How to Select the Optimal Coil Wrapping Machine for Your Steel Coils
In the demanding steel industry, where efficient handling and product protection are paramount, selecting the right **steel coil wrapping machine** is a critical decision. This choice extends beyond simply wrapping coils; it's fundamental to safeguarding valuable products, boosting operational efficiency, and controlling costs. Every factor, from wrapping material consumption to maintenance schedules, significantly impacts your bottom line. Therefore, choosing equipment that meets both current operational demands and future growth is essential. An unsuitable machine can lead to higher operational costs and potential product damage, whereas the right investment ensures security, efficiency, and long-term value.
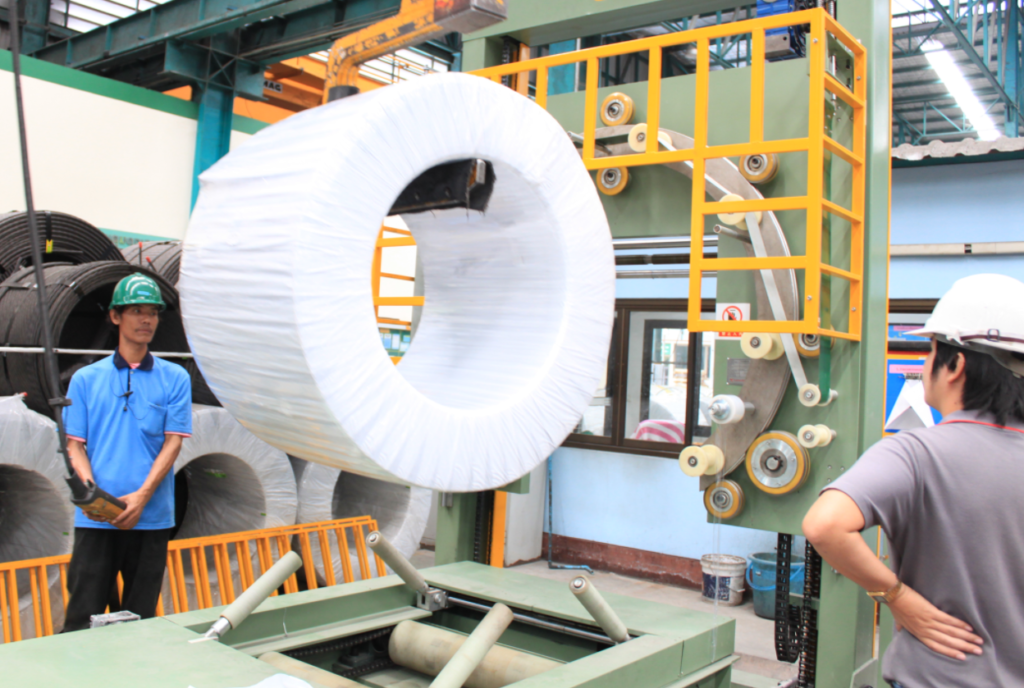
When evaluating a **coil wrapping machine**, numerous factors require careful consideration. Key parameters include:
- Load capacity
- Wrapping speed and control
- Adaptability for various coil sizes (ID, OD, width)
- Compatibility with different wrapping materials (e.g., stretch film, VCI paper)
- Maintenance requirements and ease of use
Understanding these technical specifications provides clarity on essential versus optional features. Armed with the right information, you can make an informed decision that supports your business objectives, minimizes operational risks, and contributes to a smooth, efficient packaging workflow.
Transitioning to automated coil wrapping might seem like a significant undertaking, particularly when balancing initial investment against long-term benefits like reduced labor costs and material savings. However, with a clear assessment of your requirements and the available technology, you can identify a machine that not only fulfills current needs but also possesses the flexibility to adapt to future industry changes and business growth.
[claim] Selecting the ideal **coil wrapping machine** necessitates a thorough understanding of core features, a precise assessment of operational needs, and strategic consideration for future scalability. This investment transcends mere equipment acquisition; it's a commitment to sustained productivity, reduced operational costs, and dependable protection for high-value steel coils.
1. Essential Features to Evaluate in a Steel Coil Wrapping Machine
1.1. Robust Construction and Load Capacity
A primary consideration is the machine's structural integrity and load-bearing capability. The steel industry environment demands heavy-duty equipment. A reliable coil wrapping machine must be constructed from high-quality materials (e.g., heavy-gauge steel frames) to withstand continuous operation and support the significant weight of steel coils without compromising performance or safety. Ensure the specified load capacity comfortably exceeds your heaviest coil weight.
Beyond just handling weight, robust construction ensures operational stability and precision during the wrapping cycle. This minimizes vibrations and misalignments, crucial for consistent wrap quality and preventing damage to the coil or the machine itself. Look for features like high-quality bearings and reinforced support structures.
1.2. Precision Wrapping and Speed Control
Precision is vital for effective and efficient coil packaging. Steel coils vary significantly in dimensions (Inner Diameter, Outer Diameter, Width) and surface characteristics. The wrapping machine must offer precise control over parameters like:
- Wrapping Overlap: Adjustable overlap ensures complete coverage and protection.
- Film Tension: Consistent, adjustable tension prevents damage to sensitive coils and optimizes film usage.
- Rotational Speed: Variable speed control (often via VFDs - Variable Frequency Drives) allows operators to tailor the wrapping process to specific coil types and wrapping materials, optimizing cycle times.
Advanced coil wrappers often utilize PLC (Programmable Logic Controller) systems for precise automation and repeatability. This level of control minimizes material waste, reduces the risk of coil damage during wrapping, and ensures consistent package quality compliant with specifications.
1.3. Ease of Maintenance and User-Friendly Operation
The operational effectiveness of a coil wrapping machine heavily depends on its usability and maintainability. Complex controls or cumbersome maintenance procedures can lead to significant downtime and operational bottlenecks. Opt for machines featuring:
- Intuitive Interface: A user-friendly HMI (Human-Machine Interface) simplifies operation, parameter adjustments, and troubleshooting, reducing training time and potential errors.
- Accessible Components: Easy access to key components like film carriages, rollers, and lubrication points simplifies routine maintenance tasks.
- Self-Diagnostics: Modern machines often include diagnostic systems that alert operators to potential issues or required maintenance, enabling proactive servicing and minimizing unexpected breakdowns.
A machine designed for straightforward operation and maintenance reduces dependency on highly specialized technicians, minimizes downtime, and ensures the equipment remains in optimal working condition for longer.
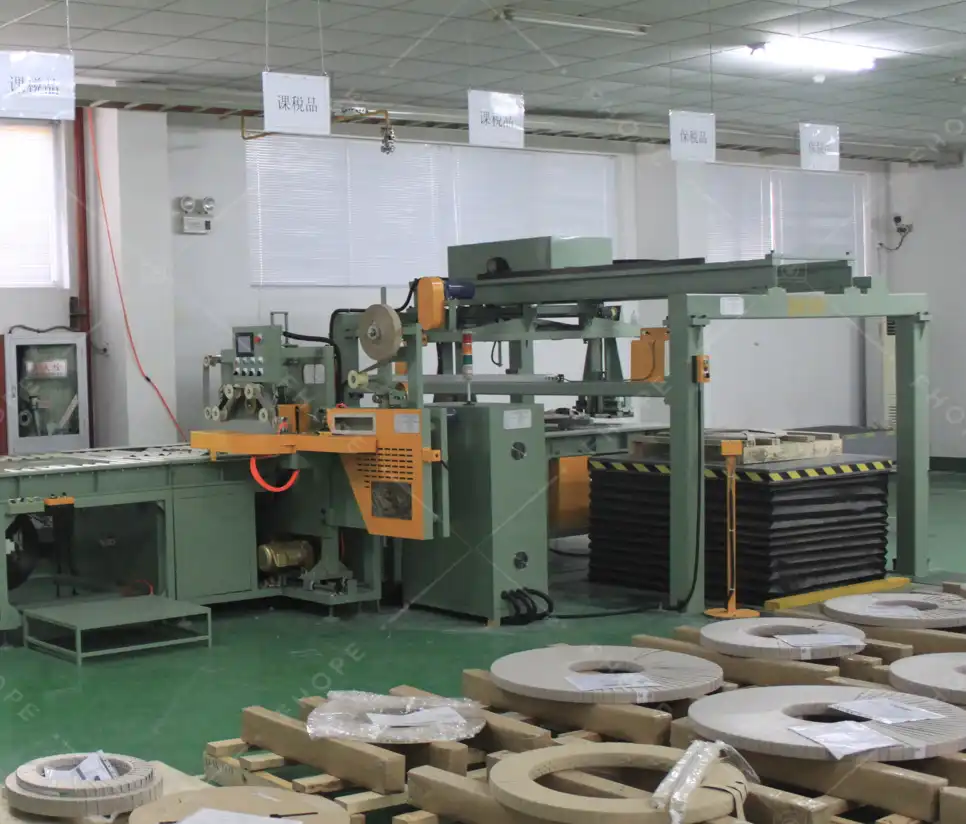
2. Assessing Adaptability: Ensuring Your Machine Meets Diverse Needs
2.1. Flexibility for Various Coil Sizes and Materials
Adaptability is crucial for maximizing the utility of your investment. A versatile coil wrapping machine should efficiently handle a wide range of coil specifications:
- Size Range: Confirm the machine's minimum and maximum coil ID, OD, and width capabilities align with your product portfolio.
- Material Compatibility: Ensure the machine can effectively apply various wrapping materials, such as different gauges of stretch film, VCI (Volatile Corrosion Inhibitor) film/paper, or protective woven fabrics, depending on your protection requirements.
Adjustable parameters, like guide roller positions, wrapping ring speed, and film delivery systems, enable quick changeovers between different coil types. This flexibility streamlines workflow, reduces the need for multiple specialized machines, and ensures consistent packaging quality across diverse products.
2.2. Future-Proofing with Modularity and Scalability
The steel industry landscape is dynamic. Production requirements, coil specifications, and automation levels can change. Investing in a modular coil wrapping machine offers significant long-term advantages. Modularity allows for:
- Upgrades: Adding components like automatic top sheet dispensers, integrated weighing systems, or automated labeling units as needs evolve.
- Integration: Easily integrating the wrapper into a larger automated packaging line with conveyors, palletizers, or strapping machines.
A modular design allows your wrapping system to grow with your business, protecting your initial investment and ensuring the equipment remains a relevant and productive asset for years to come.
2.3. Customization Options for Specific Requirements
While standard machines cover many applications, unique operational needs may necessitate customization. Leading manufacturers often offer tailored solutions, such as:
- Specialized Material Handling: Custom conveyor designs or coil tilting mechanisms for specific plant layouts or product types.
- Enhanced Environmental Protection: Options for specific wrapping patterns or materials to meet stringent storage or shipping conditions.
- Data Integration: Capabilities to interface with plant-level control systems (MES/ERP) for production tracking and quality control.
Discussing your specific challenges and requirements with potential suppliers can reveal valuable customization options that optimize the machine's performance and integration within your unique operational context, ensuring precise alignment with your packaging standards.
3. Prioritizing Safety: Key Features for Operator and Product Protection
3.1. Integrated Automated Safety Mechanisms
Safety is non-negotiable in industrial environments. Modern coil wrapping machines must incorporate comprehensive safety features:
- Emergency Stops (E-Stops): Strategically placed E-stop buttons allow immediate halting of all machine movements.
- Safety Fencing/Guarding: Physical barriers prevent operator access to hazardous moving parts during operation.
- Interlocked Doors/Gates: Access doors equipped with safety interlocks stop the machine if opened during a cycle.
- Light Curtains: Optical safety barriers detect personnel entering restricted zones and trigger a machine stop.
- Overload Protection: Sensors prevent damage to the machine or product by detecting excessive loads or resistance.
These automated systems are crucial for protecting operators from potential hazards associated with heavy loads and automated machinery, minimizing workplace accidents.
3.2. Ergonomic Design for Operator Well-being
An ergonomically designed machine enhances both safety and productivity. Consider features that reduce operator strain and simplify interaction:
- Accessible Controls: HMIs and control panels positioned at comfortable heights and reach distances.
- Easy Film Loading: Systems designed for quick and physically non-demanding replenishment of wrapping materials.
- Clear Visibility: Good sightlines to the wrapping zone allow operators to monitor the process safely.
Ergonomic design minimizes operator fatigue, reduces the risk of musculoskeletal injuries, and can contribute to fewer operational errors, ultimately leading to a safer and more efficient work environment.
3.3. Compliance with Industry Safety Standards
Ensuring the coil wrapping machine complies with relevant safety standards is essential for due diligence and operational integrity. Key standards include:
- CE Marking: Indicates conformity with health, safety, and environmental protection standards for products sold within the European Economic Area (learn more about CE Marking).
- OSHA Guidelines (USA): While OSHA doesn't certify equipment, machines should be designed following OSHA principles for machine guarding and electrical safety (relevant OSHA standards).
- ISO Standards: Relevant ISO standards pertaining to machinery safety (e.g., ISO 12100 for risk assessment).
Compliance signifies that the machine meets rigorous third-party or regulatory safety criteria, providing assurance of its safe design and construction. This is crucial not only for domestic operations but also for facilitating international trade and meeting global customer expectations.
4. Calculating ROI: How Coil Wrappers Reduce Long-Term Operational Costs
4.1. Optimizing Material Usage and Reducing Waste
Automated coil wrapping machines offer precise control over wrapping material application, significantly reducing waste compared to manual methods. Key features contributing to savings include:
- Consistent Overlap Control: Applying the exact required overlap minimizes excess material use.
- Powered Pre-Stretch: Film carriages stretch the film before application (often up to 250-300%), increasing yield per roll and improving load containment with less material.
- Programmed Wrap Cycles: Tailored programs ensure the optimal amount of film is used for each specific coil size and type.
Reducing consumption of stretch film, VCI paper, or other wrapping materials translates directly into lower recurring operational costs and supports sustainability goals by minimizing plastic or paper waste. Potential material savings can often reach 20-50% compared to manual wrapping.
4.2. Lowering Labor Costs Through Automation
Automating the coil wrapping process drastically reduces the manual labor required for packaging. This leads to significant cost savings by:
- Reducing Headcount: Fewer operators are needed to manage the wrapping station.
- Redeploying Labor: Valuable personnel can be reassigned to more complex, higher-value tasks within the facility.
- Increasing Throughput: Automated wrappers operate consistently and often faster than manual wrapping, increasing the number of coils processed per shift.
The reduction in direct labor costs associated with wrapping, combined with increased efficiency, provides a strong justification for the investment in automation, often leading to a rapid return on investment (ROI).
4.3. Minimizing Downtime and Maintenance Expenses
Reliable, well-maintained coil wrapping machines contribute to cost savings by minimizing expensive production downtime. Look for:
- Durable Components: High-quality motors, bearings, and structural elements designed for longevity reduce the frequency of breakdowns.
- Predictive/Preventive Maintenance Features: Onboard diagnostics and maintenance alerts facilitate proactive servicing, preventing major failures.
- Readily Available Spare Parts: Ensure the manufacturer provides good support and quick access to essential spare parts.
Conclusion: Finding a Coil Wrapping Machine That Fits Your Strategic Goals
Selecting the right steel coil wrapping machine is a critical strategic decision with far-reaching impacts on operational efficiency, product quality, cost management, and workforce safety. A well-chosen machine delivers a seamless, reliable wrapping process that effectively protects valuable steel coils during handling, storage, and transit.
By carefully evaluating essential features like robust construction, precision control, adaptability to various coil sizes and materials, integrated safety mechanisms, and ease of maintenance, you can identify equipment that aligns perfectly with your current operational needs and future growth trajectory. Consider factors like potential material savings through optimized usage, labor cost reduction via automation, and minimized downtime through reliable design.
The benefits of investing in the appropriate automated coil wrapping machine are clear: streamlined workflows, significant long-term cost savings, enhanced worker safety, and consistent, high-quality packaging. This decision is not merely about acquiring equipment; it's about bolstering your operational resilience and competitiveness in the demanding steel industry landscape.
[claim] A thoughtfully selected **coil wrapping machine** serves as a valuable long-term asset, delivering continuous operational savings, reducing reliance on manual labor, and ensuring dependable protection for steel coils in today's challenging industrial environment.