Load Analysis of Roller Conveyor Systems
- Load Analysis of Roller Conveyor Systems
- Introduction
- Understanding Overload in Roller Conveyor Systems
- Load Monitoring and Safety Mechanisms
- Role of Sensor Technology in Load Analysis
- Data Collection and Signal Processing for Load Analysis
- Analyzing Conveyor Load Data for Improved Efficiency
- Directional Control in Conveyor Systems
- The Importance of Overload Protection in Conveyor Design
- Conclusion
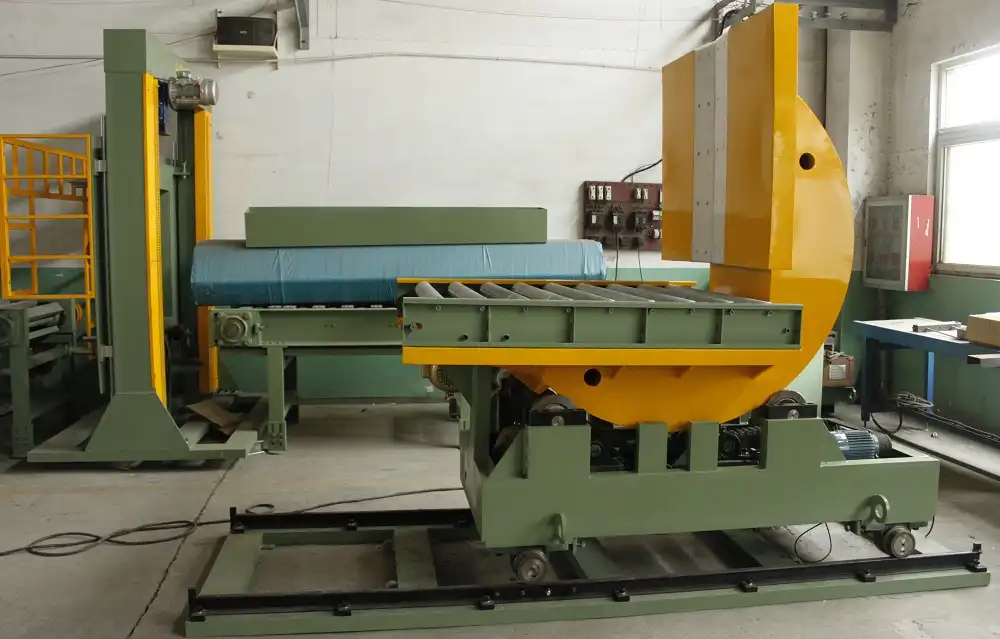
Introduction
Roller conveyor systems play a crucial role in various industries by facilitating the efficient movement of goods and materials. However, when these systems are overloaded, the added strain can lead to excessive wear and tear on mechanical components, reducing the lifespan of internal machine parts. This article delves into the effects of overload on roller conveyor systems, addressing the critical importance of monitoring load conditions to ensure safe and optimal operation. As a manufacturer of roller conveyor lines, understanding and managing overload situations are paramount for maintaining equipment integrity and extending service life.
Understanding Overload in Roller Conveyor Systems
Overloading in roller conveyor systems refers to situations where the weight or volume of the load exceeds the system’s designed capacity. Overload can stem from multiple factors, including unexpected increases in production load, improper distribution of goods, or a lack of regular maintenance checks. When an overload occurs, it places immense pressure on the rollers, belts, and other mechanical components, which can lead to:
- Accelerated Wear and Tear: Prolonged overload accelerates the wear of mechanical parts, reducing the system’s overall lifespan.
- Mechanical Failures: Overloaded systems are more likely to experience breakdowns, leading to unscheduled downtime and costly repairs.
- Decreased Operational Efficiency: Excessive loads slow down conveyor speeds and increase power consumption, impacting productivity and operational efficiency.
For manufacturers, recognizing and managing overload scenarios is essential to prevent these adverse effects. This can be achieved through implementing overload monitoring and protective mechanisms that safeguard the conveyor system.
Load Monitoring and Safety Mechanisms
To handle overload scenarios effectively, modern roller conveyor systems incorporate advanced load-monitoring technologies. These systems utilize sensors and control mechanisms to monitor load conditions in real time, offering an early warning or automatic response to prevent damage. When an overload is detected, there are generally two types of responses based on the severity of the overload:
- Warning Signals for Minor Overloads: If the overload is within a manageable range, the system can provide visual or auditory alerts to notify operators. This allows them to take corrective action, such as redistributing the load or adjusting conveyor speed, before serious issues arise.
- Automatic Shutdown for Severe Overloads: For significant overloads that pose a high risk to the equipment, the system can automatically shut down the conveyor to prevent damage. This shutdown response is critical in protecting the rollers, motor, and other components from the excessive force that an overload would exert on them.
Implementing these safety mechanisms not only helps to maintain the longevity of the conveyor system but also enhances overall workplace safety by reducing the likelihood of accidents related to equipment failure.
Role of Sensor Technology in Load Analysis
Sensor technology plays a pivotal role in monitoring and analyzing the load on roller conveyor systems. By collecting real-time data on load conditions, sensors enable operators to detect potential overloads before they cause harm. The typical load-monitoring setup includes the following components:
- Tension Sensors: These sensors detect the tension on conveyor belts or rollers, which increases with higher loads. Excessive tension is a clear indicator of an approaching overload, prompting immediate corrective action.
- Load Cells: Load cells measure the weight of goods being transported on the conveyor. When the weight exceeds a preset limit, the load cell triggers an alert or initiates protective action.
- Vibration Sensors: In cases where mechanical stress builds up due to overloading, vibration sensors detect abnormal vibrations in the system. These vibrations can signal imbalances or excessive strain on mechanical components, helping to identify and address issues early on.
Data Collection and Signal Processing for Load Analysis
Once load-related data is collected by sensors, it undergoes processing through a series of steps designed to enhance its accuracy and usability for analysis. The following process is typically employed:
- Signal Conversion: Sensors convert mechanical signals, such as tension or weight, into electrical signals that can be measured.
- Amplification and Filtering: The raw signals are then amplified to ensure accuracy and filtered to remove any noise, which could distort the data.
- Data Acquisition and Digitization: The processed signals are gathered by a data acquisition system, which digitizes the information and transmits it to a computer.
- Real-Time Monitoring and Analysis: The computer continuously records the dynamic changes in load conditions. Software programs then analyze these variations to identify trends, detect overload patterns, and predict potential maintenance needs.
Analyzing Conveyor Load Data for Improved Efficiency
By analyzing the data from load monitoring systems, manufacturers can gain valuable insights that help optimize conveyor performance. For instance, trends in load data can reveal specific times or processes that are more likely to lead to overloads. With this information, companies can adjust operational procedures, such as by limiting the weight of materials loaded during peak times or by optimizing the spacing between loads to avoid congestion on the conveyor.
Analyzing load data also enables predictive maintenance. Rather than waiting for a failure to occur, operators can schedule maintenance based on load patterns, replacing parts before they reach critical wear levels. This approach minimizes downtime, reduces maintenance costs, and prolongs the service life of the conveyor system.
Directional Control in Conveyor Systems
In addition to managing load, roller conveyor systems require precise directional control to handle loads efficiently. Many conveyor lines are designed to transport materials in both forward and reverse directions, enabling flexibility in movement and processing. The motor driving the roller conveyor, typically connected through a gearbox, provides bi-directional control that facilitates:
- Smooth Transport of Goods: Precise directional control ensures that goods move smoothly along the conveyor, reducing the likelihood of jams or bottlenecks.
- Efficient Loading and Unloading: By adjusting the conveyor’s direction, operators can load and unload materials in a streamlined manner, enhancing productivity and reducing manual handling time.
To achieve effective directional control, advanced conveyor systems use control units that regulate motor speed and direction based on real-time feedback from sensors. This coordination helps prevent excessive strain on the rollers and other mechanical components, especially when changing the direction of movement under load.
The Importance of Overload Protection in Conveyor Design
Overload protection is a critical consideration in conveyor design, especially for applications involving heavy or high-volume loads. Manufacturers can incorporate various design elements to enhance overload protection, such as:
- Heavy-Duty Rollers and Bearings: Using robust materials for rollers and bearings helps withstand high loads without compromising the system’s structural integrity.
- Reinforced Frames and Supports: Reinforced frames provide extra support, reducing the risk of mechanical failure due to excessive weight.
- Safety Clutches and Torque Limiters: Safety clutches and torque limiters automatically disengage the drive when an overload is detected, protecting the motor and gearbox from damage.
By focusing on overload protection during the design phase, manufacturers can create conveyor systems that not only withstand demanding operational conditions but also deliver a longer service life with minimal maintenance needs.
Conclusion
Load analysis and overload protection are fundamental to the efficient and safe operation of roller conveyor systems. Through the integration of advanced sensor technology, real-time data collection, and intelligent control mechanisms, modern conveyor systems can effectively manage overload conditions. This proactive approach minimizes the risk of equipment damage, reduces maintenance costs, and ensures consistent productivity. For manufacturers, investing in load monitoring and overload protection not only extends the life of the conveyor system but also contributes to a safer, more reliable production environment. As industries continue to evolve, the development of sophisticated load analysis tools will play a key role in enhancing the functionality and durability of roller conveyor systems.

Get Your Best Solution !