How to Reduce Maintenance Costs with Automated Coil Upenders
- How to Reduce Maintenance Costs with Automated Coil Upenders
- 1. Understanding the Maintenance Burden of Manual Coil Upenders
- 2. Automated Coil Upenders: A Shift Toward Efficiency
- 3. Key Features That Lower Maintenance Costs
- 4. Implementing Predictive Maintenance Strategies
- 5. Reducing Downtime with Automated Solutions
- 6. Long-Term ROI of Automated Coil Upenders
- 7. Maximizing Your Investment Through Proper Use and Training
- Conclusion
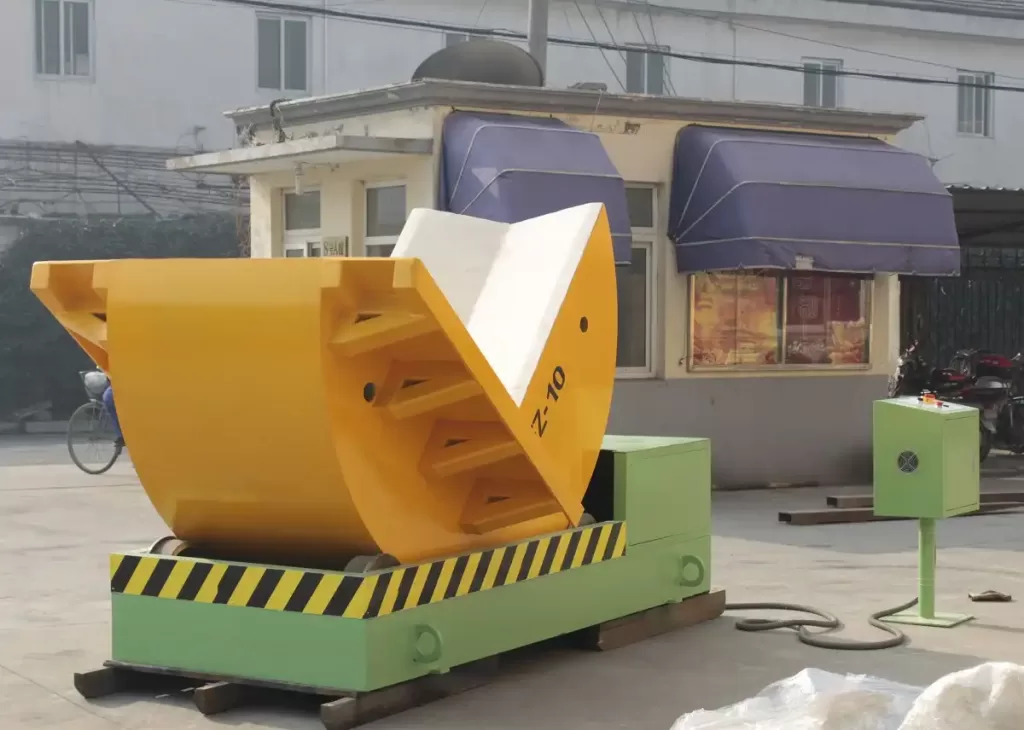
Maintenance costs are a significant concern for industries that handle large, heavy materials like steel coils. As operations scale up, the strain on machinery can become costly if not managed efficiently. This is where automated coil upenders step in, revolutionizing the way businesses handle coil flipping, storage, and transport. By reducing the manual labor required, automated coil upenders can significantly minimize maintenance costs while improving efficiency and safety in the workplace.
In this article, we'll explore how automating the coil handling process can lead to long-term cost savings, reduce downtime, and improve overall operational productivity. We will also discuss strategies to ensure that your investment in automated coil upenders yields maximum returns through reduced maintenance requirements.
1. Understanding the Maintenance Burden of Manual Coil Upenders
Manual coil upenders, while commonly used in the past, present several challenges that can drive up maintenance costs. First, the frequent human interaction with these machines introduces the potential for operational errors. Whether it's improper coil handling or not following the correct operational protocol, these errors lead to increased wear and tear on machinery.
Manual upenders also require frequent servicing, as they tend to suffer from misalignment, unbalanced loads, and mechanical stress from improper handling. The high degree of manual intervention means that machine parts wear out faster, leading to increased downtime and high repair costs. Furthermore, manual upenders are typically less capable of handling the increasing production volumes required by modern industries, leading to even more maintenance issues as the demand grows.
The cost of training employees to handle manual machines can also add to maintenance expenses. Incorrect operation by inadequately trained staff often results in machine breakdowns and, subsequently, higher repair costs. Overall, manual coil upenders require a level of maintenance that can quickly strain budgets.
2. Automated Coil Upenders: A Shift Toward Efficiency
Automated coil upenders are specifically designed to eliminate many of the problems associated with manual operations. These machines use advanced programmable controls to ensure precise movements, reducing the risk of operator error and equipment damage. By automating the coil turning process, these machines deliver consistency and accuracy that greatly reduces the wear and tear on mechanical parts.
Automation reduces human interaction, and with it, the risk of accidents or incorrect usage. As a result, automated coil upenders require fewer repairs and suffer less frequent breakdowns. The predictable operation also means that businesses can implement more reliable preventive maintenance schedules, reducing the need for emergency repairs that often come with high costs and extended downtimes.
3. Key Features That Lower Maintenance Costs
Several features of automated coil upenders contribute directly to reducing maintenance costs. Let’s take a closer look at some of the most impactful ones:
a) Programmable Logic Controllers (PLC)
Modern coil upenders are equipped with PLC systems that allow for precise control over every aspect of the machine’s operation. These controllers ensure that coils are flipped, tilted, and moved with exact precision, avoiding mechanical stress. This reduced stress on the components ensures a longer lifespan for parts, minimizing the need for costly replacements.
Additionally, PLC systems can be programmed to perform self-diagnostics, alerting operators to potential issues before they escalate into major problems. This proactive maintenance approach leads to early detection of minor faults, allowing for low-cost repairs rather than full-scale breakdowns.
b) Built-in Safety Mechanisms
One of the key cost drivers for maintenance is accidental damage caused by improper handling or human error. Automated coil upenders come with a variety of safety features that prevent such incidents. For instance, load-balancing sensors ensure that coils are always positioned correctly before they are flipped, preventing any damage to both the coil and the machine itself.
By avoiding these errors, businesses can save a considerable amount on maintenance, as fewer repairs will be required due to operational mishaps. These built-in safety features are especially valuable in operations where high-value materials, like steel coils, are handled.
c) Durable Design and Materials
Automated coil upenders are built to last. Their durable construction—often using reinforced steel frames and high-grade materials—means they are less prone to damage and corrosion. This robust design reduces the need for frequent part replacements and contributes to lower overall maintenance costs.
Moreover, many automated upenders come with sealed bearings and protected components, which reduces exposure to dust, moisture, and debris that could cause wear and tear over time. With fewer external factors damaging the machine, maintenance intervals are longer, further decreasing the associated costs.
4. Implementing Predictive Maintenance Strategies
While automated coil upenders are designed to require less maintenance, adopting a predictive maintenance strategy can further reduce costs. Predictive maintenance involves using data analytics and sensors to monitor machine performance in real time. By analyzing this data, businesses can predict when a part is likely to fail and take proactive measures to replace it before a breakdown occurs.
Sensors in automated coil upenders can monitor temperature, vibration, and load performance to detect early signs of wear. This allows maintenance teams to address potential issues before they escalate, minimizing the chance of unexpected downtime and costly emergency repairs. Predictive maintenance ensures that the machine is serviced only when necessary, avoiding the expense of unnecessary preventive maintenance checks.
5. Reducing Downtime with Automated Solutions
One of the most significant benefits of automated coil upenders is the reduction in downtime. Downtime due to machine failures is one of the most costly aspects of maintenance, as it not only requires repairs but also halts production. Automated coil upenders, with their reliable performance and minimal need for human intervention, can significantly reduce the amount of time machines spend out of operation.
By streamlining the coil flipping process and eliminating many of the manual steps, automated upenders help keep production moving smoothly. With fewer breakdowns, businesses can keep their production lines running at full capacity, resulting in higher throughput and lower operational costs.
6. Long-Term ROI of Automated Coil Upenders
While the initial investment in an automated coil upender may be higher than that of a manual machine, the long-term cost savings far outweigh the upfront cost. Automated systems lead to reduced labor expenses, fewer repairs, and lower downtime—all of which contribute to a higher return on investment (ROI).
Moreover, automated machines often qualify for tax incentives or other financial benefits aimed at encouraging businesses to adopt more efficient technologies. These incentives can offset some of the initial costs and make the investment even more attractive.
Businesses that invest in automated coil upenders will find that the reduced maintenance costs, combined with increased productivity, lead to significant savings over the machine’s lifespan. Additionally, because automated machines have longer lifespans due to their robust design and predictive maintenance capabilities, the total cost of ownership is lower compared to manual alternatives.
7. Maximizing Your Investment Through Proper Use and Training
While automated coil upenders are designed to reduce maintenance requirements, it is still essential to ensure that your team is properly trained to operate the machinery. Operator training can have a direct impact on how smoothly the machines run, how frequently they require maintenance, and how long they last.
Investing in proper training for your staff ensures that they understand how to use the machine correctly, follow best practices, and troubleshoot any minor issues that may arise. This not only reduces the chance of operational errors that could lead to breakdowns but also maximizes the machine’s lifespan and minimizes the total cost of ownership.
Conclusion
In today’s competitive manufacturing environment, reducing maintenance costs while maintaining high operational efficiency is crucial. Automated coil upenders provide a reliable solution by significantly reducing the strain on machinery, improving safety, and minimizing human error. These machines not only lead to reduced maintenance costs but also improve productivity and help businesses achieve a higher ROI.
By leveraging automation, implementing predictive maintenance, and ensuring proper training, companies can reduce the total cost of ownership for coil handling equipment. As industries continue to move toward automation, investing in automated coil upenders will prove to be a cost-effective decision that pays off in the long term.

Get Your Best Solution !