I see many clients struggle when they first handle steel coils. They worry about accidents, delays, and costly damage. They want a practical way to move coils with confidence.
Transporting steel coils safely and efficiently requires the right mindset. I focus on proper lifting techniques, correct protective materials, and secure strapping or wrapping. These steps help keep coil edges free from harm and reduce risk, ensuring the entire operation flows smoothly (50 words).

"Steel coil transport")
Transition Paragraph:
I have guided countless professionals who face coil handling challenges every day. They want real solutions, not generic advice. They usually need clear precautions, helpful equipment, and proven methods to secure coils. I want to show those key points. Let’s go deeper into these topics now.
What Are the Key Precautions for Handling Steel Coils?
I remember my first time dealing with massive steel coils. I felt anxious because I realized any mistake could lead to severe safety issues. I needed a proven approach.
snippet paragraph:
The main precautions focus on protective gear, careful lifting procedures, and stable surfaces. I prioritize protective clothing, proper training for crane or forklift operators, and consistent handling protocols. These steps prevent accidents and minimize coil damage.
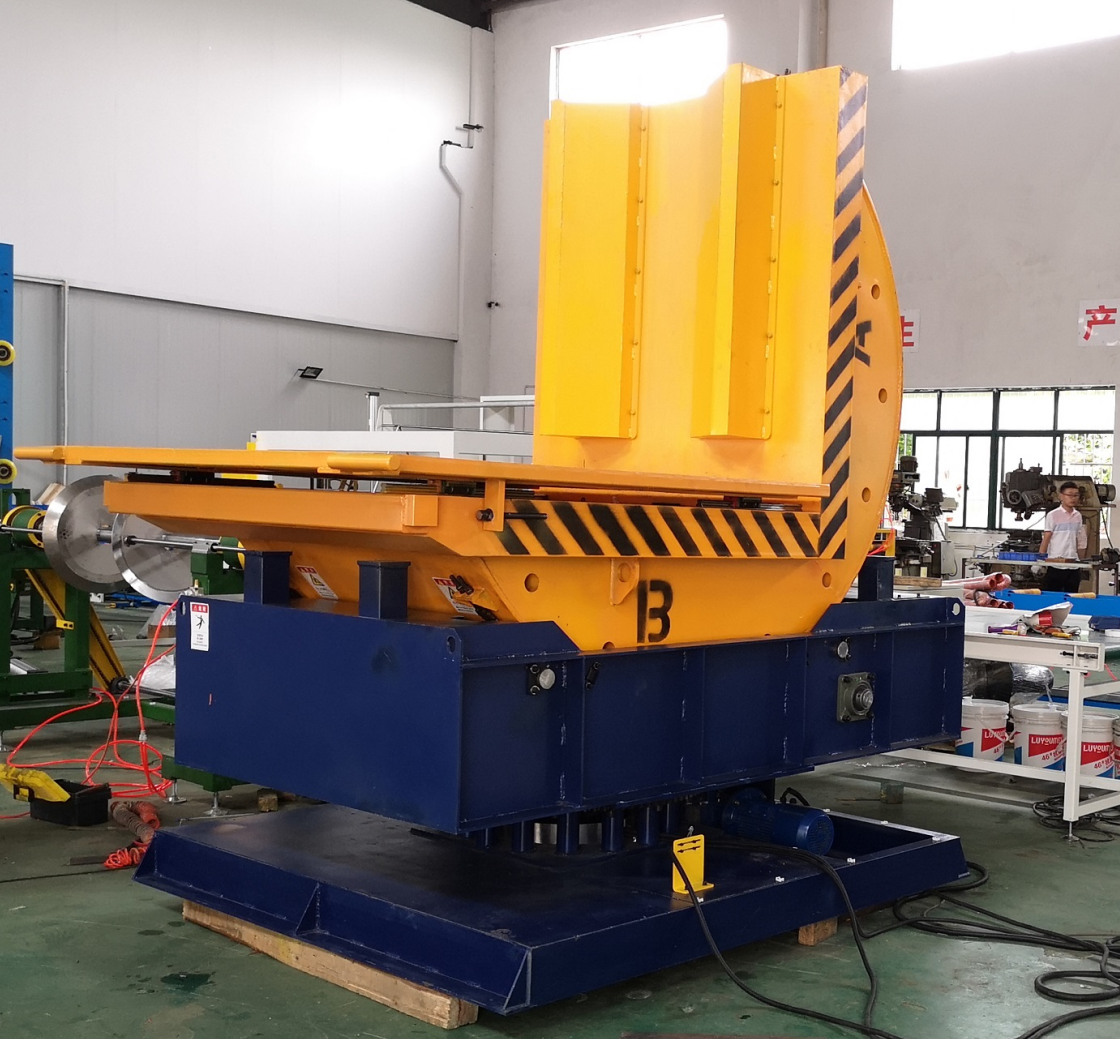
"Safe coil handling")
Dive deeper Paragraph:
Handling steel coils demands skill, precision, and vigilance. I believe in creating a standard operating procedure that guides every step. When I talk with people like David—an experienced specialist at a mid-sized manufacturing company—I hear how easy it is to overlook small details. These small details are often the very things that lead to dangerous mishaps. I see it happen when operators try to save time by skipping routine checks or by assuming that a coil is stable without checking load distribution. Shortcuts like these can create hazards that harm operators and cause product damage.
Why a Clear Procedure Matters
A documented procedure ensures consistency across shifts and teams. I want each operator to know exactly where to stand, how to connect lifting hooks or straps, and which safety measures to follow. Consistency improves overall efficiency. This also helps reduce guesswork and fosters accountability. In my operations, I carefully map out each step, from coil inspection to final positioning. That approach removes confusion and clarifies responsibilities.
Precaution | Reason |
---|---|
Use Personal Protective Equipment (PPE) | Shields operators from sharp edges and possible falls |
Inspect Lifting Devices | Prevents mechanical failure that can cause severe accidents |
Follow Load Restrictions | Avoids overloading equipment, ensuring stability |
Check Coil Center of Gravity | Minimizes tipping risk and controls alignment |
Maintain a Clear Pathway | Reduces collisions and promotes smooth movement |
The Role of Proper Training
Training is the foundation of safe coil handling. I see many teams invest in equipment but neglect operator training. That is a mistake. Even the most advanced crane or forklift can become a hazard in the hands of an untrained operator. Regular training sessions, refresher courses, and mentorship programs help close that gap. This fosters not only greater safety but also higher productivity. A well-trained team handles coils faster, with fewer errors and minimal downtime.
I also believe that continuous improvement is essential. We can always refine our processes, update our guidelines, and improve our training programs. Steel coils keep evolving in size, weight, and composition. Our handling methods must evolve too. This is the path toward long-term efficiency and safety.
Which Equipment Is Best for Handling Steel Coils?
I enjoy exploring different machinery options for steel coil handling. I talk to engineers, operators, and suppliers to discover the perfect tools that meet specific safety standards (30 words).
Selecting the right machinery involves assessing coil size, weight, and handling frequency. I often suggest coil upenders, specialized forklifts, or cranes. Each piece of equipment enhances safety and reduces manual labor (50 words).
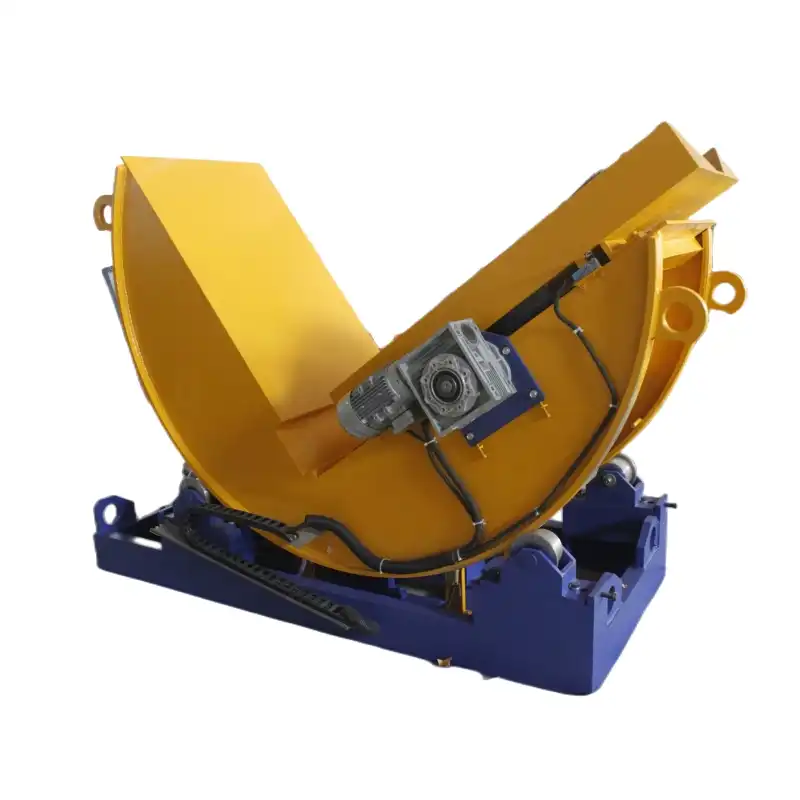
"Machinery for steel coil management")
Choosing the best equipment is not about picking the biggest crane or the most sophisticated forklift. It is about striking a balance between load capacity, maneuverability, and practical usage. I have worked with many organizations that overlook the importance of matching equipment to operational needs. They might choose a crane that can lift more than needed. That seems good on paper, but it can sometimes complicate floor layouts or increase maintenance costs. On the other hand, choosing something too small leads to unsafe overload conditions.
Evaluating Different Solutions
When I assess options, I always start with load capacity. I want to be sure that the equipment can safely handle the maximum expected coil weight. I then look at the shape and size of the coils. Round coils can be placed differently than rectangular or irregular shapes. I prefer equipment with adjustable supports or attachments because it offers flexibility. In my experience, forklift extensions or pivoting arms come in handy when moving various coil dimensions.
Equipment Type | Ideal Use Case |
---|---|
Coil Upender | Shifts coils from horizontal to vertical safely |
Coil Tilter with Cradle | Holds coils firmly during rotation |
Forklift with Extended Forks | Transports lighter coils for shorter distances |
Overhead Crane | Ideal for large coils in high-volume areas |
Automated Coil Wrapping Machine | Ensures secure packaging and consistent load protection |
Automation Benefits
Automation is a rising star in steel coil handling. I see more companies investing in automated coil wrapping machines to reduce manual tasks. Automated solutions improve consistency, reduce packaging defects, and speed up production lines. At Fhopepack, I have observed how integrated systems can transform an entire workflow. Operators can focus on quality checks instead of grueling lifting tasks, and we see fewer workplace injuries. Automation also provides real-time data, helping us track each coil’s movement and condition. This data helps us make informed decisions about maintenance schedules and process improvements. It gives a transparent view of where each coil is in the handling process.
Another important benefit is scalability. If I install a fully or semi-automated system, I know I can tweak or expand it as production grows. This approach supports long-term cost savings. Rather than buying multiple small systems over time, investing in a flexible automation solution can accommodate rising demand. I have seen how this strategy pays off when we do the math on labor costs, downtime, and quality control. Operators often report higher job satisfaction when they no longer risk physical strain by handling coils manually. With an efficient setup, everyone wins—fewer injuries, faster throughput, and improved coil condition upon delivery. (300 words)
How Can You Secure Steel Coils During Transport?
I have watched steel coils roll off trailers because they were not secured properly. These events cause major damage and create safety hazards that nobody wants to face (30 words).
Securing steel coils in transit requires well-placed restraints and protective materials. I typically use cradles, chocks, or custom wedges, combined with sturdy strapping. This ensures the coil remains stable through bumps and turns (50 words).
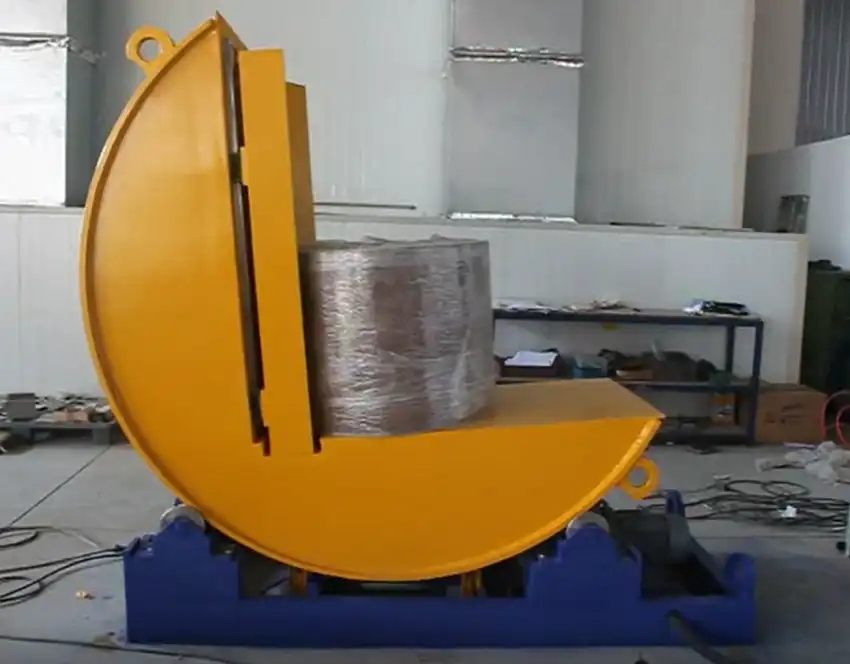
"Proper coil securing methods")
Transporting steel coils is more than loading and tying them down. I consider the entire journey. This includes anticipating road conditions, loading dock design, and the typical behavior of drivers. Every bump, turn, and sudden stop can shift the coil’s weight. If the coil is not properly braced, it can slide or tip, damaging the coil and surrounding cargo. It can also endanger the driver or anyone nearby. That risk grows with heavier coils, which carry more kinetic energy. I recall an incident where a truck driver had to swerve unexpectedly to avoid a minor road obstacle. Because the coil was poorly secured, it snapped its restraints and rolled. This caused a significant delay and a serious safety threat.
Key Components of Coil Securement
- Positioning: I start by placing coils in a stable orientation. I prefer using coil saddles or specialized cradles designed to handle the coil’s curved edges.
- Blocking and Bracing: I make sure blocks and wedges are firmly in place to limit movement. A small gap between the coil and the bracing can lead to gradual shifting during transit.
- Straps and Chains: I choose tensioned straps or chains with the right load rating. Over-tensioning can damage the coil edges, while under-tensioning can lead to slack that compromises stability.
- Edge Protectors: Steel coils often have sharp edges. Placing corner protectors between the coil and strap helps distribute pressure and prevents the strap from cutting into the metal.
Securement Method | Function |
---|---|
Cradles or Saddles | Provide a stable base for round coils |
Chocks or Wedges | Prevent side-to-side or forward-backward movement |
Tensioned Straps or Chains | Maintain coil position under dynamic conditions |
Edge Protectors | Safeguard straps from sharp coil edges |
Anti-Skid Mats | Add friction to reduce sliding risks |
Tailoring Methods for Different Coils
Not all coils are created equal. Thinner steel coils might need more gentle handling to avoid denting or distortion, while thicker or heavier coils need heavy-duty bracing. I always check coil thickness and center of gravity. This helps me decide if I need extra blocking or stronger straps. Another factor I consider is whether the coil is coated, painted, or wrapped. A finished coil is more prone to cosmetic damage like scuffs or scratches. That is where protective materials make a big difference.
I have also found that climate can affect coil securement. In cold weather, metal straps can become brittle. In humid or rainy conditions, friction between coil and trailer bed might change. I always adapt based on these variables, taking extra steps to preserve coil quality and ensure safe transport. Sometimes that includes using protective coverings or ensuring that moisture does not pool under the coil. That attention to detail prevents corrosion and saves me the hassle of dealing with rejected shipments later.
Finally, I learn from every shipment. After each delivery, I check how well the coil stayed in place. This post-transport review helps me refine my methods. I might discover that one set of straps loosened slightly, or that a particular wedge arrangement worked best for a certain coil size. Over time, these adjustments add up to a streamlined and highly reliable process. The goal is always the same: prevent accidents, minimize coil damage, and keep transport efficient. (300 words)
Conclusion
Transporting steel coils safely and efficiently involves attention to every step. I focus on strict precautions, the right equipment, and firm securement methods. These strategies help me protect both workers and products (38 words).