Choosing the right packing solution for color-coated steel coils is crucial for ensuring their protection and preventing damage. With the wrong packing method, your products could be prone to scratches, corrosion, or misalignment. It's important to understand how to select the best solution.
Selecting the best packing solution for color-coated steel coils involves balancing protection, efficiency, and cost. Factors like the environment, handling methods, and automation can significantly influence your choice.
The right packing solution ensures that color-coated steel coils are protected from environmental damage and handling issues. Let’s dive into the various packing methods available and how to enhance protection and efficiency.
What Are the Most Effective Packing Methods for Color Coated Steel Coils?
Packing color-coated steel coils is different from packing regular steel coils. The main concern here is to prevent surface damage that can ruin the product's appearance. This requires using the right materials and methods to ensure that the coils stay in optimal condition throughout their journey.
The most effective packing methods for color-coated steel coils include using protective layers, stretch wrapping, and specific cradles. These methods prevent scratches, dents, and exposure to moisture, which can all damage the surface.
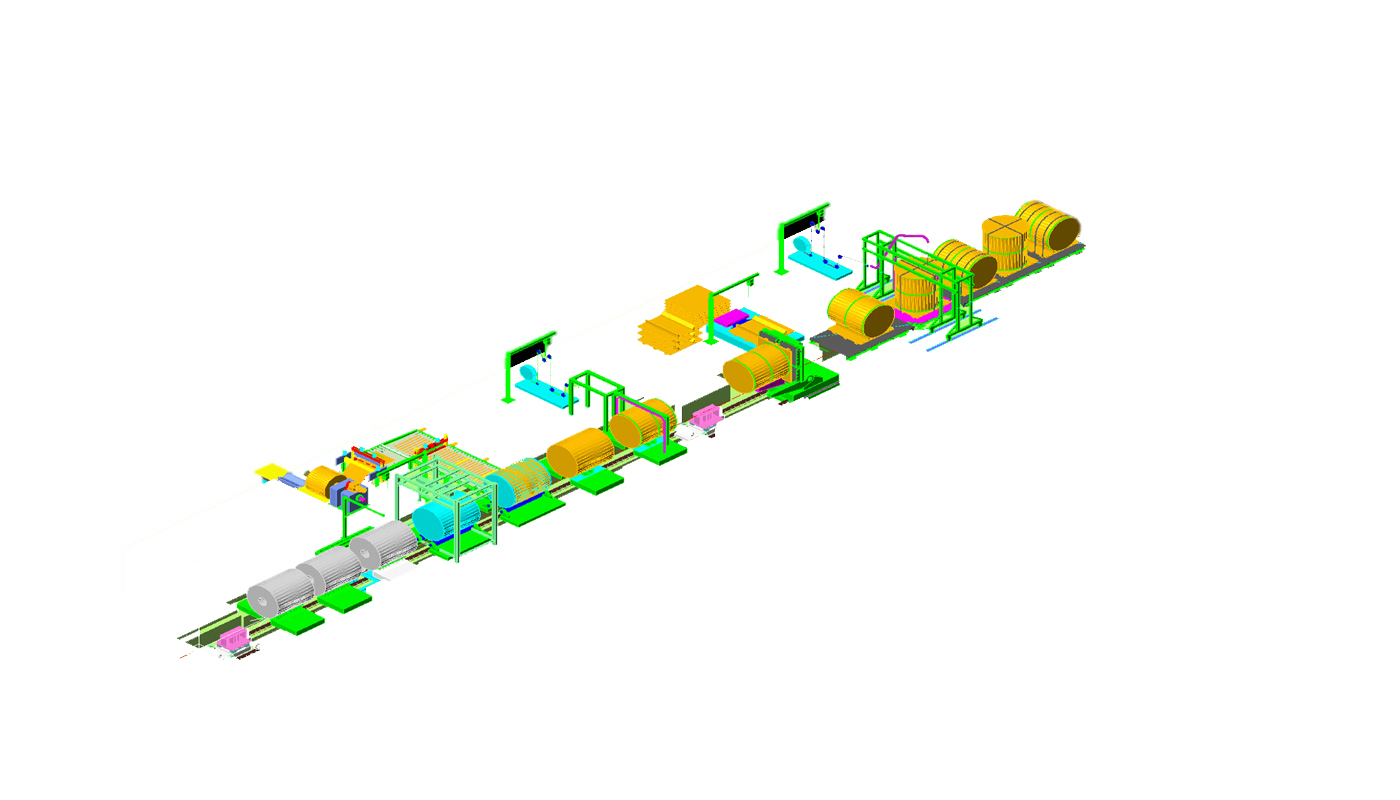
Protective Layers and Stretch Wrapping
Protective layers like plastic films or special paper are often used to shield the color-coated surface from damage. These materials protect the steel from abrasion, corrosion, and any external environmental factors. Stretch wrapping is another widely used method, providing both physical protection and stability during transportation.
One common approach is to use stretch wrap, which is applied tightly around the coil. The wrap keeps the coils securely in place, preventing them from shifting or scratching against other coils. This method is cost-effective and easy to apply, making it ideal for many manufacturers.
Packing Method | Benefits | Potential Drawbacks |
---|---|---|
Protective Films | Shields from scratches and contaminants | Can be less durable in extreme environments |
Stretch Wrapping | Secures coils, prevents shifting | Can be time-consuming without automation |
Coated Paper | Protects against corrosion | Requires careful handling to avoid tears |
Cradles and Custom Racks
Custom cradles and racks are also essential for maintaining coil shape and preventing deformation. When packing color-coated coils, it's important to ensure that the coils remain in their correct position during transportation. Custom racks and cradles are designed to hold the coils securely while providing protection against impact during transit.
While these cradles are effective, they do take up more space than traditional methods. Additionally, they can add to the overall cost, which is why they are often used for higher-end or delicate products.
How Can Automated Packing Systems Enhance Protection and Efficiency?
Automating the packing process can significantly enhance both protection and efficiency. Automated packing systems are designed to handle steel coils with minimal human intervention, ensuring consistency and reducing the risk of damage. These systems can also speed up the packing process, allowing for higher throughput and reduced labor costs.
Automated packing systems improve both the efficiency and protection of color-coated steel coils. With machines designed to apply consistent layers and wraps, the risk of human error is minimized.
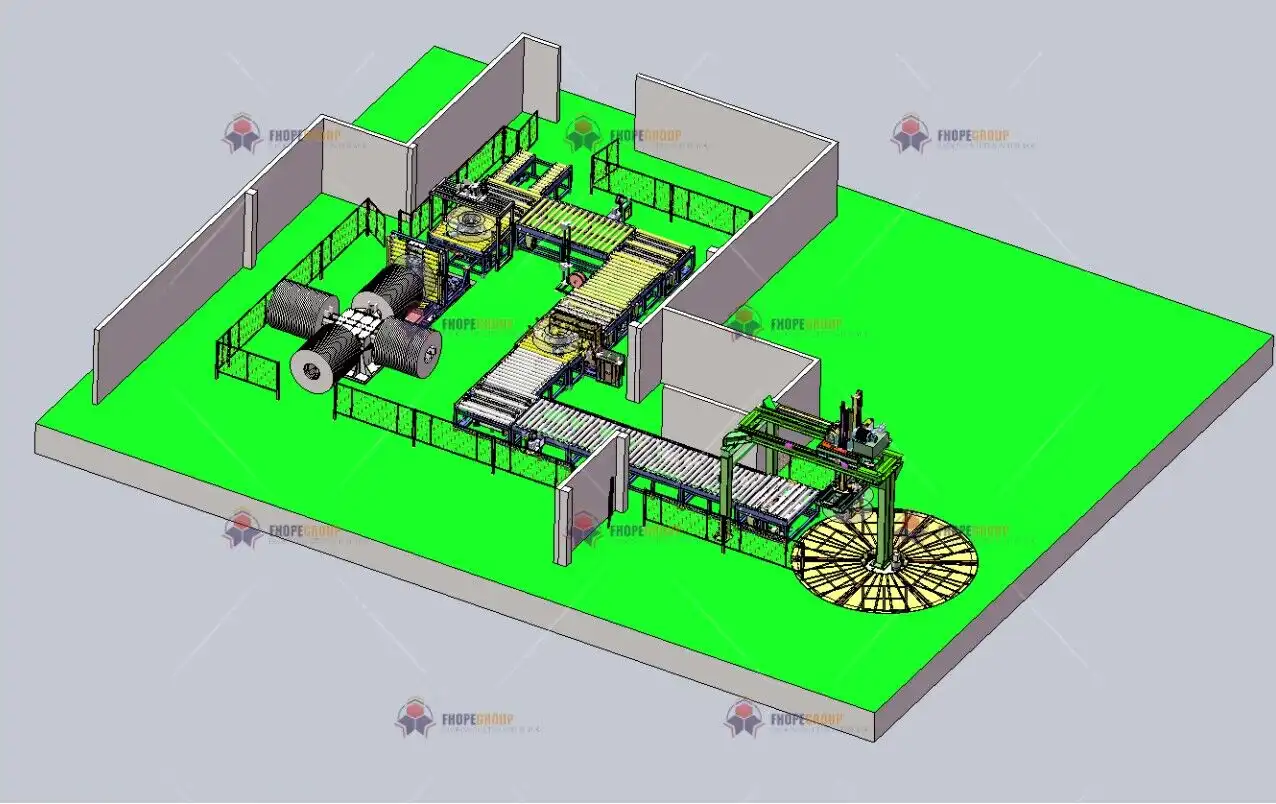
Benefits of Automation in Packing
Automated systems such as coil wrapping machines and pallet inverters improve the quality of packing by consistently applying protective layers. These systems also enhance safety by reducing human interaction with heavy or hazardous materials. With automation, the packing process becomes faster and more reliable, leading to fewer accidents and reduced risk of product damage.
Furthermore, automated systems can work 24/7 without fatigue, increasing the efficiency of production lines. Automation also ensures that the packaging process is standardized, which reduces errors and improves overall product quality.
Automation Type | Advantages | Limitations |
---|---|---|
Coil Wrapping Machines | Consistent wrapping, reduces labor costs | High upfront costs, requires space |
Pallet Inverters | Streamlines handling and reduces damage | Maintenance can be complex |
Robotic Arms | Precise and efficient packing | Requires technical expertise |
Reducing Manual Labor and Enhancing Precision
Manual packing often leads to variability in the wrapping process, which can result in damage. Automated machines, on the other hand, offer precision in their actions, ensuring that each coil is wrapped evenly and securely. By reducing manual labor, these machines free up workers to focus on other aspects of production while maintaining high-quality packing standards.
What Key Factors Should Be Considered When Selecting a Packing Solution?
When selecting a packing solution for color-coated steel coils, several factors need to be considered to ensure the solution meets both practical and economic needs. These factors include the type of coil, transportation methods, environmental conditions, and cost-effectiveness.
Selecting the right packing solution requires considering factors like the type of coil, the distance it needs to travel, and the environmental conditions it will be exposed to. A balanced approach ensures both protection and cost-efficiency.
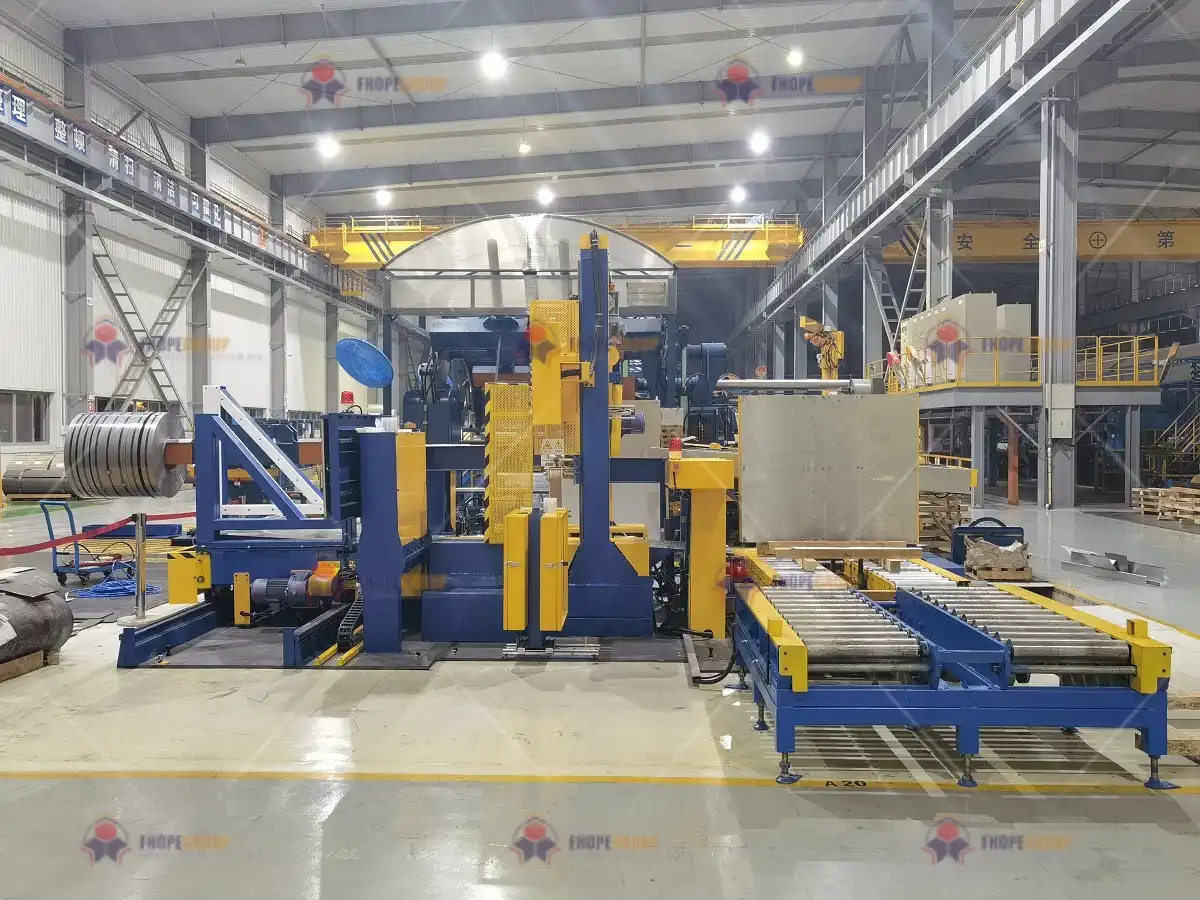
Type of Steel Coil and Handling Requirements
The first consideration should be the type of steel coil. Color-coated steel coils require extra care to avoid surface damage, which means protective wraps or films are essential. Additionally, the type of handling required for the coils, such as the need for lifting or rotating, can influence the packing method. Coils that need to be transported over long distances might need extra layers of protection.
Each coil type also has different characteristics that must be addressed, such as weight, size, and finish. By understanding these features, businesses can choose packing materials and techniques that offer the most protection without excessive costs.
Environmental Considerations
Environmental factors such as humidity, temperature, and exposure to chemicals are essential when selecting the packing solution. For instance, in areas with high humidity, extra moisture-resistant layers may be necessary to prevent corrosion. If the steel is to be exposed to harsh chemicals during transport, additional protective coatings may be needed.
Factor | Consideration | Solution |
---|---|---|
Coil Type | Surface protection needed | Protective films, stretch wrap |
Handling Method | Lift, rotate, or transport? | Custom cradles, automated systems |
Environmental Risk | Exposure to moisture, chemicals | Moisture-resistant packaging |
Cost vs. Protection
Lastly, the cost is a crucial factor. While more advanced systems like automated packing machines may be more expensive, they offer increased efficiency and consistency. On the other hand, simple methods like stretch wrapping might be more affordable but could require more manual labor. Companies need to evaluate the trade-off between protection, efficiency, and cost to find the best solution for their needs.
Conclusion
Choosing the best packing solution for color-coated steel coils involves balancing cost, protection, and efficiency. By considering automation, the right materials, and environmental factors, businesses can ensure their coils are well-protected and transported safely.