How to Ensure Minimum Downtime with a Well-Supported Steel Coil Packing Line
- How to Ensure Minimum Downtime with a Well-Supported Steel Coil Packing Line
- Introduction
- 1. Understanding the Causes of Downtime in Steel Coil Packing Lines
- 2. The Importance of Preventive Maintenance
- 3. Real-Time Monitoring and Predictive Maintenance
- 4. Implementing an Efficient Material Management System
- 5. Training and Skill Development for Operators
- 6. The Role of Automation in Reducing Downtime
- 7. Optimizing System Design for Maximum Uptime
- 8. Partnering with Reliable Equipment Manufacturers and Service Providers
- 9. Continuous Improvement through Data and Feedback Loops
- 10. Regular Audits and System Reviews
- Conclusion
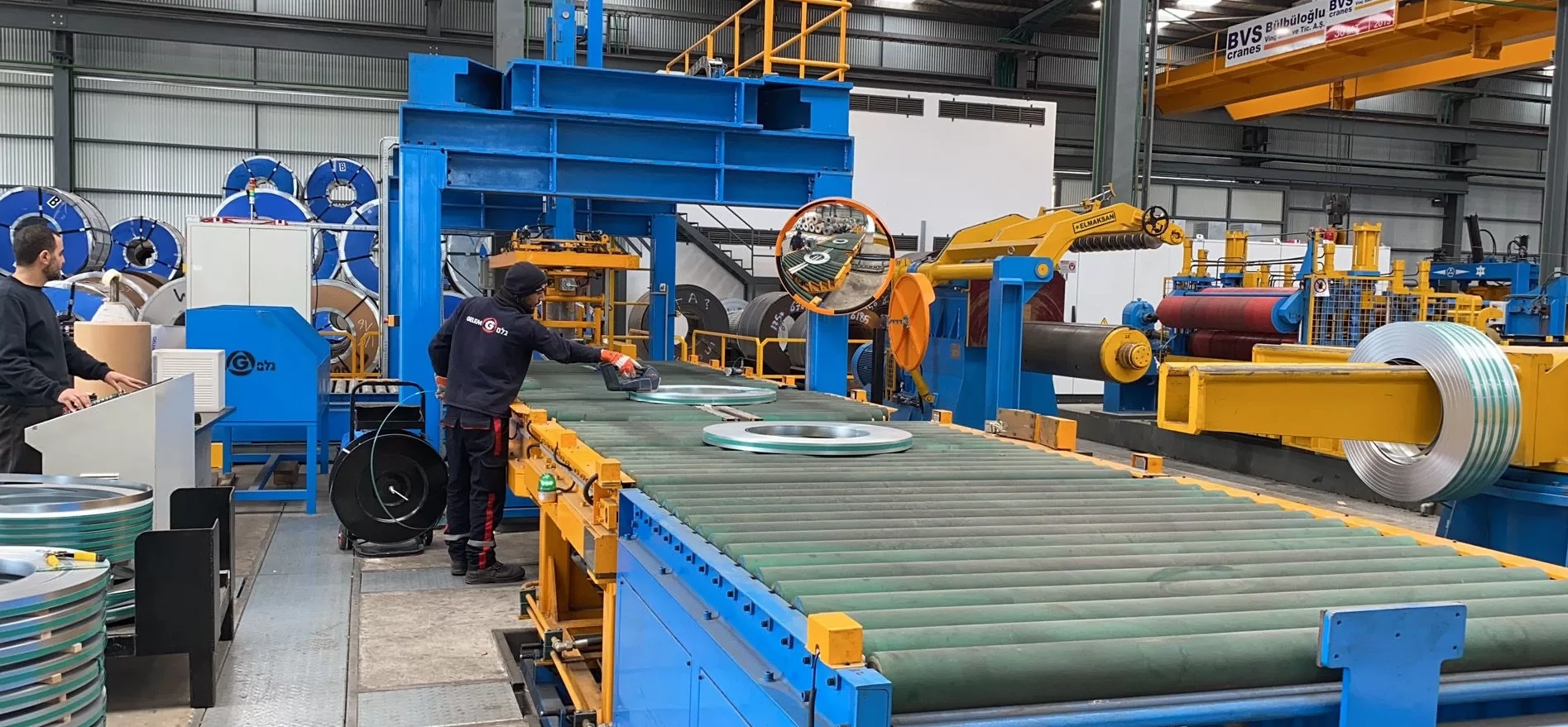
Introduction
In the world of industrial manufacturing, particularly in the steel industry, ensuring continuous operation with minimal downtime is critical to maintaining high levels of productivity and profitability. A steel coil packing line is one of the key areas where downtime can have a significant impact on the overall efficiency of operations. Whether due to mechanical failures, lack of preventive maintenance, or poor system integration, unplanned downtime can lead to costly delays and lost revenue.
In this article, we will explore the best practices and strategies to ensure minimum downtime in a steel coil packing line. By implementing these approaches, companies can improve the reliability and performance of their packing systems, reduce maintenance costs, and ensure that their operations run smoothly. With a focus on preventive maintenance, real-time monitoring, skilled support, and effective system design, this article will provide actionable insights that can be applied to steel coil packing operations of any size.
1. Understanding the Causes of Downtime in Steel Coil Packing Lines
Common Downtime Causes
Downtime in a steel coil packing line can be attributed to various factors, both mechanical and operational. Understanding these causes is the first step toward minimizing their impact. Some of the most common causes include:
- Mechanical Failures: Equipment breakdowns, such as failures in motors, conveyor belts, or wrapping mechanisms, are a major cause of unplanned downtime.
- Operator Errors: Incorrect machine settings, improper handling of coils, or a lack of training can result in system malfunctions or delays.
- Material Shortages: Insufficient packing materials, such as strapping or wrapping film, can halt operations until supplies are replenished.
- Software Issues: In systems that rely on automation and software controls, bugs or errors in the control system can disrupt operations.
- Scheduled Maintenance: While necessary, poorly timed or overly frequent maintenance can also contribute to downtime, especially if not well-coordinated.
Identifying the root causes of downtime allows companies to implement targeted strategies to address these issues and keep the packing line running smoothly.
2. The Importance of Preventive Maintenance
How Preventive Maintenance Reduces Downtime
One of the most effective strategies for reducing downtime is the implementation of a comprehensive preventive maintenance program. Unlike reactive maintenance, which addresses equipment breakdowns after they occur, preventive maintenance focuses on regular inspections, servicing, and part replacements to prevent failures before they happen.
Key Elements of Preventive Maintenance
- Scheduled Inspections: Regular inspections of critical components, such as conveyors, wrapping arms, and strapping tools, help to identify wear and tear before it leads to a breakdown.
- Lubrication and Cleaning: Ensuring that moving parts are well-lubricated and free from debris reduces the risk of mechanical failures caused by friction or blockages.
- Replacement of Wear Parts: Certain parts, such as belts and rollers, experience more wear and tear than others. Replacing these parts on a fixed schedule helps avoid unexpected breakdowns.
By implementing preventive maintenance, companies can significantly reduce the likelihood of sudden equipment failures and prolong the lifespan of their steel coil packing systems.
3. Real-Time Monitoring and Predictive Maintenance
Leveraging IoT for Real-Time Monitoring
In today’s industrial environment, Internet of Things (IoT) technology is playing a pivotal role in reducing downtime through real-time monitoring and predictive maintenance. IoT-enabled sensors can be integrated into the steel coil packing line to monitor key parameters such as temperature, vibration, motor speed, and pressure.
How Real-Time Monitoring Helps
- Early Detection of Anomalies: Sensors detect abnormal readings in real-time, such as increased vibration or overheating, and alert operators before the issue escalates into a full-blown failure.
- Remote Monitoring: Operators can monitor the system remotely through dashboards, allowing for immediate intervention if issues arise, even outside of normal working hours.
- Data Analytics for Predictive Maintenance: By analyzing data from the IoT sensors, companies can predict when certain components are likely to fail and schedule maintenance accordingly. This predictive maintenance approach minimizes unplanned downtime and ensures the system runs at optimal efficiency.
Benefits of Predictive Maintenance
Predictive maintenance goes a step beyond preventive maintenance by using data-driven insights to predict when equipment needs attention. This proactive approach allows companies to reduce unplanned maintenance, avoid costly repairs, and minimize downtime.
4. Implementing an Efficient Material Management System
Ensuring Continuous Supply of Packing Materials
Another key factor in minimizing downtime is ensuring a continuous supply of packing materials, such as steel strapping, plastic wrap, and protective coatings. Material shortages can bring the packing line to a standstill, particularly in high-volume operations where even a brief delay can lead to significant production losses.
Best Practices for Material Management
- Automated Inventory Tracking: Implement an automated inventory tracking system that uses sensors to monitor the stock levels of packing materials in real-time. This system can trigger automatic reorders when supplies are low, ensuring that materials are always on hand when needed.
- Supplier Reliability: Partner with reliable suppliers who can deliver materials quickly and consistently. Establishing strong relationships with key suppliers ensures that you have access to urgent supplies in case of unexpected demand surges.
- Buffer Stock: Maintain a buffer stock of essential materials to cover any unexpected supply chain disruptions or delivery delays.
By managing material flow efficiently, companies can prevent downtime caused by material shortages and keep the packing line running without interruptions.
5. Training and Skill Development for Operators
Why Operator Training is Essential
Operator error is another common cause of downtime in steel coil packing systems. Insufficient training can lead to improper machine settings, mishandling of materials, or failure to recognize early warning signs of equipment malfunctions. To minimize downtime, it is crucial to invest in operator training and skill development.
Key Areas of Focus for Operator Training
- Machine Operation: Operators should be thoroughly trained in the correct operation of all equipment in the packing line, including how to adjust settings for different coil sizes and materials.
- Troubleshooting: Training operators to identify and troubleshoot common issues can prevent minor problems from escalating into larger ones that require system shutdowns.
- Safety Protocols: Ensuring that operators understand and follow safety protocols reduces the risk of accidents that can lead to system stoppages.
By empowering operators with the skills and knowledge they need, companies can minimize errors that lead to downtime and ensure smooth and efficient operation of the packing line.

6. The Role of Automation in Reducing Downtime
How Automation Streamlines Operations
Automation plays a critical role in reducing downtime by eliminating manual errors and ensuring that operations run smoothly with minimal human intervention. In a steel coil packing line, automation can enhance efficiency in several ways:
- Automated Wrapping and Strapping: Automated systems can accurately wrap and strap steel coils without the variability that comes with manual labor. This not only ensures consistency but also speeds up the process, reducing the risk of delays.
- Automated Diagnostics: Modern packing lines come equipped with self-diagnostic systems that can detect issues early on. These systems notify operators of potential problems, allowing for timely intervention before downtime occurs.
- Continuous Operation: Automation allows the packing line to operate continuously, with minimal stops, as robots and automated machinery handle most of the work.
Automation also enables predictive analytics, where real-time data is used to foresee potential breakdowns or material shortages, further reducing the chances of downtime.
7. Optimizing System Design for Maximum Uptime
The Importance of Well-Designed Systems
One of the key factors that can influence downtime in a steel coil packing line is the design of the system itself. A poorly designed system may be prone to frequent breakdowns, difficult maintenance, and inefficiencies that lead to more frequent interruptions. On the other hand, a well-engineered packing line is built to run smoothly, minimizing points of failure and optimizing throughput.
Key Aspects of an Optimized System Design
- Modularity: Modular system design allows for individual components of the packing line to be maintained or replaced without shutting down the entire operation. This means that if a conveyor or wrapping machine requires maintenance, the rest of the system can continue to function.
- Redundancy: Incorporating redundant systems, such as backup power supplies or secondary wrapping stations, ensures that the line can continue running even if one component fails. Redundancy helps maintain operational continuity in the event of a failure.
- Ergonomic Layout: The physical layout of the packing line should be designed to minimize bottlenecks and allow for easy access to machines for maintenance and adjustments. This can help operators troubleshoot and resolve issues more quickly, reducing downtime.
- Integrated Control Systems: A unified control system that allows operators to monitor and control the entire packing line from a single interface can greatly reduce the time needed to make adjustments or respond to alarms.
An optimized system design helps ensure that maintenance tasks are easier to perform, breakdowns are less frequent, and the entire operation runs with fewer interruptions.
8. Partnering with Reliable Equipment Manufacturers and Service Providers
Choosing the Right Equipment Supplier
To minimize downtime, it is crucial to partner with reliable manufacturers and service providers who offer high-quality equipment and responsive support. The reliability of the machines in a steel coil packing line is directly related to the quality of the equipment and the after-sales service provided by the manufacturer.
What to Look for in a Manufacturer
- Proven Track Record: Look for manufacturers with a history of producing durable, high-performance equipment for the steel industry. Reading customer testimonials and case studies can provide insight into how well the equipment performs in real-world scenarios.
- After-Sales Support: A strong after-sales support team is essential for minimizing downtime. The manufacturer should offer prompt technical support, readily available spare parts, and maintenance services that can help keep your equipment running smoothly.
- Custom Solutions: Every steel coil packing operation is unique. Choose a manufacturer that can provide customized equipment tailored to your specific needs, as this will ensure optimal performance and a longer operational life for your packing line.
By working with reliable partners, companies can ensure they have access to the right equipment, maintenance support, and expertise needed to keep their packing line running at maximum efficiency.
9. Continuous Improvement through Data and Feedback Loops
Using Data to Drive Continuous Improvement
In a modern steel coil packing line, data collection and analysis are key components of ensuring continuous improvement and minimizing downtime. With the increasing use of IoT and automation, companies now have access to a wealth of data related to equipment performance, material usage, and packing line efficiency.
How to Use Data Effectively
- Performance Metrics: Continuously tracking key performance indicators (KPIs) such as cycle times, material usage, and machine uptime allows companies to identify areas of improvement.
- Feedback Loops: Implementing feedback loops, where data is used to refine processes, helps companies make data-driven decisions to optimize performance. For example, analyzing data on the wear patterns of certain components can inform more precise maintenance schedules, ensuring that parts are replaced before they fail.
- Root Cause Analysis: When downtime does occur, it’s important to use data to conduct a thorough root cause analysis. By identifying the underlying causes of downtime, companies can implement targeted solutions to prevent similar issues from arising in the future.
Data-driven continuous improvement ensures that the packing line is always evolving, reducing downtime and improving efficiency over time.
10. Regular Audits and System Reviews
Why Regular Audits are Essential
Even the most well-maintained systems can benefit from regular audits and reviews to ensure that they are performing optimally. Regular audits help identify any emerging issues or inefficiencies that could lead to downtime in the future.
Key Areas to Audit
- Equipment Performance: Assess the performance of key components in the packing line to ensure they are operating efficiently. Look for signs of wear, energy inefficiencies, or outdated technology that could be replaced with more efficient alternatives.
- Process Efficiency: Review the entire packing process to identify any bottlenecks, unnecessary steps, or areas where automation could improve speed and reduce downtime.
- Compliance and Safety: Regular audits should also ensure that the packing line meets all safety and regulatory standards. Non-compliance can result in costly fines and unexpected shutdowns.
By conducting regular audits, companies can take a proactive approach to identifying and resolving potential issues before they result in downtime.
Conclusion
Ensuring minimum downtime in a steel coil packing line requires a combination of preventive maintenance, real-time monitoring, automation, and strategic system design. By leveraging predictive maintenance technologies, training operators effectively, managing material supplies, and continuously optimizing processes through data analysis, companies can significantly reduce unplanned downtime and improve overall operational efficiency.
Partnering with reliable equipment manufacturers and conducting regular audits further strengthens the packing line’s ability to run smoothly with minimal interruptions. By adopting these best practices, companies can maintain high levels of productivity, reduce maintenance costs, and maximize their return on investment. The result is a well-supported, efficient steel coil packing system that delivers consistent performance with minimal downtime.