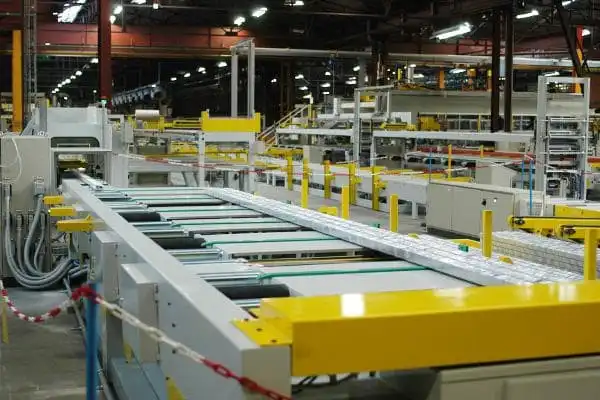
Aluminum profiles, widely used in construction, automotive, and industrial applications, require careful handling and packaging to prevent damage during storage and transportation. Scratches, dents, and bending can easily occur, compromising the quality and usability of the extrusions. An automated aluminum profile packing line, incorporating both bundling and wrapping functions, offers a robust solution to enhance protection, streamline operations, and improve overall efficiency.
The Challenge of Packaging Aluminum Extrusions
Aluminum profiles often feature delicate surface finishes (like anodizing or powder coating) and come in long, sometimes awkward shapes. Manual or semi-automated packaging processes can be labor-intensive, inconsistent, and may not provide adequate protection, leading to higher scrap rates and customer complaints. Efficiently securing and protecting these profiles is crucial.
Understanding Automated Aluminum Profile Packing Lines
An aluminum profile packing line is typically an integrated system designed specifically for handling and packaging extrusions. Key components automate the process, moving from individual profiles or small groups to fully secured and protected bundles ready for shipment. The core functions usually involve bundling the profiles together and then wrapping the bundle.
Key Process: Bundling Aluminum Profiles
Bundling involves grouping several aluminum profiles together into a more stable and manageable unit.
- Purpose: To unitize profiles, prevent individual movement, and create a consistent shape for easier handling and wrapping.
- Methods: This is often achieved using automatic strapping machines (using PP or PET straps) or specialized orbital bundlers that apply stretch film or tape around a section of the bundle.
- Benefits: Simplifies downstream handling, reduces the risk of profiles shifting against each other, and prepares the load for protective wrapping.
Key Process: Wrapping for Protection
Once bundled, the entire unit is typically wrapped for comprehensive protection.
- Purpose: To shield profiles from dust, moisture, scratches, and impacts during transit and storage.
- Methods: Stretch wrapping is common, where layers of stretch film are applied around the bundle. Orbital stretch wrappers are particularly suited for long products like aluminum profiles. Shrink wrapping, where a film bag is placed over the bundle and then heated to shrink tightly, is another option offering excellent containment.
- Materials: Polyethylene (PE) stretch film is widely used. Depending on requirements, specialized films like VCI (Vapor Corrosion Inhibitor) film might be used for enhanced corrosion protection.
- Benefits: Significantly reduces the likelihood of surface damage, keeps profiles clean, and provides load stability.
Integrating Bundling and Wrapping for Maximum Efficiency
The real power of an automated aluminum profile packing line lies in the seamless integration of bundling and wrapping stations. Profiles are fed into the line, automatically bundled, and then immediately conveyed to the wrapping station.
- Workflow: This continuous flow minimizes manual handling between steps, reducing bottlenecks and potential damage points.
- Efficiency Gains: Automation significantly increases throughput compared to manual methods, allowing manufacturers and fabricators to keep pace with production output. Explore various options for an aluminum packing line to see how integration works.
(Image Placeholder: Ensure relevant image is here with descriptive alt text, e.g., "Automated aluminum profile packing line showing bundling and stretch wrapping stations")
Customization and Flexibility
Modern aluminum profile packing lines are not one-size-fits-all. They offer significant customization to meet specific operational needs:
- Profile Handling: Systems can be configured to handle various profile lengths, shapes, and weights.
- Bundle Configuration: Programming allows for different bundle sizes and stacking patterns.
- Wrapping Parameters: Adjustments can be made for film tension, number of wraps, and wrap patterns to optimize material usage and protection levels.
- Integration: These lines can often be integrated with upstream processes (like cutting or stacking) and downstream systems (labeling, palletizing, warehouse management). Further information on handling aluminum components can provide context.
Benefits for Fabricators and Extruders
Investing in an integrated bundling and wrapping line offers several key advantages:
- Improved Efficiency and Throughput: Automates a labor-intensive process, increasing packaging speed.
- Enhanced Product Protection: Consistent and secure packaging minimizes damage during handling and shipping, reducing costly returns and scrap.
- Lower Labor Costs: Reduces the need for manual labor in the packaging area, allowing staff to be reallocated to higher-value tasks.
- Consistent Package Quality: Automation ensures every bundle is packaged to the same standard.
- Optimized Material Usage: Precise control over strapping and film application can reduce material waste compared to manual methods.
Considerations for Implementation
When considering an automated packing line, factors include:
- Line Footprint: Ensuring sufficient space and appropriate layout within the facility.
- Integration: Compatibility with existing material handling equipment and control systems.
- Operator Training: Equipping staff to operate and maintain the machinery effectively.
- Maintenance: Understanding the preventative maintenance schedule to ensure long-term reliability.
Conclusion
For businesses dealing with aluminum profiles, ensuring products reach their destination in perfect condition is paramount. An aluminum profile packing line that effectively integrates bundling and wrapping technologies provides a powerful solution. By automating these critical steps, companies can significantly improve packaging efficiency, enhance product protection, reduce labor costs, and maintain consistent quality, ultimately contributing to a more streamlined and profitable operation.