How Can a Coil Wrapping Machine Help Reduce Downtime in Your Operations?
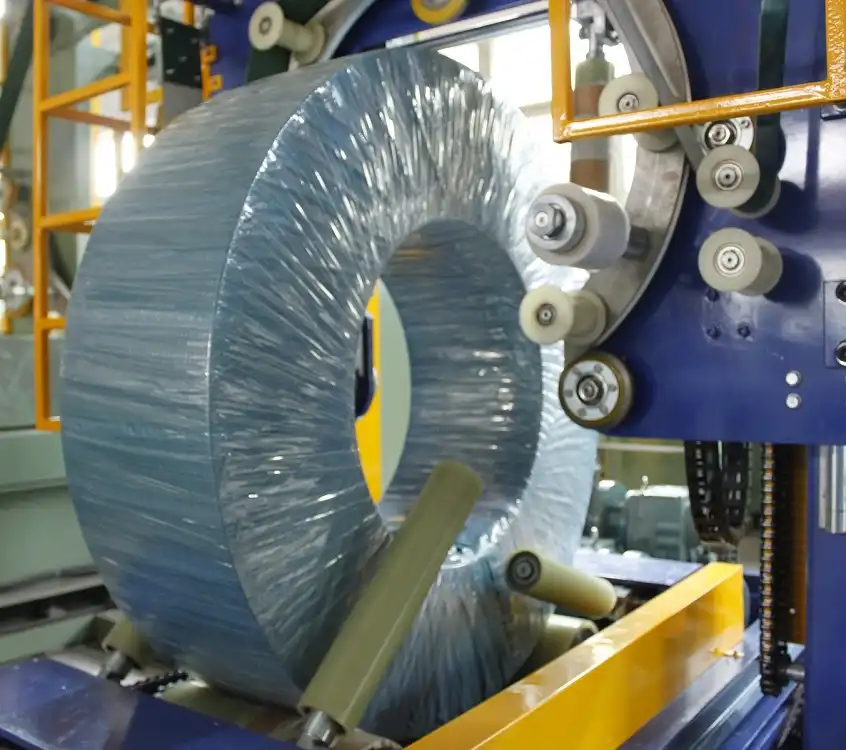
In high-volume industrial operations, particularly within manufacturing and logistics, downtime is more than just an inconvenience—it’s a costly setback impacting productivity, profitability, and overall workflow efficiency. For industries handling heavy coils of metal, wire, or cable, every minute lost to packaging delays or manual handling inefficiencies accumulates, causing significant disruptions. An automated coil wrapping machine offers a robust solution, streamlining the packaging process to minimize downtime and maintain smooth, continuous operations.
Implementing a coil wrapping machine automates how coils are handled, wrapped, and prepared for shipment or storage, directly addressing bottlenecks that lead to operational delays. As downtime decreases through optimized packaging, overall operational capacity increases, supporting higher output levels and improved scheduling control. This guide explores the specific ways these machines contribute to reducing downtime.
1. Accelerating the Packaging Cycle Time
1.1 Enhanced Packaging Speed through Automation
One of the most significant advantages of a coil wrapping machine is its ability to dramatically accelerate the packaging process compared to manual methods. Traditional wrapping requires multiple steps, careful material handling, and considerable physical effort, all contributing to longer cycle times. An automated coil wrapper, designed for speed and consistency, can wrap a coil securely in a fraction of the time. This increase in packaging throughput allows operations to handle higher volumes and meet tight deadlines with less risk of idle time accumulating.
The automated process ensures each coil is wrapped efficiently and uniformly, enabling a continuous production flow. Unlike manual packaging, which can be prone to variations in speed and quality, automation provides predictable cycle times, crucial for high-demand environments where maximizing output per shift is essential.
1.2 Streamlined Workflow Reduces Waiting Periods
Integrating a coil wrapping machine streamlines the overall workflow by minimizing the waiting times often associated with manual packaging stations. In a manual setup, coils might queue while operators prepare materials, position the coil, or perform the wrapping. Automation allows coils to be fed continuously into the wrapping cycle with minimal preparation or manual adjustment needed between items. This integration often connects seamlessly with upstream and downstream processes, such as coil tilting, weighing, and labeling.
This streamlined approach maintains momentum across the production line, preventing bottlenecks caused by slower packaging steps. Reducing these intermediate waiting periods significantly decreases overall downtime, allowing the operation to run more smoothly and predictably.
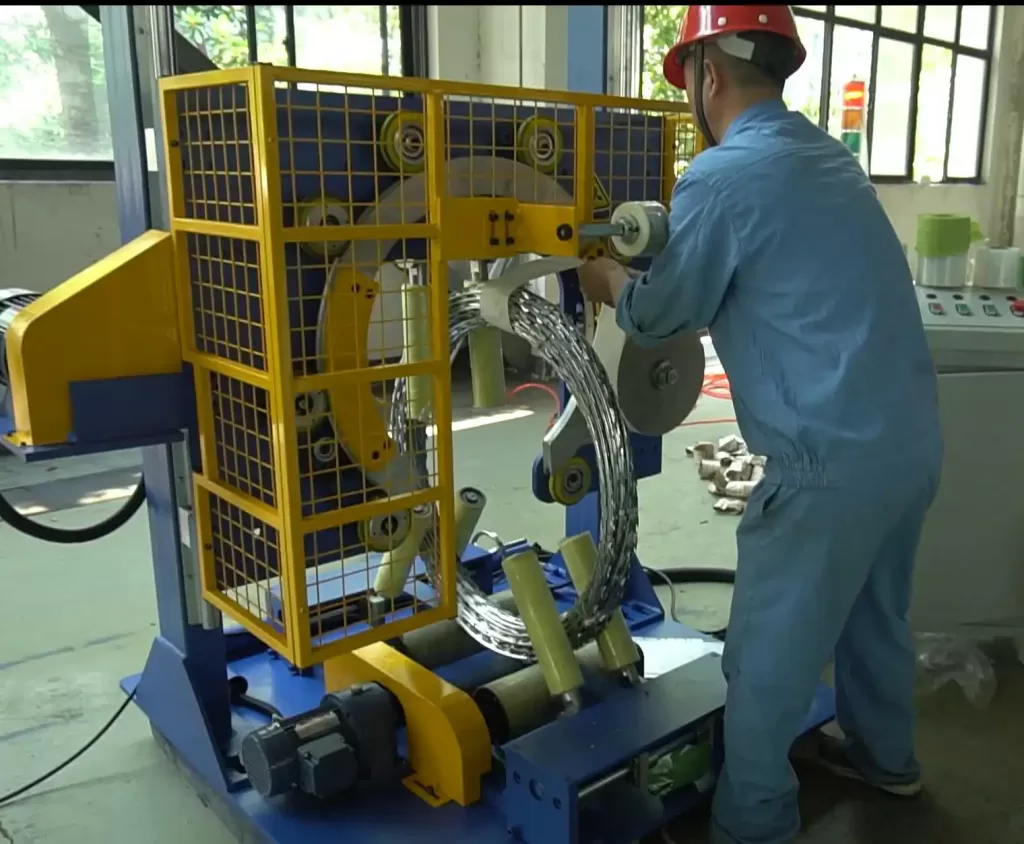
1.3 Managing High Volumes Efficiently
For operations managing large volumes of coils, maintaining efficiency during peak production periods is critical. A coil wrapping machine provides high throughput capabilities, enabling faster turnover without sacrificing packaging quality. It can consistently wrap coil after coil, ensuring the packaging station does not become a limiting factor, even when production demands surge.
This capacity for high-volume efficiency is vital for scalability. Operations can meet growing demand without proportional increases in labor costs or the risk of packaging-related bottlenecks. The result is a more productive, adaptable workflow with minimized potential for downtime due to volume pressures.
2. Minimizing Manual Intervention and Associated Errors
2.1 Reducing Operator Dependency
Automated coil wrapping significantly reduces the reliance on manual labor for the packaging task. Traditional methods often require multiple operators for handling, positioning, and wrapping heavy coils. A coil wrapping machine automates these tasks, typically requiring only one operator for oversight, loading/unloading assistance (depending on integration level), and control monitoring, rather than direct physical involvement in the wrapping itself.
Reducing the number of operators directly involved lowers labor costs and minimizes downtime potential linked to staff availability, breaks, or shift changes. Furthermore, automation frees up skilled labor for more complex tasks within the facility.
2.2 Automation Minimizes the Risk of Human Error
Human error is a frequent cause of delays and rework in manual packaging, particularly with materials like metal coils where incorrect tension or wrap placement can lead to damage or instability. Operators, even experienced ones, can introduce variability. Automated coil wrappers execute pre-programmed wrapping patterns with precision, using sensors and controls to ensure correct material application, tension, and overlap every time.
By drastically reducing the chance of errors, automation eliminates the need for time-consuming rework and prevents the associated downtime. This leads to a smoother, more reliable operation with fewer interruptions for quality corrections.
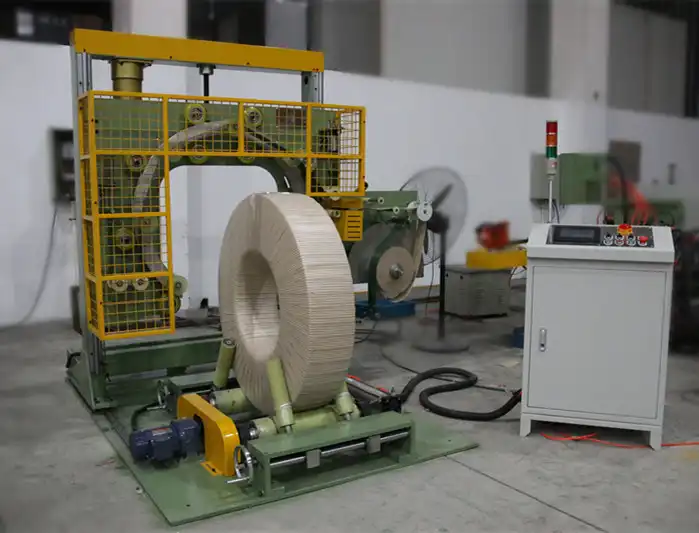
2.3 Standardizing Processes for Faster Troubleshooting
An automated coil wrapping machine introduces standardization to the packaging process. Each action is repeatable and predictable, which simplifies troubleshooting immensely. When issues arise in a manual process involving multiple variables (including operator technique), diagnosing the root cause can be complex and time-consuming. With an automated system, deviations are often machine-related and diagnostics can be performed more systematically using machine feedback and error logs.
This standardization allows maintenance teams or operators to identify and resolve problems more quickly, minimizing the duration of any unscheduled downtime. Easier troubleshooting ensures the operation maintains high levels of efficiency and availability.
3. Enhancing Consistency to Prevent Rework
3.1 Uniform Wrapping Prevents Delays
Consistency is key to reducing downtime caused by packaging failures. Automated coil wrapping machines deliver uniform, high-quality wrapping consistently, coil after coil. Manual wrapping can suffer from variations in tension, material usage, and coverage, potentially leading to insecure loads or inadequately protected products. Such errors necessitate rework, consuming valuable time and resources, and causing production delays.
The reliable consistency of machine wrapping ensures that each coil meets packaging specifications without needing manual inspection, adjustments, or re-wrapping. This dependability supports predictable production schedules, allowing wrapped coils to move smoothly to the next stage (storage, shipping) without hold-ups related to packaging quality.
3.2 Maintaining Quality Across All Production Runs
Maintaining consistent packaging quality, especially during high-volume production or across different shifts, can be challenging with manual methods. A coil wrapping machine guarantees that every coil is wrapped to the same standard, irrespective of production volume or time of day. This reliability not only enhances product presentation and protection against handling or environmental damage but also reduces the likelihood of costly returns or transit damage claims, which indirectly cause operational disruptions.
Predictable quality output supports a seamless workflow, minimizing the need for extensive quality control checks post-packaging and preventing downstream disruptions caused by packaging failures. This ensures coils are adequately prepared for storage and transportation.
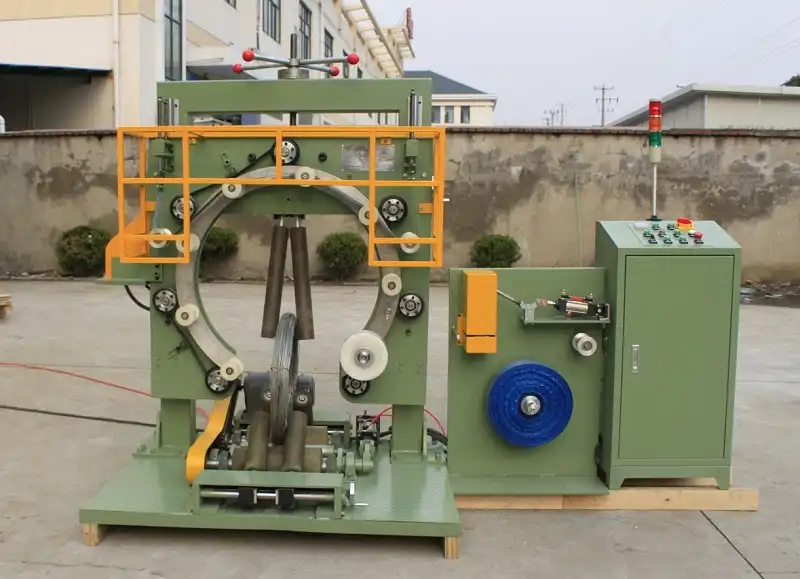
3.3 Efficient Transition Between Different Coil Specifications
Modern coil wrapping machines often feature programmable controls that allow quick adaptation to various coil sizes, widths, and wrapping material requirements. Manually adjusting wrapping methods and materials for different coil types can be slow and prone to setup errors, leading to downtime during changeovers. Automated machines can often store multiple wrapping programs ("recipes"), allowing operators to switch settings quickly and accurately via a control interface.
This adaptability minimizes downtime associated with product changeovers, maintaining production line momentum even when handling diverse orders. Faster transitions support operational flexibility and efficiency, preventing bottlenecks when switching between different coil specifications.
4. Improving Workplace Safety to Lower Unexpected Stops
4.1 Reducing Injury-Related Interruptions
Worker safety is a critical factor in maintaining operational continuity. Manual coil wrapping often involves repetitive motions, heavy lifting, and awkward postures, increasing the risk of musculoskeletal injuries and accidents. Workplace injuries lead to significant downtime due to immediate work stoppages, potential needs for replacement staff, incident investigations, and lost productivity. By automating the physically demanding tasks of coil wrapping, machines significantly reduce ergonomic risks and the likelihood of accidents, thereby minimizing unexpected downtime related to injuries. (Source: OSHA - Materials Handling and Storage)
Investing in automation creates a safer work environment. Fewer injuries mean fewer disruptions, ensuring the production line operates more reliably without the costly setbacks and human impact associated with workplace accidents.
4.2 Safer Handling Protocols for Heavy Coils
Manually maneuvering and wrapping heavy coils inherently carries risks, both to personnel and the product itself. Mishandling can lead to dropped loads, product damage (dents, scratches), and compromised wrap integrity, necessitating rework or scrapping – all sources of downtime. Coil wrapping machines are engineered to handle heavy loads securely and precisely, often integrating with automated loading/unloading systems. This controlled handling protects workers from strain and crush hazards while safeguarding the coil from damage during the packaging process.
A machine-based, safer handling process prevents accidents and product damage, reducing associated operational slowdowns and costs. This contributes to a more reliable and predictable workflow.
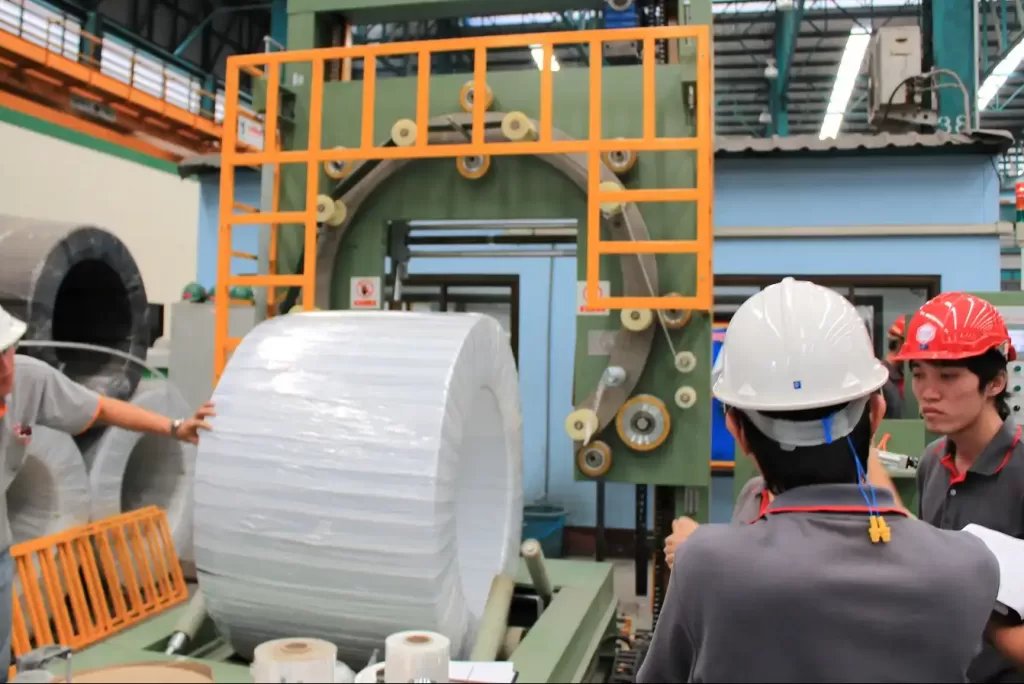
4.3 Enhanced Compliance with Safety Standards
Automated packaging equipment, including coil wrappers, is typically designed to meet stringent industry safety standards (e.g., CE marking, ISO standards). Features like safety fencing, light curtains, emergency stops, and interlocking guards are common, creating a controlled environment that minimizes operator exposure to hazards. Adhering to these standards not only reduces liability but also supports a stable operational environment less prone to safety-related interruptions, inspections, or mandated shutdowns. (Source: ISA84 - Standard on Safety Instrumented Systems)
Built-in safety compliance contributes directly to uninterrupted production. By operating within established safety protocols facilitated by the machinery, businesses can minimize downtime stemming from non-compliance issues or safety incidents.
Conclusion: Leveraging Coil Wrapping Machines for Maximum Operational Uptime
Investing in an automated coil wrapping machine is a strategic measure to significantly reduce operational downtime and boost overall efficiency. By accelerating packaging cycles, minimizing reliance on manual labor, ensuring consistent wrapping quality, and improving workplace safety, these machines directly address common causes of production bottlenecks and interruptions. Automation optimizes key aspects of the packaging workflow, leading to enhanced productivity, better resource allocation, and improved scalability.
In competitive industries where time translates directly to cost and output, minimizing downtime is paramount. A coil wrapping machine facilitates a more streamlined, efficient, and safer production environment capable of consistently meeting high demands without the frequent delays inherent in manual processes. This technology represents a valuable investment for achieving long-term operational stability and supporting sustained growth.

Get Your Best Solution !