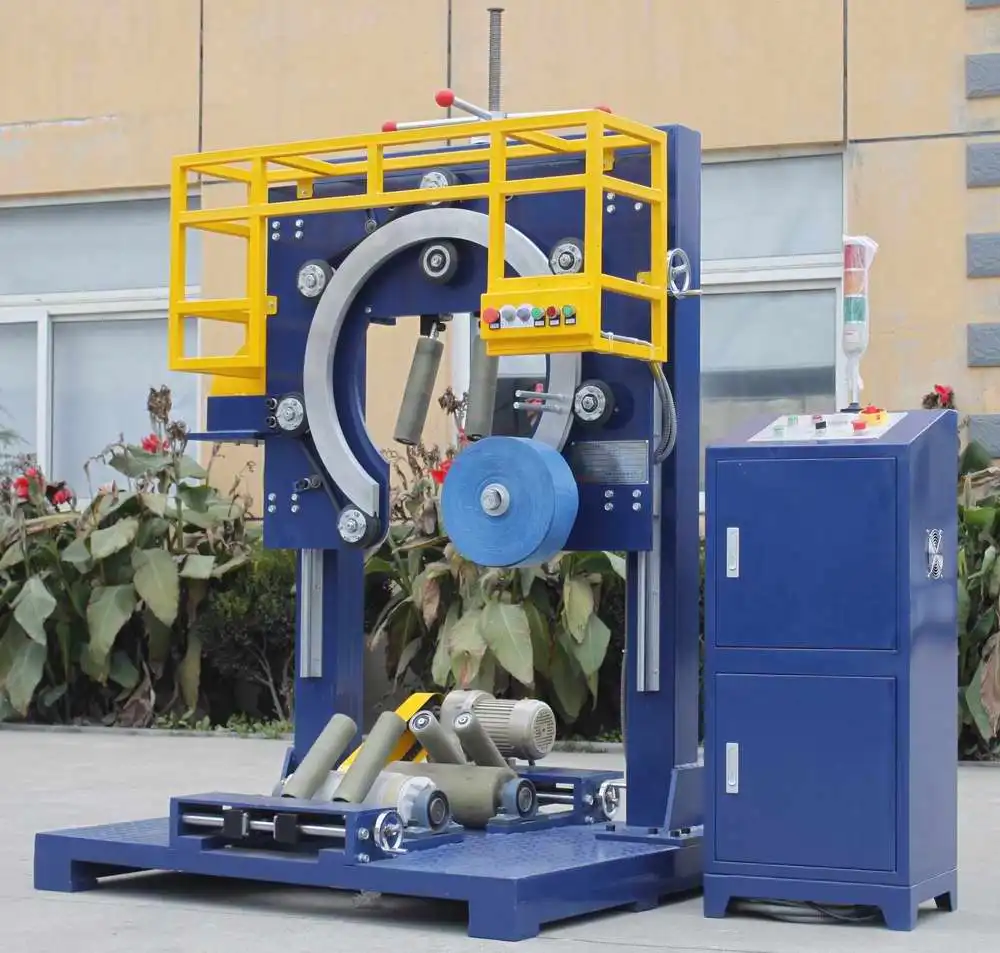
In today's competitive manufacturing landscape, achieving operational efficiency is crucial for success. Companies increasingly adopt lean manufacturing principles to eliminate waste, streamline workflows, and maximize value delivery. A key technology supporting these goals is the coil wrapping machine. This automated packaging solution plays a significant role in optimizing the final stages of production for coiled materials. Let's explore how automated coil wrapping directly contributes to lean manufacturing objectives.
Lean manufacturing is more than just cost-cutting; it's a systematic approach focused on eliminating non-value-adding activities (waste) and continuously improving processes. Coil wrapping machines directly address several types of waste identified in lean thinking, transforming manual, inconsistent packaging into an efficient, automated, and reliable operation that enhances quality, speed, and precision.
Implementing automated solutions like coil wrappers embodies the lean principle of *Kaizen* (continuous improvement). By examining how these machines integrate into production, we can understand their essential contribution to building agile, efficient, and waste-free manufacturing systems.
1. Understanding the Coil Wrapping Machine and Its Functionality
1.1. Defining the Technology
Coil wrapping machines are automated industrial packaging systems specifically designed to apply protective wrapping material (like stretch film, VCI paper, or polyethylene) around coiled products such as steel coils, aluminum coils, wire coils, cable spools, and hose coils. The primary function is to secure and protect these materials during handling, storage, and transportation. Compared to manual wrapping methods, which are often slow, labor-intensive, and inconsistent, automated coil wrappers deliver uniform, high-quality results efficiently, aligning perfectly with lean manufacturing's emphasis on standardization and waste reduction.
By integrating these machines, manufacturers accelerate the packaging phase, enhance product protection, and ensure consistency across all wrapped coils. The automation typically involves rotating the coil or a wrapping ring around the coil to apply the material systematically.
1.2. Key Components of an Automated Coil Wrapping System
A standard coil wrapping machine includes several critical components working together:
- Coil Loading/Unloading Mechanism: Often integrated with conveyors or tilters to automatically position coils for wrapping and remove them afterward, minimizing manual handling.
- Wrapping Ring or Rotating Arm: The core component that applies the wrapping material around the coil's circumference and through its eye (for orbital wrappers).
- Film/Material Dispenser: Features pre-stretch capabilities (for stretch film) and tension control to optimize material usage and ensure a secure wrap.
- Control System (PLC): Allows operators to set parameters like rotation speed, wrapping layers, overlap percentage, and tension, enabling customization for different coil types and requirements.
- Cutting and Clamping Unit: Automatically cuts the wrapping material at the end of the cycle and secures the tail, ensuring a clean finish.
- Safety Features: Includes light curtains, safety fencing, emergency stops, and interlocks to protect personnel during operation, adhering to workplace safety standards.
These components automate the entire wrapping cycle, significantly reducing the need for operator intervention and boosting overall packaging throughput.
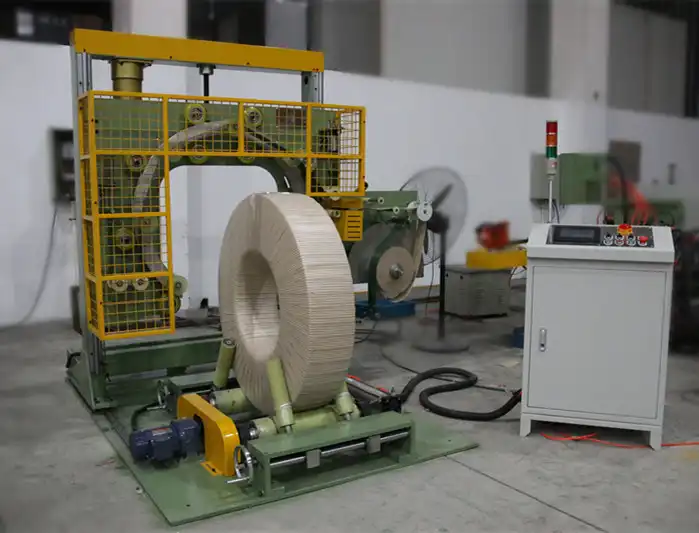
1.3. The Significance of Automation in Coil Packaging
Automation is fundamental to achieving lean objectives, and coil wrapping machines exemplify its benefits in the packaging process:
- Increased Throughput: Machines operate continuously at speeds significantly higher than manual methods, reducing cycle times.
- Reduced Labor Dependency: Automating the task frees up employees for more value-added activities, addressing labor shortages and reducing costs.
- Enhanced Quality and Consistency: Automated control ensures every coil is wrapped to the same specification, eliminating variability and improving package integrity.
- Optimized Material Consumption: Precise tension control and programmed wrapping patterns minimize the overuse of stretch film or other materials.
2. How Coil Wrapping Machines Drive Waste Reduction (Muda Elimination)
Lean manufacturing famously targets the elimination of "Muda" (waste). Coil wrapping machines contribute significantly to reducing several types of waste:
2.1. Reducing Material Waste (Overproduction, Defects)
Inefficient material use is a major source of waste in manual packaging. Coil wrapping machines address this directly:
- Optimized Material Use: Pre-stretch mechanisms in stretch wrappers can elongate film by up to 300%, drastically reducing the amount of film needed per coil compared to manual application. Precise tension control prevents excessive material application.
- Elimination of Defects: Automated wrapping ensures consistent coverage and secure seals, preventing packaging failures (defects) that might require rework or cause product damage during transit. This reduces the waste associated with damaged goods and re-packaging efforts.
- Programmable Patterns: Machines apply material exactly where needed, minimizing unnecessary overlap and reducing scrap generation, directly combating the waste of inventory and materials.
2.2. Minimizing Time Waste (Waiting, Motion)
Time is a critical resource, and manual wrapping is inherently slow and inefficient.
- Reduced Cycle Times: Automation dramatically cuts down the time required to wrap each coil, eliminating bottlenecks (waiting) in the production flow and supporting Just-In-Time (JIT) principles.
- Streamlined Workflow: Integrating wrapping machines with production lines via conveyors eliminates delays associated with moving coils manually to separate wrapping stations.
- Less Rework: Consistent, high-quality wrapping minimizes the need for inspection and rework, saving valuable production time. Operators are freed from inefficient manual motions.
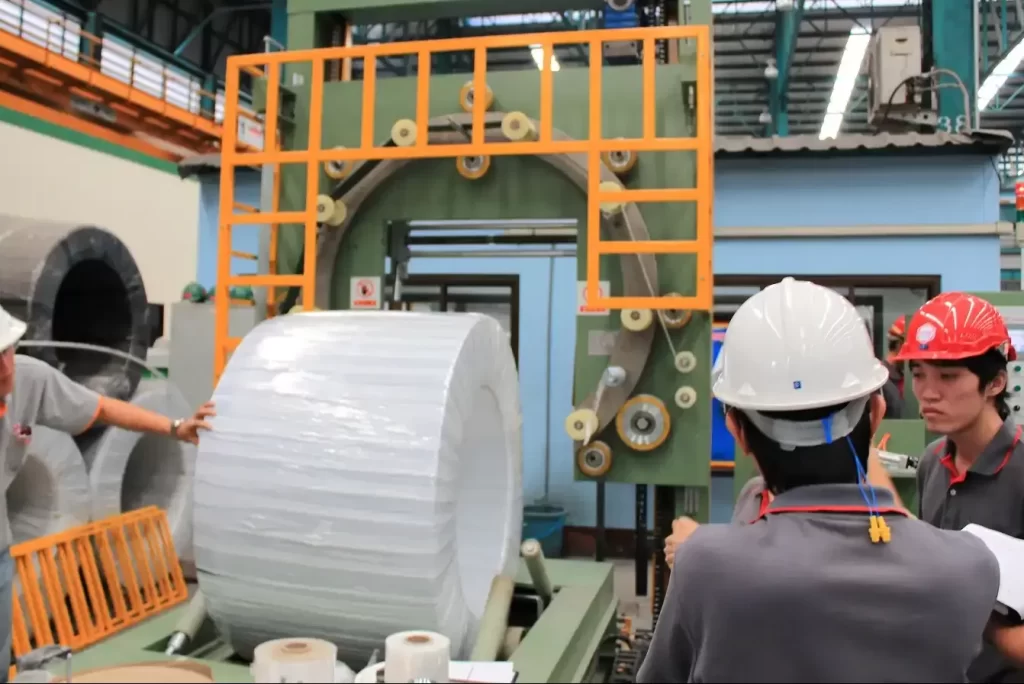
2.3. Enhancing Packaging Consistency and Reducing Variability
Variability is an enemy of lean systems. Manual wrapping inherently introduces inconsistency.
- Standardized Process: Coil wrapping machines execute the same wrapping pattern with the same tension and number of layers every time, ensuring uniformity.
- Improved Product Protection: Consistent wrapping guarantees adequate protection for all coils, reducing the risk of damage (a form of waste) during shipping and handling.
- Predictable Output: Automation leads to predictable packaging times and quality, allowing for better production planning and scheduling.
3. The Contribution of Coil Wrapping Machines to Workplace Safety
Lean manufacturing emphasizes "Respect for People," which includes providing a safe working environment. Coil wrapping machines significantly enhance safety:
3.1. Reducing Ergonomic Risks and Injuries (Motion Waste)
Manual wrapping of large, heavy coils involves repetitive lifting, bending, pushing, and stretching, posing significant ergonomic risks.
- Eliminating Manual Strain: Automation removes the need for operators to manually manipulate heavy coils or stretch wrap rolls, drastically reducing the risk of musculoskeletal disorders (MSDs) and repetitive strain injuries.
- Ergonomic Design: Machines are designed for safe operator interaction, often involving controls at accessible heights and minimizing physical exertion during setup or monitoring.
3.2. Minimizing Manual Handling Hazards
Handling heavy coils manually is inherently dangerous.
- Automated Handling: Integration with conveyors, tilters, and upenders automates the movement of coils, eliminating the risks associated with manual lifting and positioning, such as crush injuries or falls.
- Reduced Operator Exposure: Operators interact with the machine primarily through control panels, reducing their direct exposure to heavy loads and moving machinery during the wrapping cycle.
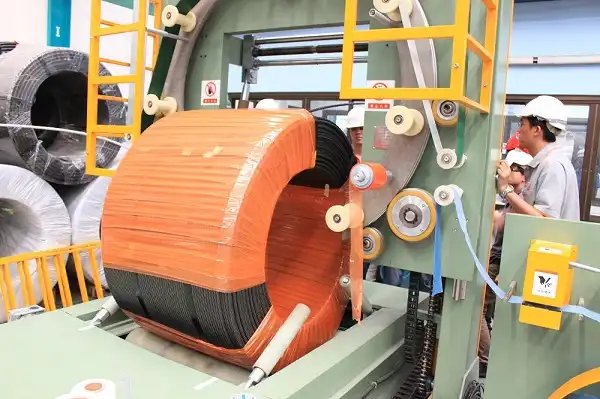
3.3. Built-in Safety Features and Compliance
Modern coil wrapping machines incorporate numerous safety features to comply with regulations (like OSHA or CE standards) and protect personnel:
- Emergency Stops: Easily accessible buttons allow immediate shutdown in emergencies.
- Safety Guarding: Physical barriers (fences, enclosures) and light curtains prevent access to hazardous areas during operation.
- Interlock Systems: Sensors ensure the machine stops if guards are opened or personnel enter restricted zones.
- Warning Systems: Alarms and lights indicate machine status or potential issues.
These features create a safer work environment, reduce accident-related downtime, and demonstrate a commitment to employee well-being.
4. Improving Customer Satisfaction through Enhanced Packaging
Ultimately, lean manufacturing aims to deliver maximum value to the customer. Coil wrapping machines contribute to this goal in several ways:
4.1. Ensuring Product Integrity and Quality upon Arrival
Delivering products in perfect condition is paramount for customer satisfaction.
- Superior Protection: Consistent, secure wrapping shields coils from environmental factors (moisture, dust, corrosion) and physical damage during transit and storage.
- Reduced Damage Claims: High-quality packaging minimizes the likelihood of customers receiving damaged goods, reducing returns, complaints, and replacement costs. This directly impacts customer perception and loyalty.
4.2. Meeting Diverse and Custom Packaging Needs
Flexibility is key to meeting specific customer requirements.
- Customizable Wrapping Programs: Machines allow manufacturers to easily adjust wrapping parameters (material type, layers, tension) to meet specific customer demands or shipping requirements (e.g., export wrapping, long-term storage).
- Professional Appearance: Consistently wrapped coils present a professional image, enhancing brand perception and customer confidence.
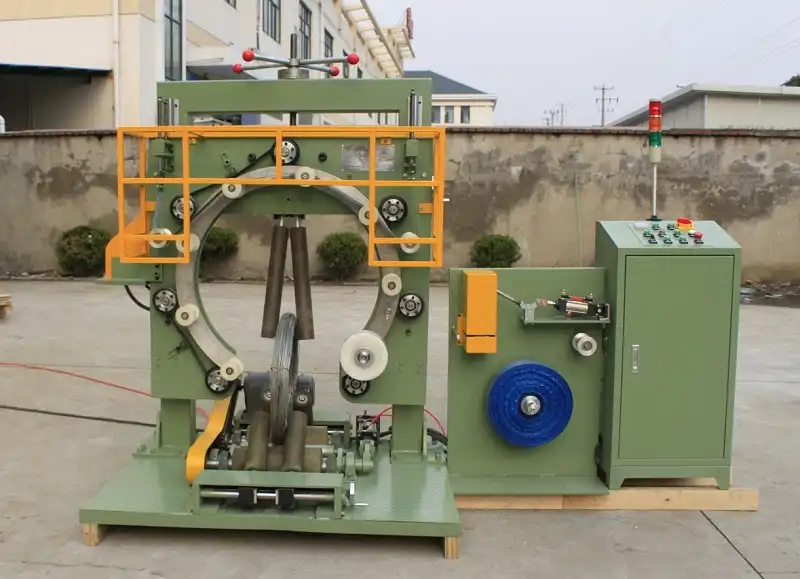
4.3. Supporting Sustainability Goals
Environmental responsibility is increasingly important to customers.
- Optimized Material Use: Reducing film consumption through pre-stretch and precision control aligns with sustainability initiatives.
- Compatibility with Eco-Friendly Materials: Many modern machines can handle recyclable or biodegradable wrapping materials, helping manufacturers meet corporate and customer environmental goals.
Conclusion: Coil Wrappers as Essential Lean Tools
Coil wrapping machines are far more than just packaging equipment; they are strategic assets for implementing lean manufacturing principles. By automating the wrapping process, they directly address multiple forms of waste—reducing material consumption, saving time, preventing defects, and minimizing unsafe motion. They enhance operational efficiency, improve workplace safety, ensure product quality, and ultimately contribute to greater customer satisfaction. For manufacturers dealing with coiled materials, integrating automated coil wrapping technology is a decisive step towards achieving a truly lean, efficient, and competitive operation.