1. The Strategic Role of Orbital Wrapping in Modern Logistics
In today's competitive manufacturing and logistics landscape, efficient and secure packaging is paramount. Orbital wrapping machines, also known as horizontal stretch wrappers, are vital tools for achieving this. They automate the process of applying protective film around goods, especially long, bulky, or irregularly shaped items, safeguarding them against damage during handling, storage, and transit.
Effective use of these machines extends beyond simple operation; it involves understanding how they contribute to:
- Enhanced Product Protection: Minimizing scratches, moisture damage, and contamination.
- Improved Load Stability: Ensuring bundles of products (like pipes, lumber, or textiles) remain cohesive.
- Increased Operational Efficiency: Reducing manual labor and speeding up packaging cycle times.
- Reduced Material Waste: Optimizing film usage compared to manual methods.
Mastering orbital wrapping requires attention to detail, from material choices to machine settings.
2. Industry Insights: The High Cost of In-Transit Damage
Feedback across sectors like building materials, metal fabrication, furniture, and textiles consistently highlights in-transit damage as a significant operational cost. Improperly wrapped goods are a primary culprit. Loads secured with stretch wrap are vulnerable if the containment force is insufficient, the wrap pattern is incorrect, or the wrong type or quality of film is used.
Optimizing your orbital wrapping process directly addresses these issues, improving:
- Load Containment: Applying the right tension to hold products securely.
- Damage Reduction: Lowering costs associated with returns, replacements, and reputational harm.
- Customer Satisfaction: Ensuring products arrive in expected condition.
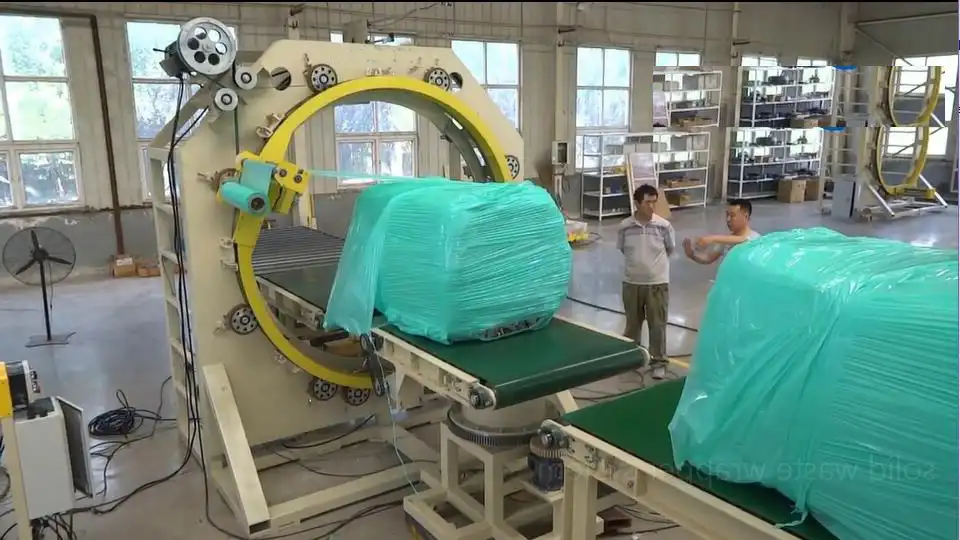
3. Material Selection: Choosing the Right Film for the Job
Selecting the appropriate wrapping material is critical for successful orbital wrapping. Using film intended for manual application often leads to poor results in automated machinery.
A. Key Material Types
- Stretch Film (LLDPE): The most common choice, valued for its elasticity, puncture resistance, and ability to provide high containment force. Available in various grades (cast, blown) and thicknesses (gauges).
- Bubble Film: Provides cushioning for delicate or surface-sensitive items. Often used in conjunction with stretch film for combined protection and stability.
- VCI Film (Volatile Corrosion Inhibitor): Used for metal products requiring rust protection during shipping and storage.
- Opaque/Colored Film: Offers UV protection or allows for color-coding inventory.
B. The Pitfalls of Low-Quality Film
While budget films seem economical, they often compromise packaging integrity:
- Prone to Tearing: Especially under the tension applied by machines.
- Poor Stretch Yield: Leading to higher material consumption.
- Inconsistent Thickness/Quality: Resulting in weak spots and uneven containment.
- Reduced Puncture Resistance: Increasing the risk of damage from handling.
Investing in high-quality film designed for machine application ensures consistent performance and better protection, often leading to lower overall costs through reduced damage and less film usage.
C. Consult and Test
Involve your packaging team and operators in selecting and testing films. Run trials with your specific products to determine the optimal material type, gauge, and pre-stretch settings for your application.
(Remember to add descriptive alt text to any images of film types)
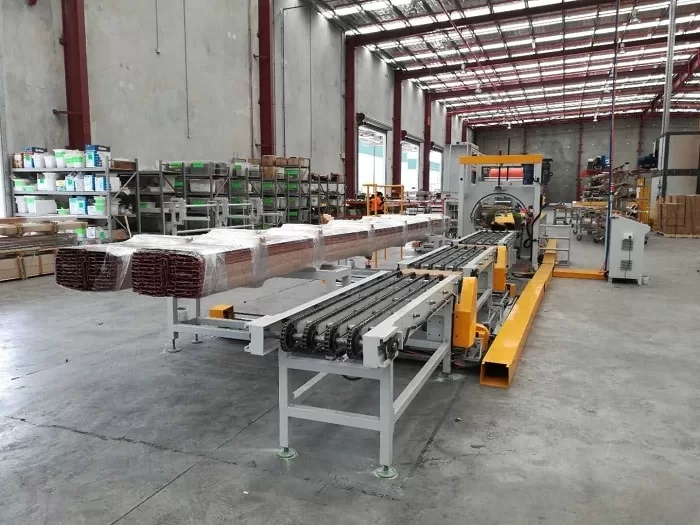
4. Wrapping Tightness: Achieving Optimal Containment Force
Containment force – the squeezing pressure the film exerts on the load – is arguably the most crucial setting for load security. It's not just about wrapping tightly; it's about wrapping correctly.
A. Tailoring Force to the Load
- Load Characteristics: Sturdy, rigid loads (like metal pipes) can tolerate higher containment force than compressible or fragile items (like insulation bundles or furniture).
- Wrap Zones: Different parts of the load may require different tension. Often, the leading and trailing ends need secure wraps to prevent unwinding.
- Machine Settings: Utilize the machine's tension control system (e.g., pre-stretch rollers, dancer bars) to precisely adjust the force. Consult your machine manual for specific adjustment procedures.
B. Preventing Film Breaks and Load Damage
- Over-Tensioning: Leads to film breaks, wasting material and causing downtime. It can also crush or damage the product itself.
- Under-Tensioning: Results in loose wraps that offer little stability, allowing the load to shift or items to come apart.
C. Measuring and Testing
Regularly test containment force using appropriate tools or methods recommended by film suppliers or packaging experts. Simple pull tests or specialized gauges can help verify that your settings are delivering the required force consistently. Adjust settings based on these tests and visual inspection of wrapped loads.
5. Wrap Pattern: Designing for Security and Efficiency
The wrap pattern dictates how the film is applied to the load. Customizing this optimizes both protection and material usage.
A. Number of Wraps/Layers
- More layers generally mean greater protection and stability but also higher material cost and longer cycle times.
- Determine the minimum number of layers needed to adequately secure your specific load based on weight, shape, and transit hazards.
B. Overlap Percentage
- The amount each successive wrap overlaps the previous one (typically 30-50%).
- Sufficient overlap ensures load integrity and prevents gaps. Too much overlap wastes film.
C. Material Combinations
- For complex needs, consider programmed patterns that apply different materials (e.g., a base wrap of stretch film followed by a layer of bubble wrap for sensitive surfaces).
D. Utilizing Machine Programs
Modern orbital wrappers often allow saving specific wrap "recipes" (tension, overlap, number of layers, carriage speed) for different products. This ensures consistency and simplifies operation.
(Remember to add descriptive alt text to any images illustrating wrap patterns)
6. Machine Assembly, Setup, and Maintenance
Optimal performance starts with correct machine installation and ongoing care.
A. Professional Installation and Calibration
- Ensure the machine is assembled according to manufacturer specifications.
- Verify that all systems – mechanical, electrical, pneumatic, or hydraulic – are correctly connected and calibrated.
- Leveling the machine is crucial for smooth operation.
B. Operator Training
- Well-trained operators understand how to load film correctly, select appropriate programs, adjust settings safely, and identify potential issues.
- Proper training minimizes errors, reduces downtime, and ensures consistent wrap quality.
C. Regular Maintenance Schedule
- Follow the manufacturer's recommended maintenance schedule.
- Regular checks include:
- Cleaning sensors and rollers.
- Inspecting belts, chains, and bearings for wear.
- Checking pneumatic or hydraulic pressures.
- Verifying safety features (e-stops, guarding).
- Preventative maintenance avoids costly breakdowns and extends the machine's lifespan.
orbital wrapping machine e600 (3)
7. Testing Before Committing: Validate Performance
Before purchasing or implementing a new orbital wrapping system, thorough testing is essential.
A. Real-World Trials
- Test the machine with your actual products, including the most challenging shapes, sizes, and weights.
- Simulate your typical production flow to assess throughput.
B. Evaluate Wrap Quality
- Inspect wrapped loads for consistency, film coverage, containment force (using measurement tools if possible), and overall stability.
- Consider conducting simulated shipping tests if feasible.
C. Supplier Consultation
- Work with potential suppliers. Many offer demonstrations or trial periods. Discuss your specific needs regarding speed, automation level, load types, and required wrap quality. [Link to Authoritative Source on Packaging Testing Standards]
8. Customization and Integration: Tailoring to Your Operation
Standard machines may not fit every need. Explore customization and integration options.
A. Adjustable Parameters
- Ensure the machine offers sufficient control over key parameters: film tension, carriage speed, ring speed, overlap percentage, and number of wraps.
- Look for user-friendly interfaces that allow easy adjustment and saving of programs.
B. Handling Diverse Loads
- If you wrap a variety of products, choose a machine with the flexibility to adapt easily (e.g., different ring sizes, programmable settings, adjustable conveyors).
C. Integration with Conveyors and Systems
- For higher throughput, consider how the wrapper integrates with infeed and outfeed conveyors and potentially broader warehouse management systems (WMS) or production lines. [Link to Internal Post on Packaging Line Automation]
- Seamless integration minimizes manual handling and bottlenecks.
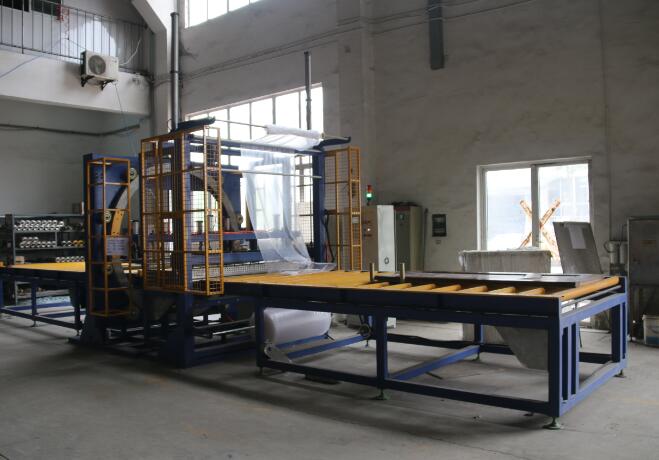
Conclusion: Unlocking the Full Potential of Orbital Wrapping
Optimizing the use of orbital wrapping machines is a multi-faceted process involving careful consideration of materials, containment force, wrap patterns, machine setup, maintenance, and operator training. By moving beyond basic operation and focusing on these key areas, businesses can:
- Significantly reduce in-transit damage and associated costs.
- Improve packaging efficiency and throughput.
- Optimize material consumption.
- Enhance overall product presentation and customer satisfaction.
Investing time in understanding and refining your orbital wrapping process yields substantial returns in product protection, operational efficiency, and bottom-line savings. It's a critical component of a robust and reliable supply chain.