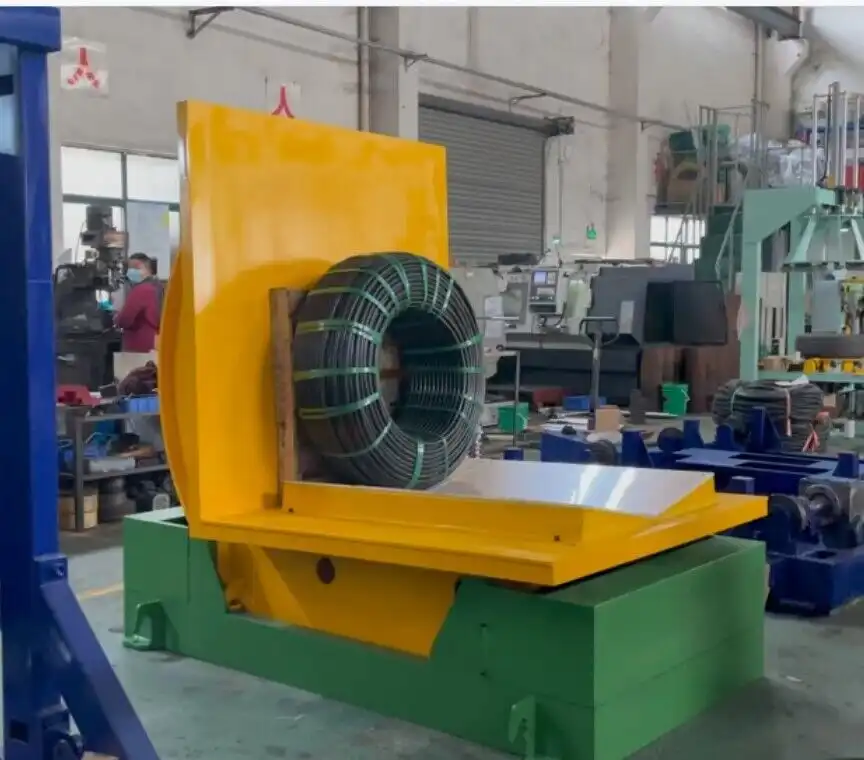
At first glance, hydraulic upenders and mold upenders might seem like two sides of the same coin, each built to lift and rotate heavy objects. However, their applications and advantages vary widely. After diving into the world of industrial upenders, I found that the hydraulic upender shines in flexibility and adaptability, while the mold upender is purpose-built for a more specific function. So, which one aligns with your operation’s goals? Let’s explore these two machines and uncover their unique features and benefits.
Choosing between a hydraulic upender and a mold upender is no simple task. Each machine brings a distinct set of benefits, and understanding these can help you make the right decision. A hydraulic upender offers a broader range of use, while a mold upender focuses on handling molds with precision. The difference might seem subtle, but for those of us familiar with heavy machinery, it’s crucial.
For anyone in industries like manufacturing or molding, understanding these nuances isn’t just helpful—it’s essential. Here, I’ll guide you through a comprehensive comparison, offering a practical look at what sets these machines apart.
[Claim: Selecting the right upender can transform operational efficiency and workplace safety.]
Here’s a comparative list for hydraulic upenders and mold upenders:
Hydraulic Upender vs. Mold Upender: Comparative List
Feature | Hydraulic Upender | Mold Upender |
---|---|---|
Primary Function | Versatile, handles various heavy loads | Specialized for safe and precise mold handling |
Industries Suited For | Manufacturing, logistics, automotive, metalworking | Injection molding, casting, plastic molding |
Load Capacity | High, capable of handling diverse shapes and weights | Moderate, tailored specifically for mold weights |
Safety Features | General safety with pressure sensors, emergency stops | Mold-specific safety like anti-slip and locking systems |
Operational Efficiency | High, supports flexible workflows | Optimized for fast, secure mold rotations |
Versatility | Highly adaptable to different load types | Focused on mold handling with limited versatility |
Design Focus | General heavy lifting and rotating | Precision and safety for mold protection |
Best Choice For | Operations needing varied load handling | Mold-centered operations requiring precise handling |
What Functions Define Each Machine?
1.1 How Each Upender Handles Industrial Tasks
Hydraulic upenders have broad applications, designed to handle diverse load types. Their hydraulic systems allow them to move and rotate items of varying shapes and sizes, making them ideal for manufacturing environments with mixed inventories. Mold upenders, by contrast, focus specifically on molds. They offer stability and safety features essential for mold handling, especially in high-precision settings like plastic or metal molding facilities.
1.2 Tailored Uses for Different Industries
For manufacturers needing versatility, hydraulic upenders serve as a “jack-of-all-trades,” adjusting to various load shapes and sizes. Mold upenders, however, are specialized tools tailored to handle molds carefully, reducing risks of damage during rotation. This focus is ideal for operations where molds require precise handling without the risk of slippage or misalignment.
1.3 Selecting the Machine Based on Function
When selecting between a hydraulic upender and a mold upender, the choice largely depends on the specific demands of your operation. If your workflow centers around handling molds—particularly in industries like injection molding or metal casting—then the mold upender’s focused design is a significant advantage. Mold upenders are optimized for stability and safety when rotating molds, reducing risks associated with slips or alignment issues. This precision ensures that molds are securely handled, which is crucial for maintaining the quality and safety of high-value molds during production.
Conversely, hydraulic upenders offer a broader range of applications, making them well-suited to environments where diverse load handling is required. Their adaptability allows operators to manage various types of heavy items, from pallets to oddly shaped machinery parts, without the need to switch between different equipment. This versatility translates to improved efficiency and flexibility in industries with mixed inventories, such as manufacturing or logistics. Ultimately, choosing the right machine means understanding the primary needs of your operation—whether it’s the targeted precision of a mold upender or the versatile power of a hydraulic upender.
How Does Each Handle Load Capacity?
2.1 Comparing Load Strengths and Capabilities
Hydraulic upenders are engineered for substantial load capacity, often handling weights far beyond the limits of mold upenders. Their hydraulic mechanisms offer robust lifting power, making them ideal for manufacturing settings dealing with oversized or irregular items. Mold upenders, while also sturdy, are calibrated specifically for molds, providing controlled lifting suited to the standard weights encountered in molding industries.
2.2 Mold-Specific Capacity and Stability
Mold upenders are optimized for molds rather than general heavy lifting. Their weight capacity aligns with the typical demands of mold industries, balancing load capability with added features for stability. This targeted load capacity ensures molds are lifted smoothly, without risking abrupt shifts that could compromise the mold’s integrity.
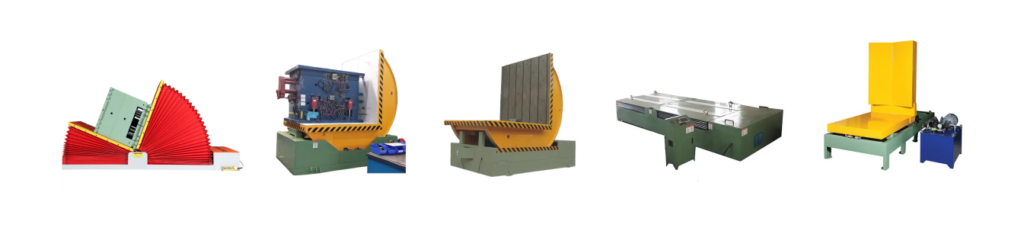
2.3 Prioritizing Load Needs Based on Application
In operations where heavy and diverse loads are the norm, a hydraulic upender’s impressive load capacity and adaptability make it an essential asset. With its robust hydraulic system, this upender can efficiently handle a wide range of weights and shapes, allowing operators to move bulky items with ease. This flexibility is invaluable in manufacturing and logistics environments, where workflows often demand the lifting and rotating of various types of loads, from metal components to large pallets. The hydraulic upender’s ability to adapt to these needs translates into smoother, more efficient handling processes, saving time and reducing the need for multiple specialized machines.
On the other hand, in mold-focused environments, where the primary challenge is to safely and precisely rotate molds, a mold upender offers unmatched stability. Its design, tailored specifically for mold handling, ensures that even the most complex molds are lifted, rotated, and placed with care. The mold upender’s focused capacity aligns with the weight and handling requirements typical of molds used in industries like plastic injection molding or casting. For operations concentrated on mold handling, this targeted capability not only enhances safety but also optimizes production speed and consistency.
Which Safety Features Stand Out?
3.1 Built-In Safety Features for Operator Protection
Safety features in hydraulic upenders are designed for flexibility, addressing the hazards that come with handling various loads. These machines typically include secure grips, pressure sensors, and emergency stops, all of which contribute to safe handling in busy manufacturing environments. Mold upenders, on the other hand, incorporate safety elements specific to mold handling, like anti-slip surfaces and automated locking mechanisms to keep molds secure.
3.2 Mold Upender Safety for Precision Handling
The mold upender’s design prioritizes mold safety, ensuring stability during rotation. This focus on safety is crucial in mold-intensive industries, where mishandling can lead to costly damage or workplace injuries. Mold upenders use unique grips and pressure controls to hold molds firmly, preventing slips that could jeopardize product quality.

3.3 Choosing the Safest Option for Your Operation
The choice between a hydraulic upender and a mold upender hinges on the specific types of items your operation manages. For environments where diverse load handling is the priority, the hydraulic upender’s wide array of safety features brings peace of mind and comprehensive protection. Equipped with pressure sensors, emergency stops, and secure grips, the hydraulic upender is designed to handle various shapes and weights, minimizing risks associated with heavy, irregularly shaped loads. These built-in safeguards create a safe working environment, particularly in high-activity settings where items need to be repositioned frequently.
On the other hand, if your operation focuses primarily on molds, the mold upender’s specialized safety features offer a more customized solution. Mold upenders are crafted with specific safety elements like anti-slip surfaces and automated locking systems that keep molds stable throughout the rotation process. This targeted approach not only prevents damage to delicate molds but also protects workers from potential accidents linked to slipping or unstable loads. By focusing on the unique demands of mold handling, the mold upender ensures both safety and precision, making it the ideal choice for operations where molds are the central focus.
Which Machine Maximizes Operational Efficiency?
4.1 Speed and Adaptability in Workflows
Hydraulic upenders support efficient workflows by adjusting to various load types without much downtime. This adaptability allows for quick item repositioning, speeding up processes in industries where each second counts. Mold upenders, however, offer streamlined efficiency specific to molds, minimizing handling time and reducing the risk of errors in mold-centric industries.
4.2 Specialized Efficiency for Mold-Handling Operations
In industries focused on molding, a mold upender can deliver efficiency gains due to its specialized design. With minimal adjustments, it enables secure, rapid rotations, keeping production speeds high without compromising safety. This efficiency is invaluable in sectors where precise mold handling is a regular necessity.
4.3 Balancing Versatility and Precision for Optimal Efficiency
Achieving optimal efficiency in industrial settings often requires a careful balance between versatility and precision, and this is precisely where hydraulic and mold upenders each have unique strengths. For operations handling a variety of loads, the hydraulic upender stands out with its adaptability. This machine’s design allows it to manage an array of weights and shapes, making it a versatile asset in dynamic environments where different items need to be positioned and rotated regularly. The hydraulic upender’s flexibility not only streamlines workflows but also reduces the need for multiple machines, which can lower costs and improve turnaround times.
In contrast, mold upenders offer a highly focused efficiency ideal for operations dedicated to mold handling. Mold upenders are purpose-built, engineered to rotate and position molds with unmatched stability and care, which is crucial in industries like plastic molding or metal casting. This specialization ensures that molds are handled with precision, minimizing the risk of damage and maintaining production quality. By tailoring their functionality to specific applications, mold upenders deliver efficiency in a targeted way, eliminating unnecessary adjustments and enhancing overall productivity.
Ultimately, choosing between these machines depends on the nature of your workload. If your operation values flexibility across varied tasks, the hydraulic upender provides a versatile solution. However, if specialized mold handling is paramount, the mold upender’s precision-focused design may better support your goals.
Conclusion
In the end, deciding between a hydraulic upender and a mold upender is about aligning your machine’s capabilities with your operation’s specific needs. Hydraulic upenders provide the versatility to handle diverse loads, while mold upenders excel in mold handling, offering targeted safety and efficiency. Whether it’s the hydraulic upender’s adaptability or the mold upender’s focused design, each machine offers unique benefits that can significantly impact your workflow and productivity.
[Claim: The right upender choice not only optimizes operations but also enhances workplace safety and efficiency.]

Get Your Best Solution !