How to Identify and Fix Common Issues During Steel Coil Packaging Line Start-Up

Introduction: Ensuring a Smooth Launch for Your Packaging Line
Implementing a new or upgraded steel coil packaging line signifies a major investment in operational efficiency and throughput. However, the initial start-up phase—the commissioning process—is often fraught with challenges. Encountering unexpected problems during this critical period can lead to costly delays, compromise product quality, impact safety, and result in unforeseen downtime.
Developing a clear understanding of common start-up issues and mastering effective troubleshooting techniques is crucial for a seamless transition to full production. This guide provides practical, instructional insights into identifying and resolving typical problems encountered during the commissioning of automated steel coil packaging systems, aligning with industry best practices and focusing on operational excellence.
1. Understanding the Core Components of Steel Coil Packaging Lines
Before diving into troubleshooting, it's essential to grasp the fundamental components and the typical workflow of a steel coil packaging line. These sophisticated, integrated systems generally comprise several key stations:
- Conveyor Systems: The backbone of the line, transporting coils between different operational stages. This includes powered roller conveyors, chain conveyors, and potentially walking beam systems.
- Coil Preparation Stations: These units prepare the coil for packaging. Examples include:
- Coil Tilters/Upenders: Orient the coil from eye-to-sky to eye-to-horizon or vice-versa.
- Centering Devices: Ensure the coil is properly positioned before entering subsequent stations.
- Cleaning/Oiling Units (Optional): Prepare the coil surface if required.
- Wrapping Machines: Apply protective layers such as stretch film, VCI (Volatile Corrosion Inhibitor) paper, or plastic sheeting around the coil's circumference and/or through the eye.
- Strapping Machines: Secure the coil using steel or PET (polyester) straps, applied circumferentially or radially (through the eye).
- Stacking and Palletizing Units: Automatically stack smaller coils or place finished coils onto pallets for storage or shipment.
- Control Systems (PLC - Programmable Logic Controller): The brain of the operation, coordinating the timing, sequence, and actions of all mechanical components, sensors, and safety devices. Human-Machine Interfaces (HMIs) provide operator control and monitoring.
The intricate nature of these automated packaging systems means that even minor configuration errors or component malfunctions can cascade, causing significant disruptions. Therefore, diligent start-up procedures and systematic troubleshooting are paramount.
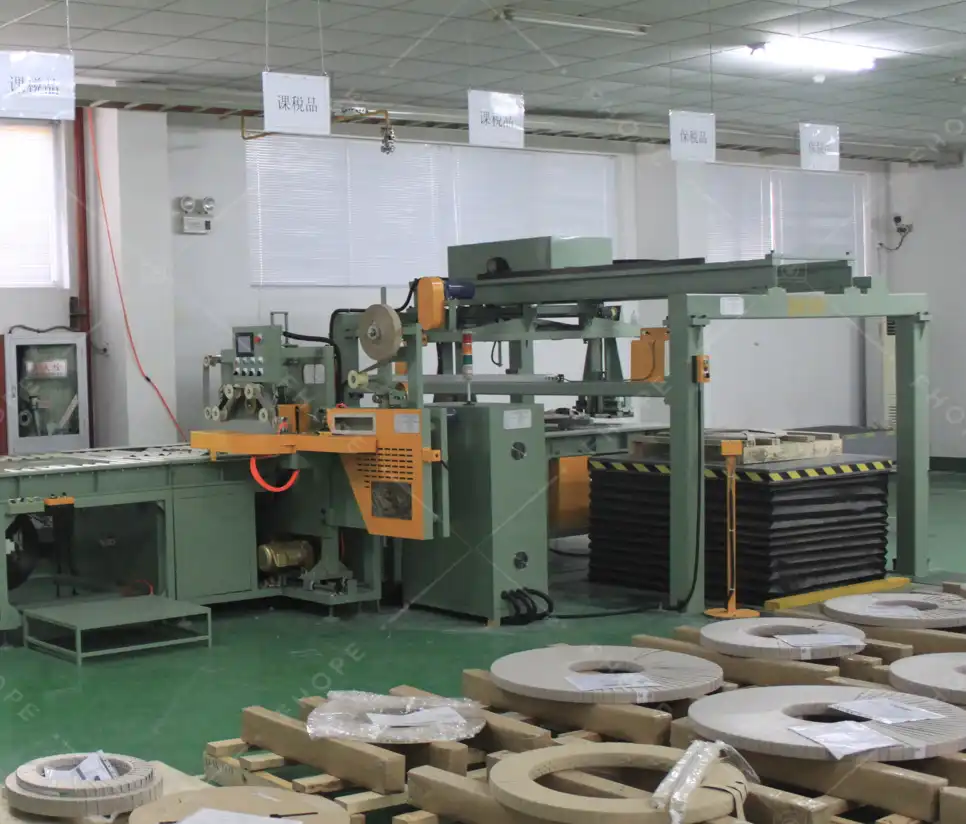
2. Common Start-Up Challenges in Steel Coil Packaging
The initial commissioning and operational ramp-up phase frequently reveals several predictable challenges. Being prepared to diagnose and address these quickly can drastically reduce commissioning time, prevent damage to equipment or product, and avoid establishing long-term operational inefficiencies. Key issues often observed include:
- Coil Transport & Alignment Issues: Improper centering, skewing, or jamming on conveyors.
- Wrapping Machine Malfunctions: Film tearing, uneven application, incorrect tension, or machine faults.
- Strapping Application Problems: Incorrect tension (too high/low), failed seals/welds, or strap misfeeds.
- Sensor & Detection Errors: Misalignment, incorrect calibration, dirt/obstruction, or faulty sensors causing sequence errors or stops.
- Power & Electrical Instability: Voltage fluctuations or interruptions affecting performance and control systems.
- Coil Handling Damage: Issues occurring during loading/unloading, causing dents or edge damage before packaging.
- Component Overheating: Motors, gearboxes, or electrical panels exceeding temperature limits.
- Material Consumption Inefficiencies: Excessive use of stretch film, VCI paper, or strapping.
- System Integration & Communication Faults: Errors in signaling or "handshakes" between different machines or modules controlled by the PLC.
Let's explore each of these common start-up problems in detail and outline effective, practical solutions.
3. Issue 1: Improper Coil Alignment and Transport on Conveyors
Problem: One of the most frequent start-up headaches is coils failing to center correctly or maintain alignment as they move along the conveyor system. Misalignment can lead to:
- Jams at downstream stations (wrapping, strapping).
- Damage to coil edges or surfaces.
- Inaccurate or incomplete packaging application.
- Sensor misreads triggering false stops.
Solution:
- Verify and Calibrate Positioning Sensors:
- Ensure all photoelectric, proximity, or laser sensors responsible for detecting coil presence and position are clean, securely mounted at the correct angle and distance, and accurately calibrated for the entire range of coil diameters and widths processed.
- Follow the manufacturer's specific calibration procedures meticulously.
- Inspect and Adjust Mechanical Guides:
- Check guide rails, side rollers, and automatic centering arms/devices. Ensure they are adjusted precisely for the coil dimensions being run.
- Verify smooth mechanical movement without binding or obstruction. Lubricate pivot points as needed.
- Optimize Conveyor Speeds and Transitions:
- Review and adjust the speeds of individual conveyor sections to ensure smooth, synchronized transitions. Mismatches, especially during acceleration or deceleration zones (like entry/exit of machines), can cause coils to shift or skew.
- Consider slightly lower speeds during initial testing until alignment is confirmed.
- Review Coil Loading Procedures:
- Ensure that the method used to load coils onto the initial conveyor section (e.g., crane, coil car) places them consistently near the centerline. Inconsistent initial placement exacerbates downstream alignment issues.
4. Issue 2: Wrapping Machine Malfunctions and Film Issues
Problem: The coil wrapping machine applies the primary protective layer. Start-up issues often manifest as:
- Uneven wrapping tension: Leading to loose or overly tight wraps.
- Frequent film tearing or excessive wrinkling: Compromising the barrier integrity.
- Incomplete coil coverage: Leaving parts of the coil exposed.
- Machine jams: Caused by film feed issues or mechanical problems.
- Poor film tail sealing: Allowing the wrap to unravel.
These issues directly compromise the protective barrier against environmental factors (moisture, dust) and physical handling damage.
Solution:
- Perform Rigorous Pre-Operation Checks:
- Thoroughly inspect the film carriage, pre-stretch rollers (if applicable), film clamping mechanisms, cutting units, and heat sealers (if used).
- Ensure all components are clean, free from debris, old adhesive residue, or bits of torn film.
- Confirm Correct Film Loading:
- Double-check that the stretch film or VCI paper roll is loaded correctly according to the machine's specifications, paying close attention to the unwind direction and proper threading through all rollers and guides.
- Calibrate and Adjust Tension Settings:
- Precisely calibrate the wrapping tension based on the coil's characteristics (weight, diameter, surface sensitivity) and the specific type and gauge of wrapping material being used.
- Run multiple test wraps on sample or non-critical coils, observing the results and making fine adjustments. Remember: excessive tension causes tears and potential coil damage; insufficient tension results in loose, ineffective protection.
- Verify Pre-Stretch Ratio (for Stretch Wrappers):
- Ensure the pre-stretch setting accurately matches the film's specified capabilities. Over-stretching weakens the film, making it prone to tearing; under-stretching wastes material. Verify the actual stretch being achieved.
- Maintain Mechanical Components:
- Lubricate rollers, bearings, chains, gears, and rotating arms according to the manufacturer's maintenance schedule using the recommended lubricants. This prevents binding, reduces friction, and ensures smooth, consistent operation.
5. Issue 3: Incorrect Strapping Tension and Seal Failures
Problem: Applying the correct strapping tension via the strapping machine is critical for coil integrity during handling and transport. Common start-up issues include:
- Excessive tension: Can damage the coil's edges or surface finish, particularly for softer metals (like aluminum) or pre-painted/coated products. Can also cause coil telescoping.
- Insufficient tension: Results in loose straps that fail to secure the coil effectively, potentially leading to unwinding, load shifting during transit, or safety hazards.
- Inconsistent tension: Variation between straps or cycles.
- Failed strap seals/welds: Weak joints that break under load.
Solution:
- Calibrate the Strapping Head Tension:
- Carefully adjust the tension settings on the strapping machine head based on:
- Coil type (material, hardness, coating).
- Coil dimensions (width, diameter) and weight.
- Strap material (steel vs. PET) and dimensions (width, thickness).
- Consult manufacturer recommendations and conduct tests. Use a tension meter if available for accurate measurement.
- Carefully adjust the tension settings on the strapping machine head based on:
- Conduct Test Cycles and Inspections:
- Strap several test coils and meticulously inspect the results. Check for:
- Excessive indentation on the coil edges.
- Strap security (cannot be easily moved or pulled loose).
- Consistency of tension around the circumference.
- Fine-tune settings until the optimal balance between security and non-damaging pressure is achieved.
- Strap several test coils and meticulously inspect the results. Check for:
- Verify Strap Feed and Sealing Mechanism:
- Ensure the strap feeds smoothly from the dispenser through the guides and into the head without snagging or twisting.
- Critically examine the sealing mechanism (e.g., friction weld for PET, notch or seal-less joint for steel). Ensure it functions correctly and consistently creates strong, reliable joints centered on the overlapping strap ends. Misaligned or incomplete seals are common failure points. Clean sealing components regularly.
- Provide Specific Operator Training:
- Train operators on how to correctly interpret strapping requirements for different products, adjust tension settings appropriately within defined limits, and visually identify signs of both over-tensioning and under-tensioning, as well as faulty seals.
automatic wire coil compressing and strapping machine packing line1 6. Issue 4: Sensor Misalignment, Calibration, and Detection Problems
- Train operators on how to correctly interpret strapping requirements for different products, adjust tension settings appropriately within defined limits, and visually identify signs of both over-tensioning and under-tensioning, as well as faulty seals.
Problem: Modern automated packaging lines rely heavily on a network of sensors (photoelectric, proximity, inductive, laser, ultrasonic) for critical functions:
- Detecting coil presence/absence.
- Confirming coil position and dimensions.
- Sequencing machine operations.
- Providing safety interlocks.
Start-up issues often stem from misaligned sensors, incorrect sensitivity settings, or failed calibration, leading to operational halts, skipped process steps, potential collisions between equipment and coils, or inaccurate packaging cycles.
Solution:
- Implement Systematic Sensor Checks:
- During commissioning and start-up, physically verify the position, mounting angle, alignment, and operational status of every single sensor against the machine drawings and functional specifications.
- Use alignment tools or jigs where provided by the manufacturer.
- Maintain Sensor Cleanliness:
- Dust, oil, grease, water, or debris accumulating on sensor lenses, faces, or reflectors can obstruct the sensing beam or alter detection characteristics. Implement a regular cleaning schedule, especially in dusty or oily environments.
- Execute Calibration Procedures:
- Carefully follow the manufacturer's documented procedures for calibrating sensors, particularly those measuring distance, position, or requiring specific sensitivity adjustments (e.g., background suppression photoeyes).
- Be aware that environmental factors (like excessive ambient light for optical sensors, or temperature changes for some types) might necessitate recalibration after initial setup.
- Ensure Secure and Stable Mountings:
- Verify that all sensors and their mounting brackets are securely fastened. Machine vibration during operation is a common culprit causing sensors to drift out of alignment over time.
- Consider adding protective guards or covers in areas where sensors are prone to accidental impact or heavy contamination.
7. Issue 5: Inconsistent Power Supply and Electrical Issues
Problem: The electrical heart of the packaging line is susceptible to the quality of the facility's power supply. Issues encountered during start-up can include:
- Voltage sags (dips) causing motors to lose torque or controllers to fault.
- Voltage surges (spikes) potentially damaging sensitive electronic components.
- Brief power interruptions leading to unexpected machine stops, loss of PLC program position, or data corruption.
- Electrical noise interfering with control signals.
These can manifest as random stoppages, difficult-to-diagnose faults, and reduced equipment lifespan.
Solution:
- Assess Power Quality at the Source:
- Verify that the incoming power feeding the packaging line meets the equipment manufacturer's specifications for voltage stability and tolerance.
- Use power quality monitoring equipment temporarily during start-up if fluctuations are suspected, identifying the nature (sags, surges, frequency shifts) and timing of disturbances.
- Install Power Conditioning Equipment:
- For critical control systems (PLCs, HMIs, industrial PCs), install uninterruptible power supplies (UPS) capable of riding through brief outages and filtering noise.
- Consider voltage stabilizers, line reactors, or power conditioners for the entire line or sensitive drives/motors if significant or frequent voltage fluctuations are detected.
- Inspect Electrical Connections and Wiring:
- Thoroughly check all power and control wiring connections, terminals within control panels, junction boxes, and at motors/devices. Ensure they are correctly sized, securely tightened (torqued to spec), and show no signs of damage, corrosion, or overheating. Loose connections are a common source of voltage drops and intermittent faults.
- Consult with Industrial Electrical Experts:
- If power quality issues are persistent or originate within the facility's broader electrical infrastructure, consult with qualified industrial electricians or power quality specialists to diagnose and implement necessary upgrades or corrections.
8. Issue 6: Improper Coil Handling During Loading and Unloading
Problem: Coil damage frequently occurs before the coil even reaches the automated packaging line or after it leaves. Mishandling during loading onto the line (via crane, forklift, coil car) or unloading/storage can cause:
- Dents on the coil body or edges.
- Edge damage (crimps, folds).
- Telescoping (inner wraps shifting relative to outer wraps).
- Surface scratches or contamination.
This pre-existing damage not only impacts final product quality but can also interfere with the packaging line's ability to handle and process the coil correctly (e.g., damaged edges snagging on conveyors or wrappers).
Solution:
- Establish and Enforce Standardized Handling Procedures:
- Develop clear, documented procedures for lifting, transporting, and placing steel coils.
- Provide rigorous training for personnel involved (crane operators, forklift drivers, line loaders) emphasizing the correct use of appropriate lifting devices (e.g., C-hooks, vertical eye coil lifters, padded forks, coil grabs). Specify safe speeds and handling techniques.
- Mandate Use of Protective Materials:
- Require the use of protective materials like coil pads (floor pads, saddle pads), edge protectors (plastic or fiberboard), or interleaving materials during handling, transport, and temporary storage to prevent metal-to-metal contact and absorb impacts.
- Evaluate Automated Loading/Unloading Options:
- Where feasible and justifiable by volume/frequency, consider integrating automated coil loading systems (e.g., automated guided vehicles (AGVs), shuttle cars, robotic loaders) that ensure gentle, precise, and repeatable placement onto the packaging line's infeed conveyor, minimizing human error and potential damage.
- Implement Pre-Loading Coil Inspection:
- Institute a quick visual inspection checkpoint before a coil is loaded onto the line. This allows operators to identify significant pre-existing damage that could cause processing issues or should be documented for quality control purposes.
9. Issue 7: Overheating of Motors, Gearboxes, and Electrical Components
Problem: During the intensive start-up, testing, and initial production phases, equipment can be pushed hard. This can lead to overheating issues in:
- Electric motors (especially conveyor drives, wrapper rotation motors, strapper head motors).
- Gearboxes and reducers.
- Hydraulic power units (if used).
- Electrical control cabinets and panels (due to drives, PLCs, power supplies).
Overheating degrades component insulation, causes nuisance tripping of protective devices, significantly reduces equipment lifespan, and can lead to sudden, unexpected shutdowns.
Solution:
- Ensure Adequate Ventilation and Cooling:
- Verify that all motors, gearboxes, and electrical cabinets have sufficient airflow for cooling.
- Check that cooling fans (on motors, in cabinets) are operational, spinning in the correct direction, and not obstructed.
- Ensure ventilation openings and filters on electrical cabinets are clean and allow free air exchange. Avoid blocking airflow around equipment.
- Monitor Operating Temperatures:
- During initial runs and under load, use non-contact infrared thermometers or thermal imaging cameras to monitor the temperatures of motors, bearings, gearboxes, hydraulic tanks, and key components within electrical panels (drives, transformers, contactors).
- Establish baseline temperatures and investigate any components running significantly hotter than expected or exceeding manufacturer limits.
- Verify Lubrication Levels and Types:
- Confirm that gearboxes and bearings are filled with the correct type and quantity of lubricant as specified by the manufacturer. Insufficient or incorrect lubrication dramatically increases friction and resultant heat. Adhere strictly to the recommended lubrication schedule.
- Check for Mechanical Binding and Overloads:
- Ensure motors are not consistently operating in an overloaded condition. Check for mechanical issues downstream that could increase load, such as conveyor misalignment, bearing failures, or improper machine setup causing excessive resistance.
- Confirm Functionality of Thermal Protection:
- Verify that motor thermal overload relays, thermistors (if fitted), and Variable Frequency Drive (VFD) temperature monitoring systems are correctly set according to motor nameplate data and are functioning properly to protect equipment from thermal damage.
stainless steel coil packing machine line1 10. Issue 8: Inefficient Consumption of Packaging Materials
- Verify that motor thermal overload relays, thermistors (if fitted), and Variable Frequency Drive (VFD) temperature monitoring systems are correctly set according to motor nameplate data and are functioning properly to protect equipment from thermal damage.
Problem: Incorrect machine settings or suboptimal parameter choices during start-up can lead to the excessive consumption of packaging materials like stretch film, VCI paper, or strapping. This directly increases operational costs and generates unnecessary industrial waste without proportionally improving coil protection.
Solution:
- Optimize Wrapping Machine Parameters:
- Systematically fine-tune the wrapping machine settings to achieve secure containment with minimal material usage. Key parameters include:
- Number of wraps (top, bottom, body layers).
- Film overlap percentage between layers.
- Pre-stretch ratio (achieving maximum stretch without compromising film integrity).
- Wrapping tension (sufficient to hold layers tight without crushing coil).
- Film carriage speed relative to rotation speed.
- Systematically fine-tune the wrapping machine settings to achieve secure containment with minimal material usage. Key parameters include:
- Select Appropriate Packaging Materials:
- Ensure you are using a stretch film or other wrapping material with the appropriate gauge (thickness), strength, puncture resistance, and pre-stretch capability tailored to your specific coil sizes, weights, and handling requirements. Sometimes, a higher-performance (but initially more expensive) film can allow for significantly reduced material usage per coil (less wraps, higher stretch).
- Calibrate Film/Strap Delivery Systems:
- Verify the accuracy and consistency of the film dispensing system. Ensure pre-stretch rollers are clean, rotating freely, and achieving the set pre-stretch ratio reliably.
- For strapping, check that the feed length is consistent and minimal strap is wasted during the cutting/sealing cycle.
- Track and Monitor Material Consumption:
- Implement a system to track material usage per coil, per shift, or per day during the start-up and initial production phase. This allows you to establish benchmarks, identify trends, and quantify the impact of optimization efforts. Set targets for material efficiency.
11. Issue 9: Communication Faults Between Integrated Systems
Problem: A modern steel coil packaging line is not just one machine, but a network of interconnected modules communicating via a central PLC. Communication breakdowns or timing errors between the PLC and different stations (e.g., the conveyor failing to signal coil arrival to the wrapper, the strapper not confirming cycle completion to allow conveyor restart) are common start-up frustrations. These faults can cause:
- Unexpected line stoppages.
- Incorrect operational sequences.
- Potential collisions between moving parts.
- Difficult-to-diagnose intermittent problems.
Solution:
- Verify Network Cabling and Connections:
- Physically inspect all network cables (e.g., Ethernet/IP, Profinet, Profibus) and hardwired communication links between the main PLC, remote I/O racks, HMIs, sensors, drives, and individual machine controllers.
- Ensure all connectors are securely seated, properly terminated, shielded (if required), and show no signs of damage or strain. Check cable routing to avoid electromagnetic interference sources.
- Systematically Test Handshake Signals:
- During commissioning, methodically test the crucial "handshake" signals between each interconnected piece of equipment. For example:
- Confirm the upstream conveyor sends a "ready to receive coil" signal.
- Verify the downstream machine receives a "coil in position" signal before starting its cycle.
- Ensure the machine sends a "cycle complete" signal before the downstream conveyor is permitted to start.
- Use the PLC monitoring software or HMI diagnostics screens to observe these signals in real-time.
- During commissioning, methodically test the crucial "handshake" signals between each interconnected piece of equipment. For example:
- Review and Debug PLC Logic:
- Carefully examine the PLC programming logic that governs the inter-machine communication, sequencing, and interlocking.
- Pay close attention to timing parameters (timers, counters), permissive conditions, and error handling routines associated with communication signals. Ensure the logic is robust and accounts for potential variations in cycle times.
- Ensure Software/Firmware Compatibility:
- Confirm that all intelligent devices on the network (PLC, HMI, drives, controllers, smart sensors) are running compatible software and firmware versions as specified by the line integrator or equipment manufacturers. Version mismatches can sometimes lead to subtle communication incompatibilities.
- Utilize Centralized Monitoring Tools:
- Leverage the capabilities of the Human-Machine Interface (HMI) or any overarching SCADA (Supervisory Control and Data Acquisition) system to monitor the status, operational mode, and communication links between different parts of the line. These systems often provide diagnostic tools that can help pinpoint communication faults rapidly.
12. The Critical Role of Operator Training in Preventing Start-Up Issues
Overlooked Yet Paramount: Perhaps the most critical factor, often underestimated, is the quality and thoroughness of operator training. A successful start-up and sustained efficient operation heavily depend on operators who understand the line's functionality, potential issues, and correct operating procedures. Operators unfamiliar with the nuances of a new or upgraded automated packaging system are more likely to make errors, misinterpret warnings, or fail to spot developing problems before they cause significant downtime.
Solution:
- Develop a Comprehensive Training Program:
- Provide structured, role-specific training that covers:
- Machine operation sequences and controls.
- Understanding and adjusting key parameters (tension, speed, overlap, recipes).
- Performing routine operator checks (cleaning, visual inspection, basic lubrication).
- Recognizing common fault indicators and performing basic troubleshooting steps.
- Safety procedures, lockout/tagout (LOTO), and emergency stops.
- Navigating and utilizing the HMI screens effectively.
- Provide structured, role-specific training that covers:
- Incorporate Hands-On Practice:
- Allocate sufficient supervised, hands-on time for operators to practice operating the equipment during the later stages of commissioning and initial production runs. Theory needs to be reinforced with practical experience.
- Provide Clear and Accessible Documentation:
- Ensure operators have easy access to well-written, clear, and concise operating manuals, standard operating procedures (SOPs), quick-reference guides, and troubleshooting flowcharts, preferably available digitally at the HMI or workstations.
- Empower Operators for First-Level Response:
- Train and authorize operators to handle minor adjustments, clear common jams (following safety protocols), and perform basic, predefined troubleshooting tasks. This reduces reliance on maintenance staff for simple issues, improving uptime.
- Foster Continuous Learning and Feedback:
- Offer periodic refresher training sessions and provide updates whenever processes, materials, or equipment parameters change. Encourage operators to provide feedback on procedures and potential improvements.
vertical coil packaging line4 Conclusion: A Proactive Strategy for Successful Packaging Line Start-Up
- Offer periodic refresher training sessions and provide updates whenever processes, materials, or equipment parameters change. Encourage operators to provide feedback on procedures and potential improvements.
Commissioning a new or upgraded steel coil packaging line inevitably involves navigating potential obstacles. However, adopting a proactive, systematic, and detail-oriented approach can significantly mitigate the frequency and impact of common start-up problems.
Success hinges on several key pillars:
- Meticulous Setup and Calibration: Ensuring all mechanical components, sensors, and control parameters are configured correctly from the outset.
- Thorough Testing and Validation: Running simulated and real product tests to verify functionality, sequencing, and performance under various conditions.
- Comprehensive Operator Training: Equipping the team with the knowledge and skills to operate the line effectively and safely.
- Robust Communication Verification: Ensuring seamless interaction between all integrated system components.
Furthermore, establishing rigorous preventative maintenance routines right from day one, conducting diligent monitoring during the initial operational phase, and fostering a collaborative culture where operators feel empowered to identify and report issues early are crucial.
Addressing potential challenges like coil misalignment, wrapping and strapping faults, sensor errors, electrical instability, and system communication glitches head-on during start-up not only ensures a smoother commissioning process but also lays a solid foundation for the long-term reliability, efficiency, safety, and optimal performance of your valuable automated packaging system. Investing the necessary time and resources to get the start-up phase right is a direct investment in preventing costly future downtime, quality defects, and operational headaches.