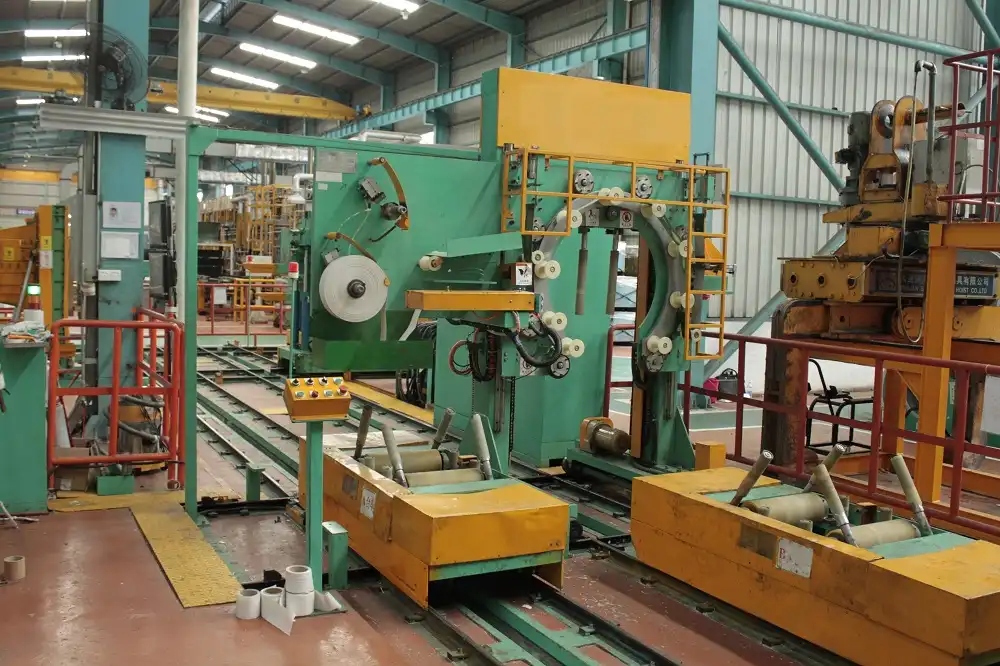
In demanding industrial environments, packaging integrity is non-negotiable. Even minor inconsistencies or errors during the packaging process can lead to significant consequences, including damaged goods during transit, costly returns, safety hazards, and potential harm to a company's reputation. For businesses handling high volumes of products, especially materials like metal coils, ensuring an efficient, consistent, and error-free packaging process is crucial. Automated wrapping solutions provide a powerful answer, offering a streamlined, reliable method that dramatically minimizes the potential for human error. By leveraging packaging automation, operations can enhance productivity while establishing a more robust system that guarantees every package meets stringent quality standards.
Packaging automation transforms wrapping operations by standardizing repetitive tasks, reducing the need for manual handling, and applying wrapping materials with engineered precision. These automated measures inherently decrease the risk of human error, leading to greater consistency and reliability across all packaged products. Unlike manual wrapping, which can vary based on operator skill, fatigue, or attention level, automated systems execute tasks according to precisely defined parameters (such as wrap counts, tension levels, and overlap percentages), leaving minimal room for mistakes. Automated wrapping delivers a level of precision and repeatability that manual methods struggle to match, making it a strategic investment for companies focused on improving packaging accuracy and overall operational excellence.
Effective packaging is far more than a final logistical step; it is a critical function impacting product safety, preservation, transportability, and ultimate customer satisfaction. Implementing automated wrapping solutions ensures each item is packaged with consistent precision and care, significantly reducing the costly errors often associated with manual processes.
[Key Takeaway] Automated wrapping solutions significantly reduce human error in packaging by standardizing processes, optimizing material usage, enhancing consistency, and safeguarding product quality throughout handling and shipping.
1. How Does Packaging Automation Eliminate Inconsistencies?
1.1 Standardizing Wrapping Quality and Application
Manual wrapping processes are inherently susceptible to variability. Different operators may apply inconsistent amounts of wrapping material, use varying tension levels, or even miss sections entirely, leading to unpredictable packaging quality. Automated wrapping solutions are engineered specifically to eliminate this variability. Using pre-set, digitally controlled parameters managed by Programmable Logic Controllers (PLCs), the machine applies a uniform wrap pattern with consistent tension and overlap around every product. This ensures each item, such as a steel coil or palletized load, receives the exact level of protection and containment required.
By removing operator-induced variability, automated systems enhance overall packaging reliability. Key benefits include:
- Uniform Standards: Every wrapped product adheres to the same predefined quality standard.
- Reduced Inspections: Less need for manual quality checks or re-wrapping due to inconsistent application.
- High Control: Provides precise control crucial for industries like metals or electronics, where robust protection is vital.
1.2 Optimizing Material Consumption and Reducing Waste
Human error frequently contributes to the inefficient use of wrapping materials during manual packaging. Operators might inadvertently apply too much film to one load and insufficient film to another, impacting both material costs and the integrity of the package. Automated systems address this directly by utilizing precise measurements and optimized stretch capabilities (often via powered pre-stretch carriages) for each wrap cycle. This ensures that the minimum necessary material is used to achieve secure containment, eliminating waste from overuse while preventing the risks associated with under-wrapping.
This precise control over material consumption not only yields significant cost savings over time but also ensures products are adequately protected for handling and transport. By maintaining optimal wrap usage, automated solutions enhance both the economic efficiency and the functional effectiveness of the packaging process, minimizing error potential while maximizing resource utilization.

1.3 Ensuring Consistency Across High-Volume Production
For operations managing high-volume packaging demands, maintaining consistency across thousands of units is paramount. Automated wrapping solutions excel in this area, capable of handling large quantities tirelessly without the performance degradation or variation common in manual processes. The machine's programmed nature guarantees that every product, whether the first or the last in a long production run, receives the same precise wrap application. This capability is particularly beneficial for businesses processing large or bulk orders where uniform protection is essential for maintaining product quality, safety, and logistical efficiency.
High-volume consistency delivered by packaging automation leads to predictable outcomes and smoother logistics, as each packaged item is uniformly prepared for storage or shipment. Automation enables operations to meet fluctuating demand while upholding stringent quality controls—a critical balance for companies aiming to maintain a competitive edge.
2. How Does Precision Wrapping Minimize Packaging Errors?
2.1 Accurate Material Application via Programmable Settings
A key advantage of automated wrapping solutions lies in their ability to apply packaging materials with exceptional accuracy. Unlike manual methods reliant on operator judgment and physical effort, automated machines can be programmed with specific parameters dictating the exact amount of material, the degree of overlap, and the placement of the wrap. This digital control ensures each package is wrapped securely and efficiently, eliminating common errors related to inconsistent material application (too much or too little film).
Precision in material application extends beyond waste reduction; it guarantees optimal load containment and protection. Automated settings provide consistent wrap tension and force, crucial for maintaining the stability and structural integrity of the package—especially vital for heavy industrial coils or unstable pallet loads that require robust protection to prevent shifting or damage during handling and transit.
2.2 Preventing Product Damage with Consistent Tension Control
The tension applied during the wrapping process is critical for product protection. Excessive tension can crush or deform sensitive products or damage packaging corners, while insufficient tension leads to loose, ineffective packaging prone to failure during shipment. Automated wrapping solutions incorporate sophisticated tension control systems (e.g., electronic sensors, variable speed motors on film carriages) that maintain precise, consistent tension throughout the wrap cycle, eliminating the inconsistencies inherent in manual application.
By removing the variability associated with manual tension control, automated systems significantly reduce the risk of product damage caused by improper wrapping. Consistent tension ensures the load is secured effectively, protecting the product while also improving the overall appearance and structural quality of the final package, minimizing risks during storage, handling, and transportation.
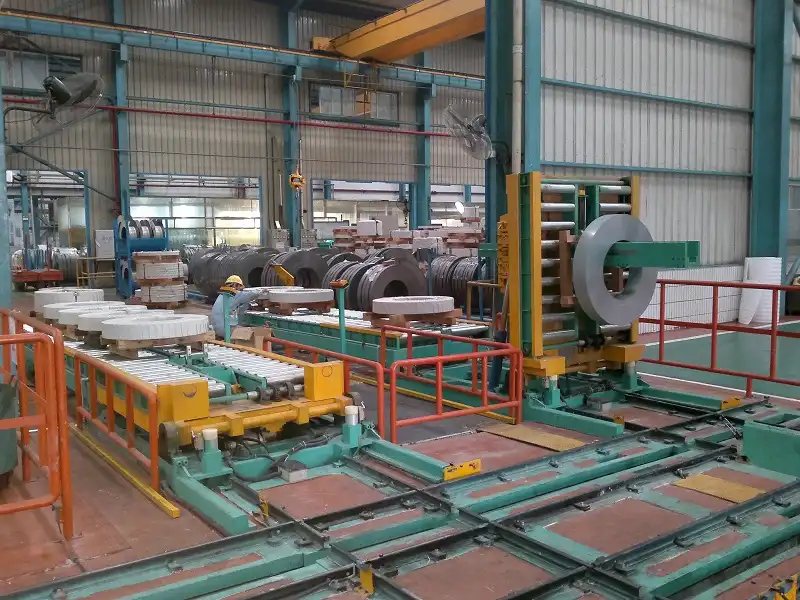
2.3 Ensuring Reliable Package Quality for Customer Satisfaction
Precision in wrapping translates directly to enhanced customer satisfaction. When products arrive consistently well-packaged—neatly wrapped, secure, and undamaged—it creates a positive impression and reinforces the supplier's commitment to quality. Automated wrapping solutions ensure uniform packaging presentation, reducing customer complaints related to shipping damage or poorly secured items.
The reliable quality provided by automation builds customer trust and loyalty. Clients learn to expect that every shipment will meet the same high packaging standards. Consistent, professional packaging not only protects the product but also enhances the perceived value and contributes positively to the overall customer experience, potentially leading to repeat business and positive referrals.
3. How Does Packaging Automation Enhance Workflow Efficiency?
3.1 Streamlining the Wrapping Cycle to Increase Throughput
Automated wrapping machines significantly reduce the time required to complete each wrap cycle compared to manual methods. Manual wrapping is often slow, physically demanding, and repetitive, whereas automated solutions perform the task rapidly with minimal operator intervention. This increase in speed is particularly advantageous in high-demand operations where maximizing throughput is critical. By accelerating the wrapping process, automation frees up valuable time and allows the entire production or distribution line to operate more efficiently.
Faster wrapping cycles mean more products can be processed and prepared for shipping or storage within a given timeframe. This results in a streamlined workflow where products move smoothly from production or picking to the wrapping station and onto the next stage (e.g., loading docks), keeping the operation agile and capable of handling larger volumes without delays.
3.2 Reducing Bottlenecks Caused by Manual Processes
Manual wrapping stations can easily become bottlenecks in a production or logistics flow. Each product requires individual positioning, wrapping, cutting, and sometimes inspection by an operator, creating potential delays. Automated machines, especially those integrated with conveyor systems, eliminate these bottlenecks by handling the entire process seamlessly and continuously. Products can be fed into the machine automatically, wrapped according to preset programs, and discharged onto outbound conveyors, minimizing manual touchpoints and waiting times.
By removing the interruptions and delays associated with manual wrapping, automated solutions enable a steadier, more predictable operational flow. This reduction in downtime makes it easier to meet production schedules, maintain consistent output levels, and improve overall equipment effectiveness (OEE), all essential factors for high-efficiency operations.
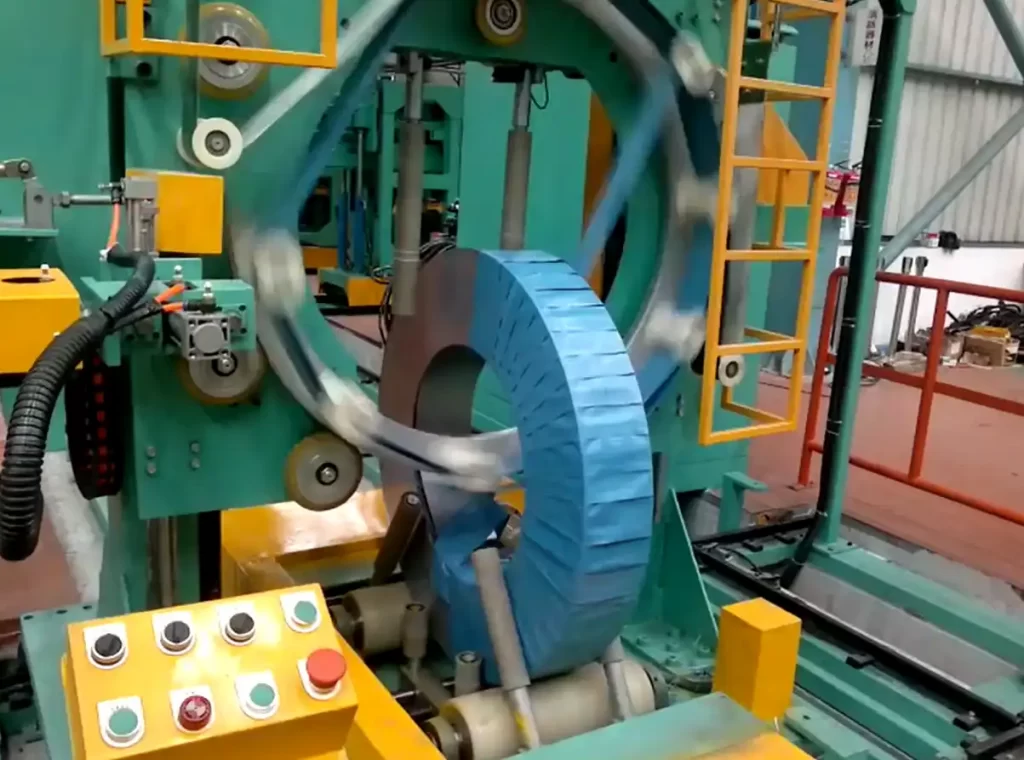
3.3 Optimizing Labor Allocation for Higher Productivity
Implementing an automated wrapping solution typically reduces the number of workers required for the wrapping task itself. This allows operations to reallocate valuable labor resources more effectively. Instead of dedicating multiple personnel to the physically demanding and repetitive task of manual wrapping, operators can be reassigned to focus on more complex, skilled, or value-adding activities such as quality assurance, machine monitoring, maintenance, or inventory management. This reallocation optimizes the workforce and reduces dependency on manual tasks prone to ergonomic risks, errors, and inefficiencies.
Optimizing labor allocation through automation fosters a more balanced and productive workforce. Employees spend less time on monotonous tasks and more time contributing to activities requiring human judgment and expertise, supporting both operational objectives and potentially improving employee engagement and job satisfaction.
4. Why is Automation Crucial for Meeting Quality Standards?
4.1 Ensuring Consistent Quality Control in Packaging
A primary advantage of automated wrapping solutions is the unparalleled consistency they introduce to quality control processes. In manual wrapping, variations between operators, shifts, or even fatigue levels can lead to significant differences in packaging quality, potentially compromising product integrity or safety. Automated systems, operating based on precise, repeatable programming, ensure that every single package meets the same high standards, every time. This level of consistency is indispensable for industries where stringent quality control is not merely preferred but mandated.
By automating the wrapping process, businesses can guarantee that each product is wrapped according to specification, eliminating inconsistencies that could result in damage, load shifting, or failure to meet customer or regulatory expectations. Automation transforms quality control from a variable factor into a reliable constant, simplifying downstream inspection processes and ensuring compliance.
4.2 Facilitating Compliance with Industry Regulations and Standards
Many industries, particularly those dealing with hazardous materials, food products, pharmaceuticals, or heavy industrial goods, operate under strict packaging regulations (e.g., concerning load stability, containment force, or tamper evidence) to ensure safety during transport and storage. Manual processes, due to their inherent variability and potential for error, present challenges in consistently meeting these rigorous standards. Automated wrapping machines, however, can be programmed and validated to adhere precisely to specific guidelines (like those from ASTM or ISTA), ensuring every package is wrapped in full compliance.
Using automation significantly reduces the risk of non-compliance, which can lead to costly fines, rejected shipments, liability issues, or damaged customer relationships. Reliable, automated compliance safeguards the business's reputation and ensures products are packaged according to required standards, facilitating smoother logistics and potentially opening doors to markets with strict regulatory requirements.

4.3 Enhancing Brand Reputation Through Superior Packaging Presentation
In today's competitive marketplace, the quality of packaging directly influences brand perception. Consistently well-packaged products signal professionalism, attention to detail, and care for the product itself, fostering customer trust and loyalty. Automated wrapping machines ensure that every product, whether a single coil or a full pallet, is presented uniformly, securely, and professionally. This consistency reassures customers about the product's quality and the supplier's reliability.
By investing in automated wrapping, businesses are not just meeting operational quality standards—they are actively enhancing their brand image and exceeding customer expectations. Every professionally packaged product leaving the facility serves as a tangible representation of the brand's commitment to excellence, boosting customer satisfaction and strengthening the company's position in the market.
Conclusion: Embracing Automation for Error-Proof Packaging
Automated wrapping solutions represent far more than a simple technological upgrade; they are a strategic imperative for businesses seeking to minimize human error, enhance packaging consistency, optimize workflow efficiency, and uphold rigorous quality standards. The precision, control, and repeatability offered by packaging automation transform a potentially variable manual task into a streamlined, reliable process free from the unpredictability and inherent risks of manual handling. For operations prioritizing quality, efficiency, safety, and cost-effectiveness, automation provides a clear path towards error-proof packaging.
The benefits of automated wrapping systems are comprehensive:
- Reduced Errors: Minimizes mistakes related to inconsistent application, tension, or material usage.
- Enhanced Consistency: Ensures every package meets identical quality and security standards.
- Improved Efficiency: Increases throughput, reduces bottlenecks, and optimizes labor.
- Cost Savings: Lowers material waste and reduces costs associated with damaged goods or re-work.
- Regulatory Compliance: Facilitates adherence to industry packaging standards and regulations.
Ultimately, this technology supports a consistently high-quality output that meets customer expectations, enhances operational resilience, and improves safety. In an industrial landscape where precision, reliability, and efficiency are paramount, automated wrapping solutions offer a proven pathway to more effective, sustainable, and competitive packaging operations.
[Final Thought] Implementing automated wrapping solutions is key to reducing human error, improving consistency, and streamlining workflows, making them indispensable for operations committed to packaging quality and efficiency. This strategic investment supports both immediate operational improvements and long-term business goals, positioning companies for greater success.

Get Your Best Solution !