How to Avoid Common Damages and Defects in Steel Coil Packaging
- How to Avoid Common Damages and Defects in Steel Coil Packaging
- 1. The Importance of Proper Steel Coil Packaging
- 2. Common Packaging Defects and Their Causes
- 3. Key Industry Standards for Steel Coil Packaging
- 4. Selecting the Right Packaging Materials
- 5. Best Practices for Handling and Moving Steel Coils
- 6. How to Prevent Corrosion and Moisture Damage
- 7. Proper Stacking and Storage Techniques
- 8. Automating Steel Coil Packaging for Consistency
- 9. Regular Quality Control Inspections
- 10. Future Trends in Steel Coil Packaging
- Conclusion: Protecting Your Steel Coils with Best Practices
Steel coil packaging is an essential part of the manufacturing and logistics process, especially given the widespread use of steel coils in construction, automotive, and industrial applications. Properly packaging steel coils ensures that the product remains intact and free from damage during transportation and storage. However, due to the weight, size, and specific characteristics of steel coils, packaging mistakes can lead to significant damages and defects that affect both product quality and operational efficiency.
In this article, we will explore how to avoid the most common damages and defects in steel coil packaging. We’ll delve into industry standards, best practices, materials used, and practical solutions, supported by real-world examples and case studies. Additionally, we’ll provide insights into future trends in steel coil packaging and how these trends are likely to shape the industry.
1. The Importance of Proper Steel Coil Packaging
Steel coils are highly sensitive to physical damage, moisture, and environmental exposure. Packaging plays a crucial role in maintaining their integrity, ensuring the quality of the end product, and minimizing losses throughout the supply chain. Steel coils are commonly prone to:
- Surface scratches
- Corrosion and rust
- Deformation and bending
- Edge damage
Each type of damage can affect the usability and lifespan of the steel coils, which ultimately impacts the operational efficiency and bottom line of businesses that handle these materials.
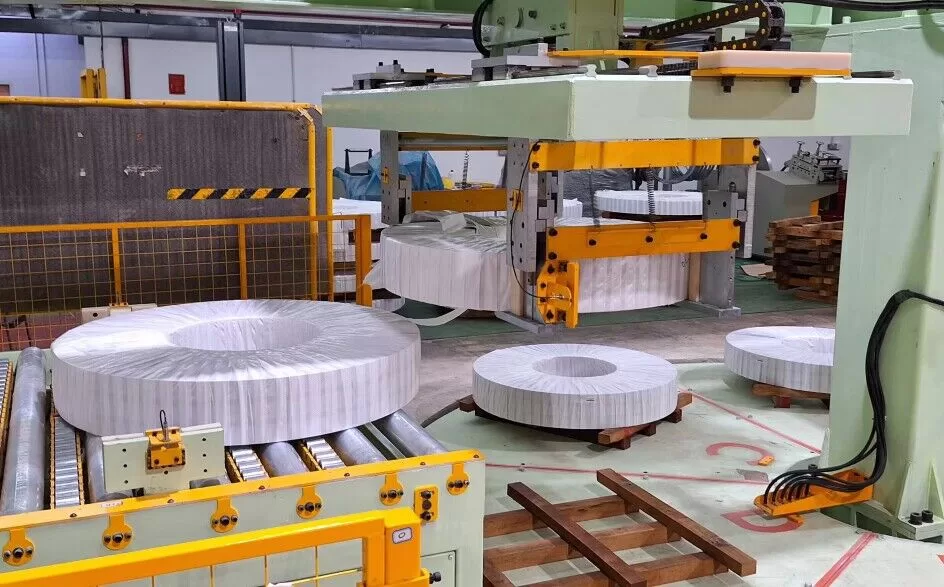
2. Common Packaging Defects and Their Causes
Before discussing solutions, let’s first understand the most common types of packaging defects. Identifying the root causes of these defects helps in selecting the best practices to avoid them:
- Improper tensioning of straps can cause coils to shift during transport, leading to deformation or dents.
- Inadequate moisture protection allows rust or corrosion to form on the surface of the coils.
- Incorrect stacking or overloading pallets can result in uneven pressure, damaging the bottom coils.
- Insufficient edge protection may cause dents and cracks during handling, especially when coils are moved by forklifts or cranes.
3. Key Industry Standards for Steel Coil Packaging
Adhering to recognized industry standards ensures that steel coils are packaged in a way that minimizes risks and optimizes protection. Some of the relevant industry standards include:
- ISO 22493: Guidelines for the protection of steel products during shipping and handling.
- ASTM A700: Practices for packaging, marking, and loading steel products for shipment.
- ISO 9001: Quality management systems that help ensure consistency and improvement in product packaging processes.
By complying with these standards, companies can enhance the safety and efficiency of their packaging operations.
4. Selecting the Right Packaging Materials

One of the first steps in avoiding damage during steel coil packaging is choosing the appropriate materials. Here are some critical materials that provide protection from various forms of damage:
- VCI (Volatile Corrosion Inhibitor) Paper: Commonly used to prevent corrosion, VCI paper releases corrosion-inhibiting vapors that protect the metal surface during storage and transportation.
- PE Stretch Film: Stretch film provides protection against physical impact and ensures that coils are tightly secured. It’s highly recommended for protecting against abrasions and scratches.
- Edge Protectors: Installing plastic or metal edge protectors helps distribute pressure evenly, preventing damage during handling.
- Desiccants: Using desiccants inside the packaging prevents moisture buildup, keeping the steel coils dry and preventing rust.
Diagram Suggestion: A cross-section diagram showing the multiple layers of protection for a steel coil, including edge protectors, stretch film, and VCI paper.
5. Best Practices for Handling and Moving Steel Coils
Handling steel coils improperly during packaging or transport can easily result in surface damage or even accidents. To mitigate this, companies should focus on:
- Using Proper Lifting Equipment: Cranes and forklifts equipped with C-hooks or coil lifters should be used for safe lifting. Ensure the equipment can handle the weight and size of the coil to avoid dropping.
- Avoiding Contact with the Ground: Always use protective barriers, such as pallets or racks, to prevent steel coils from coming into contact with rough surfaces that can cause scratches.
- Training for Workers: Provide training on safe coil handling techniques and proper use of equipment, as well as regular audits to ensure compliance.
Real-World Example: A manufacturer in Europe reduced damages by 20% after implementing mandatory training programs for forklift operators, ensuring they properly used edge protectors and lifting tools.
6. How to Prevent Corrosion and Moisture Damage
Corrosion is one of the most common problems encountered in steel coil packaging, especially in environments with high humidity or during long-distance transportation. Here’s how to prevent it:
- Use VCI Paper and Film: These materials create a protective atmosphere inside the packaging that prevents the chemical reactions leading to rust.
- Seal Packages Tightly: Proper sealing with stretch film or shrink wrap ensures that no moisture can penetrate the packaging.
- Store in Dry Conditions: Ideally, steel coils should be stored in climate-controlled environments to minimize exposure to humidity.
Case Study: A steel manufacturer in Southeast Asia, where humidity levels are high, adopted VCI films and saw a 95% reduction in corrosion-related defects during the rainy season.
7. Proper Stacking and Storage Techniques
Steel coils are heavy and need to be stacked and stored carefully to prevent deformation. Here are best practices to follow:
- Use Custom-Made Racks: Custom racks ensure that the coils are evenly supported, reducing the risk of warping or flattening of the coil edges.
- Limit Stack Height: Exceeding recommended stack heights can lead to increased pressure on lower coils, causing deformation. Follow ISO or ASTM guidelines for maximum stack height limits.
- Place Protective Layers Between Coils: Use protective barriers, such as wooden pallets or rubber mats, to prevent coils from rubbing against one another.
8. Automating Steel Coil Packaging for Consistency
Manual packaging often results in inconsistencies that can lead to defects. Automation is one of the most effective ways to ensure consistent, high-quality packaging. Automated coil packign systems can:
- Ensure Precise Tensioning: Automated strapping machines apply the exact amount of force needed to secure the coil without causing damage.
- Reduce Human Error: Automated wrapping and handling systems minimize the risk of worker mistakes, which can lead to mishandling and damage.
Future Trend: The growing use of Industry 4.0 technologies allows for integrated packaging systems that monitor packaging quality in real time. These systems can detect anomalies and adjust settings automatically to prevent potential damage.
9. Regular Quality Control Inspections
Even with the best materials and equipment, quality control is necessary to ensure the packaging is done correctly. Implementing regular inspections can prevent small issues from becoming significant problems.
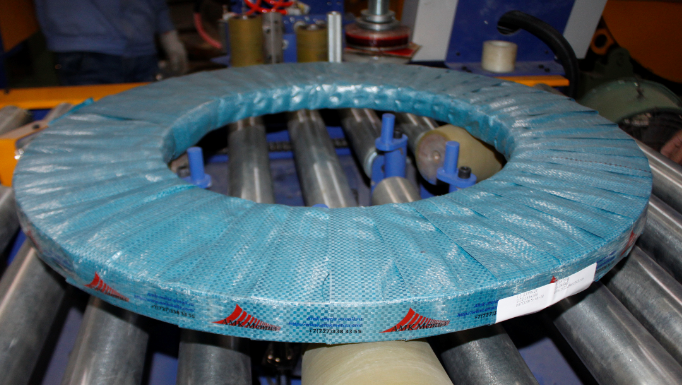
- Visual Inspections: Check each coil after packaging for any signs of surface damage or loose strapping.
- Moisture Detection: Use humidity sensors in packaging for long-distance transport to monitor the presence of moisture, which can lead to rust.
- Sample Testing: Periodically unpack random coils to verify that the packaging process is consistent and effective.
10. Future Trends in Steel Coil Packaging
As the steel coil industry continues to evolve, several trends are emerging that are set to shape the future of packaging:
- Sustainability in Packaging Materials: The move toward eco-friendly materials such as biodegradable films is gaining momentum, driven by environmental regulations and consumer demand.
- Smart Packaging Solutions: The integration of IoT sensors that can monitor packaging conditions in real time is becoming more prevalent. These sensors can track humidity, temperature, and even vibrations, helping to prevent damages before they occur.
- Advanced Automation: AI-driven systems are set to take over the more intricate aspects of packaging, allowing for faster, safer, and more precise operations.
Conclusion: Protecting Your Steel Coils with Best Practices
Avoiding common damages and defects in steel coil packaging requires a multifaceted approach that includes selecting the right materials, following industry standards, and implementing best practices for handling, storage, and transportation. By automating parts of the process and incorporating smart technologies, companies can achieve greater consistency and reduce the risk of damage.
Investing in proper training, high-quality materials, and automated solutions not only protects the product but also enhances operational efficiency and reduces costs. As the industry evolves, businesses that stay ahead of the curve in adopting innovative packaging solutions will be better positioned to deliver high-quality, damage-free products to their customers.