Orbital wrapping machines, often called orbital stretch wrappers, are essential pieces of packaging automation. They secure goods, particularly long or unwieldy items, by wrapping them tightly in stretch film. This process significantly reduces the risk of damage during handling, storage, and shipping. Found extensively in industries like logistics, building materials, automotive, and manufacturing, these machines boost efficiency and protect valuable products.
This guide details the step-by-step manufacturing process behind a modern orbital wrapper, highlighting the engineering precision, material science, and quality checks involved in creating reliable and efficient packaging equipment.
1. Design and Engineering: Laying the Foundation
The journey begins with meticulous design and engineering. This phase translates operational requirements into a functional blueprint, focusing on performance, safety, and durability.
A. Defining Specifications and Mechanics
Engineers first establish key performance indicators (KPIs):
- Load Capacity: Maximum weight and dimensions the machine must handle.
- Throughput: Required wrapping speed (cycles per minute/hour).
- Wrap Configuration: Ring speed, film overlap, and tension control parameters.
- Product Handling: Conveyor types, speeds, and integration needs.
Safety features, such as emergency stops, safety interlocks, and guarding, are integrated from the outset, complying with relevant industry standards (e.g., ANSI/PMMI standards).
B. Leveraging Simulation and Modeling
Advanced software plays a crucial role:
- CAD (Computer-Aided Design): Creates detailed 3D models of the entire machine and its components, allowing visualization and refinement before physical prototyping.
- FEA (Finite Element Analysis): Simulates operational stresses on structural parts (frame, ring) to identify potential weak points and optimize material usage for strength and longevity. This ensures the design can withstand the dynamic forces of wrapping heavy or irregular loads.
- Kinematic Simulation: Models the movement of the wrapping ring, film carriage, and conveyors to optimize cycle time and ensure smooth, collision-free operation.
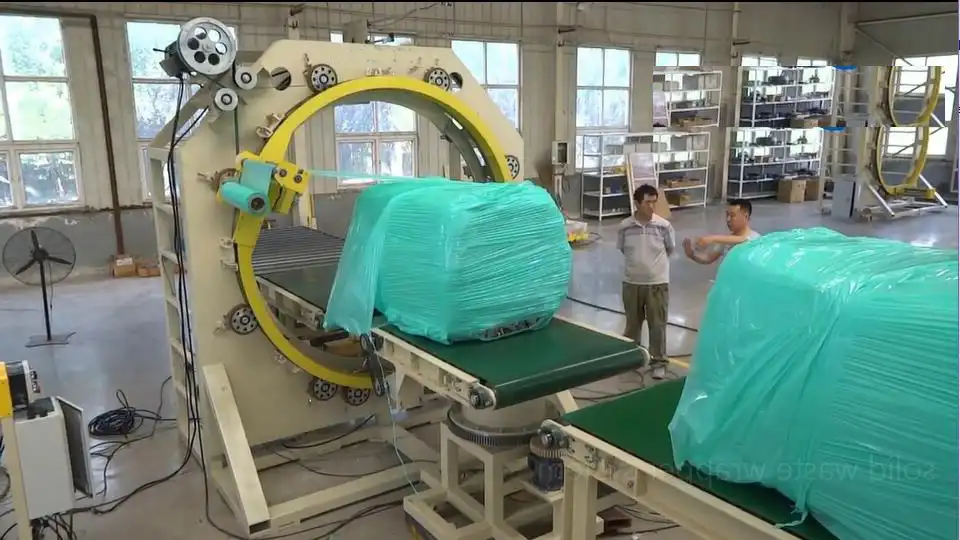
2. Material Selection: Prioritizing Durability and Performance
Choosing the right materials is critical for the orbital wrapper's lifespan, reliability, and safety under demanding industrial conditions.
A. Structural Integrity with High-Grade Steel
The machine's frame and primary structural components are typically constructed from:
- High-Grade Structural Steel: Provides the necessary rigidity and strength to support heavy loads and withstand operational vibrations.
- Surface Treatments: Steel components undergo treatments like sandblasting and priming to prepare for protective coatings, enhancing corrosion resistance. Stainless steel options may be used for specific components or entire machines operating in corrosive or washdown environments.
B. Selecting Critical Components
Beyond the frame, careful selection extends to operational components:
- Gears and Drivetrain: Precision-engineered gears (often hardened steel) ensure smooth, reliable rotation of the wrapping ring.
- Bearings: High-quality industrial bearings (e.g., spherical roller bearings, deep groove ball bearings) are selected to minimize friction, support loads, and ensure long service life for rotating elements.
- Motors and Drives: Variable Frequency Drives (VFDs) paired with robust AC motors or precise servo motors control the speed of the ring, conveyors, and film delivery system.
- Pneumatic/Hydraulic Systems: Used for functions like film clamping, cutting, and pressing devices, requiring durable cylinders, valves, and fittings rated for industrial use.
- Sensors and Controls: Reliable sensors (photoelectric, proximity, encoders) provide feedback to the PLC (Programmable Logic Controller), which manages the machine's automated sequences.
3. Component Fabrication: Precision Manufacturing in Action
With designs finalized and materials selected, fabrication begins. This stage uses advanced manufacturing techniques to produce components to exact specifications.
A. Precision CNC Machining
- CNC (Computer Numerical Control) Machining: Essential for parts requiring tight tolerances, such as bearing housings, gear mounts, and ring components. CNC mills, lathes, and grinders ensure accuracy, repeatability, and optimal fit, which minimizes vibration and wear during operation.
- Laser/Plasma Cutting and Bending: Used for shaping steel plates for the frame and guards, offering speed and precision for structural elements.
- Welding: Certified welders join structural components, following specific procedures to ensure strong, durable joints that withstand operational stresses.
B. Ensuring Component Compatibility and Quality
Each fabricated part undergoes initial quality checks:
- Dimensional Verification: Measuring critical dimensions against design blueprints.
- Material Certification: Ensuring raw materials meet specified standards.
- Weld Inspection: Checking weld quality for structural integrity.
This focus on precision ensures all components integrate seamlessly during assembly.
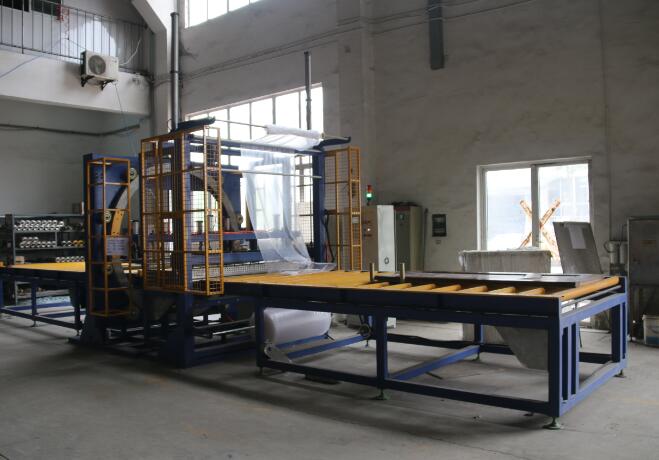
4. Assembly: Integrating Systems and Structure
Assembly is where individual components converge to form the complete orbital wrapper. This stage requires skilled technicians and meticulous attention to detail.
A. Structured Assembly Workflow
- Frame Construction: The main structure is assembled, ensuring it is level and square.
- Ring and Drive Installation: The wrapping ring, drive motors, gears, and support bearings are carefully mounted and aligned.
- Conveyor Integration: Input, output, and potentially centering conveyors are installed and linked mechanically.
- Film Delivery System: The film carriage, pre-stretch rollers, cutting/clamping mechanisms, and tension control systems are fitted.
B. Electrical and Pneumatic Systems Integration
- Wiring and Cabling: Electricians route wires according to schematics, connecting motors, sensors, safety devices, the PLC, and the HMI (Human-Machine Interface) control panel within electrical cabinets. Adherence to electrical codes (e.g., NFPA 79, IEC 60204) is crucial.
- Pneumatic Plumbing: Hoses and valves for pneumatic systems are connected and tested for leaks.
- Safety System Implementation: Emergency stops, light curtains, and safety interlocks are wired and integrated into the control system logic.
5. Testing and Validation: Ensuring Operational Excellence
Before shipment, every orbital wrapper undergoes rigorous testing to verify its performance, safety, and reliability.
A. Functional and Load Testing
- Component Tests: Individual systems (ring rotation, conveyors, film clamp/cut) are tested.
- Integrated System Tests: The machine runs through automated wrapping cycles using test loads (simulating customer products if possible).
- Load Capacity Verification: Testing with loads up to the maximum rated capacity to confirm structural and mechanical integrity.
- Speed and Performance Trials: Verifying cycle times and wrapping consistency at various operational speeds.
B. Safety and Endurance Checks
- Safety System Validation: Testing all emergency stops, guards, and interlocks to ensure they function correctly.
- Endurance Testing: Running the machine for extended periods to identify potential issues related to heat buildup, component wear, or control system stability.
- Film Performance: Evaluating the stretch film application, including pre-stretch levels, wrap tension consistency, and containment force on the load.
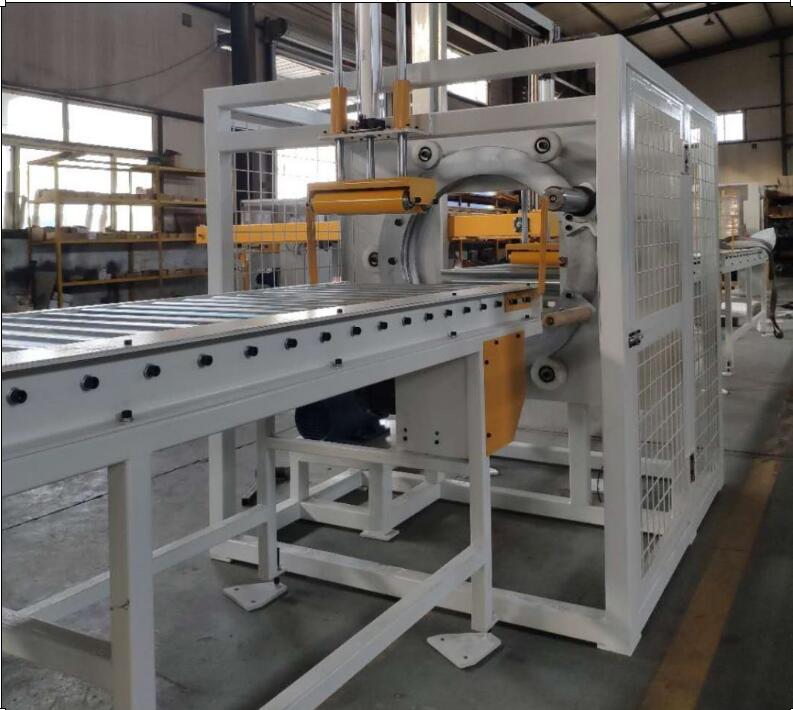
6. Finishing and Customization: Protection and User Needs
After passing all tests, the machine receives its final touches for protection and specific customer requirements.
A. Applying Protective Coatings
- Industrial Painting/Powder Coating: The frame and external components are coated to provide durable protection against corrosion, chemicals, and abrasion. Standard colors are often used, with custom options available.
B. Control Panel and Interface Customization
- HMI Configuration: The touch-screen interface is programmed with the required operational parameters, diagnostic screens, language options, and any custom functions requested by the client.
- Documentation and Labeling: Applying safety labels, operational instructions, and branding according to specifications.
7. Quality Control: A Continuous Commitment
Quality control isn't just a final step; it's integrated throughout the entire manufacturing process.
A. In-Process Quality Checks
Inspectors monitor quality at each stage: material reception, fabrication, sub-assembly, and final assembly, identifying and correcting deviations early.
B. Final Inspection and Documentation
- Pre-Shipment Verification: A final comprehensive check confirms all components are present, correctly installed, and the machine meets all order specifications and passed testing criteria.
- QA Records: All test results, inspection reports, and material certifications are documented, forming a complete quality record for the machine. Compliance with standards like ISO 9001 often guides these processes.
8. Delivery, Installation, and Commissioning: Final Steps to Operation
The completed and verified orbital wrapper is prepared for shipment and final setup at the customer's facility.
A. Secure Shipping Preparation
- Partial Disassembly (if needed): Large machines may be partially disassembled and carefully packed for safe and efficient transport.
- Protection: Components are secured and protected against vibration and environmental factors during transit.
B. On-Site Installation and Training
- Reassembly and Integration: Trained technicians reassemble the machine, connect it to power and air supplies, and integrate it with existing production lines.
- Commissioning: Fine-tuning the machine settings for the customer's specific products and performing final operational tests in the production environment.
- Operator Training: Providing comprehensive training to the customer's staff on machine operation, routine maintenance, and safety procedures.
Conclusion: Engineering Reliability for Packaging Success
Manufacturing an industrial orbital wrapper is a sophisticated process combining robust engineering, careful material selection, precision fabrication, diligent assembly, and exhaustive testing. Each step is vital for producing machinery that delivers consistent performance, enhances packaging efficiency, ensures load stability, and operates safely for years. Understanding this process highlights the value embedded in high-quality packaging automation, enabling businesses to protect their products effectively and optimize their logistical operations.