
In the demanding world of steel manufacturing, precision handling, packaging, and logistics are paramount. However, standard steel coil packing systems often struggle to meet the unique operational demands and specific challenges faced by individual producers. This is where customization transforms steel coil packing lines from a mere necessity into a strategic asset. Imagine a system meticulously engineered not just for packaging, but for significantly boosting the overall efficiency and throughput of your entire production line. By adopting tailored solutions, steel manufacturers can redefine productivity benchmarks and secure a distinct competitive advantage.
At the core of customized steel coil packing lines lie precision engineering, adaptability to specific needs, and innovative technology integration. By leveraging these elements, manufacturers can effectively streamline complex operations, drastically reduce costly downtime, enhance the quality and protection of their steel products, and optimize resource utilization. The outcome is a packing system that doesn’t just perform its function—it actively contributes to your operational excellence and bottom line.
Modern industries thrive on differentiation and efficiency. Customization empowers steel manufacturers to overcome unique hurdles, whether it involves packaging delicate surface-sensitive materials, achieving high-volume production quotas, ensuring robust protection for transport, or minimizing material waste. But what does the customization process entail, and how exactly does it translate into tangible improvements in operational efficiency? Let's explore the key aspects.
[Claim: Customized steel coil packing lines are pivotal for enhancing operational efficiency by optimizing production workflows, reducing resource wastage, improving safety, and precisely meeting specific industry demands.]
1. Why Do Steel Manufacturers Need Customized Packing Lines?
1.1 Understanding Operational Bottlenecks in Steel Coil Handling
In the high-pressure environment of steel manufacturing, operational bottlenecks can trigger cascading delays, inflate production costs, and ultimately impact profitability. Standard, off-the-shelf steel coil packing lines, while functional for generic applications, often fail to adequately address the specific nuances of individual production lines. Common issues such as significant variations in coil dimensions (width, diameter, weight), handling requirements for sensitive coatings (e.g., galvanized, painted), integration with existing plant logistics, and managing irregular production schedules can severely disrupt operations if the packing line isn't designed for flexibility and precision.
Customization provides the means to meticulously identify and eliminate these critical bottlenecks. By tailoring the packing line system—from coil transport and centering to wrapping, strapping, and labeling—to fit exact operational requirements, businesses can guarantee smoother, more consistent workflows with significantly fewer disruptions. Whether it involves incorporating automated coil tilting mechanisms, integrating precise weighing systems, or adding specialized edge protectors, customized solutions bridge the crucial gap between generic equipment capabilities and real-world steel coil handling challenges.
1.2 The Role of Customization in Addressing Specific Steel Packaging Challenges
Effective customization goes beyond simply adding features; it involves designing integrated solutions that work harmoniously with your existing production processes and address your most pressing challenges. For instance, manufacturers dealing with exceptionally large, heavy, or narrow slit steel coils often find standard packing lines inadequate or inefficient. Tailored systems can incorporate heavy-duty conveyors, adjustable wrapping orbits, or specialized strapping heads designed to handle these non-standard dimensions safely and without compromising production speed.
Furthermore, certain steel products, like those with Class A surfaces for the automotive industry or specialized alloys, demand specific protective layers (e.g., VCI film, stretch wrap, paper wrap) applied with precision to prevent damage during handling, storage, and transit. A customized packing line can integrate these multi-stage wrapping or layering processes seamlessly into the automated sequence, eliminating the need for time-consuming and potentially inconsistent manual operations. By consolidating these functions, businesses save valuable time, reduce labor costs, minimize material handling, and ensure consistent product quality and protection.
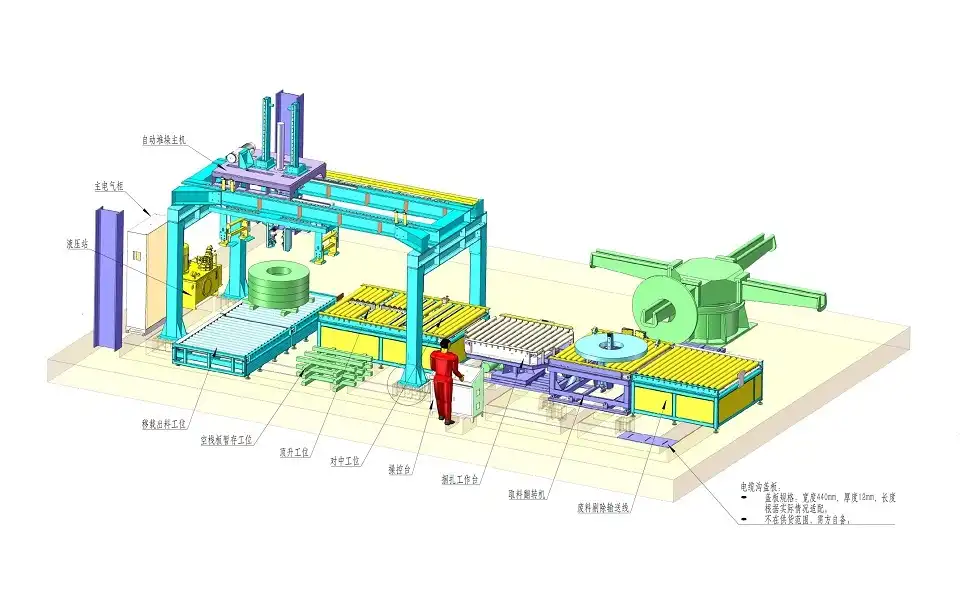
1.3 Examples of Industry-Specific Customization Features
Different segments within the steel industry benefit from specific customization features tailored to their unique operational needs and product requirements:
- Automotive Steel Producers: Often require high-speed packing lines capable of handling delicate, surface-critical coated steel coils with minimal contact and abrasion. Customizations might include non-contact centering devices, specialized wrapping materials, and integrated surface inspection systems.
- Construction Steel Suppliers: May prioritize robust, weather-resistant packaging suitable for long-term outdoor storage. Customizations could involve multi-layer wrapping with UV-resistant films, circumferential and radial strapping for package stability, and automated stacking systems.
- Export-Focused Manufacturers: Benefit from packing lines incorporating automated palletization, container loading calculations, and labeling systems compliant with international shipping standards (e.g., ISPM 15 compliance for wood pallets, specific barcode formats).
- Service Centers Handling Slit Coils: Need highly flexible lines capable of efficiently packaging numerous coils of varying widths and diameters. Features like automated coil separation, eye-to-sky or eye-to-wall orientation changes, and rapid strapping cycles are crucial.
These examples clearly illustrate how strategic customization directly aligns the packing line's capabilities with the specific operational goals and market demands of different sectors, leading to more efficient, reliable, and cost-effective production.
2. How Does Customization Improve Production Speed and Accuracy in Coil Packaging?
2.1 Streamlining Workflow with Tailored Packaging Solutions
A primary advantage of customizing your steel coil packing line is the profound ability to streamline the entire packaging workflow. Standard, inflexible lines often force businesses to adapt their internal processes and material flow *to* the limitations of the equipment. With customized solutions, this dynamic is reversed—the equipment is meticulously designed and configured to integrate seamlessly *with* the existing or optimized workflow of the business.
Consider a scenario where a production line processes steel coils of widely varying widths and diameters sequentially. A tailored packing line can incorporate dynamic adjustments, such as sensors that automatically detect incoming coil dimensions and signal the wrapping machine, strapping heads, and conveyors to adjust their parameters accordingly—all without manual intervention. This automated adaptability eliminates bottlenecks associated with manual setup changes, significantly accelerates the overall packaging cycle time, and maintains high levels of accuracy and consistency.
2.2 Reducing Downtime Through Advanced Automation and Diagnostics
Automation is a fundamental pillar of operational efficiency, and customization amplifies its positive impact exponentially. Tailored steel coil packing lines can integrate sophisticated automation features well beyond basic functions. Examples include predictive maintenance alerts based on sensor data (monitoring vibration, temperature, cycle counts), real-time operational monitoring dashboards accessible remotely, and advanced error detection and self-correction systems. These technologies work proactively to minimize both planned and unplanned downtime by addressing potential issues before they escalate into major failures.
For example, a customized line equipped with AI-driven diagnostic tools can analyze performance data to identify subtle signs of wear and tear on critical components like drive motors or strapping head parts. It can then automatically notify maintenance technicians well in advance, allowing for scheduled preventative maintenance during non-peak hours. This proactive approach drastically reduces unexpected production halts, ensures manufacturing schedules remain on track, and maximizes overall equipment effectiveness (OEE) and throughput.
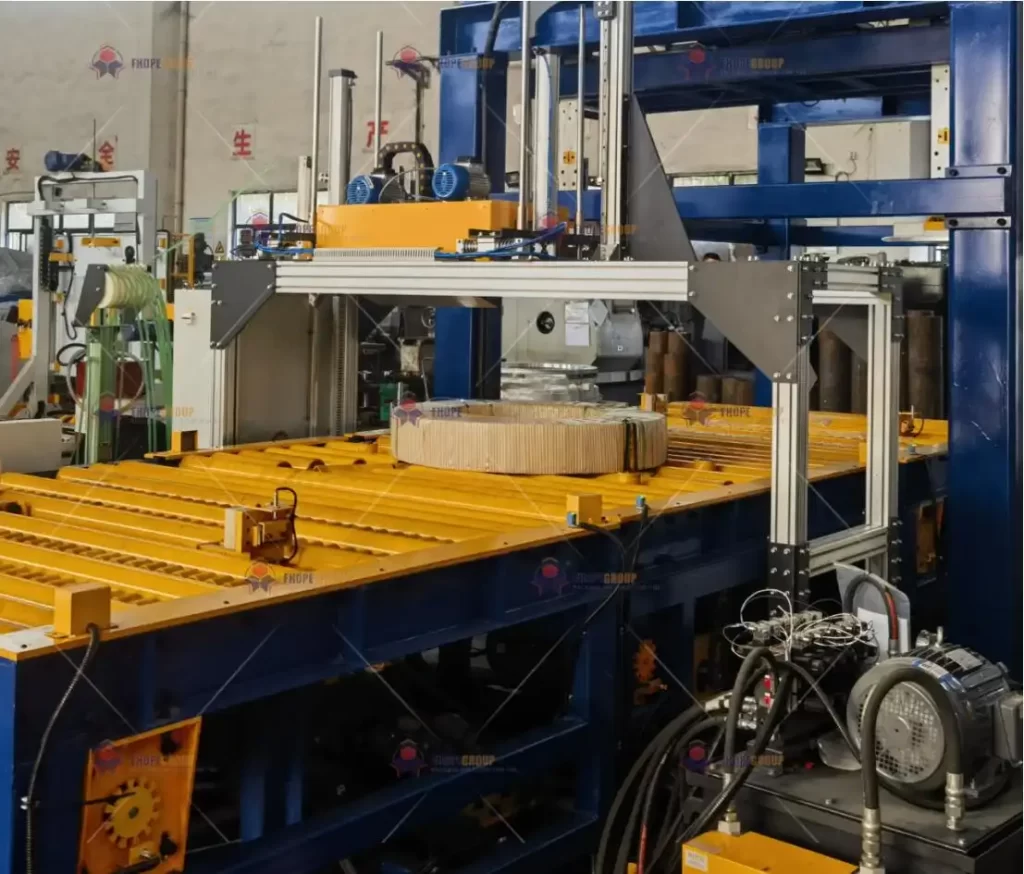
2.3 The Integration of Precision Technology for Optimal Packaging
In steel manufacturing and processing, accuracy is not merely desirable—it is absolutely essential for maintaining product quality, ensuring package integrity, and meeting customer specifications. Customized packing lines provide the platform to integrate cutting-edge precision technologies tailored to the specific needs of steel coil handling. This can include advanced optical sensors for precise coil positioning, servo-driven robotic arms for accurate placement of labels or edge protectors, laser-guided systems for consistent wrapping overlap, and load cells for verified weight documentation. These systems not only prevent costly errors but also guarantee repeatable consistency, a crucial factor when dealing with high-value or surface-sensitive steel materials.
By integrating the right precision technology, manufacturers can achieve tighter packaging tolerances, significantly enhance final product quality presentation, and reduce material waste associated with rework or damaged goods. For instance, a system that precisely controls the tension and overlap of stretch film applied to each coil ensures uniform containment force and optimal protection, minimizing the risk of coil shifting or damage during subsequent transport and handling.
3. What Role Does Customization Play in Reducing Waste and Enhancing Sustainability?
3.1 Addressing Resource Inefficiencies in Packaging Materials
Standardized, non-optimized packing lines often contribute significantly to material wastage due to their inherent one-size-fits-all design philosophy. Applying the same amount or type of wrapping material (like stretch film, VCI paper, or plastic strapping) to coils of varying sizes inevitably leads to inefficiencies. Excessive use of wrapping materials, poorly calibrated strapping tensions leading to breakage, or using oversized packaging dimensions can escalate material consumption and costs rapidly. Customization directly tackles these inefficiencies by optimizing resource usage based on actual needs.
For example, tailored systems can precisely measure the dimensions (or receive data from upstream systems) of each individual coil and dynamically adjust the wrapping program to apply only the necessary amount of film with optimal tension and placement. Similarly, strapping systems can be configured for the specific coil weight and handling requirements, preventing both under-strapping (risk of package failure) and over-strapping (wasted material). This optimized material usage not only drastically reduces packaging waste but also yields substantial cost savings. In the steel industry, where profit margins can be tight, these efficiencies have a significant positive impact on the bottom line.
3.2 Incorporating Eco-Friendly Solutions and Energy Efficiency
Environmental sustainability is no longer a niche concern but a core business imperative across industries, including steel manufacturing. Customization provides a vital pathway for businesses to integrate eco-friendly features and practices directly into their packing line operations. This can range from designing the system to effectively utilize biodegradable or recyclable wrapping materials, optimizing motor usage and incorporating energy-saving modes during idle periods, to employing reusable dunnage components or integrating waste collection systems. A customized solution actively supports greener manufacturing practices.
For instance, some forward-thinking manufacturers are incorporating energy-efficient servo motors instead of traditional hydraulic systems, utilizing variable frequency drives (VFDs) on conveyors, or even exploring options for integrating with plant-wide energy monitoring systems. By actively reducing their operational carbon footprint through tailored equipment design, these businesses not only enhance their corporate social responsibility image but also align with increasingly stringent environmental regulations and meet the growing expectations of environmentally conscious customers and stakeholders.
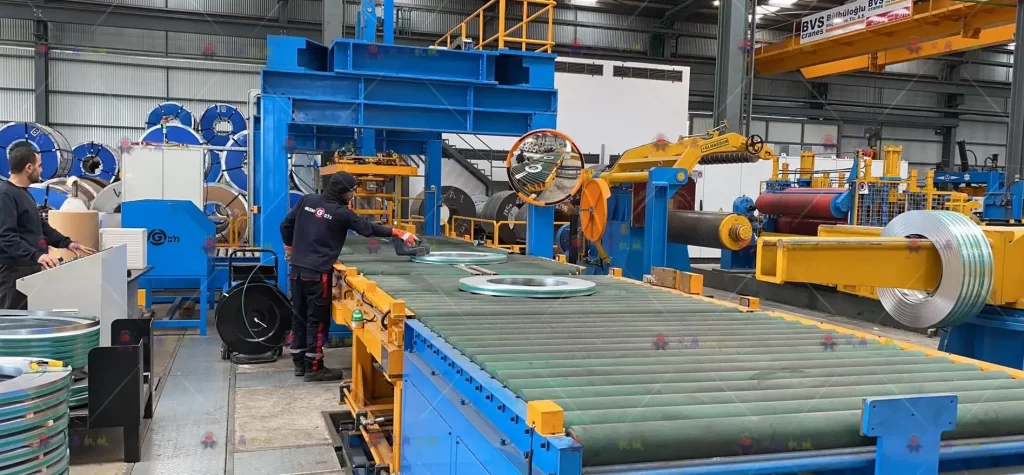
3.3 The Combined Financial and Environmental Impact
The positive impact of customization extends beyond just operational efficiency—it delivers significant environmental and financial benefits concurrently. By minimizing packaging material waste, manufacturers directly reduce their contribution to landfills and cut down on material procurement and waste disposal costs. Furthermore, incorporating automation and precision controls reduces the likelihood of packaging errors that could lead to product damage during transit, ensuring that valuable resources invested in production are not wasted due to inadequate protection.
The financial advantages are compelling and multifaceted. Businesses that demonstrate a commitment to sustainability through customized, efficient operations often find themselves better positioned to attract investment, potentially qualify for green energy incentives or tax credits, and build stronger brand loyalty among customers who prioritize environmental responsibility. Reduced energy consumption and material usage translate directly into lower operating expenses, further boosting profitability.
4. How Does Customization Impact Employee Productivity and Safety?
4.1 Simplifying Complex Processes for Operators
Customized steel coil packing lines are designed with the end-user in mind, simplifying complex workflows and making them significantly easier and more intuitive for employees to operate and manage. Systems featuring user-friendly Human-Machine Interfaces (HMIs) with clear graphical displays, pre-set packaging recipes for different coil types, and highly automated processes dramatically reduce the need for constant manual intervention, complex adjustments, or troubleshooting.
Consider a packing line integrated with intuitive touch-screen controls that provide real-time performance data, visual alerts for material replenishment (e.g., film roll change), and step-by-step guidance for operation or fault recovery. This level of customization allows employees to easily monitor operations, make swift adjustments when necessary, and quickly learn the system, minimizing training time and enhancing overall operator productivity. As a result, personnel can focus their attention on higher-level monitoring, quality assurance, and other value-adding activities rather than being bogged down by cumbersome equipment operation.
4.2 Minimizing Workplace Hazards through Ergonomics and Automation
Safety is an absolute, non-negotiable priority in any steel manufacturing or processing environment, particularly around heavy coil handling and automated machinery. Customization plays a critical role in enhancing workplace safety by allowing for the integration of advanced safety features specifically designed for the application. This includes robust physical guarding, light curtains, emergency stop systems strategically placed for easy access, automated coil loading/unloading mechanisms to eliminate manual lifting, and interlocking safety gates. These features work together to mitigate the inherent risks associated with handling multi-ton steel coils and operating high-speed automated packaging machinery.
For instance, incorporating an automated coil loading system (like a walking beam conveyor or tilter) completely removes the need for operators to manually push or lift heavy coils into position, drastically reducing the risk of musculoskeletal injuries. Similarly, built-in sensors integrated into the control system can detect abnormal conditions (like a misplaced coil or an obstruction) and automatically halt operations safely before an accident or equipment damage can occur. Customization allows safety to be engineered into the system from the ground up.
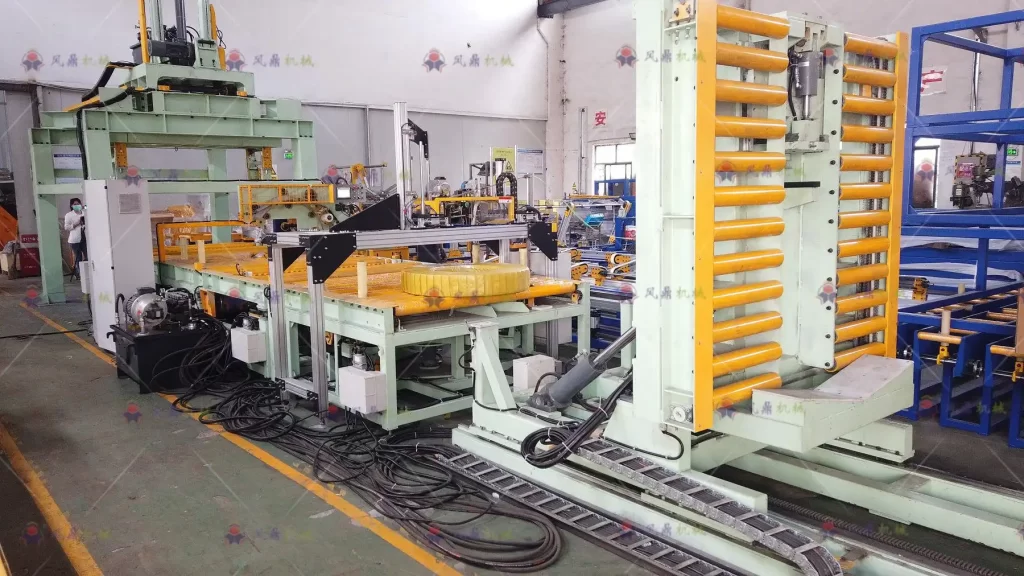
4.3 Boosting Workforce Morale and Engagement
Providing employees with a safer, more ergonomic, and efficient work environment has a direct and positive impact on workforce morale and job satisfaction. Customization, by simplifying tasks, reducing physical strain, and minimizing safety risks, demonstrates a company's tangible commitment to the well-being of its employees. When workers feel safer, more valued, and equipped with tools that help them perform their jobs effectively, their engagement levels, attention to detail, and overall productivity naturally increase.
Furthermore, a reduction in workplace incidents and accidents leads to fewer lost workdays, lower workers' compensation insurance premiums, and less operational disruption, all of which contribute positively to the overall operational efficiency and financial health of the business. Investing in customized, safe, and efficient equipment is an investment in your most valuable asset – your people.
Conclusion: The Strategic Imperative of Customized Steel Coil Packing
In today's competitive steel industry landscape, customization in steel coil packing lines has evolved from a potential upgrade to a strategic necessity. Businesses aiming to optimize operational efficiency, minimize costly waste, enhance product protection, and ensure the highest standards of workplace safety must look beyond standard solutions. Tailored packing lines, engineered to address specific production challenges, integrate seamlessly with workflows, and leverage advanced automation and precision technology, deliver unparalleled value across multiple facets of the operation.
[Claim: Investing strategically in customized steel coil packing lines empowers steel manufacturers and service centers to achieve significant gains in operational efficiency, advance their sustainability goals, reduce operational risks, and ultimately foster a safer, more productive, and more profitable work environment.]

Get Your Best Solution !