Optimizing Long Profile Packaging: Achieving Long-Term Savings with an Automatic Horizontal Single Profile Bagging Machine
In modern fabrication and manufacturing environments, efficiently packaging long, single items like extrusions, pipes, or timber profiles presents unique challenges. Manual or semi-automatic methods can be slow, labor-intensive, and inconsistent. Investing in an Automatic Horizontal Single Profile Bagging Machine offers a robust solution, delivering significant operational improvements and substantial long-term cost savings. This article explores the functional benefits and financial advantages these automated systems bring to workshops and production lines.
What is an Automatic Horizontal Single Profile Bagging Machine?
An Automatic Horizontal Single Profile Bagging Machine is specialized equipment designed to automate the process of enclosing individual long products in protective plastic film bags. Key characteristics include:
- Horizontal Operation: Profiles are fed horizontally into the machine, suitable for products that are long and relatively narrow.
- Single Profile Focus: Optimized for packaging one profile at a time, ensuring a snug and secure fit.
- Automation: The machine typically handles film feeding, bag forming (often using centerfold film), product insertion (or wrapping around the product), sealing, and cutting automatically, requiring minimal operator intervention.
These machines are commonly used for packaging aluminum extrusions, plastic profiles, metal rods, wood trim, and other lengthy materials requiring protection from dust, moisture, and surface damage during storage and transport.
Key Operational Advantages and Long-Term Savings
Automating the bagging process for single profiles yields multiple benefits that translate directly into long-term financial gains.
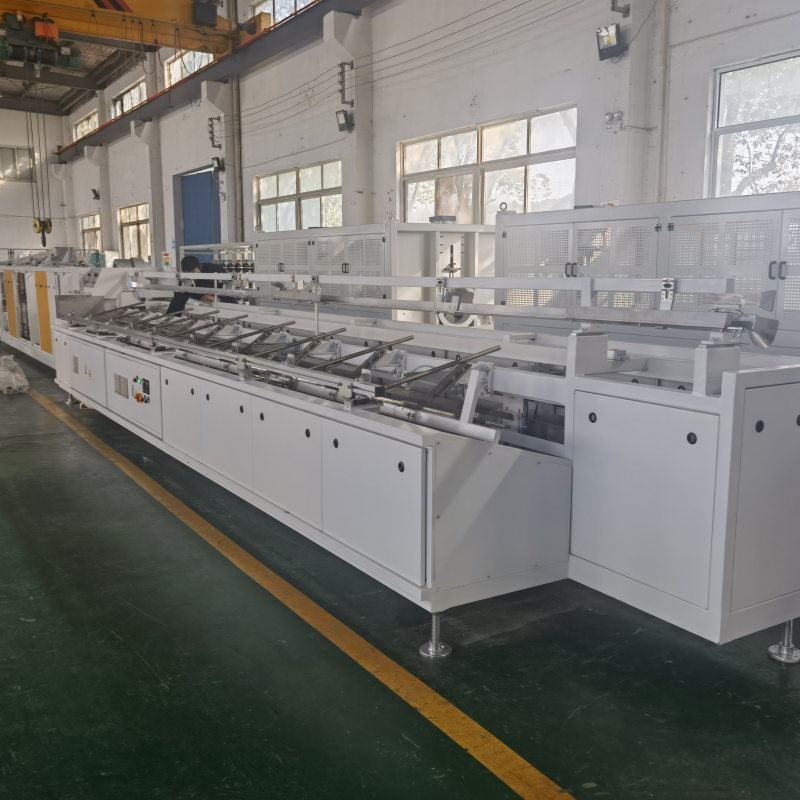
Enhanced Throughput and Productivity
Manual bagging is inherently slow and variable. An automatic machine operates at a consistent, often significantly higher speed, dramatically increasing packaging throughput.
- Increased Output: Handle significantly more profiles per shift compared to manual methods.
- Consistent Cycle Times: Predictable packaging rates allow for better production planning and scheduling.
- Reduced Bottlenecks: Alleviates packaging as a potential bottleneck in the overall production flow.
This heightened efficiency directly contributes to faster order fulfillment and increased overall plant capacity.
Significant Labor Cost Reduction
Labor is a major operational expense. Automating the bagging process drastically reduces the manual labor required.
- Lower Staffing Needs: Fewer operators are needed for the packaging task itself.
- Labor Redeployment: Valuable human resources can be reassigned to more complex or value-added tasks within the facility.
- Reduced Repetitive Strain: Automation minimizes risks associated with repetitive manual bagging motions.
These direct and indirect labor savings accumulate significantly over the machine's lifespan.
Optimized Material Usage and Waste Minimization
Precision is a hallmark of automated systems. These bagging machines are designed to use packaging film efficiently.
- Accurate Film Dispensing: Precisely measured film lengths for each profile minimize excess material use.
- Consistent Sealing: Strong, reliable seals reduce the risk of bag failures and product damage, preventing the need for repackaging.
- Reduced Scrap: Compared to manual cutting and sealing, automated processes generate less film scrap.
Minimizing material waste not only lowers direct consumable costs but also supports environmental sustainability goals.
Improved Package Quality and Product Protection
Consistency is key to protecting products and maintaining brand image. Automation ensures every package meets the same standard.
- Uniform Bag Appearance: Creates a professional, consistent look for packaged goods.
- Effective Sealing: Protects contents from dust, dirt, and moisture.
- Reduced Handling Damage: Secure packaging minimizes scratches, dents, or abrasions during internal handling, storage, and shipping.
High package integrity reduces product returns or complaints due to transit damage, safeguarding profits and customer satisfaction.
Operational Flexibility and Adaptability
Modern horizontal bagging machines offer considerable versatility.
- Adjustable Parameters: Easily accommodate profiles of varying lengths and cross-sections within the machine's specified range.
- Film Compatibility: Can often handle different types of packaging films (e.g., PE, PP) depending on protection requirements.
- Integration Potential: Can be integrated with upstream and downstream equipment like conveyors and labeling systems for seamless workflow.
This flexibility allows manufacturers to adapt to changing product lines or customer requirements without major reinvestment.
Calculating the Return on Investment (ROI)
While the initial acquisition cost represents a capital investment, the Return on Investment (ROI) for an automatic horizontal bagging machine is often compelling and realized relatively quickly. Key factors contributing to ROI include:
- Direct Labor Savings: Reduced wages, benefits, and associated overheads.
- Material Cost Reduction: Savings from minimized film consumption and waste.
- Increased Throughput Value: Higher output capacity enabling greater sales volume.
- Reduced Product Damage: Lower costs associated with rework, scrap, or returns.
- Improved Efficiency: Faster overall process flow.
Many operations find that these combined savings lead to a payback period typically ranging from one to three years, making it a strategically sound financial decision.
Integration and Operational Considerations
Successfully implementing an automatic bagging machine involves several practical points:
- Installation & Footprint: Ensure adequate space and proper utilities (power, compressed air) are available.
- Training: Operators require training on machine operation, adjustments for different profiles, film loading, and basic troubleshooting. Manufacturers usually provide this.
- Maintenance: Adherence to the manufacturer's recommended preventive maintenance schedule (lubrication, inspection of seals/blades) is crucial for longevity and reliable performance.
- Safety: Modern machines incorporate safety features like guarding, interlocks, and emergency stops. Ensure operators are trained on safe operating procedures.
Addressing these considerations proactively ensures a smooth transition and maximizes the machine's uptime and effectiveness.
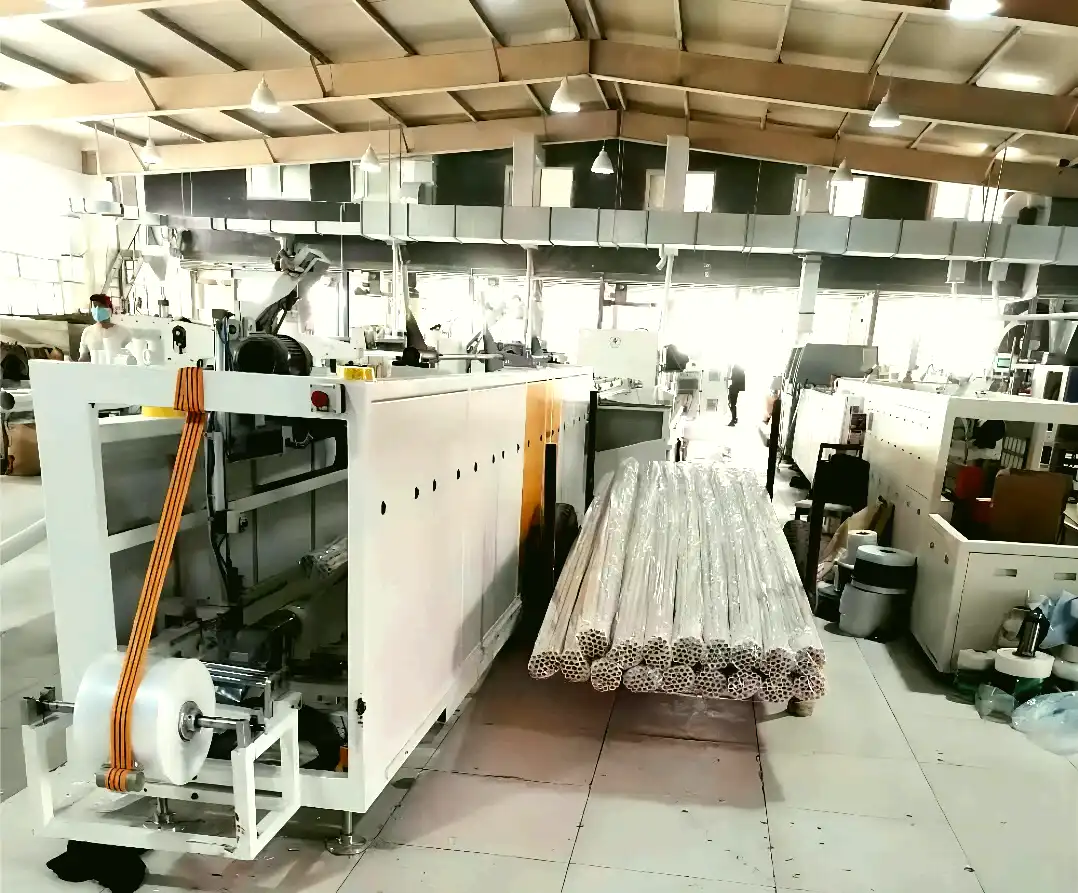
Choosing the Right Machine for Your Needs
Selecting the appropriate automatic horizontal single profile bagging machine depends on specific application requirements:
- Profile Dimensions: Determine the minimum and maximum length, width, and height of profiles to be packaged.
- Speed Requirements: Match the machine's output capacity (profiles per minute/hour) to your production volume.
- Film Specifications: Consider the type (e.g., LDPE), thickness, and width of the packaging film required.
- Level of Automation: Assess needs for features like automatic profile feeding, label application, or integration with existing lines.
- Budget: Balance features and performance against available capital investment funds.
Carefully evaluating these factors ensures the chosen machine aligns perfectly with operational needs and budget constraints.
Real-World Application Insights
The video included at the beginning of this article provides a visual demonstration of a typical automatic horizontal single profile bagging machine in operation. Observe the speed, consistency, and efficiency with which it packages long profiles. Fabricators using such systems consistently report substantial improvements in packaging speed, reduced labor dependency, and better protection for their finished products compared to previous methods.
Conclusion: A Strategic Investment for Long-Term Efficiency
Investing in an Automatic Horizontal Single Profile Bagging Machine is more than just acquiring new equipment; it's a strategic move towards greater operational efficiency, reduced costs, and enhanced product quality. The cumulative long-term savings derived from reduced labor, minimized material waste, increased throughput, and better product protection provide a strong justification for the initial investment. By embracing automation in packaging, fabrication and manufacturing businesses can streamline operations, improve their competitive edge, and build a foundation for sustainable growth and profitability.