Comprehensive Training Guide for Efficient Pallet Inverter Use
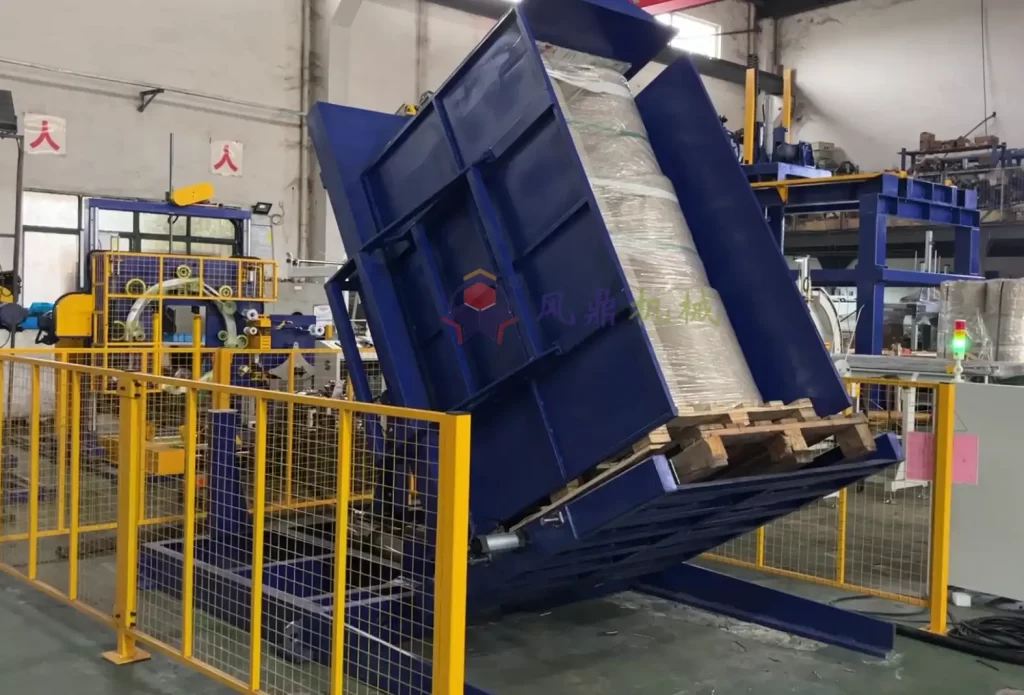
In modern warehousing and logistics, maximizing efficiency and ensuring operational safety are critical goals. The pallet inverter is a valuable tool that significantly contributes to achieving these objectives by simplifying tasks like pallet rotation, pallet exchange, and the careful handling of delicate goods. However, simply acquiring a pallet inverter isn't enough; comprehensive team training is crucial to unlock its full potential, minimize operational downtime, and prevent costly workplace accidents.
This guide provides a detailed framework for training your team on the efficient and safe use of a pallet inverter, covering essential strategies, key focus areas, and actionable steps to effectively integrate this equipment into your workflow.
1. Establishing Foundational Knowledge: Understanding the Pallet Inverter
Effective training begins with a solid understanding of the pallet inverter's function and operational purpose. Explain that a pallet inverter is specifically designed to securely grip and rotate palletized loads (often 180 degrees), enabling quick and easy exchange of damaged, unsuitable, or company-specific pallets without manual restacking. Highlight its importance in industries dealing with sensitive, fragile, or perishable goods where maintaining load integrity during pallet transfer is vital.
Initial training modules should clearly cover:
- Core mechanics: How the inverter clamps, lifts, and rotates the load.
- Operational benefits: Why it enhances efficiency and safety in your specific context (e.g., reducing manual handling, speeding up QA checks, transferring to hygienic pallets).
- Compatibility: The types of loads, pallet sizes, and weights the specific model is designed to handle safely.
2. Prioritizing Safety: Essential Pallet Inverter Protocols
Operator safety must be the foremost priority in all pallet inverter training. These are powerful machines, and incorrect operation can lead to severe injuries or equipment damage. Ensure every team member fully understands and adheres to established safety protocols. Key safety training elements include:
- Load Capacity Adherence: Emphasize never exceeding the manufacturer's specified maximum load weight and dimensions.
- Personal Protective Equipment (PPE): Mandate the use of appropriate PPE, such as steel-toed boots, gloves, and potentially hard hats, depending on the environment.
- Energy Control (Lockout/Tagout): Train relevant personnel on proper lockout/tagout procedures for maintenance, cleaning, or repair to prevent unexpected machine activation.
- Operational Clear Zones: Define and enforce safe operating zones around the inverter, ensuring personnel maintain a safe distance during rotation cycles.
- Emergency Stops: Ensure all operators know the location and function of all emergency stop buttons.
Conducting regular safety drills and integrating safety checks into pre-operational procedures reinforces safe habits and maintains high vigilance levels.
3. Developing Practical Skills: Hands-On Operational Training
Theoretical knowledge must be complemented by structured hands-on training. Supervised practice is essential for building competence and confidence in operating the pallet inverter. This practical training should methodically cover:
- Proper Load Placement: Demonstrating how to accurately position the palletized load onto the inverter's loading platform or forks.
- Secure Clamping Techniques: Training on adjusting clamping pressure correctly for different load types to ensure stability without causing damage.
- Control Panel Navigation: Familiarizing operators with all controls, indicators, and settings needed to initiate and manage the inversion cycle.
- Cycle Monitoring: Teaching operators to observe the rotation process, watching for load shifts or instability, and knowing how to pause or stop if necessary.
- Safe Unloading Procedures: Guiding operators on how to safely remove the inverted pallet and the original pallet from the machine.
Start practical sessions with empty pallets or stable dummy loads before progressing to actual product loads. This allows trainees to master the controls and movements in a low-risk environment.
4. Tailoring Training to Specific Team Roles
Different team members interact with the pallet inverter in various capacities. Role-specific training ensures that operators, supervisors, and maintenance staff understand their distinct responsibilities related to the equipment.
Consider these focuses:
- Operators: Require in-depth training on daily operation, control panel mastery, efficient and safe load handling, basic troubleshooting (e.g., clearing simple jams), and routine cleaning.
- Supervisors: Need training focused on overseeing safe operation, ensuring protocol compliance, monitoring operator performance, understanding workflow integration, and recognizing when maintenance is required.
- Maintenance Personnel: Require comprehensive technical training covering the inverter’s electrical, hydraulic, and mechanical systems, preventative maintenance schedules, advanced troubleshooting, repair procedures, and spare parts management.
5. Integrating Manufacturer Specifications and Guidelines
Every pallet inverter model comes with manufacturer-specific operating manuals, capacity limits, recommended speeds, and maintenance schedules. It is imperative that your training program incorporates these official guidelines. Deviating from them can compromise safety, reduce the machine's lifespan, and potentially void warranties.
Provide easy access to manufacturer manuals (physical or digital) and consider creating simplified quick-reference guides or operational checklists based on these documents. This reinforces adherence to factory standards.
6. Emphasizing Proactive Maintenance Training
Efficient pallet inverter utilization relies heavily on consistent and correct preventative maintenance. Neglecting maintenance leads to unexpected breakdowns, reduced performance, and costly downtime. Training should instill the importance of maintenance across relevant roles.
Key maintenance training areas include:
- Daily Operator Checks: Training operators to perform pre-shift inspections (e.g., checking hydraulic fluid levels, inspecting hoses for leaks, ensuring guards are in place).
- Scheduled Lubrication: Ensuring maintenance staff (or designated operators) follow the correct lubrication schedule for bearings, chains, and other moving parts.
- Early Issue Detection: Teaching operators and maintenance staff to recognize warning signs like unusual noises, vibrations, slow operation, or error codes.
- Reporting Procedures: Establishing clear protocols for reporting maintenance needs or malfunctions promptly to the appropriate personnel.
Empowering operators with basic troubleshooting knowledge for common, minor issues (like sensor obstructions) can often resolve problems quickly and minimize calls to maintenance.

Get Your Best Solution !
7. Utilizing Modern Training Technologies
Enhance training effectiveness by incorporating technology. Options include:
- Virtual Reality (VR) Simulators: Offer immersive, risk-free environments for operators to practice complex maneuvers and emergency procedures.
- Augmented Reality (AR) Tools: Can overlay digital instructions or highlight components during hands-on maintenance tasks.
- E-Learning Modules: Provide accessible, self-paced learning for theoretical knowledge, safety refreshers, and quizzes.
- Video Tutorials: Use manufacturer videos or create custom videos demonstrating specific procedures or troubleshooting steps.
These technologies can increase learner engagement, improve knowledge retention through interactive experiences, and provide standardized training across shifts or locations.
8. Implementing Mentorship and Peer Learning
Pairing new trainees with experienced, proficient operators as mentors can significantly accelerate the learning curve. Mentors provide real-time, on-the-job guidance, share practical tips, answer questions immediately, and offer constructive feedback in a supportive manner.
This approach fosters a culture of shared knowledge and collaboration, making trainees feel more comfortable seeking assistance and learning best practices directly from seasoned colleagues.
9. Ensuring Long-Term Proficiency: Continuous Education and Refresher Training
Pallet inverter training should be viewed as an ongoing process, not a single event. Implement a schedule for continuous education and periodic refresher training or recertification. This is essential for:
- Reinforcing safety protocols and operational best practices.
- Introducing updates related to equipment modifications or new procedures.
- Addressing any bad habits that may have developed over time.
- Ensuring compliance with evolving industry standards or regulations.
Consider annual or bi-annual refresher sessions combined with practical assessments.
10. Evaluating Training Effectiveness: Performance Audits and Feedback
Regularly evaluate the impact of your training program through performance audits. Observe operators during routine work to assess their adherence to safety procedures, operational efficiency, and overall competence with the pallet inverter.
Combine audits with structured feedback sessions. Solicit input from trainees and experienced operators regarding the training content, delivery methods, and areas needing improvement. This feedback loop is invaluable for refining the program and ensuring it meets the team's actual needs.
11. Building Flexibility Through Cross-Training
Implement a cross-training strategy to ensure multiple team members are qualified to operate the pallet inverter. This enhances operational flexibility, providing coverage during employee absences, shift changes, or periods of high demand. Cross-training reduces reliance on a small number of specialists and can help prevent operational bottlenecks.
12. Measuring Success: Tracking Key Performance Indicators (KPIs)
Quantify the success of your training initiatives by tracking relevant Key Performance Indicators (KPIs). Monitor metrics such as:
- Cycle Time: Average time taken per pallet inversion/exchange. Improvements indicate increased efficiency.
- Safety Incidents: Number of accidents, near misses, or reported safety violations related to inverter use. A decrease signifies effective safety training.
- Equipment Downtime: Frequency and duration of machine unavailability due to operational errors or maintenance issues. Reduced downtime suggests better operational and maintenance practices.
- Product Damage Rates: Instances of goods damaged during the inversion process. Lower rates indicate improved load handling skills.
Analyzing these KPIs provides tangible evidence of training effectiveness and highlights areas needing further attention or adjustment.
Conclusion: Investing in Your Team for Optimal Pallet Inverter Performance
Effectively training your team to use a pallet inverter is a critical investment that pays dividends in increased productivity, enhanced workplace safety, reduced operational costs, and extended equipment life. A comprehensive training program encompassing foundational knowledge, rigorous safety protocols, practical hands-on skills, role-specific instruction, adherence to manufacturer guidelines, and proactive maintenance awareness is essential.
By embracing continuous learning, leveraging technology, and measuring results through KPIs, you empower your workforce to operate the pallet inverter confidently and efficiently. This commitment to training ensures your operations remain safe, productive, and competitive within the demanding logistics landscape.

Get Your Best Solution !