How Packaging Machines Effectively Handle Aluminum Products
FHOPE is a well-known company specializing in producing and selling packaging/handling machines for top-notch aluminum sheets, strips, foils, and related, aluminum alloys. Our expertise encompasses a wide range of aluminum packaging methods, ensuring the safe transport of your goods.
We excel at utilizing customized packaging strategies tailored to diverse product attributes and varying shipping distances. Customer satisfaction is our top priority at FHOPE, and we are dedicated to meeting specific packaging needs and preferences with precision and care.
Aluminum sheets packaging
Aluminum sheets are primarily packaged methods: bottom locking, standard box, plywood, and corner protection styles. These packaging techniques can be mechanized for efficiency.
Packaging Methods:
When employing bottom locking, standard box, plywood, or corner protection styles for aluminum sheets, begin by laying a plastic film at the box’s bottom. Add a layer of neutral or weakly acidic moisture-resistant paper or similar material.
Follow these loading methods:
- Apply oil and interleave sheets with paper before packing.
- Apply oil and pack sheets without interleaving paper.
- Pack sheets without oil but with paper or foam plastic sheets in between.
- Pack sheets without oil or interleaving paper.
- Pack sheets after applying a surface film.
Automated Packaging:
This packaging process can largely be automated using customized equipment such as automatic paper placement, sheet handling, oil spraying, top layer application, and steel strapping.
Simple Packaging:
For straightforward packaging, wrap the sheets with neutral or weakly acidic moisture-resistant paper, add a layer of plastic film, seal, place on a cushion, and secure with steel straps.
Budget-Friendly Options:
For cost-effective solutions, direct placement on the cushion with steel strapping is recommended. Additionally, we provide automatic/semi-automatic steel strapping machines for customer use.
Aluminum strips
Vertical strips packaging:
When packing aluminum strips for vertical storage and transport, an automatic adding paper/film machine can efficiently apply protective wrapping. This packaging line integration improves productivity over manual methods.
First, the strips are fed vertically into the automatic machine. It then wraps each roll with a neutral moisture-resistant paper using precision dispensing and wrapping motions. The machine applies a plastic film overlay in a continuous motion. A built-in compartment pre-loads desiccant that is automatically deposited into strip cores during the wrapping process.
The wrapped rolls exit the machine ready for efficient box loading. Multiple rolls can now be quickly placed and aligned in vertical packaging boxes on a concurrent conveyor line in an organized fashion. A lid attachment on the automated system covers and tapes the box shut, completing an integrated packaging and sealing operation with minimal human involvement.
Horizontal strips packaging:
For this method, an automatic wrapping machine precisely covers each aluminum strip roll in neutral paper followed by plastic film. It places desiccant inside cores during this process.
The rolls then discharge to an automatic strapping system. With an integrated crisscross pallet bed and adjustable steel straps, it efficiently secures:
- Individual wrapped rolls onto the pallet mesh
- Multiple rolls connected together prior to placement
- For additional protection, the wrapping machine can apply an outer hardboard layer over the film-wrapped rolls before strapping.
Automating these packaging steps improves throughput versus manual work. Rolls receive consistent, high-quality multilayer wraps with optimized moisture barriers.
Plus, fully automated packaging lines ensure efficient handling between processes. Rolds transition seamlessly between wrapping, connection, and securing stations.
Adopting such integrated machinery streamlines aluminum strip packaging per the crisscross pallet method. It sustains protection during shipping while reducing labor needs for premium service exporters like FHOPE.

Aluminum foil packaging
When packing aluminum foil rolls or coils horizontally, protective materials are applied. An automatic adding machine wraps each item in neutral moisture-resistant paper followed by a plastic bag. It integrates a cushion and deposits desiccant inside.
The bag ends are then heat-sealed. An automated turner flips the wrapped roll onto its horizontal position if needed.
Conveyors transfer items to racking stations where they are placed into boxes either manually or through automatic pack-out arms. Robotic arms precisely position rolls side-by-side or in layers as boxes fill.
Once loaded, box lids are automatically attached before tape sealing by integrated machines. Filled cartons next proceed to automatic strapping equipment. Adjustable straps are applied to reinforce outer packaging.
Whether foil rolls are stored horizontally or coils vertically, Fhope can customize appropriate packaging lines. Automated processes ensure consistency and maximize throughput compared to manual methods. Integrated machinery protects aluminum products for varied applications and shipping needs.
Aluminum profile packaging
When it comes to aluminum profiles packaging. With a commitment to excellence and efficiency, FHOPE Machinery offers a comprehensive array of automated systems designed to streamline the packaging process for aluminum profiles.
At the heart of FHOPE Machinery’s offerings is the automatic feeding system, which orchestrates the seamless introduction of individual aluminum profiles into the packaging line. This precise and efficient process ensures a steady flow of profiles, optimizing production speed and consistency.
Once the profiles are in the packaging line, FHOPE Machinery’s automated transfer mechanisms come into play. These systems swiftly and accurately transport the profiles to the wrapping station, where they undergo stretch wrapping or film tapping.
This automated transfer process not only saves time but also enhances the overall packaging quality by ensuring uniform and secure wrapping of each profile.
After the wrapping process is complete, automation handling extends to the unloading and alignment stage. The automatic unloading system gently guides the profiles off the line and aligns them with precision, readying them for stacking.
This meticulous alignment is crucial for maintaining order and organization in the stacking phase, ultimately leading to more efficient storage and transportation of the packaged profiles.
Whether bundling several profiles together for secure packaging or bagging profiles for added protection, FHOPE Machinery’s systems are equipped to handle diverse packaging requirements with ease and efficiency.
FHOPE tailors fully integrated packaging lines from profile infeed to load outfeed. Custom solutions optimize protection and throughput for all aluminum packaging applications.
Automated processes sustainably meet client needs worldwide through customizable turnkey solutions. High-speed wrapping, stacking, bundling and strapping integration streamlines previous manual handling with consistent, high-quality results.
Building profile packaging
FHOPE uses automated pallet wrapping systems to efficiently bundle large quantities of building profiles for transportation and storage.
Horizontal wrapping machines encompass bundles on six sides with precision multi-axis film application. Programmable wrapping profiles ensure comprehensive coverage for maximum moisture protection. Integrated robotic arms nest components into organized pallet-sized configurations. Stackers then layer bundles onto pallets in synchronized sequence under robotic control.
Loaded pallets transfer to automatic 2/3/4/6-way strapping machines.
Adjustable tension strapping securely and efficiently fastens bundles.
Surrounding film reinforcement enhances strap durability.
Customizable solutions from profile infeed to load outfeed meet all containment needs. FHOPE sustainably serves aluminum fabricators through customized, efficient profile packaging worldwide.
Aluminum wire packaging
luminum wire coils machine are typically either coated with oil or left untreated before being wrapped with paper or burlap for protection. Consequently, wire coils can opt for core wrapping with film or additional wrapping with woven straps. This packaging method allows for standalone usage or integration with conveyor lines, which are equipped with automatic centering and sensing capabilities.
To meet space requirements and facilitate transportation, aluminum wire coils often need compression equipment. FHOPE’s compression machines assist customers in achieving comprehensive packaging integration by offering a comprehensive range of functions:
· Compression:
These machines excel at compressing aluminum wire coils, effectively reducing their overall size. By compacting the coils, they optimize storage and transportation space, making logistics more efficient and cost-effective.
· Bundling:
Equipped with bundling capabilities, FHOPE’s machines securely package the compressed wire coils. This bundling ensures that the coils are kept intact and organized throughout handling and transit, minimizing the risk of damage or disarray.
· Core Wrapping:
FHOPE’s compression machines also support core wrapping of wire coils. By providing an additional layer of protection and stability, core wrapping enhances the durability of the coils, safeguarding them against potential damage during transportation and storage.
· Pallet Wrapping:
With the ability to pallet wrap, these machines facilitate the efficient and secure packaging of multiple wire coils on pallets. This feature streamlines the loading and unloading process, preparing the coils for shipment in a structured and secure manner.
· Turning Over:
Designed for functionality, the machines are capable of turning over packaged wire coils. This feature allows for easy access during unloading or further processing, enhancing operational flexibility and convenience.
· Unloading:
FHOPE’s compression machines incorporate mechanisms for automated unloading of packaged wire coils. By automating the unloading process, they optimize handling efficiency, reduce manual labor requirements, and enhance overall productivity.
· Separating from the Stand:
Equipped with the capability to separate packaged wire coils from their stands or supports, these machines prepare the coils for distribution or storage. This function ensures that the coils are ready for the next stage of the supply chain, promoting seamless logistics operations.
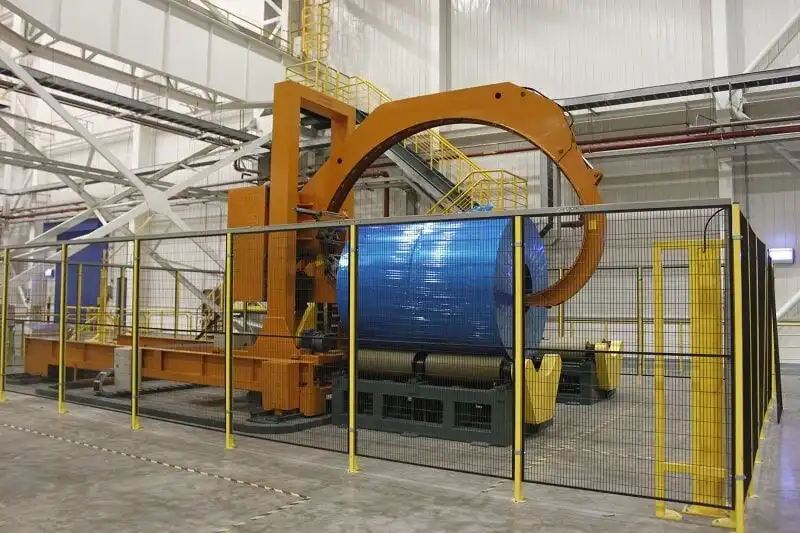
Our machine’s commitment to innovation and customer-centric solutions ensures that aluminum wire coil packaging is not only efficient but also tailored to meet the unique requirements of each client. By combining advanced technology with practical packaging solutions, FHOPE continues to be a trusted partner in the industry, providing comprehensive and reliable packaging solutions for aluminum wire coils.