
In the demanding landscape of industrial manufacturing, optimizing operational efficiency and managing costs are paramount. As industries worldwide contend with escalating labor expenses and the continuous need for process streamlining, many are adopting automated solutions, particularly in packaging operations. Among these innovations, automated steel coil packing lines emerge as pivotal advancements. These systems offer manufacturers a robust strategy to significantly curtail operational expenditures while reducing dependence on manual labor. This article delves into how these automated systems achieve cost savings, enhance productivity, and address labor challenges in the metals industry.
We will explore the core benefits of implementing steel coil packing lines, examine their key features contributing to efficiency, and discuss their suitability across various industrial applications. Understanding these aspects reveals why automation in coil packaging is not merely a trend but a strategic imperative for sustainable growth and competitiveness.
Recent advancements highlight that automated coil packing technology not only cuts costs but also substantially improves packaging quality and consistency. This uniformity minimizes the risk of product damage during handling and transit, leading to fewer returns and enhanced customer satisfaction. Companies integrating these systems consistently report marked reductions in operational expenses and notable gains in productivity metrics.
By replacing physically demanding and repetitive manual tasks with sophisticated machinery, businesses can meet high production targets more effectively. Automation minimizes human error, reduces workplace injury risks, and allows for better allocation of human resources to value-added activities, benefiting the entire organization.
1. Why Are Automated Steel Coil Packing Lines Crucial for Cost Reduction?
1.1. Navigating Industrial Cost Pressures with Automation
In today's competitive industrial environment, intense cost pressures necessitate innovative solutions for expense reduction. Automated steel coil packing lines directly address this need by optimizing operations, significantly reducing manual labor hours, and minimizing the consumption of packaging materials like stretch film and strapping. The automation of the packing process yields savings not only in direct labor but also in associated overhead costs (e.g., training, benefits, injury compensation), making these systems a strategically sound long-term investment.
The financial impact becomes evident when analyzing operational efficiency. Automated systems operate continuously with minimal supervision, freeing up personnel for more complex or strategic roles rather than repetitive packing tasks. This reallocation enhances shop floor efficiency and boosts overall workforce productivity, contributing directly to the bottom line.
1.2. Achieving Cost Savings Through Packaging Standardization
A primary cost-saving mechanism of automated coil packing lines is the standardization of the packaging process. Manual packaging inherently introduces variability; different workers may apply inconsistent tension or use varying amounts of material, potentially leading to inadequate protection, product damage during transit, or material wastage. Automated lines, conversely, apply wrapping film or strapping with precise, repeatable consistency for every coil. This precision minimizes packaging errors, reduces material consumption, and lowers costs associated with inconsistencies and potential product damage claims.
Furthermore, standardized packaging aids in meeting regulatory requirements and customer specifications, particularly for international shipments. Consistent, high-quality packaging improves product safety, ensures compliance, and reduces the likelihood of costly rejections or returns. Ultimately, standardization leads to a more predictable and controllable cost structure, essential for accurate budgeting and financial planning.
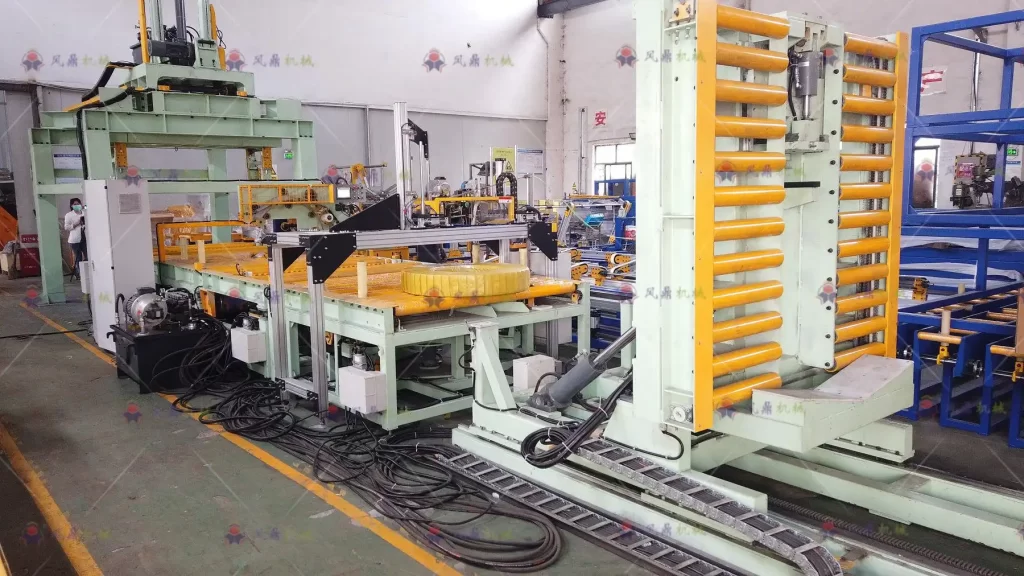
1.3. Maximizing Resource Utilization and Minimizing Waste
The resource efficiency delivered by automated coil packing lines extends beyond direct cost savings. These systems are precisely programmed to use the optimal amount of wrapping film or strapping for secure packaging, effectively eliminating material overuse and waste common in manual processes. This operational efficiency benefits the company's budget and aligns with growing corporate sustainability goals. As businesses face increasing pressure to adopt environmentally responsible practices, reducing packaging waste through automation offers a tangible contribution to greener operations.
2. How Do Steel Coil Packing Lines Minimize Labor Dependency?
2.1. Transitioning from Manual Effort to Automated Efficiency
Traditionally, packaging heavy steel coils involved significant manual labor—a process often characterized by inefficiency and potential safety hazards. Implementing automated coil packing lines fundamentally shifts this dynamic, drastically reducing the need for direct human involvement. Equipped with advanced sensors, intelligent controls, and robotic handling mechanisms, these systems manage the entire packaging sequence with minimal operator oversight. This automation directly translates to reduced staffing requirements for packaging tasks on the production floor.
This transition allows for strategic reallocation of human resources. Instead of performing repetitive, physically demanding packing tasks, employees can be trained for and assigned to higher-value roles involving machine supervision, quality control, maintenance, or process improvement. This not only optimizes labor utilization but can also lead to improved job satisfaction and skill development within the workforce.
2.2. Enhancing Workplace Safety and Reducing Physical Strain
Manual handling of steel coils poses significant ergonomic risks. The weight and bulkiness of coils often require multiple workers for safe maneuvering and packaging, increasing the potential for musculoskeletal injuries from lifting, pushing, and repetitive motions. Automated coil packing lines eliminate these hazardous manual tasks by mechanizing the process. This automation dramatically lowers the incidence of workplace injuries related to heavy lifting and repetitive strain. Furthermore, these systems incorporate safety features like light curtains, safety interlocks, emergency stops, and controlled movements to protect personnel during operation and maintenance.
The reduction in workplace injuries yields substantial financial benefits beyond employee well-being. Fewer incidents mean lower workers' compensation claims, reduced lost workdays and absenteeism, and potentially lower insurance premiums—representing significant indirect cost savings attributable to automation.

2.3. Addressing Labor Shortages in Manufacturing
The manufacturing sector, particularly heavy industries, often faces challenges in recruiting and retaining skilled labor. In regions experiencing labor shortages, automated coil packing lines provide a critical solution. Automation enables facilities to maintain or even increase production throughput with a reduced workforce size. This capability becomes invaluable when finding and keeping qualified workers is difficult. By implementing automated systems, businesses can ensure operational continuity and meet market demands reliably, even when faced with a constrained labor pool.
3. What Key Features Drive Cost Savings in Coil Packing Lines?
3.1. Advanced Control Systems for Precision and Material Optimization
Modern steel coil packing lines feature sophisticated control systems, typically utilizing Programmable Logic Controllers (PLCs) and Human-Machine Interfaces (HMIs). These systems allow for precise, programmable control over parameters such as wrapping speed, film tension, overlap percentage, and strapping placement. This ensures each coil is packaged according to exact specifications consistently, minimizing material waste and ensuring optimal load containment without human variability. Precise control optimizes the use of consumables, directly lowering the cost per packaged coil.
Advanced controls also enable rapid and easy changeovers between different coil sizes or packaging recipes. This operational flexibility minimizes machine downtime when switching production runs, thereby maximizing equipment utilization and overall production throughput, further contributing to cost-efficiency.
3.2. Energy-Efficient Design for Reduced Utility Expenses
Energy consumption is a significant operational cost in manufacturing. Leading coil packing lines are designed with energy efficiency in mind. Features such as high-efficiency motors, Variable Frequency Drives (VFDs) that adjust motor speed based on load, and intelligent power-saving modes during idle periods help minimize electricity consumption. Over the operational lifespan of the equipment, these energy savings accumulate, leading to noticeably lower utility bills and a reduced carbon footprint.
Investing in energy-efficient machinery not only reduces direct costs but also helps companies meet environmental regulations and corporate sustainability targets. This enhances the company's public image and aligns operations with global trends towards greener manufacturing practices.

3.3. Integrated Diagnostics for Proactive Maintenance
Unplanned downtime due to equipment failure can be extremely costly. Many modern coil packing lines incorporate integrated diagnostic systems and condition monitoring sensors. These tools track machine performance, monitor critical components (like motors, bearings, and actuators) in real-time, and provide alerts for potential issues before they escalate into breakdowns. This capability enables predictive maintenance strategies, allowing maintenance teams to schedule repairs proactively during planned downtime.
Predictive maintenance significantly enhances machine reliability and uptime, preventing costly production interruptions. It also helps extend the overall lifespan of the equipment by addressing wear and tear proactively, reducing the need for major repairs or premature replacement, thus preserving the capital investment and lowering long-term operational costs.
4. Are Coil Packing Lines Suitable for Diverse Industrial Applications?
4.1. Versatility in Handling Different Coil Materials and Dimensions
A key strength of automated coil packing lines is their inherent adaptability. These systems are engineered to effectively handle a wide spectrum of coil materials, including steel (carbon, stainless, galvanized), aluminum, copper, brass, wire, cable, and other specialty alloys. Recognizing that different materials have unique surface properties and handling requirements, these lines offer adjustable settings for parameters like wrapping tension, rotational speed, and protective layer application. This ensures secure and damage-free packaging regardless of the coil's composition.
This versatility extends to physical dimensions. Coil packing lines can typically accommodate a broad range of coil diameters, widths, and weights. Adjustable conveyors, centering devices, and wrapping/strapping heads allow the system to process both narrow slit coils and large master coils efficiently. This flexibility makes automated lines ideal for service centers, mills, and manufacturers dealing with diverse product portfolios, streamlining their packaging operations onto a single, adaptable system.
4.2. Customizable Features for Enhanced Product Protection
For industries where coils face long transit times, harsh environmental conditions, or specific handling protocols, superior product protection is non-negotiable. Automated coil packing lines can be configured with specialized features beyond standard wrapping. Options may include:
- Application of VCI (Volatile Corrosion Inhibitor) film or paper to prevent rust.
- Integration of edge protectors (corner boards) to guard against physical damage.
- Use of specific wrapping materials like HDPE or woven fabric for weather resistance.
- Multi-layer wrapping capabilities for added durability.
- Circumferential and/or through-eye strapping for maximum load stability.
These enhanced protection features are particularly valuable in sectors like automotive manufacturing, construction materials supply, aerospace, and export-oriented industries. By tailoring the packaging process, automated lines minimize the risk of costly damage during shipping and storage, ensuring product quality upon arrival and enhancing overall customer satisfaction.

4.3. Scalability to Accommodate Business Growth
Investment in capital equipment must consider future needs. Automated coil packing lines are often designed with scalability in mind. Many systems feature a modular construction, allowing businesses to start with a configuration matching their current throughput and add modules—such as automated coil loading/unloading, labeling systems, palletizing, or additional wrapping/strapping stations—as production volumes increase. This modularity provides a cost-effective path for expansion without requiring a complete system replacement.
This inherent scalability protects the initial investment and ensures the packaging operation can keep pace with business growth. It allows companies to remain agile, efficiently managing fluctuating production demands and maintaining consistent packaging quality and throughput as they expand their market reach or product offerings.
Conclusion: Strategic Investment for Cost-Efficiency and Operational Excellence
Implementing automated steel coil packing lines represents a significant strategic advantage for manufacturers aiming to reduce operating costs and optimize labor utilization. By automating this critical final stage of production, companies unlock substantial benefits ranging from direct cost savings on labor and materials to enhanced workplace safety, improved packaging quality, and greater operational consistency. These systems deliver far more than just automation; they foster a more streamlined, reliable, and efficient manufacturing environment poised for long-term success.
With their adaptability to various materials and sizes, energy-efficient designs, and advanced features like predictive maintenance, automated coil packing lines offer enduring value across diverse industrial sectors. As pressures from labor costs, efficiency demands, and safety requirements continue to shape the industry, investing in this technology provides a robust solution that delivers both immediate returns and future-proof scalability, aligning perfectly with core financial and operational objectives.

Get Your Best Solution !