How We Helped a Major Manufacturer Achieve Peak Performance with Their Steel Coil Packing Line
- How We Helped a Major Manufacturer Achieve Peak Performance with Their Steel Coil Packing Line
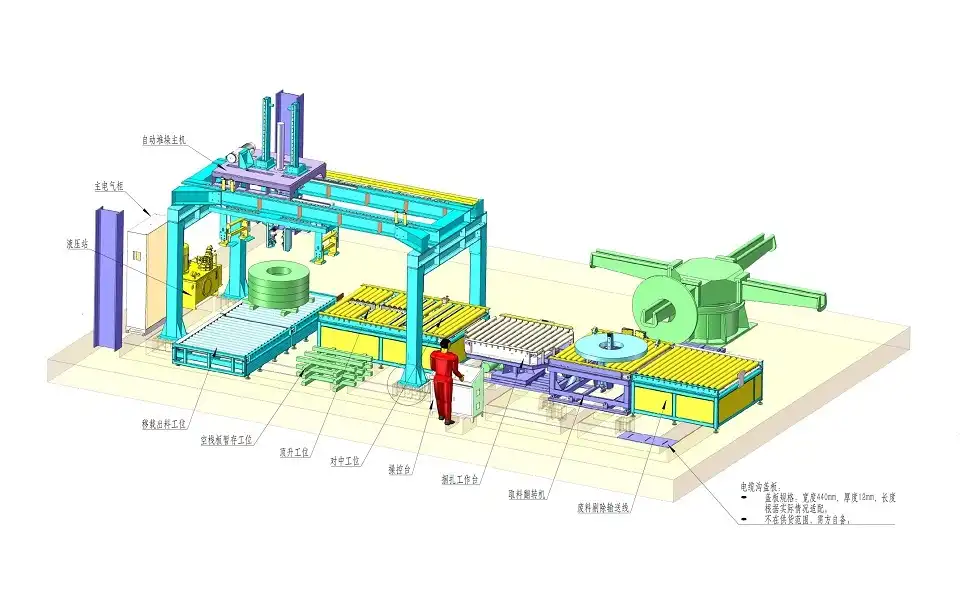
In today’s highly competitive manufacturing landscape, efficiency and productivity are critical to staying ahead. This is especially true in industries that handle heavy and sensitive materials like steel coils, where precision in packaging can make or break a company’s output. In this article, we’ll dive deep into how we worked with a major steel coil manufacturer to streamline their steel coil packing line, boosting their performance and operational efficiency. By leveraging automation and advanced technology, we were able to overcome their challenges and set new standards for their production process.
1. Understanding the Client’s Challenges
Every successful collaboration begins with a thorough understanding of the client’s unique challenges. In this case, our client was a major manufacturer dealing with a high volume of steel coils on a daily basis. Their existing steel coil packing system was outdated and relied heavily on manual labor, which led to several issues:
- Inconsistent packaging quality: Manual handling often resulted in uneven packaging, leading to damages during shipping and storage.
- High labor costs: The company had to employ a large number of workers to keep up with demand, significantly increasing operational expenses.
- Slow production speed: Manual processes were slow, leading to bottlenecks in the packing line and affecting overall throughput.
- Safety concerns: Handling heavy steel coils manually presented significant risks to workers, with frequent accidents and injuries reported.
With these issues in mind, our mission was clear: we needed to introduce an automated steel coil packing solution that would solve these problems while increasing their overall efficiency.
2. Designing the Right Automated Steel Coil Packing Line
Once we had a full understanding of the client’s pain points, we began designing a customized solution that would meet their specific needs. We focused on three main goals: improving speed, ensuring consistent packaging quality, and enhancing safety.
Automation for Efficiency
The first step was incorporating automation into the packing line. This was a game changer. By replacing manual labor with machines, we were able to drastically reduce the time it took to package each coil. The system we introduced featured automated strapping, wrapping, and coil positioning mechanisms. These machines worked seamlessly together, allowing for continuous operation and eliminating human error.
Consistent and Secure Packaging
A key feature of the new system was its ability to ensure consistent packaging across all coils. The automated strapping and wrapping machines were programmed to apply even tension and secure the coils in a manner that minimized movement during transit. This not only protected the coils from damage but also significantly reduced the likelihood of product returns due to defects.
Safety Improvements
One of the most pressing issues we addressed was worker safety. Manual handling of heavy steel coils is risky, and even the most experienced workers can fall victim to accidents. By introducing automated coil handling systems, we significantly reduced the need for human intervention. The system featured automated coil lifting and positioning, which reduced the risk of injury to workers and ensured a safer work environment.
3. Implementation: Overcoming Challenges
Implementing a new automated system in a manufacturing environment is rarely without challenges, and this case was no exception. There were several hurdles we had to overcome to ensure the smooth transition from manual processes to an automated steel coil packing line.
Integration with Existing Systems
One of the major challenges was integrating the new system with the client’s existing infrastructure. The steel coil production line was already in place, and the new packaging system had to work in harmony with the existing setup. To achieve this, we developed custom interfaces and connectors that allowed the packing line to communicate effectively with other parts of the production process. This minimized downtime during the installation phase and ensured a seamless transition.
Training the Workforce
A significant aspect of the implementation process was ensuring that the client’s workforce was comfortable with the new technology. Many of the workers were accustomed to manual processes and needed to be retrained to operate and maintain the new machines. We provided comprehensive training programs that included both theoretical and hands-on learning. This empowered the workers to take full advantage of the new system and ensure its smooth operation from day one.

Get Your Best Solution !
4. Results: Improved Performance and Efficiency
After the successful implementation of the automated steel coil packing line, the results were immediate and impressive. The client saw a dramatic improvement in several key performance areas:
Enhanced Productivity
The automation of the packing line resulted in a significant boost in productivity. The time required to package each coil was reduced by nearly 50%, allowing the company to process more orders in less time. This increase in throughput had a direct impact on the company’s bottom line, enabling them to meet growing demand without the need for additional labor.
Cost Savings
By reducing the need for manual labor, the client was able to cut labor costs by approximately 30%. Additionally, the consistent packaging reduced the number of damaged products, further saving costs associated with returns and replacements. Over the course of a year, these savings amounted to a substantial increase in profitability.
Improved Safety
The automation of heavy coil handling led to a 70% reduction in workplace accidents. This not only created a safer working environment but also reduced the company’s liability and workers’ compensation claims. Employee morale improved as workers no longer had to perform dangerous tasks, contributing to a more positive workplace culture.
Higher Packaging Quality
The client also reported a marked improvement in packaging quality. With automated strapping and wrapping, each coil was secured with precision, reducing the likelihood of damage during transit. This led to fewer customer complaints and enhanced the company’s reputation for delivering high-quality products.
5. Long-Term Benefits and ROI
One of the most critical aspects of any capital investment is the return on investment (ROI). For our client, the initial costs of installing an automated steel coil packing line were offset by long-term savings and operational improvements.
Reduced Maintenance Costs
While the new system was a significant investment, the reduced maintenance costs made it a wise long-term decision. Automated systems, when properly maintained, tend to have fewer breakdowns than manual systems. We implemented a preventive maintenance schedule that ensured the machines operated at peak efficiency without unexpected downtimes. This proactive approach reduced the frequency of repairs and extended the lifespan of the equipment.
Scalability and Future-Proofing
Another key benefit of the automated system was its scalability. As the client’s production volume continues to grow, the packing line can easily be upgraded or expanded to handle increased demand. This future-proofing aspect ensures that the client remains competitive and agile in a rapidly evolving market.
6. The Importance of Partnering with the Right Solution Provider
This success story highlights the importance of working with a trusted automation solutions provider. Our experience and expertise in designing, installing, and maintaining automated packing lines were instrumental in delivering a system that not only met the client’s immediate needs but also positioned them for long-term success.
When looking for a partner to help you optimize your manufacturing processes, it’s essential to choose a provider that understands your industry and has a track record of successful implementations. Our ability to customize solutions and provide ongoing support was key to helping this manufacturer achieve peak performance.
Conclusion
By automating their steel coil packing line, our client was able to overcome major challenges and unlock new levels of performance, safety, and efficiency. From reducing labor costs to improving packaging consistency, the benefits of the new system were immediate and far-reaching. This project is a testament to the transformative power of automation in the steel coil industry. If your business is facing similar challenges, consider investing in an automated packing solution that can help you achieve the same results.
In today’s fast-paced manufacturing world, embracing automation is no longer an option—it’s a necessity for achieving peak performance and staying competitive.

Get Your Best Solution !