How to Choose the Right Board Turning Machine / Pallet Inverter for Your Business
Selecting the right board turning machine, often referred to as a pallet inverter or load turner, is a critical decision for any business involved in material handling. Whether you're managing a warehouse, manufacturing facility, or distribution center, the appropriate equipment significantly impacts operational efficiency, safety, and your bottom line. Making the optimal choice can seem complex, but understanding your specific needs is key.
Choosing incorrectly can lead to inefficiencies, increased operational costs, and potential safety hazards. Conversely, the right pallet changing machine streamlines operations, reduces manual labor costs, and enhances workplace safety. Success lies in aligning the machine’s capabilities with your unique requirements, considering factors such as your factory layout, existing material handling processes, load types, and production throughput demands.
Every facility operates differently. The pallet inverter you select must integrate smoothly into your workflow, respect space limitations, and ideally accommodate future growth. Let’s break down the essential factors to guide your decision, ensuring you choose a machine that meets both current needs and future-proofs your operations.
Table of Contents
- What Are the Key Benefits of Using a Pallet Inverter?
- How Do I Choose Between an Offline and an Inline Pallet Inverter?
- What Role Does Factory Layout Play in Selecting the Right Machine?
- How Can I Maximize Efficiency with the Right Pallet Inverter Choice?
1. What Are the Key Benefits of Using a Pallet Inverter?
Automating the process of turning, swapping, or inverting palletized loads offers substantial advantages.
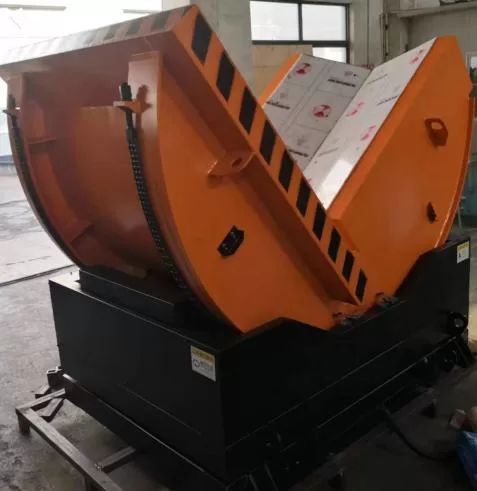
1.1 Increased Efficiency and Reduced Labor Costs
A primary benefit of using a board turning machine or pallet inverter is the significant boost in operational efficiency. Automating the process of flipping, rotating, or transferring loads between pallets drastically cuts down manual handling time. This automation frees up workers from strenuous, repetitive tasks, allowing them to be redeployed to more value-added activities, optimizing overall productivity.
Furthermore, automation directly translates to reduced labor costs. Fewer personnel are needed for manual handling, and automated systems provide consistent output without breaks or overtime, ensuring predictable performance even during peak production demands.
1.2 Improved Workplace Safety
Manual handling of heavy or awkward loads like stacks of boards or palletized goods presents significant risks of musculoskeletal injuries from lifting, bending, and twisting. Pallet inverters automate these tasks, dramatically reducing the risk of workplace accidents. Adhering to safety guidelines, such as those outlined by OSHA for material handling, is crucial. By minimizing manual handling risks, you decrease the likelihood of injuries, leading to fewer workers’ compensation claims, reduced downtime, and a safer, more positive work environment for your staff. The long-term impact of enhanced safety contributes significantly to operational stability and employee morale.
1.3 Consistent Handling and Workflow Optimization
Machines offer superior consistency compared to manual labor, especially for repetitive tasks. A pallet inverter performs the same turning or transfer operation with precision every time, eliminating handling errors, minimizing product damage, and ensuring uniform load integrity. This consistency is vital in industries like food and beverage, pharmaceuticals, printing, and construction materials, where precise handling is essential for quality control. By automating load inversion, you reduce the risk of defects, ensure smoother workflow transitions, and maintain a steady production pace.
2. How Do I Choose Between an Offline and an Inline Pallet Inverter?
Pallet inverters generally fall into two categories based on their integration into your workflow: Offline (standalone) and Inline (integrated).
2.1 Offline Pallet Inverter (Standalone)
An offline pallet inverter operates as a standalone unit, typically loaded and unloaded using a forklift or pallet jack. The typical process involves:
- Loading the palletized goods (e.g., boards, boxes, bags) onto the machine's platform.
- Placing a new target pallet on top of the load (or below, depending on the machine design).
- Activating the machine, which clamps the load securely and rotates it (often 180 degrees).
- Removing the original pallet.
- Unloading the inverted load on the new pallet using a forklift.
Key Characteristics:
- Flexibility: Can be placed anywhere with sufficient space and access.
- Lower Initial Cost: Generally less expensive than fully integrated inline systems.
- Forklift Dependent: Relies on manual loading/unloading via forklift, which can affect cycle time.
- Suitable For: Lower to moderate throughput operations, facilities where full automation isn't required, or tasks like swapping rental pallets, recovering damaged goods, or switching to hygienic pallets.
This system offers significant efficiency gains over purely manual methods but may introduce bottlenecks if forklift availability is limited or if cycle time is critical.
2.2 Inline Pallet Inverter (Integrated)
An inline pallet inverter is designed for seamless integration into an automated production or conveyor line. Loads arrive via conveyor, are automatically fed into the inverter, processed, and then exit onto another conveyor.
- Palletized load enters the machine via an input conveyor.
- A new pallet is automatically dispensed or manually placed.
- The machine clamps, inverts (typically 180 degrees), and transfers the load.
- The original pallet is automatically ejected or manually removed.
- The load exits on the new pallet via an output conveyor.
Key Characteristics:
- High Throughput: Designed for continuous, high-volume operations.
- Fully Automated: Minimal manual intervention required, reducing labor needs and human error.
- Seamless Integration: Connects directly with upstream and downstream automated systems (conveyors, wrappers, AGVs).
- Higher Initial Cost: Requires a larger investment due to automation components and integration complexity.
- Suitable For: High-volume manufacturing and distribution centers, industries requiring consistent, fast pallet transfers integrated within a production line.
Inline systems maximize speed and efficiency, making them ideal for large-scale operations where minimizing handling time and labor is paramount.
2.3 Making the Right Choice: Offline vs. Inline
The decision hinges on your operational scale, workflow, budget, and automation goals:
- Choose Offline if:
- Your throughput needs are moderate.
- You require flexibility in machine placement.
- Your budget is constrained.
- Full automation is not a primary goal or feasible currently.
- You primarily use forklifts for material movement around the inverter.
- Choose Inline if:
- You have high-volume pallet handling requirements.
- You need seamless integration into an existing or planned automated conveyor line.
- Maximizing speed and minimizing manual labor are critical priorities.
- You have the budget for a higher initial investment for long-term efficiency gains.
Carefully assess your production volume, workflow patterns, and strategic automation plans to determine the best fit.
3. What Role Does Factory Layout Play in Selecting the Right Machine?
Your facility's physical layout profoundly influences the type and placement of a pallet inverter.
3.1 Assessing Your Current Factory Layout and Workflow
Before selecting a machine, thoroughly analyze your current material flow:
- Where do raw materials enter and finished goods exit?
- What are the primary paths for pallet movement?
- Are there existing bottlenecks in material handling?
- How much space is available in potential locations for the inverter?
- What are the floor loading capacities?
Understanding these dynamics helps identify the optimal location and type of machine (offline vs. inline, stationary vs. mobile options if available) that enhances, rather than hinders, your workflow.
3.2 Maximizing Space Utilization and Workflow Efficiency
Space is often a premium resource. The chosen pallet inverter must fit comfortably within your layout without obstructing traffic lanes or critical operational areas.
- Offline machines: Require clear access for forklifts from potentially multiple sides.
- Inline machines: Need dedicated space within a conveyor line, considering entry, exit, and potential buffering zones.
Consider mobile pallet inverter options if turning needs occur at multiple, non-fixed locations. Effective facility layout planning aims to minimize travel distances and handling steps, and the pallet inverter should support this goal.
3.3 Considering Machine Footprint and Customization
Pallet inverters come in various sizes and configurations. Measure your available space accurately and compare it against the machine's footprint, including operational clearances. Many manufacturers offer customization options:
- Modified dimensions for tight spaces.
- Specific clamping mechanisms for delicate or unusual loads.
- Variable rotation speeds or degrees.
- Integration features for specific conveyor types or control systems.
Clearly communicate your layout constraints and operational needs to potential suppliers to explore suitable standard models or necessary customizations.
4. How Can I Maximize Efficiency with the Right Pallet Inverter Choice?
Choosing the right machine is the first step; optimizing its use is crucial for realizing the full benefits.
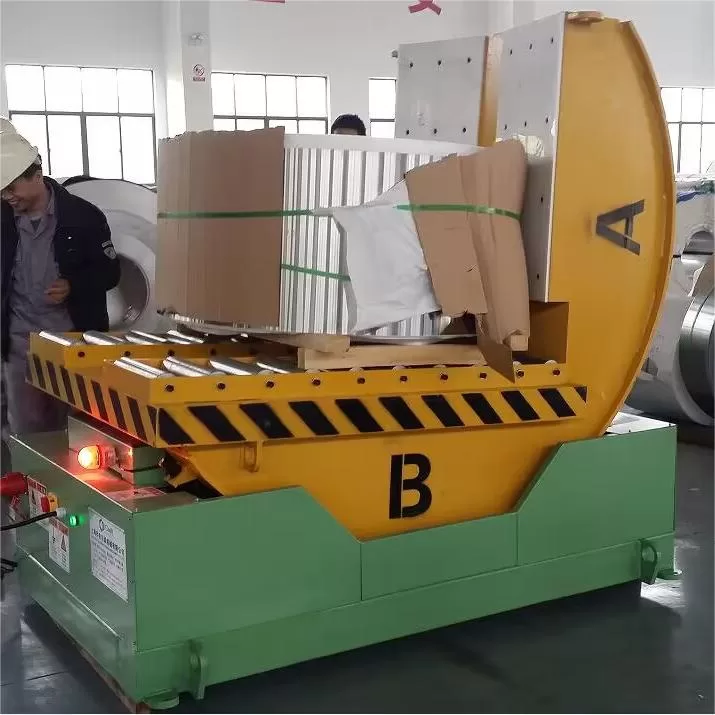
4.1 Aligning Machine Capabilities with Production Demands
Ensure the selected machine's specifications match your actual needs:
- Load Capacity: Can it handle your heaviest and largest pallet loads?
- Cycle Time: Does its speed meet your required throughput? (e.g., pallets per hour)
- Pallet Type Compatibility: Does it work with the types and sizes of pallets you use (wood, plastic, CHEP, etc.)?
- Load Type Suitability: Is the clamping pressure and method appropriate for your products (e.g., boxes, bags, fragile items)?
Avoid over-investing in capabilities you don't need or under-investing and creating a new bottleneck. A careful match ensures optimal performance and return on investment.
4.2 Reducing Downtime Through Proper Maintenance
Like any equipment, pallet inverters require regular maintenance to operate reliably and efficiently.
- Preventive Maintenance: Follow the manufacturer's recommended schedule for inspections, lubrication, and parts replacement.
- Operator Training: Ensure staff are trained on proper operation and basic upkeep.
- Spare Parts: Keep critical spare parts on hand to minimize downtime during unexpected failures.
Proactive maintenance prevents costly breakdowns, extends the machine's lifespan, and ensures consistent performance, safeguarding your investment.
4.3 Leveraging Automation for Streamlined Operations
Maximize the benefits of your investment by fully leveraging its automation potential.
- Integration (Inline): Ensure seamless communication and synchronization with connected conveyors and control systems.
- Workflow Optimization (Offline): Plan forklift routes and staging areas around the offline inverter to minimize travel time and waiting.
- Data Monitoring: If available, utilize machine diagnostics and performance data to identify potential issues or areas for further optimization.
Automation reduces manual touchpoints, minimizes errors, ensures consistent cycle times, and allows personnel to focus on higher-level tasks, ultimately driving overall operational efficiency.
Conclusion
Choosing the right board turning machine or pallet inverter is a strategic decision that can yield significant improvements in efficiency, safety, and cost-effectiveness for your material handling operations. By thoroughly evaluating your specific needs—including production volume, workflow, factory layout, and automation goals—and carefully comparing the capabilities of offline versus inline systems, you can select a solution that delivers tangible benefits.
Understanding your unique operational context, from factory floor constraints to pallet handling processes, empowers you to make an informed choice. Whether you opt for a flexible offline unit or a high-throughput inline system, the right pallet changing machine will streamline workflows, enhance safety, reduce operational costs, and contribute positively to your bottom line for years to come.