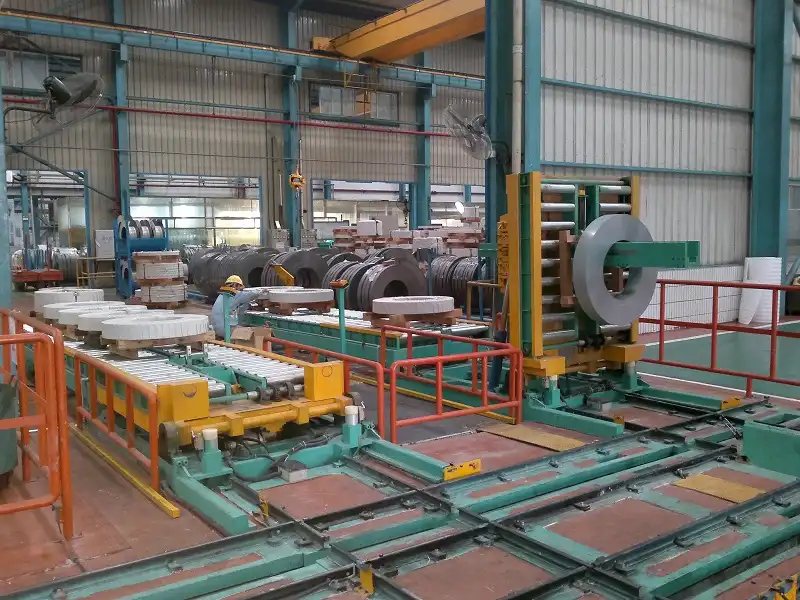
Steel coil packing lines are a cornerstone of efficient logistics in the steel industry, but not all systems are created equal. When we commit to delivering a tailored solution, our goal goes beyond meeting industry standards—we aim to address every unique requirement our clients present. Customization isn't just a feature; it's the foundation of operational success for our clients.
We understand that no two manufacturing facilities are identical. This principle drives our commitment to adapting our steel coil packing lines to fit your workflow seamlessly. The process involves meticulous planning, advanced engineering, and a relentless focus on quality to ensure every customization enhances performance and adds measurable value.
Creating a robust steel coil packing line isn't merely a mechanical task; it’s a process of collaboration and innovation. From the initial consultation to the final delivery, we prioritize flexibility, efficiency, and user-centric design. The result? Systems that exceed expectations and pave the way for streamlined operations.
1. Why Is Customization Critical in Steel Coil Packing Lines?
1.1 Unique Industry Challenges
Steel manufacturers often face an array of challenges specific to their production lines. These might include irregular coil sizes, tight storage spaces, or the need for integration with existing systems. Standardized packing lines rarely account for these complexities, leaving businesses to compromise on efficiency or spend more on modifications post-installation.
Our approach eliminates this concern. By beginning with an in-depth analysis of your facility and operational needs, we tailor every aspect of the packing line to tackle these unique hurdles head-on. For instance, we incorporate modular components to handle varying coil dimensions or advanced automation to improve throughput in high-demand facilities.
1.2 Addressing Operational Bottlenecks
Operational bottlenecks are one of the most significant barriers to efficiency in steel coil packing. Whether it’s delays caused by manual adjustments or interruptions in the packing cycle due to machine incompatibility, these issues cost time and money.
By designing systems that address these bottlenecks proactively, we ensure seamless workflows. Our team identifies pain points in your current setup and develops solutions like automated coil alignment or high-speed strapping mechanisms to optimize productivity.
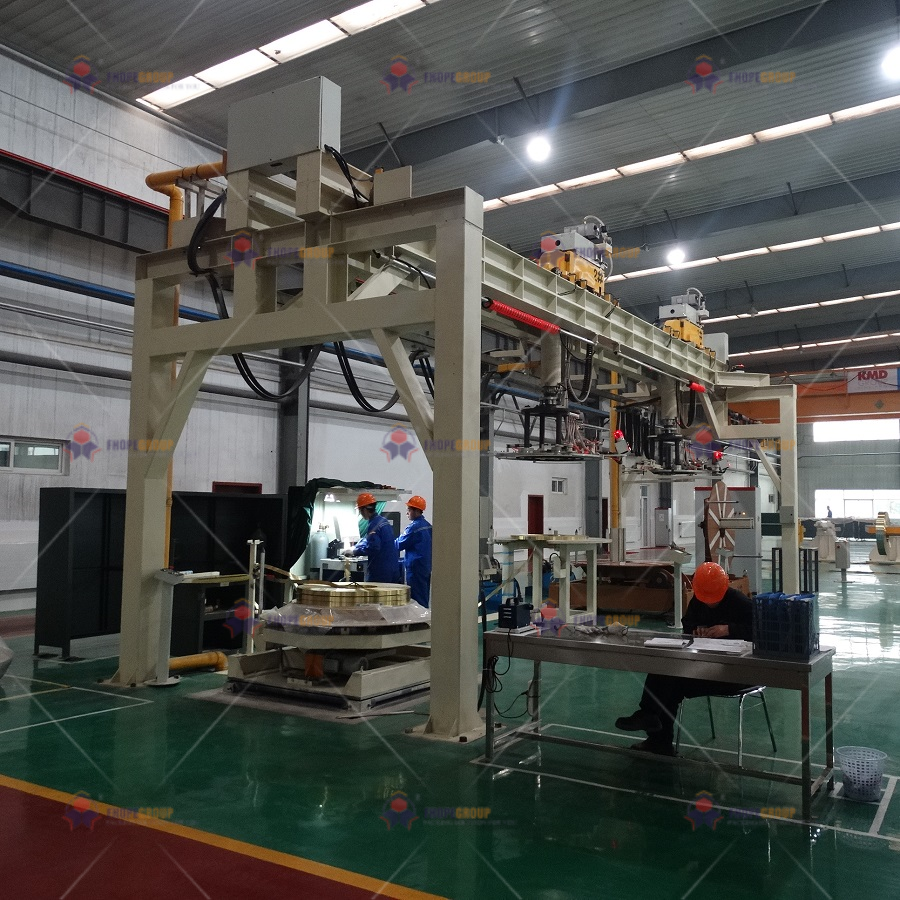
1.3 The Importance of Scalable Solutions
Manufacturing environments evolve, and so do their requirements. A system designed today must be adaptable for tomorrow's challenges, whether they stem from increased production volumes or technological advancements.
Scalability is an integral aspect of our customization process. Features like interchangeable components, modular designs, and software upgrades allow our packing lines to grow alongside your business. This future-proofing approach ensures long-term value and reduces the need for costly overhauls.
2. What Steps Do We Take to Incorporate Customizations?
2.1 Collaborative Design Process
Our process begins with a simple yet powerful step: listening. By engaging directly with your team, we understand your operational goals, production demands, and any specific challenges you face. These insights form the blueprint for a customized packing line that works for you.
During this phase, our team of engineers and designers collaborates with stakeholders to create a system blueprint that reflects your priorities. Whether it’s selecting advanced safety features or incorporating data analytics tools, we ensure your input shapes every decision.
2.2 Engineering Precision
Once the design is finalized, the real work begins. Our engineering team leverages cutting-edge technology to build the customized components needed for your packing line. Precision is non-negotiable. Every detail, from the alignment of rollers to the tension in strapping mechanisms, is meticulously crafted to meet exacting standards.
This stage is also where we integrate any unique technologies requested during the design phase. For example, if you require a fully automated labeling system or an advanced coil weighing module, we incorporate it seamlessly into the system.
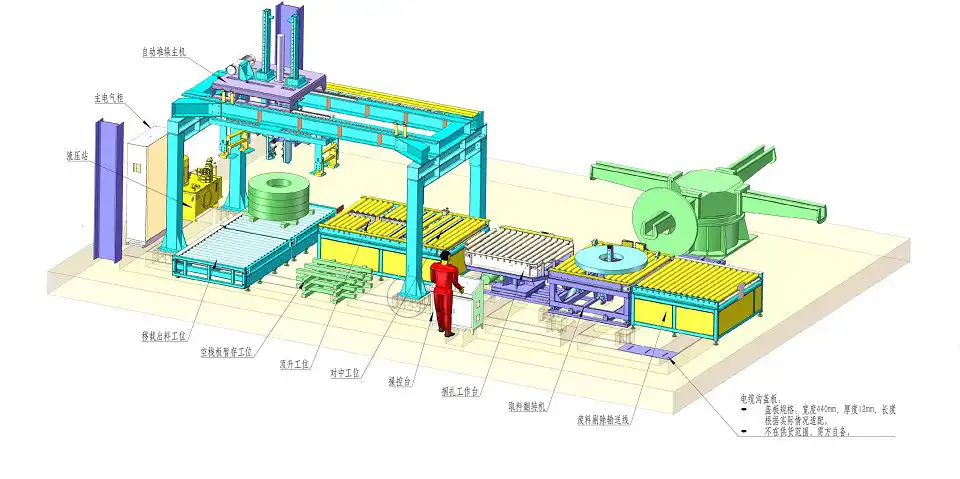
2.3 Quality Assurance in Every Detail
Customization means nothing without reliability. Before delivery, every system undergoes rigorous testing to ensure it performs flawlessly under real-world conditions. This includes stress-testing the system with simulated loads, evaluating its response times, and ensuring it meets your productivity benchmarks.
Our commitment to quality assurance extends to post-installation support. Once your packing line is operational, we remain available for troubleshooting, maintenance, and upgrades. This ensures the system delivers consistent performance and adapts to your evolving needs.
3. How Does Customization Impact Long-Term Efficiency?
3.1 Maximizing Operational Uptime
Customized steel coil packing lines are designed to align perfectly with your operational requirements, reducing downtime caused by equipment inefficiencies. For instance, by automating previously manual processes, we eliminate unnecessary delays and improve overall workflow speed.
These systems also feature components tailored to your production environment, such as advanced sensors that detect and adjust to irregular coil sizes. This level of optimization ensures your operations can handle increasing demands without compromising performance.
3.2 Enhancing Maintenance Schedules
Off-the-shelf systems often come with the challenge of fitting standardized maintenance protocols into unique production setups. Customization mitigates this by enabling predictive maintenance tools and simplified component access.
By integrating IoT-enabled diagnostics, our packing lines provide real-time updates on wear-and-tear and potential malfunctions. These insights allow maintenance teams to address issues proactively, saving time and reducing long-term repair costs.

3.3 Long-Term Cost Efficiency
Investing in a customized packing line isn’t just about immediate operational improvements; it’s about securing long-term savings. Tailored systems are designed to minimize energy consumption, reduce material waste, and ensure compatibility with future upgrades.
For example, we incorporate energy-efficient motors and smart conveyor systems that adapt speed based on workload, reducing utility expenses. Additionally, modular designs make future expansions cost-effective, as individual components can be added without the need for a complete system overhaul.
4. What Innovations Are We Bringing to the Process?
4.1 Embracing Advanced Automation
Automation is a key focus in our customization process. From robotic coil handling to AI-driven packing adjustments, we continuously integrate the latest advancements to enhance productivity and accuracy.
These systems reduce human error and ensure consistent output quality. For instance, automated strapping mechanisms can apply precise tension every time, preventing loose packaging that could compromise product safety during transportation.
4.2 Leveraging Data for Smarter Decisions
Modern manufacturing thrives on data, and so do our customized solutions. By embedding smart analytics tools, our packing lines provide actionable insights into every stage of the process.
Operators can monitor key performance metrics, such as cycle times and machine efficiency, directly from an intuitive dashboard. This transparency enables data-driven decisions that improve operations and uncover hidden inefficiencies.

4.3 Future-Ready Technologies
We recognize that industries are evolving rapidly. To keep you ahead of the curve, we include forward-thinking features in every customization. These might include blockchain-enabled traceability systems for supply chain transparency or augmented reality (AR) tools for training and maintenance.
By designing with the future in mind, our packing lines ensure you remain competitive and adaptable, no matter how the market shifts.
Conclusion
Creating a customized steel coil packing line isn't just about addressing current needs; it's about setting your operations up for long-term success. By incorporating tailored solutions, advanced technologies, and future-ready designs, we ensure every system not only meets but exceeds expectations.
The process is a collaborative journey, driven by precision engineering and an unwavering commitment to quality. Whether it’s enhancing efficiency, reducing costs, or future-proofing your operations, customization transforms your packing line into a strategic asset.
[Customization isn’t a luxury—it’s a necessity in today’s competitive manufacturing landscape. Through our process, we make it seamless and impactful, delivering results that last for years to come.]

Get Your Best Solution !