A Fabricator's Guide to Selecting Steel Tube Bundling Equipment
Efficiently handling and packaging steel tubes is crucial for streamlining operations in metal fabrication and processing facilities. Steel tube bundling machines automate the process of gathering, arranging, and securing tubes into stable bundles, improving handling efficiency, worker safety, and package integrity for transport and storage. Selecting the right equipment requires careful consideration of operational needs and available technology.
Key Considerations Before Sourcing Tube Bundling Machinery
Before searching for specific suppliers, thoroughly define your application requirements. This ensures you invest in a system that truly meets your needs:
- Tube Specifications: Document the full range of tubes you handle, including:
- Material (e.g., carbon steel, stainless steel, copper, aluminum)
- Diameter Range
- Length Range
- Wall Thickness
- Surface Finish (potential for scratching)
- Bundle Configuration: Determine the desired bundle characteristics:
- Shape: Hexagonal, square, or rectangular bundles are common. Hexagonal bundles often provide better packing density.
- Size & Weight: Specify the target dimensions (cross-section) and maximum weight per bundle, aligning with downstream handling equipment (cranes, forklifts) and transport limitations.
- Required Throughput: Calculate the number of tubes or bundles needed per hour or shift. This dictates the necessary speed and automation level of the bundling line.
- Level of Automation: Choose the appropriate level based on throughput, labor availability, and budget:
- Manual: Operator manually arranges tubes and initiates strapping. Suitable for low-volume operations.
- Semi-Automatic: Machine assists with forming or strapping, but requires significant operator involvement.
- Fully Automatic: Integrated systems handle counting, layering, forming, strapping, and potentially weighing and labeling with minimal operator intervention. Ideal for high-volume production. Explore options like an automatic tube bundling and strapping machine for maximum efficiency.
- Integration: How will the bundling machine fit into your existing production line? Consider upstream processes (e.g., cutting, finishing) and downstream steps (e.g., weighing, storage, loading).
- Strapping/Wrapping Needs: Specify the type (steel or plastic strap), number of straps per bundle, and tension requirements. Some applications may require stretch wrapping for added protection or stability.
- Budget and ROI: Establish a realistic budget considering the initial investment, installation, training, and ongoing operational costs. Calculate the potential return on investment based on labor savings, increased throughput, and improved safety.
Effective Strategies for Finding Steel Tube Bundling Solutions
Once your requirements are clear, use these methods to identify suitable equipment and suppliers:
1. Industry Trade Shows and Exhibitions
Events like FABTECH (link to relevant trade show site, e.g., https://www.fabtechexpo.com/) are invaluable. They allow you to:
- See machinery in operation.
- Compare different manufacturers side-by-side.
- Discuss technical specifications directly with engineers.
- Network with industry peers and learn about their experiences.
2. Online Research and Supplier Directories
Utilize targeted online searches using specific keywords:
- "Steel tube bundling machine"
- "Automatic pipe bundling line"
- "Hexagonal tube bundler"
- "Tube packaging systems"
- "Industrial pipe handling equipment"
Look beyond basic search results. Explore online industrial equipment directories and manufacturer websites. Focus on suppliers providing detailed technical specifications, videos of their equipment in action, and case studies.
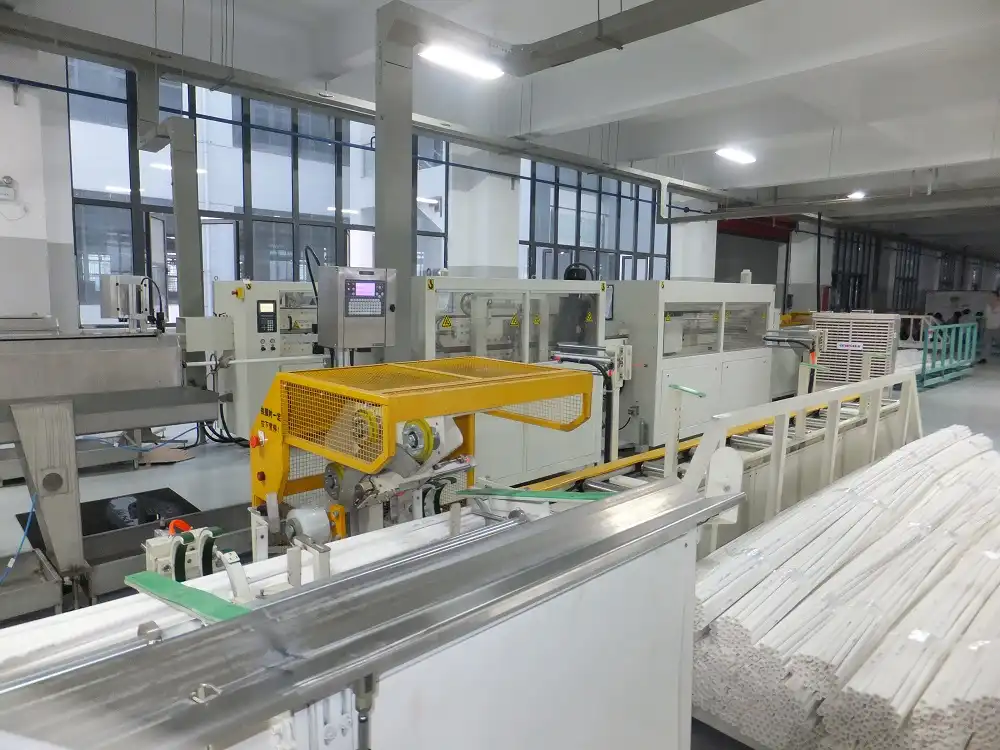
3. Leveraging Industry Publications and Online Resources
Trade magazines (like The Fabricator) and specialized websites often feature articles, technical papers, and supplier directories related to tube and pipe processing and handling technology. These resources provide insights into current trends and reputable manufacturers.
4. Consulting with Equipment Manufacturers and Integrators
Contact manufacturers directly who specialize in tube handling and packaging. Many offer consultation services to help tailor solutions. Look for companies experienced in building automatic steel tube packing lines if high levels of automation are required. Be prepared to share your detailed requirements. System integrators can also be valuable partners, especially for complex, multi-component lines.
5. Networking and Peer Recommendations
Talk to colleagues, contacts at other fabrication shops, or members of industry associations. Referrals from trusted sources who have experience with specific suppliers or types of equipment can provide valuable, real-world insights into reliability, performance, and after-sales support.
Evaluating Potential Suppliers
Once you have a shortlist, evaluate potential suppliers based on:
- Technical Specification Match: Does the proposed equipment precisely meet your documented requirements?
- Customization Capabilities: Can they adapt the standard machine to accommodate unique tube sizes or bundle configurations?
- Installation, Training, and Support: What level of support is offered during and after installation? Is operator training included? What is their service response time?
- References and Case Studies: Request references from companies with similar applications. Review detailed case studies if available.
- Lead Time and Delivery: Understand the manufacturing lead time and delivery schedule.
automatic pipe bagging machine for pvc and ppr (1) Conclusion
Finding the right steel tube bundler and bundling machine is a critical step in optimizing your material handling process. By clearly defining your operational requirements, leveraging industry resources, and thoroughly vetting potential suppliers, you can select equipment that enhances efficiency, improves safety, and delivers a strong return on investment for your fabrication facility. A methodical approach ensures the chosen solution aligns perfectly with your production needs.