I often see maintenance teams at steel mills worry about how to handle large coils for inspection or repairs. They want a device that can simplify flipping and reduce damage (30 words).
A custom mechanical upender helps steel mills rotate heavy coils or equipment from horizontal to vertical with less strain. I often rely on this device to allow thorough inspections, faster maintenance, and safer coil handling. It improves workflow by reducing manual lifts and providing stable support during regular mechanical checks.
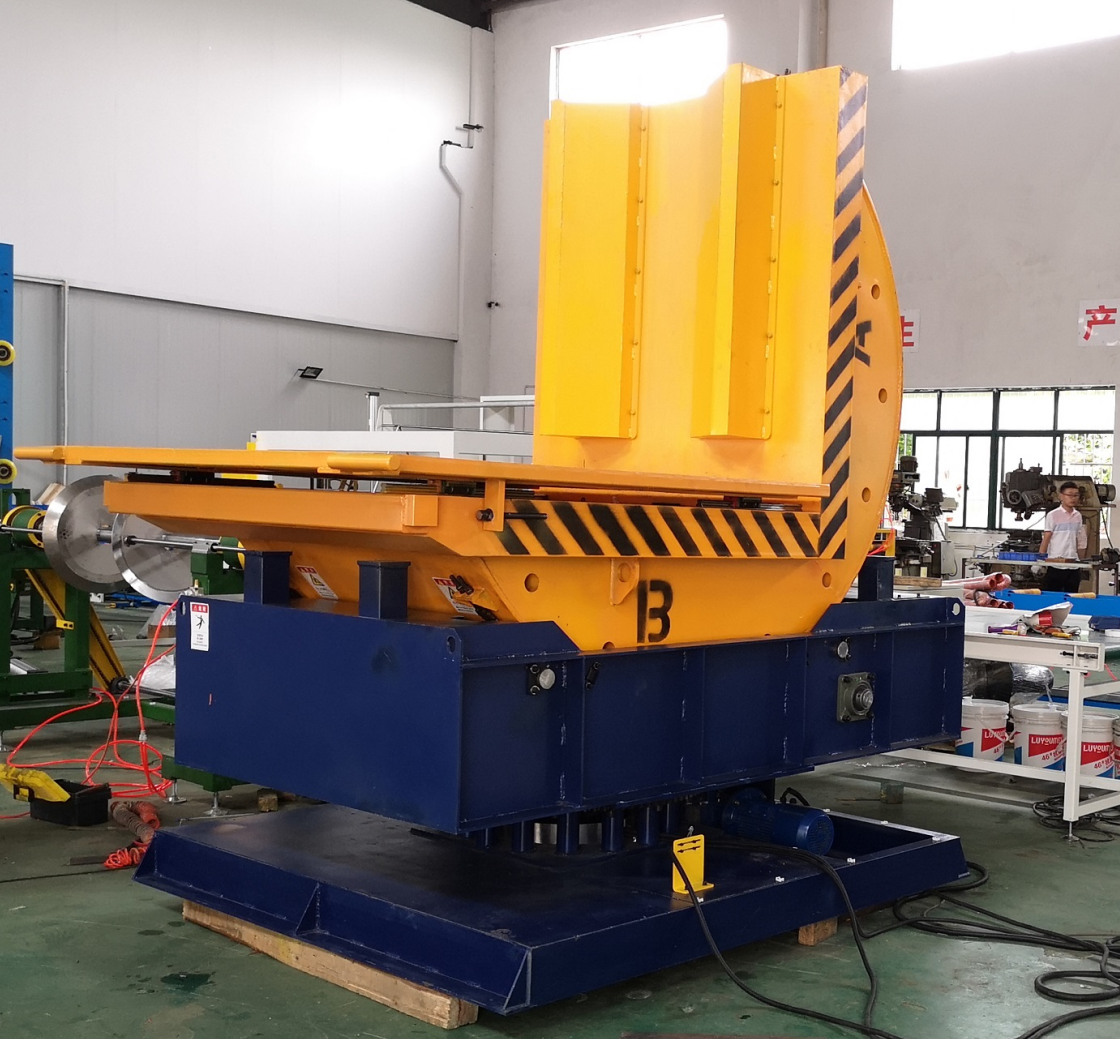
"Mechnical upender in action")
I have worked with many steel mills that find upenders essential for maintenance tasks. They use them to flip large rolls or other equipment for cleaning, welding, and internal repairs. Let me explain more about how this device can transform your maintenance procedures and help your team work safely and efficiently.
Why Do Steel Mills Rely on Custom Upenders?
I recall a plant manager who struggled to lift heavy steel rolls for crucial inspections. He needed a custom upender that offered stability and saved time during daily maintenance tasks .
Steel mills rely on custom upenders for flipping and orienting heavy coils. I have seen how these devices lower the risk of bending or warping components. They also simplify retooling and part replacement. By stabilizing loads, they help maintenance teams perform internal checks, welding, or cleaning tasks without major disruptions.
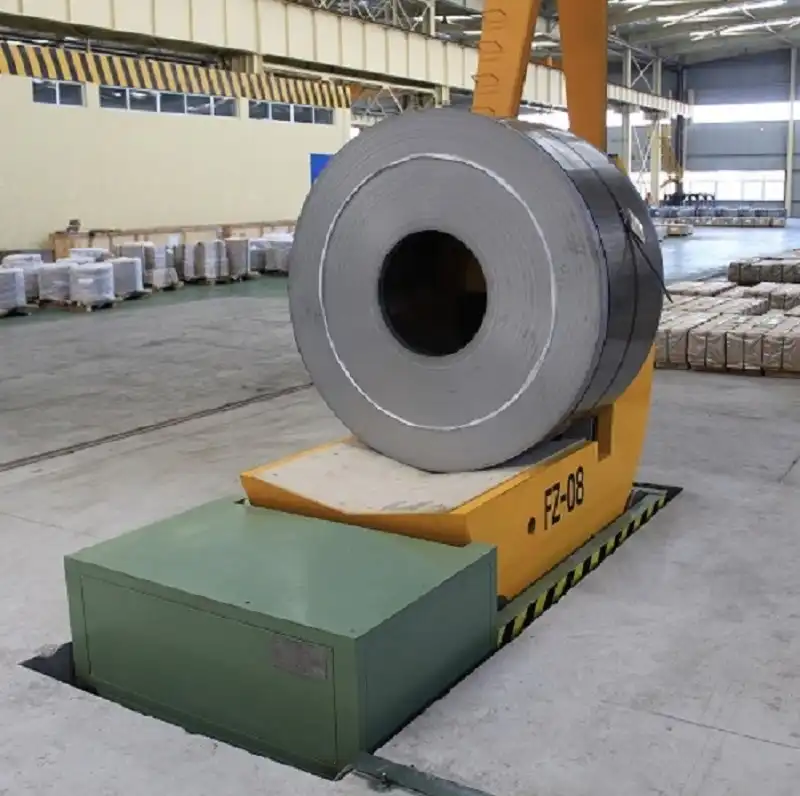
"Steel Coil Upending for Maintenance")
The Mechanics Behind a Custom Upender
A custom mechanical upender uses a rotating platform or cradle to shift a load from horizontal to vertical or vice versa. I think of it as a controlled tipping process, designed to keep steel coils, rolls, or other cylindrical products stable. Unlike makeshift solutions that use cranes or forklifts at awkward angles, a custom upender has a stable frame that keeps the product in place during the rotation. That reduces the risk of slippage and protects the product’s outer surface.
I also see these upenders built with heavy-duty motors and gear systems to support different load capacities. Some upenders can handle smaller coils that weigh a few hundred kilograms, while others can tackle massive rolls that weigh several tons. The key is that the design is customized. Different steel mills have different coil dimensions, storage requirements, and production speeds. A tailored upender addresses those specific factors by offering a cradle width that fits the coil diameter, or a rotation angle that makes it easier for workers to do internal checks.
Feature | Benefit |
---|---|
Tailored Cradle Size | Accommodates various coil diameters |
Controlled Rotation Speed | Lowers mechanical stress |
Safety Interlocks | Prevents accidental tipping |
Heavy-Duty Gears | Handles large load capacities |
Ergonomic Controls | Simplifies operator workflow |
I remember talking to David, a purchaser at a mid-sized company. He wanted an upender that could handle steel coils as well as aluminum rolls with different diameters. Instead of purchasing two separate units, he asked for a variable cradle design and an adjustable rotation speed. That solution helped his team run maintenance tasks on a range of products without risking damage from makeshift lifting methods. It also allowed them to do more thorough checks on each coil’s interior. They could rotate the coil slowly and inspect all sides for cracks or wear.
I have seen how a custom upender boosts worker morale. Operators dislike lifting heavy parts with tools that are not built for that job. They feel safer when the machine has a stable design with clear controls. In the long term, the steel mill experiences fewer injuries and less downtime. When workers trust their equipment, they work faster and spot problems earlier. This synergy between safety and productivity is what makes custom upenders vital in a maintenance setting. (266 words)
How Does Upending Improve Safety During Repairs?
I often talk to line workers who feel nervous about rotating bulky rolls with cranes or manual rigs. They fear sudden slips or collisions that can injure staff and damage equipment.
An upender eases these worries by guiding the coil through a stable axis of rotation. I see fewer dropped loads, reduced operator strain, and faster access to repair points. This ensures a safer workspace (50 words).
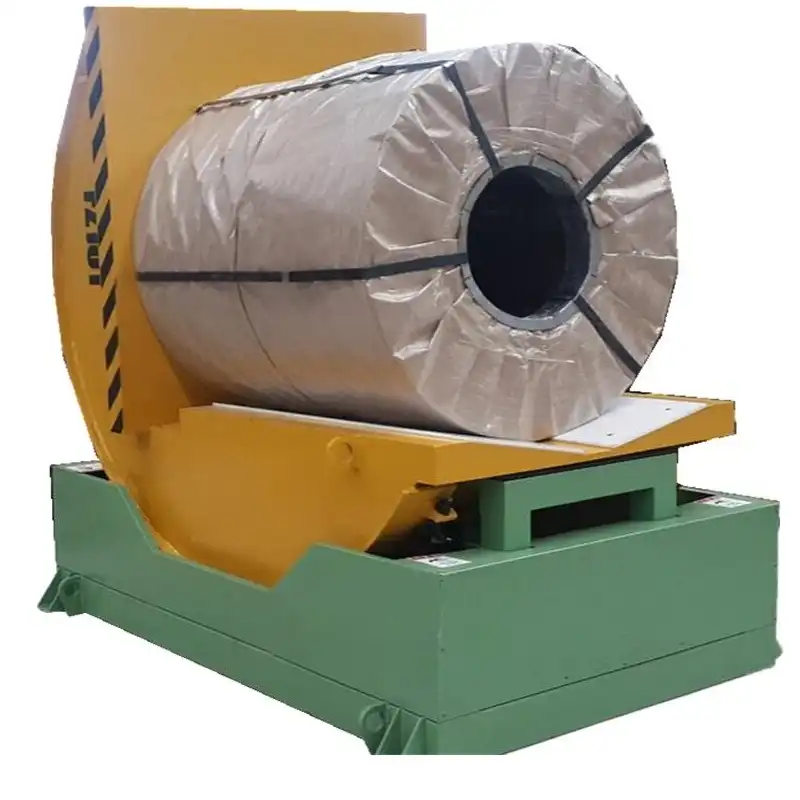
"title")
Reducing Workplace Hazards
I believe that a custom upender lowers workplace hazards in multiple ways. It removes the guesswork of flipping heavy coils and eliminates reliance on forklift forks or crane hooks for partial lifts. Instead, the upender’s cradle embraces the coil so it does not slip out. In a busy steel mill, this matters a lot because the floors can get slick with dust or small debris. A small jolt could make a coil shift dangerously. With an upender, the risk of coil rolling out of place drops significantly.
I think about the times I have witnessed operators guide coils with ropes or boards. That method might work on a smaller scale, but it is dangerous at an industrial level. Even well-trained teams can make mistakes if they rely on improvised methods. A slip or unexpected shift can cause major injuries and property damage. A robust upender solves this by ensuring that every rotation follows a consistent, calculated path.
Addressing Physical Strain
Maintenance workers often need to reach different parts of a coil to check for cracks, corrosion, or buildup. When the coil remains in a single orientation, they may twist their bodies or climb onto risky platforms to see all sides. This leads to back strain or repetitive stress injuries over time. An upender changes that dynamic. It rotates the coil so the team can access key areas while standing in a safer, more ergonomic position. I see less fatigue and fewer accidents when workers do not need to hunch or stretch in uncomfortable ways.
Safety Factor | How Upender Helps |
---|---|
Coil Stability | Secures coil in a cradle |
Risk of Slips | Moves coil smoothly, lowering sudden shifts |
Operator Strain | Positions coil for easy inspection |
Floor Congestion | Frees up forklift and crane usage |
Speed of Maintenance | Speeds up checks without shortcuts |
Enhanced Productivity and Team Morale
I find that safety goes hand in hand with productivity. If workers feel confident that the upender will hold the load securely, they can concentrate on their primary tasks. They will not be distracted by fear or the need to do endless checks. By removing these stress points, the team can do maintenance faster. That means the steel mill can return the coil to production sooner, reducing downtime. It also helps create a positive feedback loop: a safer environment means happier staff and fewer delays, which leads to better overall performance. I have seen these benefits play out in multiple operations.
I also note that modern upenders often come with sensors or automated stop functions. That means the device will pause if it detects an obstruction or if the load is not seated correctly. This is another layer of protection that a crane or forklift cannot always provide. Over time, these features build trust between operators and machines, and that trust is key to a productive maintenance workflow. (260 words)
When Is a Customized Upender Most Valuable?
I spoke with a senior engineer who tried to use a standard upender for a non-standard coil shape. The mismatch caused surface damage and frequent machine adjustments (30 words).
A customized upender shines when your steel mill handles unique coil sizes or specialized machinery. I have seen it reduce downtime and limit reconfiguration needs by tailoring rotation angles, cradle widths, and weight capacities (50 words).
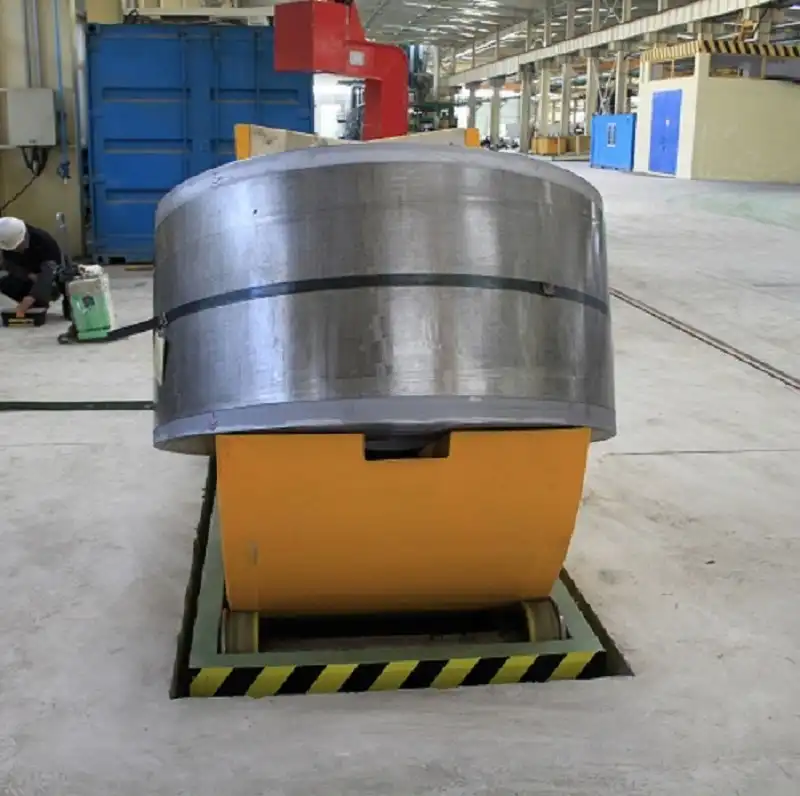
"title")
Designing an Upender for Special Maintenance Needs
Some steel mills run standard coil sizes all day, but others handle a mix of custom alloys, different thicknesses, or odd shapes. I realize that one-size-fits-all solutions often lead to inefficiencies, especially for mills that produce coils in short runs or require frequent changeovers. A customized upender can address those challenges by letting you specify key parameters. You can choose the rotation speed, the type of clamp, and the angle of tilt. That control means the device can adapt to different coil diameters without risking misalignment or stress on the coil edges.
Key Customization Options
Custom Feature | Benefit |
---|---|
Adjustable Cradle Width | Fits multiple coil diameters |
Variable Tilt Angles | Fine-tunes orientation for detailed inspections |
Multi-Speed Rotation | Adapts speed to coil weight or operator needs |
Enhanced Safety Sensors | Detects anomalies and halts rotation early |
Remote Control Units | Allows safe operation from a distance |
I recall advising a client who processes specialty steel for aerospace components. Their coils were much narrower but denser than typical automotive coils. A standard upender had trouble gripping the narrower coil securely. The coil rattled within the cradle and created tiny surface abrasions. We fixed this by adding adjustable side supports that conformed to the narrower width, as well as extra padding in the cradle to protect delicate surfaces. We also installed a slower rotation setting to accommodate the heavier weight. That approach solved multiple problems at once.
Practical Tips for Customization
I usually start by gathering data on coil dimensions, weight ranges, and specific maintenance steps. Sometimes, the coil needs to be rotated in smaller increments so the operator can check hidden seams. Other times, we want a quick 90-degree tilt so we can do fast cleaning or part replacement. Once I have that data, I work closely with the engineering team to pick the right drive mechanism, decide on motor capacity, and choose protective materials for contact points.
I also factor in future expansion. Steel mills often grow or change product lines. A good custom upender can scale with those changes. For instance, it could handle a bigger diameter range by swapping out cradle inserts, or it might have a modular design that lets you upgrade the motor for heavier loads. I see this as a better long-term investment because you will not need to buy a new upender every time coil dimensions change.
A customized upender also helps with quality control. If I can place the coil in different orientations and examine it thoroughly, I can catch potential flaws before they become bigger problems. That is especially important if the coil will go on to be formed, welded, or coated. A small crack can expand during these processes if not caught early. With a device that fits the coil perfectly, we can see every nook without wrestling with half-baked lifting solutions. (310 words)
Conclusion
I believe custom upenders transform maintenance at steel mills by speeding up inspections, reducing handling risks, and accommodating unique coil shapes. They help me create a safer, more efficient workflow that meets every production demand (41 words).