1. Understanding Orbital Stretch Wrappers: The Fundamentals
Choosing the right orbital stretch wrapper for your specific needs can seem complex given the variety of models available. These machines are essential for securely packaging products, minimizing transit damage, and boosting operational efficiency. Selecting an unsuitable model, however, can lead to inefficiencies or underutilized capabilities.
This guide provides a comprehensive overview to aid your selection process, covering everything from assessing your packaging needs to understanding key machine features. Whether you run a small business aiming to improve packaging or manage an industrial facility needing a heavy-duty solution, this information will help you select the ideal orbital stretch wrapper.
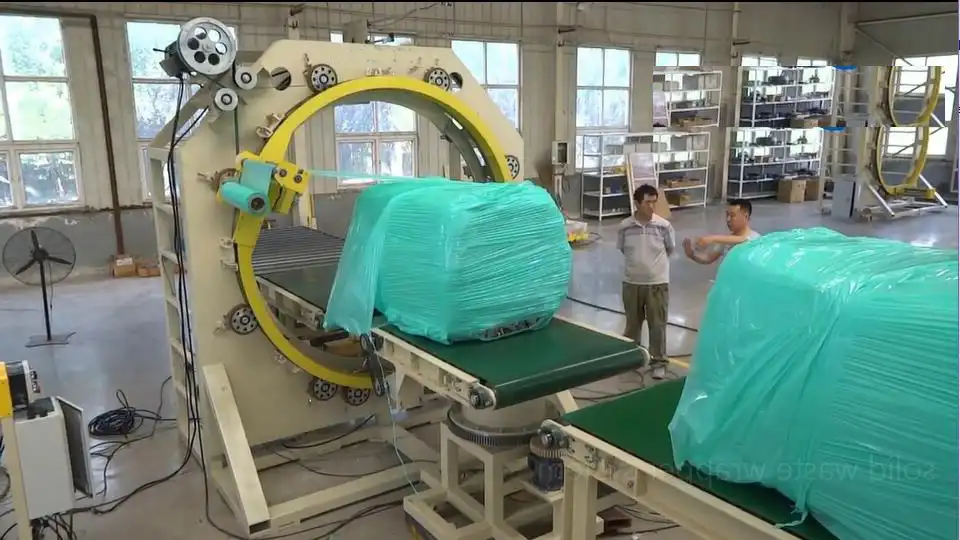
1.1 What is an Orbital Stretch Wrapper?
First, let's clarify what an orbital stretch wrapper is and its mechanism. Unlike traditional turntable wrappers designed for pallets, orbital wrappers feature a vertical ring that rotates around a stationary product. This ring dispenses stretch film, creating a tight, secure wrap around items, particularly those that are long, bulky, or irregularly shaped, such as pipes, lumber, doors, windows, textiles, or bundled materials.
1.2 Core Functions and Benefits
The primary function is applying stretch film automatically and consistently. Key benefits include:
- Load Security: Ensures products are tightly bundled and stabilized for transport.
- Product Protection: Shields items from dust, moisture, and surface damage.
- Efficiency: Automates the wrapping process, saving time and labor compared to manual methods.
- Consistency: Provides a uniform wrap quality for every product.
- Versatility: Effectively wraps items unsuitable for standard pallet wrappers.
1.3 Key Industries Served
Orbital stretch wrappers are valuable across numerous sectors:
- Building Materials: Wrapping lumber, pipes, insulation, siding, doors, and windows.
- Manufacturing: Securing components, finished goods, extrusions, and bundled parts.
- Textiles: Packaging rolls of fabric, carpet, or other materials.
- Furniture: Protecting assembled or flat-packed furniture items.
- Automotive: Wrapping long parts like exhausts or bundled components.
2. Assessing Your Specific Packaging Requirements
Identifying your specific packaging needs is the crucial first step. This involves a thorough analysis of the products you handle, your required throughput, and any unique operational challenges.
2.1 Analyzing Product Characteristics
Consider the physical attributes of the items you need to wrap:
- Dimensions (Length, Width, Height): Determine the maximum and minimum sizes. Long items (pipes, lumber) have different needs than bulky items (furniture).
- Shape: Are products uniform, irregular, or bundled? Orbital wrappers excel with non-standard shapes.
- Weight: Note the typical and maximum weight of the products.
- Fragility: Do items require specific tension control to avoid damage?
2.2 Determining Packaging Volume and Speed Needs
Estimate your throughput requirements:
- Volume: How many items or bundles do you need to wrap per hour, shift, or day?
- Speed: Do you need a machine integrated into a high-speed production line, or is lower throughput acceptable?
- Low to Medium Volume: May suit semi-automatic machines.
- High Volume: Often requires fully automatic systems for maximum efficiency.
Matching machine capacity to your volume prevents bottlenecks or unnecessary investment in oversized equipment.
3. Evaluating Critical Load Specifications
Carefully assessing the machine's ability to handle your product load specifications is vital to prevent operational issues and potential damage. Focus on the machine's ring size and weight capacity relative to your products.
3.1 Ring Diameter and Product Dimensions
The ring diameter (or opening size) dictates the maximum cross-sectional dimension (width and height) of the product the machine can accommodate.
- Measure Your Largest Products: Accurately measure the maximum width and height of the items you intend to wrap.
- Select Appropriate Ring Size: Choose a machine with a ring diameter sufficiently larger than your product's maximum cross-section to allow smooth passage and effective wrapping without contact or constriction.
- Smaller Rings: Suitable for compact items like small bundles or extrusions.
- Larger Rings: Necessary for bulky goods like doors, windows, panels, or large bundles of material.
3.2 Machine Weight Capacity
Equally important is the machine's maximum weight capacity. Exceeding this limit can strain components, lead to poor wrap quality, cause premature wear, or result in equipment failure.
- Identify Heaviest Loads: Determine the weight of the heaviest products you will wrap.
- Verify Machine Specification: Ensure the wrapper's stated weight capacity comfortably exceeds your maximum product weight.
- Light-Duty Models: Suitable for lighter products often found in smaller operations.
- Heavy-Duty Models: Built with robust conveyors and frames to handle substantial weights typical in industrial settings (e.g., steel bundles, large timber packs).
4. Exploring Automation Levels and Features
The level of automation significantly impacts labor requirements, throughput, and initial cost. Consider which level best suits your operation.
4.1 Semi-Automatic vs. Fully Automatic Systems
- Semi-Automatic Orbital Wrappers:
- Operation: Require an operator to manually place the product, initiate the wrap cycle, attach the film tail initially, and cut the film upon completion.
- Pros: Lower initial cost, simpler mechanics, suitable for lower volume or varied product runs.
- Cons: Requires dedicated operator time, slower throughput, potential for inconsistency in film attachment/cutting.
- Fully Automatic Orbital Wrappers:
- Operation: Integrate into a conveyor line. Automatically sense the product, feed it into the wrapping ring, apply, seal, and cut the film without operator intervention.
- Pros: High throughput, minimal labor required, consistent wrapping, ideal for integrated production lines.
- Cons: Higher initial investment, more complex integration and maintenance.
4.2 Advanced Features: Sensors and Integration
Modern wrappers offer features enhancing efficiency and control:
- Product Sensors: Automatically detect the leading and trailing edges of the product for precise start/stop of the wrapping cycle.
- Remote Operation/Monitoring: Allows control and status checks from a central location or mobile device.
- Conveyor Integration: Seamless connection with existing or new powered conveyor systems for automated product flow.
- Variable Speed Control: Adjust ring rotation and conveyor speed for different products or line requirements.
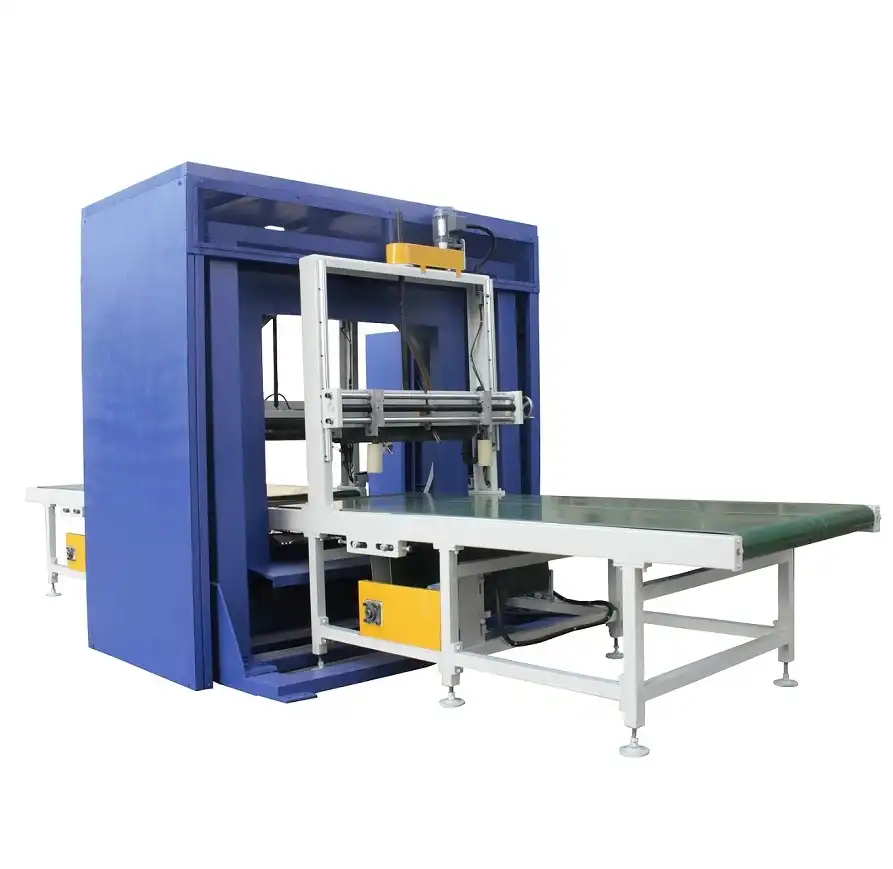
5. Prioritizing Durability and Build Quality
An orbital stretch wrapper is a significant investment; its durability and build quality are paramount for long-term performance and return on investment (ROI).
5.1 The Importance of Robust Construction
Look for machines built for industrial environments:
- Frame Materials: Heavy-gauge steel frames provide stability and longevity, resisting vibration and wear. Stainless steel options are available for corrosive environments or food/pharma applications.
- Component Quality: High-quality motors, bearings, belts, and electrical components reduce the likelihood of breakdowns.
- Ring Construction: A well-engineered, balanced ring ensures smooth rotation and consistent film application, especially at higher speeds.
A robust structure withstands the rigors of daily operation, ensuring reliable performance.
5.2 Long-Term Reliability and Maintenance Costs
While higher build quality may mean a higher initial price, it often translates to lower lifetime costs:
- Reduced Downtime: Durable machines experience fewer breakdowns.
- Lower Maintenance Needs: Quality components require less frequent repair or replacement.
- Longer Equipment Lifespan: A well-built machine will serve your operation for many years.
Consider the manufacturer's reputation for building reliable equipment.
6. Considering Operational Efficiency and Costs
Beyond the purchase price, evaluate the ongoing operational costs, including energy consumption and stretch film usage.
6.1 Energy Consumption Considerations
- Power Requirements: Check the machine's voltage and power consumption ratings.
- Energy-Saving Features: Look for models with:
- Variable frequency drives (VFDs) that adjust motor speed based on need.
- Sleep modes or automatic shutdowns during idle periods.
- Efficient motor designs.
An energy-efficient wrapper reduces utility bills and supports sustainability goals.
6.2 Optimizing Stretch Film Usage
Stretch film is a recurring cost. Efficient film usage is key to cost-effectiveness:
- Pre-Stretch Capability: Machines with powered pre-stretch systems elongate the film before application (e.g., 200-300% stretch). This uses less film per wrap while maintaining load containment, significantly reducing material costs.
- Adjustable Film Tension: Allows precise control over how tightly the film is applied, optimizing containment without crushing the product or wasting film.
- Film Break Detection: Sensors that stop the machine if the film breaks prevent wasted cycles.
7. Focusing on User-Friendliness and Safety
The machine must be easy and safe for operators to use, regardless of its technical sophistication.
7.1 Intuitive Controls and Operation
- Control Panel: Look for a clear, user-friendly interface (e.g., touchscreen HMI) with intuitive controls for setting parameters like wrap counts, tension, and overlap.
- Ease of Film Loading: A simple, accessible film carriage design speeds up roll changes.
- Troubleshooting Guides: On-screen diagnostics or clear manuals help operators resolve minor issues quickly.
7.2 Essential Safety Features and Standards
Safety is non-negotiable:
- Emergency Stop Buttons: Easily accessible E-stops should be strategically placed.
- Safety Guarding: Physical barriers or light curtains prevent access to moving parts (like the rotating ring) during operation.
- Interlocked Doors: Access panels should have safety interlocks that stop the machine when opened.
- Compliance: Ensure the machine meets relevant safety standards (e.g., CE marking in Europe, OSHA guidelines in the US).
8. Investigating Customization Possibilities
Standard models may not perfectly fit every unique application. Many manufacturers offer customization options.
8.1 Tailoring Film Delivery Systems
- Different Film Widths/Types: Options to accommodate various stretch film roll widths or specialized films (e.g., UV resistant, colored).
- Dual Roll Holders: For faster changeovers or applying different film types simultaneously.
8.2 Programmable Wrapping Cycles
- Custom Patterns: Ability to program specific wrap patterns for different products (e.g., more wraps on ends, specific overlap percentages).
- Recipe Storage: Save frequently used wrapping parameters for quick recall when changing products.
- Integration Options: Custom conveyors, top sheet dispensers (for added dust/moisture protection), or integration with upstream/downstream automation.
Discuss your specific needs with potential suppliers to explore tailored solutions.
9. Evaluating Manufacturer Support and Service
The relationship with the manufacturer or supplier doesn't end at purchase. Reliable support and maintenance services are crucial for maximizing uptime.
9.1 Warranty, Service Plans, and Training
- Warranty: Understand the duration and coverage (parts, labor).
- Service Plans: Inquire about preventative maintenance programs offered by the manufacturer or local distributors.
- Operator/Maintenance Training: Does the supplier provide comprehensive training upon installation?
9.2 Spare Parts Availability and Technical Support
- Spare Parts: Are critical spare parts readily available, either from the manufacturer or locally? Delays can cause significant downtime.
- Technical Support: Is responsive technical support (phone, online, field service) available when issues arise? Local support can be a significant advantage.
Conclusion: Making the Right Investment for Your Business
Selecting the optimal orbital stretch wrapper requires a detailed evaluation of your products, operational volume, automation needs, and budget. By carefully considering factors like load specifications, build quality, energy efficiency, safety features, customization options, and post-sale support, you can identify a machine that enhances your packaging process.
Investing thoughtfully in the right orbital wrapper translates to improved load security, reduced product damage, lower labor and material costs, and increased overall productivity—benefiting your business for years to come. Take the time to research, consult with suppliers, and potentially view demonstrations to make an informed decision aligned with your long-term operational goals.