How Intelligent Controls Can Improve Efficiency in Steel Coil Packing Lines
- How Intelligent Controls Can Improve Efficiency in Steel Coil Packing Lines
- 1. Understanding Intelligent Controls in Steel Coil Packing Lines
- 2. The Role of Automation in Enhancing Packing Line Efficiency
- 3. Leveraging Data Analytics for Process Optimization
- 4. Integrating Machine Learning for Intelligent Decision-Making
- 5. Enhancing Quality Control with Intelligent Sensors
- 6. Compliance with Industry Standards and Best Practices
- 7. Practical Applications and Solutions in Steel Coil Packing
- 8. Future Trends: The Evolution of Intelligent Controls in Steel Coil Packing
- 9. Cost-Benefit Analysis: Investing in Intelligent Controls
- 10. Best Practices for Implementing Intelligent Controls
- Conclusion
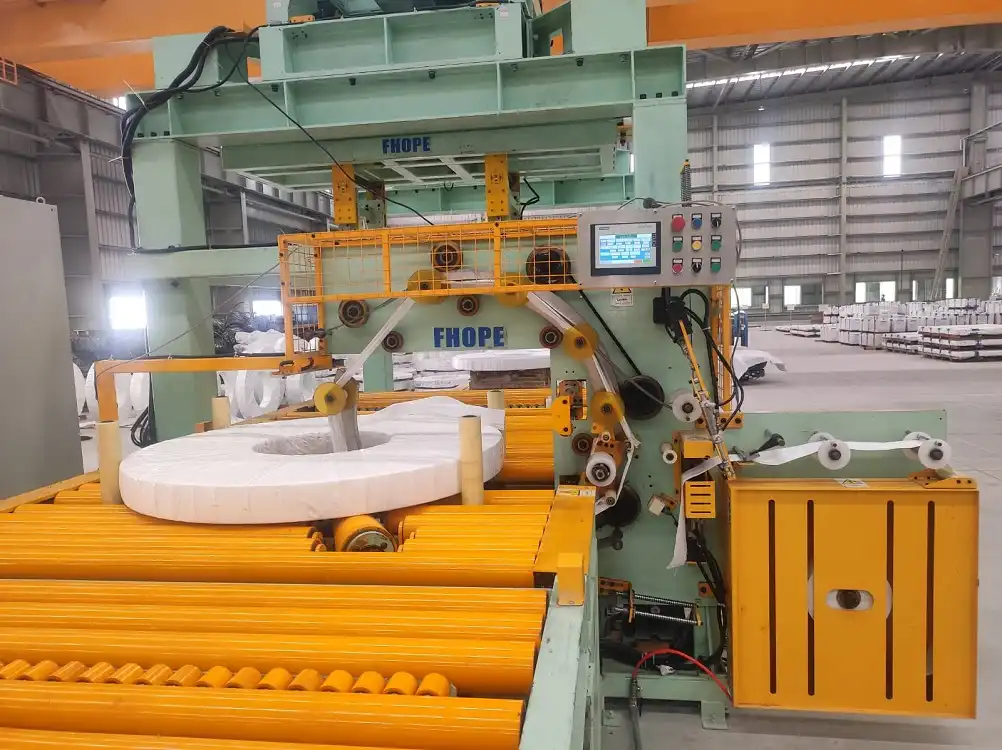
In the dynamic landscape of steel manufacturing, efficiency and precision are paramount. Steel coil packing lines play a crucial role in ensuring that finished products are securely packaged for transportation and storage. As industries strive to optimize their operations, the integration of intelligent controls has emerged as a game-changer. These advanced systems leverage automation, data analytics, and smart technologies to enhance the performance of steel coil packing lines, leading to significant improvements in efficiency, cost savings, and product quality.
This article delves into how intelligent controls can revolutionize steel coil packing lines. We will explore the key components, benefits, industry standards, real-world applications, and future trends that make intelligent controls indispensable in modern steel manufacturing.
1. Understanding Intelligent Controls in Steel Coil Packing Lines
Intelligent controls refer to advanced systems that utilize automation, sensors, data analytics, and machine learning to manage and optimize industrial processes. In the context of steel coil packing lines, intelligent controls oversee every aspect of the packing process, from coil handling and wrapping to strapping and quality inspection.
Key Components of Intelligent Controls:
- Programmable Logic Controllers (PLCs): Serve as the brain of the packing line, coordinating the operation of various machines and sensors.
- Sensors and Actuators: Monitor parameters such as coil dimensions, tension levels, and wrapping material usage, and execute actions based on real-time data.
- Human-Machine Interface (HMI): Provides operators with a user-friendly interface to monitor and control the packing line.
- Data Analytics Platforms: Analyze collected data to identify patterns, predict maintenance needs, and optimize packing processes.
By integrating these components, intelligent controls create a smart packing line that adapts to varying production demands, minimizes errors, and maximizes efficiency.
2. The Role of Automation in Enhancing Packing Line Efficiency
Automation is at the core of intelligent controls, transforming traditional manual packing lines into highly efficient, automated systems. Automation in steel coil packing lines involves the use of automated machinery to handle tasks such as wrapping, strapping, and conveying coils.
How Automation Improves Efficiency:
- Speed and Throughput: Automated systems can operate at higher speeds than manual processes, significantly increasing the number of coils packed per hour.
- Consistency and Precision: Automation ensures that each coil is wrapped and strapped with uniform tension and placement, reducing variability and enhancing product quality.
- Reduced Labor Costs: By minimizing the need for manual intervention, automation lowers labor costs and reallocates human resources to more strategic tasks.
Real-World Example: A steel manufacturer in Germany implemented an automated wrapping and strapping system, resulting in a 30% increase in packing throughput and a 20% reduction in labor costs within the first year of operation.
3. Leveraging Data Analytics for Process Optimization
Data analytics plays a pivotal role in intelligent controls by providing insights into the performance of steel coil packing lines. By collecting and analyzing data from various sensors and machines, manufacturers can identify inefficiencies, predict maintenance needs, and optimize packing parameters.
Benefits of Data Analytics:
- Predictive Maintenance: Analyzing data trends helps predict equipment failures before they occur, reducing unplanned downtime and extending machinery lifespan.
- Process Optimization: Data-driven insights allow for the fine-tuning of packing parameters such as wrapping tension and strapping pressure, ensuring optimal performance.
- Quality Control: Continuous monitoring and analysis help maintain high packing standards, reducing the likelihood of damaged coils during transport.
Case Study: A North American steel producer utilized data analytics to monitor wrapping tension in real-time. This led to a 15% decrease in material waste and a 10% improvement in packing consistency, enhancing overall operational efficiency.
4. Integrating Machine Learning for Intelligent Decision-Making
Machine learning (ML) enhances intelligent controls by enabling systems to learn from data and make informed decisions autonomously. In steel coil packing lines, ML algorithms can analyze vast amounts of data to optimize packing processes and predict potential issues.
Applications of Machine Learning:
- Adaptive Control Systems: ML algorithms adjust packing parameters in real-time based on coil size, weight, and material properties, ensuring optimal wrapping and strapping for each coil.
- Anomaly Detection: Machine learning models can identify abnormal patterns in data, signaling potential equipment malfunctions or deviations in packing quality.
- Demand Forecasting: By analyzing historical production data, ML can predict future packing needs, allowing for better resource allocation and inventory management.
Example: An Italian steel mill integrated machine learning into their packing line, enabling the system to adapt wrapping tension dynamically. This resulted in a 25% reduction in packing material usage and a 20% increase in packing speed.

Get Your Best Solution !
5. Enhancing Quality Control with Intelligent Sensors
Quality control is a critical aspect of steel coil packing, ensuring that each coil is securely wrapped and strapped to prevent damage during transportation. Intelligent sensors embedded in the packing line monitor various parameters to maintain high-quality standards.
Types of Sensors Used:
- Tension Sensors: Measure the tension applied during wrapping and strapping, ensuring that coils are neither over-wrapped nor under-wrapped.
- Dimension Sensors: Verify the size and weight of each coil, allowing the system to adjust packing parameters accordingly.
- Temperature and Humidity Sensors: Monitor environmental conditions that could affect the integrity of the packing materials.
Benefits:
- Real-Time Monitoring: Immediate detection of deviations ensures that corrective actions can be taken promptly, maintaining consistent packing quality.
- Automated Adjustments: Intelligent controls use sensor data to automatically adjust machine settings, eliminating the need for manual interventions and reducing the risk of human error.
Case Study: A Japanese steel manufacturer implemented intelligent sensors in their packing line, resulting in a 30% improvement in packing quality and a significant decrease in product damage during shipping.
6. Compliance with Industry Standards and Best Practices
Adhering to industry standards is essential for ensuring the safety, reliability, and quality of steel coil packing lines. Intelligent controls help manufacturers comply with various ISO and ASTM standards by providing precise control and comprehensive documentation.
Key Industry Standards:
- ISO 9001: Focuses on quality management systems, ensuring that packing lines consistently meet customer and regulatory requirements.
- ASTM D3951: Specifies standard practices for commercial packaging, ensuring that packed coils are prepared for safe transportation and handling.
- ISO 14001: Pertains to environmental management, encouraging practices that reduce environmental impact, such as minimizing material waste and energy consumption.
How Intelligent Controls Facilitate Compliance:
- Automated Documentation: Intelligent systems automatically log packing parameters and quality metrics, providing detailed records for compliance audits.
- Consistent Performance: Automation ensures that packing processes adhere to predefined standards, reducing variability and enhancing product reliability.
- Environmental Monitoring: Sensors track energy usage and material waste, helping manufacturers meet ISO 14001 requirements and promote sustainability.
Real-World Example: A European steel producer integrated intelligent controls to comply with ASTM D3951, resulting in zero packaging-related compliance issues and improved customer satisfaction.
7. Practical Applications and Solutions in Steel Coil Packing
Intelligent controls offer a wide range of practical applications and solutions that address common challenges in steel coil packing. From automated material handling to smart packaging algorithms, these technologies provide tangible benefits that enhance operational efficiency and product quality.
Key Applications:
- Automated Material Handling: Intelligent conveyor systems and robotic arms streamline the movement of coils through the packing line, reducing manual handling and increasing throughput.
- Smart Packaging Algorithms: Advanced algorithms optimize the use of packing materials, ensuring that each coil is wrapped and strapped efficiently while minimizing waste.
- Real-Time Feedback Systems: Continuous monitoring and feedback allow operators to make informed decisions and adjust packing processes on the fly, ensuring optimal performance at all times.
Solutions Offered:
- Customized Packing Programs: Intelligent controls can be programmed to handle different types of coils, adapting packing parameters based on specific requirements.
- Integrated Safety Features: Automated systems incorporate safety mechanisms such as emergency stop buttons and protective barriers, ensuring a safe working environment.
- Remote Monitoring and Control: Operators can monitor and control packing lines remotely, allowing for greater flexibility and responsiveness to changing production needs.
Case Study: A South Korean steel manufacturer implemented an intelligent control system that included automated material handling and smart packaging algorithms. This integration led to a 40% increase in packing efficiency and a 20% reduction in material costs, demonstrating the effectiveness of intelligent controls in solving real-world challenges.
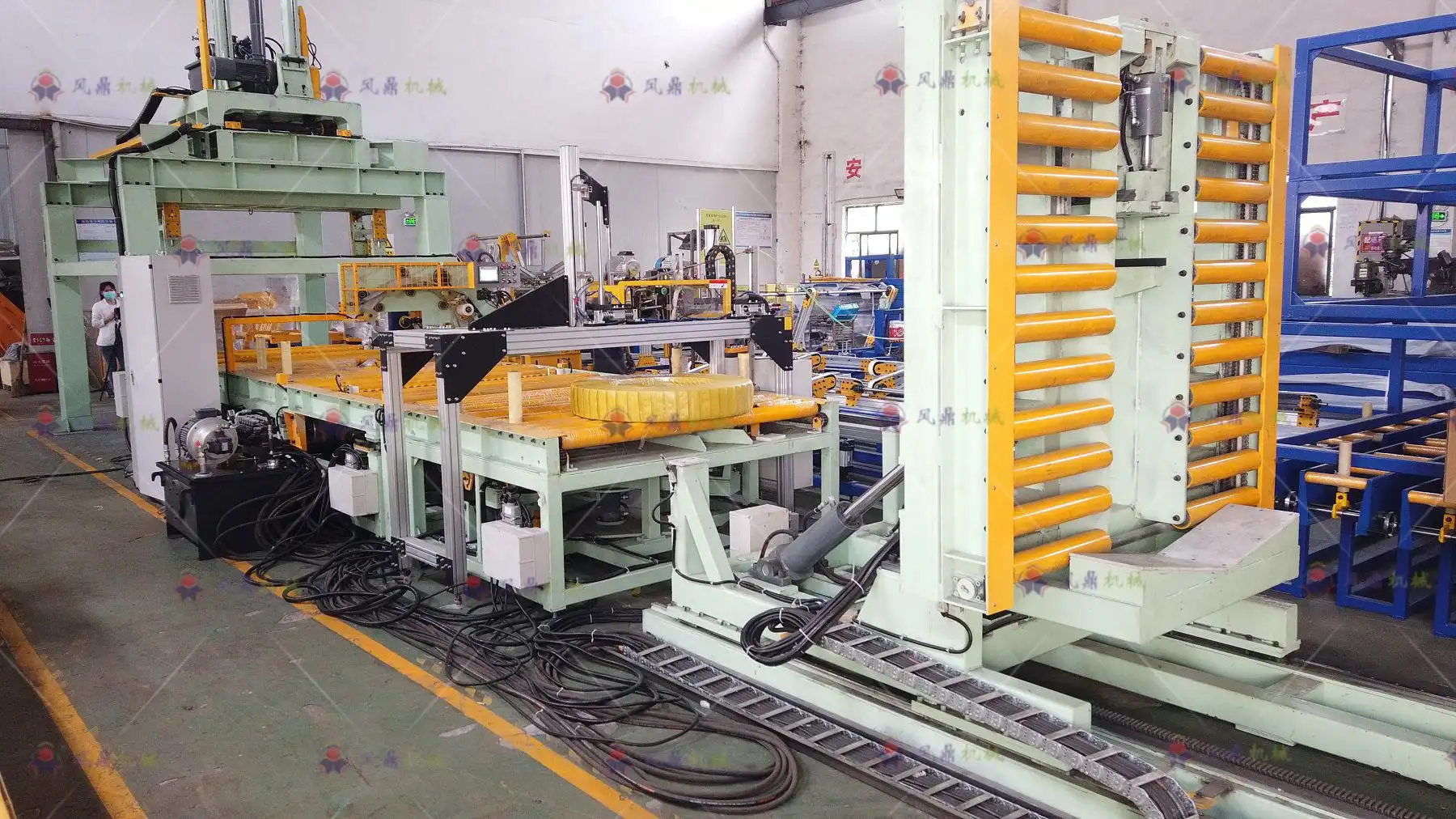
8. Future Trends: The Evolution of Intelligent Controls in Steel Coil Packing
As technology continues to advance, the role of intelligent controls in steel coil packing lines is set to evolve further. Emerging trends such as Artificial Intelligence (AI), Machine Learning (ML), and Blockchain are poised to enhance the capabilities of intelligent controls, driving even greater efficiency and innovation in the industry.
Emerging Trends:
- AI and Machine Learning Integration: AI-powered systems can analyze vast amounts of data to identify patterns and optimize packing processes in real-time, leading to continuous improvement and adaptability.
- Blockchain for Supply Chain Transparency: Blockchain technology can provide secure, immutable records of each coil's packing and handling history, enhancing traceability and accountability in the supply chain.
- Augmented Reality (AR) for Maintenance: AR can assist technicians in performing maintenance tasks by overlaying digital information onto physical equipment, improving accuracy and reducing downtime.
- Sustainable Packaging Solutions: Intelligent controls will increasingly focus on sustainable practices, such as optimizing material usage, reducing energy consumption, and integrating eco-friendly packaging materials.
Future Outlook: The integration of these advanced technologies will make intelligent controls even more powerful, enabling steel manufacturers to achieve unprecedented levels of efficiency, quality, and sustainability in their packing lines.
Illustration Suggestion: A futuristic diagram showing the integration of AI, blockchain, and AR within an intelligent steel coil packing line can help visualize how these technologies interconnect to drive efficiency and innovation.
9. Cost-Benefit Analysis: Investing in Intelligent Controls
Understanding the cost-benefit analysis of implementing intelligent controls is essential for manufacturers considering this investment. While the initial costs can be significant, the long-term benefits often justify the expenditure.
Initial Investment:
- Equipment Costs: Purchasing and installing intelligent control systems, including PLCs, sensors, and automated machinery.
- Training and Implementation: Training staff to operate and maintain the new systems, as well as integrating them into existing production lines.
- Software and Licensing: Costs associated with acquiring and maintaining the necessary software for data analytics and machine learning.
Long-Term Savings:
- Labor Cost Reduction: Lowering the number of operators needed and reallocating labor to more strategic tasks.
- Increased Throughput: Higher packing speeds and reduced downtime lead to increased production capacity.
- Material Efficiency: Optimized use of packing materials reduces waste and lowers material costs.
- Maintenance Savings: Predictive maintenance minimizes unplanned downtime and extends equipment lifespan, reducing maintenance expenses.
- Quality Improvements: Enhanced packing quality reduces product damage and associated costs, such as returns and rework.
ROI Calculation:
To calculate ROI, manufacturers can use the following formula:ROI=(Net Profit from Investment−Cost of InvestmentCost of Investment)×100\text{ROI} = \left( \frac{\text{Net Profit from Investment} - \text{Cost of Investment}}{\text{Cost of Investment}} \right) \times 100ROI=(Cost of InvestmentNet Profit from Investment−Cost of Investment)×100
By evaluating both the direct savings and indirect benefits such as improved quality and customer satisfaction, manufacturers can determine the financial viability of investing in intelligent controls.
Real-World Example: A steel manufacturer in the Middle East invested $500,000 in an intelligent control system for their packing line. Within two years, they realized savings of $700,000 through reduced labor costs, increased throughput, and lower material waste, resulting in a ROI of 40%.
10. Best Practices for Implementing Intelligent Controls
To maximize the benefits of intelligent controls in steel coil packing lines, manufacturers should adhere to best practices during implementation. These practices ensure a smooth transition, minimize disruptions, and enhance the overall effectiveness of the system.
Key Best Practices:
- Comprehensive Planning: Develop a detailed implementation plan that outlines objectives, timelines, and resource allocations. Involve key stakeholders to ensure alignment and buy-in.
- Pilot Testing: Before full-scale deployment, conduct pilot tests to identify potential issues and make necessary adjustments. This helps mitigate risks and ensures that the system operates as intended.
- Continuous Training: Provide ongoing training for operators and maintenance staff to keep them updated on the latest technologies and operational procedures.
- Regular Maintenance and Updates: Schedule regular maintenance checks and keep the system updated with the latest software and firmware to ensure optimal performance.
- Data-Driven Decision Making: Leverage the data collected by intelligent controls to make informed decisions about process improvements, resource allocation, and strategic planning.
Case Study: A steel mill in Australia followed these best practices when implementing an intelligent control system. By conducting pilot tests and providing continuous training, they achieved a seamless integration with their existing operations and realized maximum efficiency gains without significant downtime.
Conclusion
Implementing intelligent controls in steel coil packing lines represents a significant step forward in achieving operational excellence. By leveraging automation, data analytics, and smart technologies, manufacturers can dramatically improve efficiency, reduce costs, and enhance product quality. The integration of intelligent controls not only addresses immediate operational challenges but also positions steel manufacturers for future growth and innovation in the Industry 4.0 era.
From reducing labor dependency and minimizing downtime to optimizing material usage and ensuring compliance with industry standards, intelligent controls offer a comprehensive solution for modern steel coil packing needs. As technology continues to advance, the capabilities of intelligent controls will expand, providing even greater opportunities for efficiency and sustainability in steel manufacturing.
Investing in intelligent controls is not just about keeping up with technological trends—it’s about future-proofing your operations, ensuring that your packing lines are robust, adaptable, and capable of meeting the ever-evolving demands of the global steel market. By embracing these advanced systems, steel manufacturers can achieve a competitive edge, drive long-term profitability, and maintain high standards of quality and safety.

Get Your Best Solution !