Coil wrapping machines are indispensable in industries where precision, efficiency, and adaptability are key. From steel manufacturers to cable producers, these machines streamline the packaging process, ensuring that coils of various sizes and shapes are securely wrapped for storage or transportation. However, not all coils are uniform. They can vary in diameter, width, weight, and even shape, posing unique challenges that must be addressed by the machines designed to handle them.
For any business dealing with diverse coil requirements, understanding how these machines adapt to such variations is crucial. The ability of a machine to accommodate different coil specifications not only impacts operational efficiency but also ensures the integrity of the product during handling and shipping.
The adaptability of coil wrapping machines lies in their design, programming, and customization options. Whether dealing with small, flat coils or large, heavy, and irregularly shaped ones, these machines employ innovative features to meet industrial demands. But how exactly do they achieve this level of versatility?
[claim] Coil wrapping machines handle varying coil sizes and shapes by employing adjustable components, customizable programming, and advanced sensors that ensure precision and flexibility.
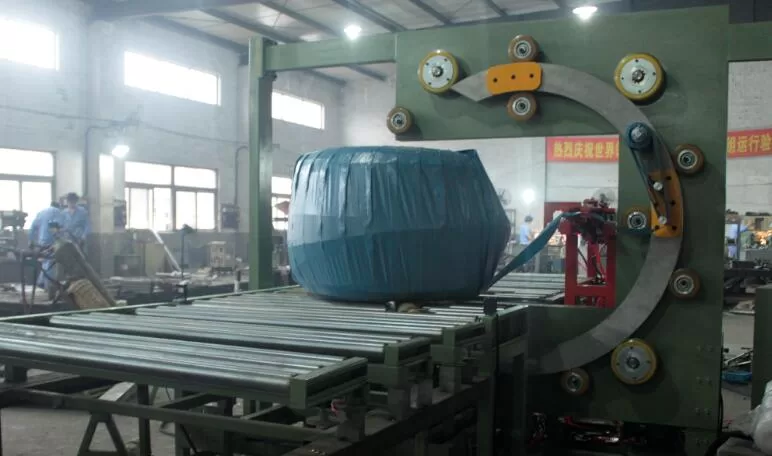
1. What Role Do Adjustable Components Play in Coil Wrapping?
1.1 Importance of Adjustable Frames and Rollers
One of the most critical factors in handling coils of different sizes and shapes is the adjustability of the machine’s components. Adjustable frames, rollers, and wrapping arms allow the machine to accommodate a wide range of dimensions. For instance, the frame can expand or contract to fit coils with varying diameters, while rollers can be repositioned to ensure stability during the wrapping process.
Without such adaptability, machines would be limited to handling a narrow range of coil sizes, making them less practical for industries that require versatility. Adjustable components ensure that the wrapping process remains consistent, regardless of coil dimensions, thereby maintaining product integrity and reducing the likelihood of damage during transportation.
1.2 Comparing Fixed vs. Adjustable Machines (With Table)
To illustrate the advantages of adjustability, here’s a comparison between fixed and adjustable machines:
Feature | Fixed Machines | Adjustable Machines |
---|---|---|
Flexibility | Limited to specific dimensions | Can handle a wide range of sizes |
Setup Time | Minimal for standard sizes | Slightly longer for adjustments |
Cost Efficiency | Lower initial cost | Higher ROI for diverse operations |
Product Versatility | Low | High |
While fixed machines are suitable for operations with uniform coil sizes, adjustable machines are essential for industries dealing with diverse product specifications. The ability to adapt to different coil sizes ensures higher efficiency and fewer bottlenecks in the production process.
1.3 How Adjustable Components Improve Efficiency
Adjustable components not only enhance versatility but also improve operational efficiency. For instance:
- Reduced Changeover Time: Machines with quick-adjust features allow operators to switch between coil sizes with minimal downtime.
- Enhanced Stability: Adjustable rollers and supports ensure that coils of all shapes remain secure during the wrapping process.
- Lower Error Rates: By customizing the machine’s settings for each coil size, the likelihood of misalignment or improper wrapping is significantly reduced.
This adaptability is particularly valuable in industries where production schedules are tight, and product variation is high.
1.4 Breaking Down Machine Versatility with Real-World Examples
Consider two scenarios:
- Scenario 1: A steel manufacturer uses adjustable coil wrapping machines to handle coils ranging from 500mm to 2000mm in diameter. Their ability to quickly adjust machine settings has reduced downtime by 40%.
- Scenario 2: A cable producer wraps coils of varying widths and weights. By utilizing machines with adjustable wrapping arms, they’ve eliminated the need for multiple machines, saving both space and costs.
These examples highlight how adjustable components enable businesses to achieve greater operational flexibility and efficiency.
1.5 Fact Check: Are Adjustments Always Necessary?
- True: Adjustable components are essential for operations with diverse coil sizes and shapes.
- False: All coil wrapping machines need adjustable parts. Fixed machines are sufficient for uniform production lines.
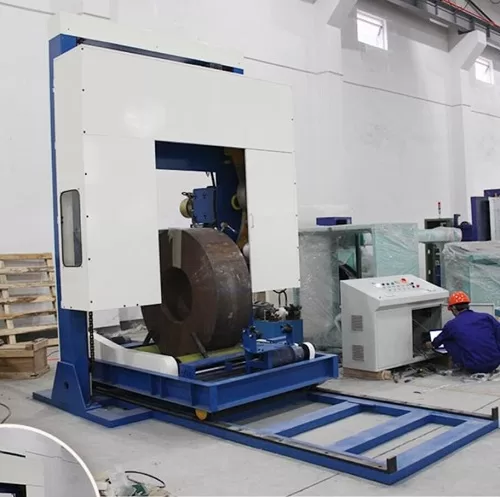
2. How Does Programming Enable Flexibility in Coil Wrapping?
2.1 Role of Pre-Set Programs for Different Coil Types
Modern coil wrapping machines come equipped with pre-set programs designed to handle a wide variety of coil types. These programs are tailored to specific dimensions, weights, and shapes, allowing operators to switch between configurations with the push of a button. For example, a machine might include pre-loaded settings for small, lightweight coils as well as larger, heavy-duty ones, ensuring consistent performance without requiring manual adjustments.
Pre-set programs also minimize human error. Operators no longer need to fine-tune the machine for every coil type, as the software automatically adjusts parameters such as wrapping speed, tension, and roller positioning. This feature is especially beneficial in industries where production lines handle multiple coil sizes within a single shift.
2.2 Benefits of Custom Programming (With Table)
While pre-set programs are convenient, custom programming offers even greater flexibility. Customization allows businesses to fine-tune machine settings for unique coil specifications or special requirements. Here’s a comparison of pre-set and custom programming:
Feature | Pre-Set Programs | Custom Programming |
---|---|---|
Ease of Use | High (Plug-and-play) | Moderate (Requires expertise) |
Flexibility | Limited to standard coil types | Unlimited (Handles unique shapes) |
Cost Efficiency | Low setup cost | Higher ROI for specialized needs |
Error Reduction | High | Very high |
Custom programming is particularly valuable for industries that deal with unconventional coil shapes or require highly specific wrapping techniques, such as spiral wrapping or multi-layer protection.
2.3 Diving Deeper: Advanced Algorithms for Irregular Coils
One of the most impressive features of modern coil wrapping machines is their ability to handle irregularly shaped coils using advanced algorithms. These algorithms analyze data from sensors (such as coil dimensions and weight) and dynamically adjust machine operations in real time.
For example:
- Dynamic Wrapping Tension: The machine adjusts the wrapping film tension to accommodate uneven surfaces, ensuring a secure and uniform wrap without damaging the product.
- Path Optimization: Algorithms calculate the most efficient wrapping path for irregular shapes, reducing film waste and speeding up the process.
These innovations not only improve the quality of the wrapping process but also reduce material costs and energy consumption, adding significant value to the operation.
2.4 Conclusion: Efficiency Through Intelligent Software
Programming is the brain of a coil wrapping machine. Pre-set programs provide a foundation for handling standard coil sizes, while custom programming and advanced algorithms enable the machine to adapt to unique challenges. Together, these features ensure that the machine operates efficiently, regardless of the diversity in coil specifications.
2.5 Fact Check: Manual Control vs. Automated Programs
- True: Automated programs reduce setup time and improve consistency in the wrapping process.
- False: Manual control is always more precise than automated programs. Advanced algorithms outperform manual adjustments in most cases.
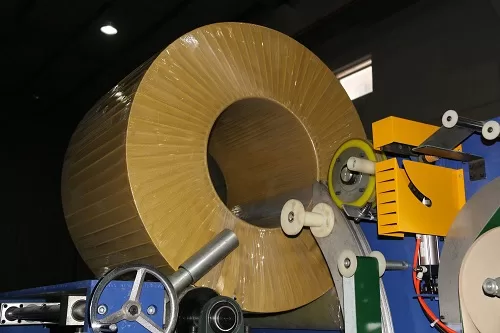
3. What Are the Challenges of Wrapping Irregular Shapes?
3.1 Identifying Common Irregular Coil Shapes (With Table)
Not all coils are perfectly circular or uniform in size. Some industries, such as cable manufacturing and steel processing, deal with irregularly shaped coils that present unique challenges. Below is a breakdown of common irregular coil shapes and their specific difficulties:
Coil Shape | Challenges in Wrapping | Solutions |
---|---|---|
Oval Coils | Uneven tension, inconsistent wrapping | Dynamic tension adjustment |
Flat Coils | Limited height for wrapping layers | Multi-layer programming |
Spiral Coils | Complex surface geometry | Path optimization algorithms |
Asymmetrical Coils | Instability during wrapping | Adjustable supports and rollers |
These challenges require machines with advanced customization options, robust sensors, and precision programming to ensure proper wrapping.
3.2 How Machines Compensate for Irregularities
Wrapping irregular coils demands a combination of mechanical and software solutions. Here’s how machines adapt:
- Adjustable Rollers and Arms: These components stabilize coils of varying shapes, ensuring they remain secure during the wrapping process.
- Real-Time Sensor Feedback: Sensors detect irregularities in the coil’s surface or dimensions and adjust wrapping tension and speed accordingly.
- Custom Wrapping Patterns: For coils with unique shapes, custom patterns can be programmed to ensure full coverage and protection.
These features work together to overcome the challenges posed by irregular shapes, ensuring that the wrapping process remains consistent and efficient.
3.3 Real-Life Case Studies: Success Stories in Handling Irregular Coils
- Case Study 1: A cable manufacturer faced issues wrapping oval coils, which often resulted in loose or uneven wraps. After upgrading to a machine with dynamic tension control, they achieved a 50% improvement in wrap consistency and reduced film waste by 30%.
- Case Study 2: A steel processing plant dealt with large, asymmetrical coils that frequently shifted during wrapping. By implementing machines with adjustable supports and real-time sensor feedback, they eliminated instability issues and increased production speed by 20%.
These examples demonstrate how innovative features enable machines to handle even the most challenging coil shapes effectively.
3.4 Key Innovations in Technology for Irregular Coil Wrapping
Recent advancements in coil wrapping technology have focused on improving versatility and precision. Key innovations include:
- AI-Powered Sensors: These sensors analyze coil dimensions and surface irregularities in real time, enabling more accurate adjustments.
- Automated Balancing Systems: Machines equipped with balancing systems stabilize uneven or asymmetrical coils during wrapping.
- Energy-Efficient Motors: Newer machines use energy-efficient motors to handle heavy, irregular coils without overheating or excessive power consumption.
These technologies ensure that even the most irregular coils can be wrapped efficiently and securely, meeting the demands of modern industries.
Fact Check: Wrapping Irregular Shapes
- True: Advanced sensors and programming enable machines to wrap irregular coils with precision.
- False: Irregular coil shapes always require manual intervention. Modern machines can handle most irregularities autonomously.
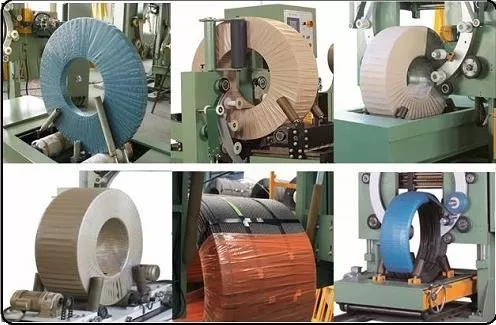
4. Why Is Sensor Technology Critical for Precision?
4.1 Role of Sensors in Detecting Coil Dimensions
Sensor technology is the backbone of precision in modern coil wrapping machines. Before the wrapping process begins, sensors detect critical parameters such as the coil’s diameter, width, and weight. This data allows the machine to make real-time adjustments to ensure optimal wrapping performance.
For example, sensors can measure the diameter of a coil and adjust the wrapping arm’s position accordingly. Similarly, weight sensors ensure that the machine applies adequate tension to secure the coil without causing damage. Without these capabilities, the wrapping process would rely on manual measurements, increasing the likelihood of errors and inefficiencies.
4.2 Types of Sensors Used in Coil Wrapping Machines (With Table)
Different sensors are employed in coil wrapping machines to monitor and adapt to various aspects of the process. Here’s a breakdown of the most common types and their functions:
Sensor Type | Function | Example Application |
---|---|---|
Ultrasonic Sensors | Measure coil diameter and width using sound waves | Adjusting wrapping arm position |
Weight Sensors | Detect the coil’s weight to ensure proper tension | Avoiding over-tightening or instability |
Proximity Sensors | Determine the distance between coil and machine parts | Preventing collisions during wrapping |
Photoelectric Sensors | Detect coil edges or irregularities in shape | Ensuring complete wrapping coverage |
Temperature Sensors | Monitor machine temperature during operation | Preventing overheating during long shifts |
These sensors work together to ensure that the machine operates efficiently and produces consistent results, even when dealing with varying coil specifications.
4.3 How Sensors Enable Seamless Adaptation to Coil Variations
The integration of sensors into coil wrapping machines enables seamless adaptation to coils of different sizes and shapes. Here’s how:
- Dynamic Adjustments: Sensors provide real-time feedback, allowing the machine to adjust wrapping tension, speed, and path dynamically.
- Error Detection: If a coil is misaligned or improperly loaded, sensors can halt the operation and alert the operator to prevent further issues.
- Material Optimization: By accurately measuring coil dimensions, sensors help reduce film waste by applying the exact amount of wrapping material needed.
For example, a machine equipped with ultrasonic and weight sensors can handle a transition from a small, lightweight coil to a large, heavy one without operator intervention. This automation not only saves time but also ensures precision and consistency.
4.4 Future of Automation: AI-Driven Sensor Systems
The future of coil wrapping machines lies in the integration of artificial intelligence (AI) with sensor technology. AI-driven systems can analyze sensor data to predict maintenance needs, optimize machine settings, and even detect subtle changes in coil specifications that may indicate manufacturing defects.
Some potential advancements include:
- Predictive Maintenance: AI algorithms analyze temperature and vibration data to identify signs of wear in machine components before they fail.
- Self-Learning Systems: Machines equipped with AI can learn from previous wrapping cycles to improve efficiency and accuracy over time.
- Enhanced Safety Features: AI-powered sensors can detect operator proximity and automatically pause operations to prevent accidents.
These innovations will further enhance the adaptability and efficiency of coil wrapping machines, making them indispensable in modern manufacturing environments.
Fact Check: Sensor Technology
- True: Sensors provide real-time feedback that enhances precision and efficiency in the wrapping process.
- False: Sensors are only necessary for advanced machines. Even basic machines benefit from sensor integration to improve performance.
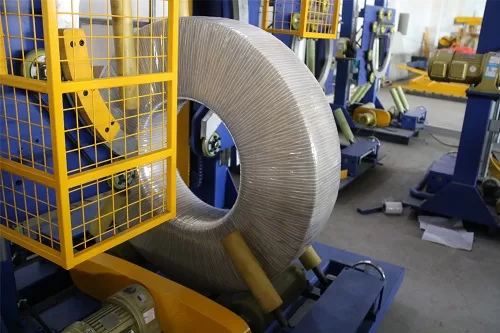
Conclusion
[claim] Coil wrapping machines achieve their versatility and precision through a combination of adjustable components, intelligent programming, advanced sensors, and operator training.
From accommodating diverse coil sizes and shapes to ensuring consistent wrapping quality, these machines represent the pinnacle of automation and efficiency in industrial packaging. Adjustable frames and rollers provide mechanical adaptability, while programming and AI-driven sensor systems enable intelligent adjustments in real time. Together, these features allow the machines to handle everything from standard circular coils to irregularly shaped ones with ease.
As industries continue to demand greater efficiency and customization, the role of coil wrapping machines will only grow. Businesses that invest in high-quality machines and prioritize operator training can maximize their operational efficiency and reduce costs associated with downtime, maintenance, and material waste. By understanding how these machines handle varying coil specifications, companies can make informed decisions that align with their production needs and long-term goals.
Would you like me to expand further or provide additional details on any specific sub-section?