How Coil Slitters improving Competitive Edge in the Digital Age
Advanced technologies in integrated slitting and packing systems, coupled with Enterprise Resource Planning (ERP) solutions, are revolutionizing the coil processing industry. These innovations enable manufacturers to enhance their competitive edge by simplifying intricate workflows and providing unprecedented control over their operations. Such integrated systems offer valuable insights into manufacturing processes and inventory management through comprehensive tracking of product attributes, from raw material to finished goods.
A. Advancements in Coil Slitting
The coil slitting sector has undergone remarkable transformation in recent years, driven by evolving market demands and technological progress. Modern coils are more substantial, often featuring wider widths and thicker gauges, necessitating equipment upgrades to handle increased gauges and higher-strength materials. This shift has prompted a wave of investment in cutting-edge slitting lines capable of processing these advanced materials with greater precision and efficiency.
Industry leaders are leveraging state-of-the-art technologies to optimize their operations, incorporating features such as automated blade positioning, real-time thickness monitoring, and advanced tension control systems. These innovations not only improve product quality but also significantly reduce setup times and material waste.
Key automated functions now available in modern slitting operations include:
- Real-time order tracking: Providing instant visibility into order status and progress
- Dynamic production scheduling: Optimizing machine utilization and minimizing downtime
- Smart coil allocation: Ensuring the most efficient use of raw materials
- Seamless multi-facility coordination: Enabling smooth operations across multiple production sites
B. Evolution in Coil Packing
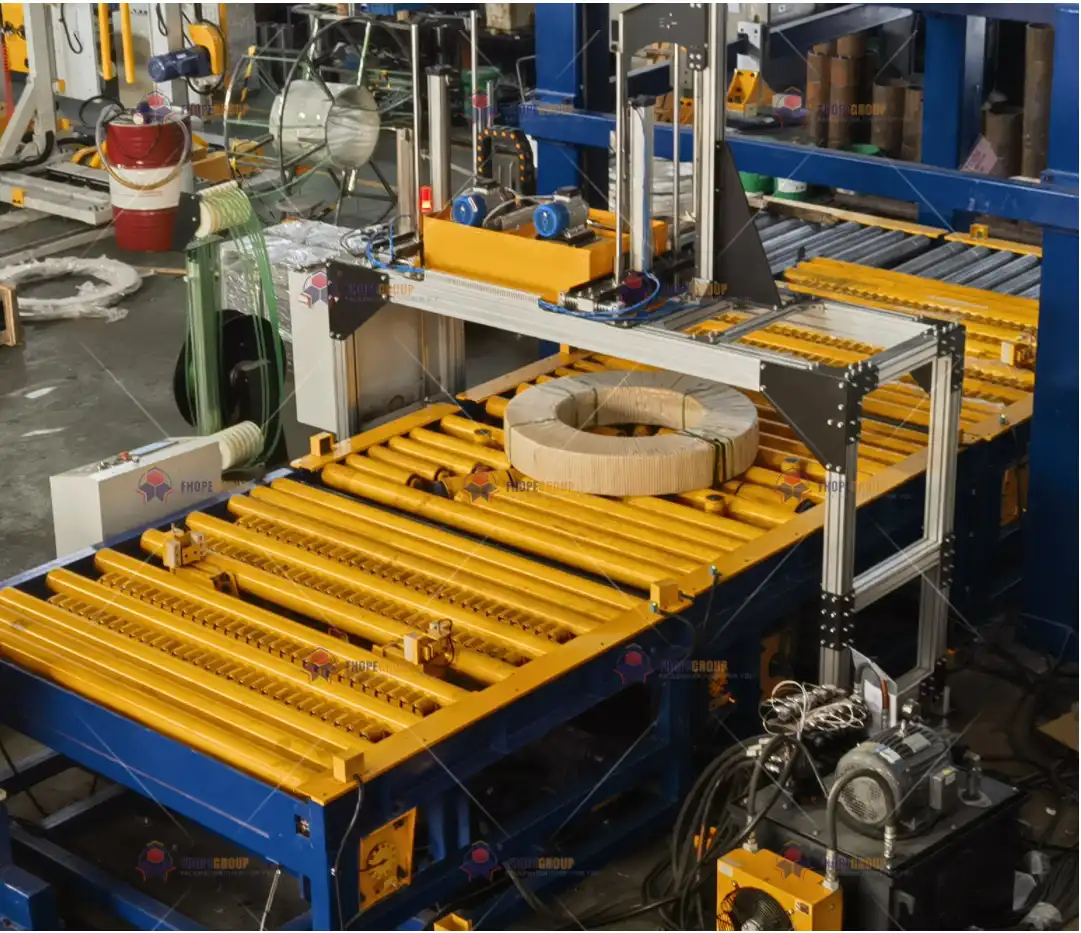
Coil packing lines have become integral to efficient slitting operations, evolving from a manual, labor-intensive process to a highly automated and sophisticated system. Automation in packing processes significantly reduces labor costs, enabling a streamlined workflow from slitting to warehouse automation. This integration has dramatically improved throughput and reduced the risk of product damage during handling.
Increasingly rigorous packaging standards demand superior protection and advanced materials, driving the adoption of sophisticated packing solutions. These may include automated strapping systems, robotic palletizers, and advanced wrapping technologies that ensure coils are securely packaged for transport while minimizing material usage.
Progressive companies are implementing cutting-edge packing technologies to enhance operational efficiency and meet the exacting requirements of their customers. These systems often incorporate smart sensors and vision systems to ensure packaging quality and consistency.
Automated capabilities in modern packing systems include:
- Continuous quality assurance monitoring: Ensuring each package meets specified standards
- Intelligent packing sequence optimization: Maximizing efficiency in the packing process
- Precise allocation of packing materials: Reducing waste and optimizing material usage
- Coordinated management of multi-location packing operations: Ensuring consistency across different facilities
C. Maximizing Profitability
In today’s fiercely competitive landscape, a cutting-edge ERP system is indispensable for precise cost and margin analysis. These systems go beyond basic accounting functions, integrating data from every aspect of the operation to provide a holistic view of the business.
ERP solutions facilitate continuous performance evaluation and identify opportunities for operational enhancements. By analyzing data on material usage, machine performance, labor efficiency, and quality metrics, companies can make data-driven decisions to improve their bottom line.
Tailored ERP platforms empower coil processors to:
- Conduct granular margin analysis: Understanding profitability at the product, customer, and order level
- Detect pricing anomalies: Quickly identifying and addressing underpriced products or services
- Identify underperforming production lines or external processors: Pinpointing areas for improvement or reassessment
These capabilities allow companies to respond quickly to market changes, optimize their product mix, and make informed strategic decisions about equipment investments and capacity planning.
D. Customized Software Solutions
Bespoke ERP solutions designed for the coil processing industry drive improvements in productivity, customer service, and overall business performance. These comprehensive systems manage diverse aspects of operations, from production monitoring to advanced customization capabilities.
Key features of these specialized systems often include:
- Material traceability: Tracking the entire lifecycle of a coil from receipt to shipment
- Advanced inventory management: Optimizing stock levels and reducing carrying costs
- Quality control integration: Ensuring adherence to customer specifications and industry standards
- Customer relationship management: Improving communication and service levels
- Business intelligence tools: Providing actionable insights through data analytics and reporting
By integrating these various aspects of the business, coil processors can achieve a level of operational excellence that was previously unattainable. The result is a more agile, efficient, and profitable operation that is well-positioned to meet the challenges of an ever-evolving market.
As the industry continues to advance, those companies that embrace these technological innovations will find themselves at a significant advantage, able to offer higher quality products, faster turnaround times, and more competitive pricing. The future of coil processing lies in the intelligent integration of advanced machinery, automated packing systems, and sophisticated ERP solutions, creating a seamless and highly efficient production environment.