeed Conveyors: Tailored conveyor systems (e.g., powered rollers, belt conveyors, chain conveyors) facilitate smooth product flow into and out of the wrapping zone, especially for heavy or awkwardly shaped items.
- Top Pressure Plates or Side Guides: These options help stabilize tall, unstable, or lightweight products during the wrapping cycle, ensuring a consistent and secure wrap.
- Pre-set Wrapping Programs: Saving specific wrapping parameters (tension, speed, number of wraps) for different products allows operators to switch between jobs quickly and consistently with the touch of a button.
- Integration with Weighing or Labeling Systems: For end-of-line applications, integrating the wrapper with scales or label applicators can streamline the entire packaging and shipping preparation process.
Discuss your specific needs with manufacturers to explore available customization options that can optimize your wrapping process.
9. Sustainable Packaging: Eco-Friendly Wrapping Solutions
Environmental responsibility is increasingly vital. Selecting a horizontal wrapping machine that supports sustainable packaging practices offers both ecological and economic benefits:
- Compatibility with Eco-Friendly Materials: Ensure the machine can effectively run thinner gauge films, recycled-content films, or potentially biodegradable/compostable options if applicable to your needs.
- High Film Pre-Stretch Efficiency: Maximizing film stretch significantly reduces the volume of plastic consumed per pallet, lowering both costs and environmental impact. Look for reliable pre-stretch percentages (e.g., up to 300%).
- Energy Efficiency: Choose machines with energy-saving motors, drives, and components to reduce electricity consumption and lower your carbon footprint.
- Optimized Wrapping Programs: Precise control over wrap parameters minimizes unnecessary film usage, reducing waste. Features like band wrapping (only wrapping specific sections) can also save material.
Adopting sustainable wrapping practices can enhance your brand image and potentially reduce packaging taxes or fees in certain regions.
10. Real-World Results: Case Studies in Efficiency Gains
Examining how other businesses benefited from strategic machine selection provides valuable insights:
Case Study 1: Building Materials Distributor
- Challenge: A distributor of long building materials (like siding and pipes) faced bottlenecks due to slow manual wrapping and inconsistent load security, leading to shipping damage.
- Solution: They invested in a fully automatic orbital horizontal wrapping machine integrated with their existing conveyor system. The machine featured high pre-stretch and customized guides for various product profiles.
- Result: Packaging throughput increased by 70%, labor dedicated to wrapping was reduced by 50%, and shipping damage claims dropped significantly due to improved load stability.
Case Study 2: Furniture Component Manufacturer
- Challenge: A manufacturer of wooden furniture components needed to protect finished surfaces during storage and transit but found manual wrapping time-consuming and used excessive film.
- Solution: They opted for a semi-automatic horizontal wrapper with adjustable tension controls and a powered pre-stretch unit.
- Result: Film consumption was reduced by over 40% due to the pre-stretch system. Wrapping time per bundle decreased, freeing up labor for other tasks, and product protection improved noticeably.
These examples underscore the tangible efficiency gains achievable by matching the right horizontal wrapping technology to specific operational challenges.
11. Beyond the Purchase: The Importance of Support and Training
The most efficient machine can underperform without proper installation, operator training, and ongoing maintenance. Reliable after-sales support is critical for long-term success:
- Comprehensive Operator Training: Ensure the manufacturer provides thorough training on machine operation, adjustments, safety procedures, and basic troubleshooting. Well-trained operators maximize uptime and minimize errors.
- Preventive Maintenance Programs: Regular maintenance is key to machine longevity and reliability. Inquire about manufacturer-recommended maintenance schedules and available service packages.
- Technical Support Availability: Prompt and knowledgeable technical support (phone, online, or field service) is essential for quickly resolving unexpected issues and minimizing costly downtime.
- Spare Parts Availability: Confirm the ready availability and reasonable cost of common wear parts (e.g., belts, rollers, cutting blades) to ensure quick repairs when needed.
Investing in a machine from a supplier with a strong support network protects your investment and ensures sustained operational efficiency.
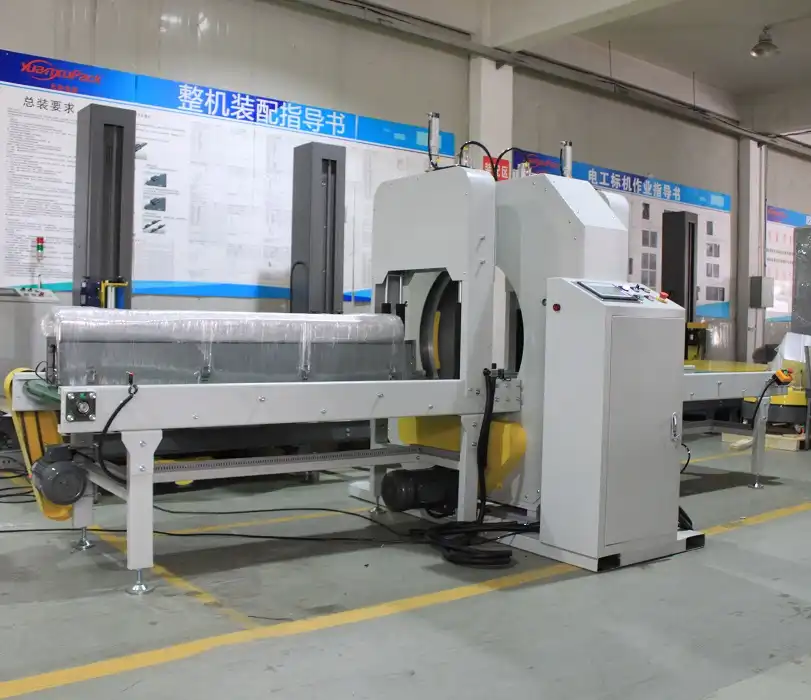
12. The Future of Wrapping: Smart Technology and AI Integration
The evolution of horizontal wrapping technology continues, with future trends pointing towards even smarter and more integrated systems:
- Advanced IoT and Data Analytics: Expect deeper integration of sensors collecting data on machine health, film consumption, and operational efficiency. Cloud-based platforms will allow for remote monitoring, performance benchmarking, and data-driven decision-making.
- Predictive Maintenance: Using sensor data and algorithms, machines will increasingly predict potential component failures before they happen, allowing maintenance to be scheduled proactively, further reducing unplanned downtime.
- AI-Driven Optimization: Artificial intelligence may enable machines to automatically optimize wrapping parameters (like tension and speed) in real-time based on product characteristics or sensor feedback, ensuring maximum efficiency and load security with minimal waste.
- Robotic Integration: Closer integration with robotics for automated loading, unloading, and line transitions will become more common, especially in fully automated, high-speed environments.
Staying aware of these future trends can help inform long-term investment strategies and keep your operations at the forefront of packaging efficiency.
Conclusion: Making an Informed Decision for Optimal Efficiency
Selecting the right horizontal wrapping machine is a strategic investment that directly impacts your operational efficiency, labor costs, product protection, and overall competitiveness. A thorough analysis involves understanding machine types, evaluating key features, considering industry-specific needs, balancing cost against long-term ROI, and factoring in customization, sustainability, and after-sales support.
By carefully weighing factors like automation level, speed, durability, versatility, and TCO, you can identify a horizontal stretch wrapper that meets your current requirements and supports future growth. Avoiding common pitfalls and prioritizing features like high pre-stretch, ease of use, and robust construction will ensure you maximize the benefits of your investment.
Ultimately, a well-chosen horizontal wrapping machine streamlines your packaging process, reduces waste, protects your products, and frees up valuable resources, contributing significantly to a more efficient and profitable operation. Conduct your market analysis diligently, consult with reputable manufacturers, and choose the solution that best aligns with your unique business objectives.

Get Your Best Solution !