# How Do Coil Wrapping Machines Differ in Terms of Safety Features? A Comprehensive Guide
Handling heavy loads like steel coils demands uncompromising safety. Coil wrapping machines are crucial in many industrial settings, but their safety features can differ substantially, impacting operational risk and efficiency. Understanding these variations is key to selecting equipment that safeguards both personnel and materials effectively.
Safety in coil wrapping machines goes beyond basic operator protection; it influences productivity, regulatory compliance, and long-term operational costs. Machines equipped with robust safety mechanisms significantly reduce workplace incidents and enhance overall operational reliability.
For businesses considering an investment in coil wrapping technology, grasping the nuances of available safety features is paramount. This guide explores the critical safety differences between machines to help you align your choice with your operational safety and efficiency objectives.
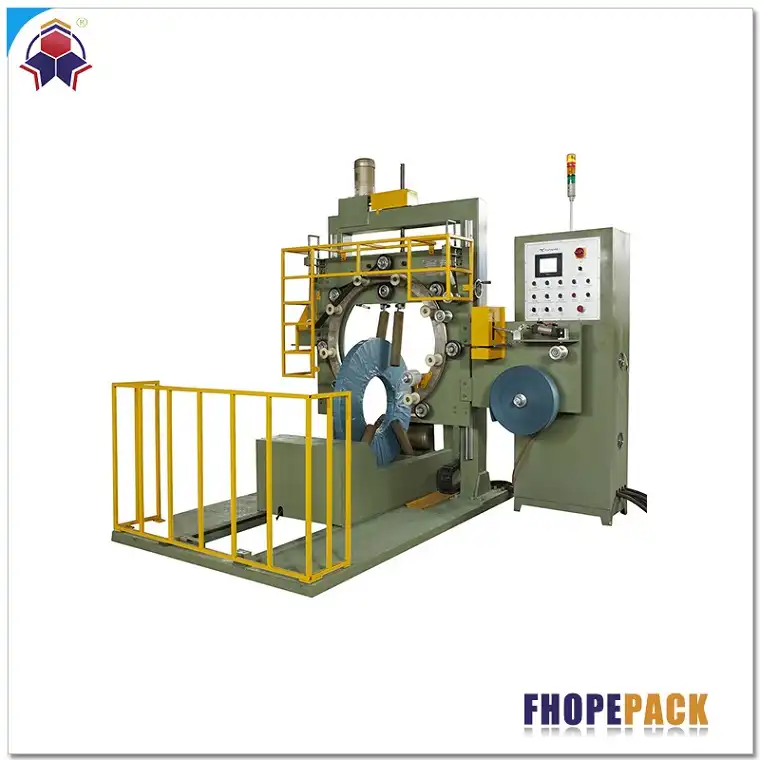
---
### Table of Content
1. Why are Robust Safety Features Crucial in Coil Wrapping Machines?
* 1.1 The Paramount Importance of Operator Protection
* 1.2 Ensuring Compliance with Safety Regulations
* 1.3 Minimizing Downtime and Operational Disruptions
2. What are the Standard Safety Features Found in Coil Wrapping Machines?
* 2.1 Essential Emergency Stop Mechanisms
* 2.2 Physical Safety Barriers and Machine Guarding
* 2.3 Basic Automated Detection Systems
3. How Do Advanced Safety Technologies Elevate Operational Safety and Efficiency?
* 3.1 Integration of Smart Sensors for Enhanced Precision and Monitoring
* 3.2 Automated Fault Detection and Diagnostic Capabilities
* 3.3 Boosting Operational Efficiency Through Integrated Safety
4. Are Customizable Safety Features a Worthwhile Investment?
* 4.1 Tailoring Safety Measures to Specific Operational Needs
* 4.2 Evaluating the Long-Term Cost Benefits of Customization
* 4.3 Building Trust and Fostering a Safety-First Culture
---
## 1. Why are Robust Safety Features Crucial in Coil Wrapping Machines?
### 1.1 The Paramount Importance of Operator Protection
Coil wrapping machines frequently handle large, heavy, and unwieldy loads, presenting significant risks. Operators can be vulnerable to injuries from moving components, unexpected coil shifts, improper loading, or system malfunctions. Essential safety features mitigate these risks directly.
* **Key Protections:** Features such as easily accessible emergency stop buttons, interlocked safety barriers, light curtains, and intuitive control interfaces are fundamental for preventing accidents.
* **Impact:** By minimizing risks to personnel, these features foster a safer working environment, boost employee morale, and reduce the likelihood of serious incidents.
### 1.2 Ensuring Compliance with Safety Regulations
Industrial operations are subject to strict safety standards mandated by regulatory bodies like the Occupational Safety and Health Administration (OSHA) in the U.S. or equivalent international organizations adhering to standards like ISO 12100 (Safety of machinery).
* **Compliance:** Coil wrapping machines designed with certified safety mechanisms help businesses meet these legal requirements, thereby avoiding potential penalties, legal issues, and operational shutdowns during safety audits.
* **Verification:** Look for machinery that explicitly states compliance with relevant regional or international safety standards.
### 1.3 Minimizing Downtime and Operational Disruptions
Workplace accidents cause not only human suffering but also significant operational disruption. Production halts, investigation processes, and potential equipment damage lead to costly downtime.
* **Reliability:** Machines incorporating advanced safety features inherently reduce the frequency and severity of such incidents. This ensures more consistent productivity and operational continuity.
* **Investment:** Investing in superior safety is, therefore, a direct investment in operational reliability and efficiency.
---
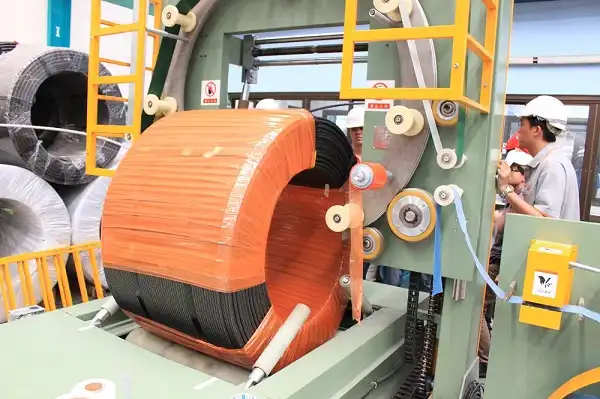
## 2. What are the Standard Safety Features Found in Coil Wrapping Machines?
### 2.1 Essential Emergency Stop Mechanisms
Emergency stop (E-stop) buttons are a universal safety requirement on industrial machinery.
* **Function:** They provide a means for operators or bystanders to immediately halt all machine movement in an emergency situation, preventing injury or limiting damage.
* **Placement:** Effective E-stop systems include multiple buttons strategically located around the machine for quick access from various operational points. Their design ensures they are easily identifiable and fail-safe.
### 2.2 Physical Safety Barriers and Machine Guarding
Physical guards are crucial for preventing accidental contact with moving parts or hazardous zones.
* **Types:** These can range from fixed perimeter fencing to interlocked access doors or light curtains that stop the machine if an operator enters a restricted area during operation.
* **Purpose:** Guarding is designed to withstand potential impacts and create a clear physical separation between personnel and machine hazards, as outlined in standards like ISO 14120 (Safety of machinery - Guards).
### 2.3 Basic Automated Detection Systems
Many modern coil wrapping machines incorporate sensors for basic anomaly detection.
* **Examples:** These might include sensors to confirm correct coil positioning before wrapping begins or simple detectors to identify obstructions in the wrapping path.
* **Action:** Upon detecting an issue, these systems typically stop the machine and alert the operator, preventing improper wraps, material jams, or minor collisions.
While these standard features provide a fundamental level of safety, more advanced systems offer significantly enhanced protection and operational benefits.
## 3. How Do Advanced Safety Technologies Elevate Operational Safety and Efficiency?
### 3.1 Integration of Smart Sensors for Enhanced Precision and Monitoring
Advanced coil wrappers often utilize sophisticated sensor networks for real-time process monitoring.
* **Capabilities:** Smart sensors (e.g., vision systems, laser scanners, ultrasonic sensors) can detect subtle irregularities like coil telescoping, edge misalignment, or inconsistencies in wrap tension. They can also monitor the status of safety components themselves.
* **Benefit:** This precise monitoring allows the control system to make micro-adjustments or initiate immediate shutdowns, preventing accidents, reducing material waste, ensuring wrap quality, and minimizing downtime caused by process errors.
### 3.2 Automated Fault Detection and Diagnostic Capabilities
Premium machines often feature integrated systems that continuously monitor machine health and diagnose potential faults.
* **Functionality:** These systems can identify issues like motor overheating, sensor malfunctions, or deviations from normal operating parameters *before* they lead to a hazardous failure or breakdown.
* **Interface:** Diagnostic information is typically displayed on an HMI (Human-Machine Interface) panel, providing clear alerts and guidance for troubleshooting, enabling proactive maintenance.
* **Value:** This predictive capability significantly enhances safety by addressing problems proactively, reduces costly emergency repairs, and extends the machine's operational lifespan.
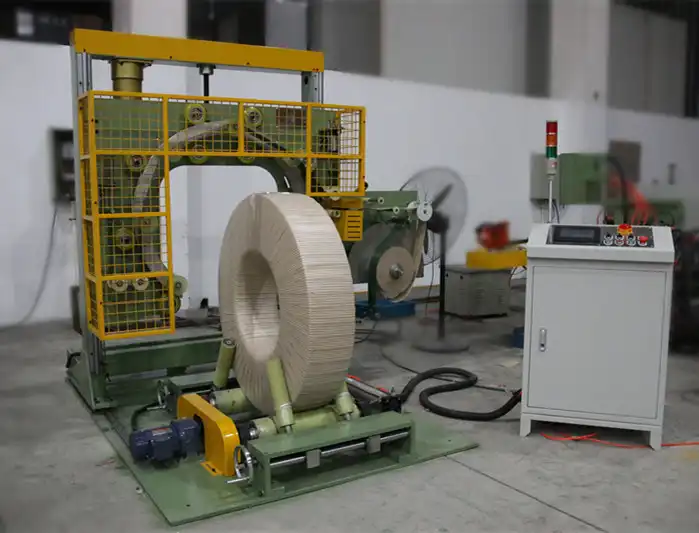
### 3.3 Boosting Operational Efficiency Through Integrated Safety
Advanced safety technologies are often designed to work seamlessly with automated processes, enhancing rather than hindering efficiency.
* **Examples:** Features like automated coil loading/unloading sequences synchronized with safety interlocks, zone-based safety systems that only stop specific parts of the machine, and remote monitoring capabilities allow operations to run smoothly and continuously while maintaining high safety standards.
* **Synergy:** By intelligently integrating safety into the workflow, businesses can achieve higher throughput, reduce manual intervention in hazardous areas, and optimize overall equipment effectiveness (OEE).
---
## 4. Are Customizable Safety Features a Worthwhile Investment?
### 4.1 Tailoring Safety Measures to Specific Operational Needs
Every operating environment has unique challenges. Customizable safety features allow businesses to address their specific risks effectively.
* **Application-Specific Needs:** For instance, facilities handling particularly heavy or unstable coils might require enhanced load securing and C-hook interlocking systems. Operations in corrosive environments might need specialized sensor enclosures and materials. High-volume lines may benefit from advanced light curtain configurations for faster, safer access.
* **Risk Assessment:** Customization should be based on a thorough risk assessment of the specific application, ensuring that safety investments are targeted where they provide the most benefit.
### 4.2 Evaluating the Long-Term Cost Benefits of Customization
While customized safety solutions might involve a higher upfront cost, they often yield substantial long-term returns.
* **ROI Factors:**
* **Reduced Accidents:** Preventing even a single serious incident can save enormous costs related to medical expenses, insurance premium hikes, legal fees, and lost productivity.
* **Minimized Downtime:** Tailored safety systems that address specific operational bottlenecks or failure points can improve uptime and reliability.
* **Enhanced Compliance:** Meeting or exceeding industry-specific safety standards can prevent fines and enhance market reputation.
* **Improved Efficiency:** Safety features designed around specific workflows can sometimes streamline processes compared to generic solutions.
### 4.3 Building Trust and Fostering a Safety-First Culture
Investing in customized, state-of-the-art safety features demonstrates a clear commitment to employee well-being.
* **Employee Morale:** Workers feel valued and protected in an environment where safety is visibly prioritized, leading to higher morale, better engagement, and reduced turnover.
* **Client Confidence:** Clients and partners recognize this commitment to operational integrity and safety, enhancing the company's reputation for reliability and responsibility.
* **Brand Image:** A strong safety record, supported by advanced and tailored equipment, becomes a competitive advantage.
---
## Conclusion: Making the Right Choice for Safety and Performance
Coil wrapping machines exhibit significant variations in their safety features, ranging from basic, essential protections to highly advanced, customizable systems integrated with smart technology. Understanding these differences—from E-stops and guarding to smart sensors and automated diagnostics—is crucial for selecting equipment that truly meets your operational needs.
Prioritizing comprehensive safety features when choosing a coil wrapping machine is not merely about compliance; it's a strategic investment. It directly contributes to protecting your workforce, minimizing costly downtime, ensuring regulatory adherence, and ultimately boosting operational efficiency and reliability. By carefully evaluating the safety technologies available, you can secure a foundation for safer, more productive, and sustainable operations.