Eco-Friendly Packaging: How Automated Systems Reduce Resource Waste in Steel Coil Packaging
- Eco-Friendly Packaging: How Automated Systems Reduce Resource Waste in Steel Coil Packaging
- 1. The Environmental Impact of Traditional Packaging Methods
- 2. How Automated Systems Help Cut Down Material Waste
- 3. Energy Efficiency in Automated Steel Coil Packaging
- 4. Consistency and Accuracy: Reducing Waste in Every Package
- 5. Reducing Transportation Emissions with Optimized Packaging
- 6. Automated Palletizing: Reducing Packaging Waste at the End of the Line
- 7. The Role of Smart Technology in Monitoring and Reducing Waste
- 8. Lowering Operational Costs Through Automation
- 9. Sustainability in Packaging Materials
- 10. Compliance with Environmental Regulations
- 11. Reducing Waste Throughout the Supply Chain
- 12. Long-Term Sustainability Through Automation
- 13. Case Study: Real-World Impact of Automated Steel Coil Packaging
- Conclusion
In today's rapidly evolving world, sustainability is no longer just a buzzword—it's a critical priority for industries across the globe. For the steel industry, where large volumes of material are produced, packaged, and shipped, the need for eco-friendly packaging solutions is particularly pressing. Steel coil packaging, in particular, poses significant challenges when it comes to resource waste and environmental impact. Traditional packaging methods often involve excess materials and energy use, contributing to higher costs and an unsustainable ecological footprint.
But, thanks to technological advancements, there's a solution that can help the steel industry become greener while also improving efficiency: automated packaging systems. These systems not only streamline operations but also drastically reduce the amount of material and energy wasted during the packaging process. In this comprehensive article, we'll explore how automated systems can help reduce resource waste in steel coil packaging, offering both environmental and economic benefits.
1. The Environmental Impact of Traditional Packaging Methods
When it comes to packaging steel coils, traditional methods are far from efficient. Manual packaging often leads to inconsistent wrapping, excessive use of materials, and energy waste. This inefficiency can have a substantial environmental impact, contributing to both material waste and higher energy consumption.
For example, manual wrapping can result in uneven layers of plastic or stretch film, which increases material usage. Similarly, the inconsistent application of tension during strapping can lead to the need for more straps than necessary. Over time, these small inefficiencies add up, creating a wasteful and environmentally harmful packaging process.
By continuing with these outdated methods, companies may also face increasing pressure from regulatory bodies, consumers, and environmental organizations to adopt more sustainable practices. This is where automation comes into play, offering a more eco-conscious alternative.

2. How Automated Systems Help Cut Down Material Waste
One of the most effective ways that automated systems contribute to eco-friendly packaging is by reducing the amount of packaging material used. Automated packaging machines are designed with precision in mind. Whether it's stretch film, strapping material, or protective padding, these machines ensure that only the required amount of material is used—nothing more, nothing less.
For instance, automated wrapping machines can adjust the amount of stretch film based on the size and weight of each steel coil. This prevents overuse, which is common in manual packaging where workers may apply more layers than necessary for fear of not providing enough protection. With automation, coils are wrapped consistently with just the right amount of material, resulting in significantly less plastic waste.
In addition, automated strapping machines apply uniform tension to straps, ensuring that each strap is tight enough to secure the coil without wasting excess material. By eliminating human error, these systems help reduce both material waste and costs, making packaging more sustainable.
3. Energy Efficiency in Automated Steel Coil Packaging
Another major area where automated systems excel is in reducing energy consumption. Traditional packaging processes often rely on manual labor and outdated machinery, both of which can be energy-intensive. Workers may use equipment inefficiently, leading to unnecessary energy consumption that inflates the company’s carbon footprint.
Automated systems, on the other hand, are built to operate with energy efficiency in mind. Advanced packaging machines consume less energy by optimizing their operations and running only when needed. For example, some machines are equipped with power-saving modes that allow them to enter a low-energy state when not in use. This ensures that energy is conserved during downtime, which isn’t possible with older, less sophisticated machines.
Additionally, servo-driven motors found in modern automated equipment operate more efficiently than traditional electric motors. These systems adjust their energy usage based on the load they’re handling, further reducing unnecessary power consumption.
4. Consistency and Accuracy: Reducing Waste in Every Package
A key advantage of automated systems is their ability to provide consistent, high-quality packaging for every coil, regardless of size or shape. In manual processes, packaging quality can vary from one worker to another, leading to inconsistent application of materials. This not only affects the security of the packaging but also results in material overuse as workers try to ensure protection.
With automation, every coil is packaged to exact specifications. Automated wrapping machines apply the same amount of stretch film to each coil, ensuring that no additional material is wasted. Similarly, automated strapping systems apply uniform tension, eliminating the need for extra straps that would otherwise be used in manual processes.
The precision of automated systems also means fewer packaging errors, which reduces the likelihood of rework. When a coil is incorrectly packaged, it may need to be unwrapped and re-packaged, leading to more wasted materials and energy. By improving accuracy and reducing the need for rework, automated systems further minimize waste and contribute to more eco-friendly packaging practices.
5. Reducing Transportation Emissions with Optimized Packaging
In addition to minimizing material and energy waste, automated packaging systems can also help reduce the environmental impact of transportation. Optimized packaging means that steel coils take up less space on trucks, trains, or ships, allowing for more efficient use of transportation resources.
By ensuring that coils are wrapped tightly and securely, automated systems prevent over-packaging, which can make coils bulkier than necessary. This compact packaging allows for more coils to be loaded onto a single vehicle, reducing the number of trips needed to transport the same amount of product. Fewer trips mean lower fuel consumption and reduced greenhouse gas emissions, making the transportation of steel coils more sustainable.
Furthermore, tightly wrapped coils are less likely to shift or become damaged during transit, reducing the need for replacement shipments. This, in turn, reduces the overall energy consumption associated with the transportation of steel products.
6. Automated Palletizing: Reducing Packaging Waste at the End of the Line
One often overlooked aspect of steel coil packaging is the palletizing process. Traditional palletizing methods involve manually stacking and securing coils onto pallets, which can result in inconsistent load distribution and increased use of materials like shrink wrap and strapping.
Automated palletizing systems, however, can stack coils in a way that maximizes space efficiency and reduces the need for additional materials. By using precise algorithms and robotic arms, automated palletizers ensure that coils are arranged optimally, reducing the need for excessive wrapping or strapping.
Moreover, automated palletizers can adapt to different pallet sizes and configurations, allowing companies to use recyclable materials or reusable pallets, further contributing to a reduction in resource waste. This not only makes the packaging process more sustainable but also reduces costs associated with packaging materials and disposal.
7. The Role of Smart Technology in Monitoring and Reducing Waste
Smart technology plays a significant role in improving the sustainability of automated steel coil packaging systems. Many automated machines are now equipped with sensors, real-time monitoring, and data analytics capabilities that allow operators to monitor material usage, energy consumption, and system efficiency.
These systems can detect inefficiencies or waste in real time, enabling operators to make adjustments on the fly. For example, if a machine is using more film than necessary to wrap a coil, the system can alert the operator, who can then adjust the settings to reduce material waste. In some cases, the machines themselves can make these adjustments automatically, further minimizing the chances of overuse.
The ability to collect and analyze data also helps companies track their sustainability efforts and make informed decisions about how to reduce waste. By understanding exactly where and how resources are being used, businesses can identify opportunities for further improvement, ultimately contributing to a greener packaging process.
8. Lowering Operational Costs Through Automation
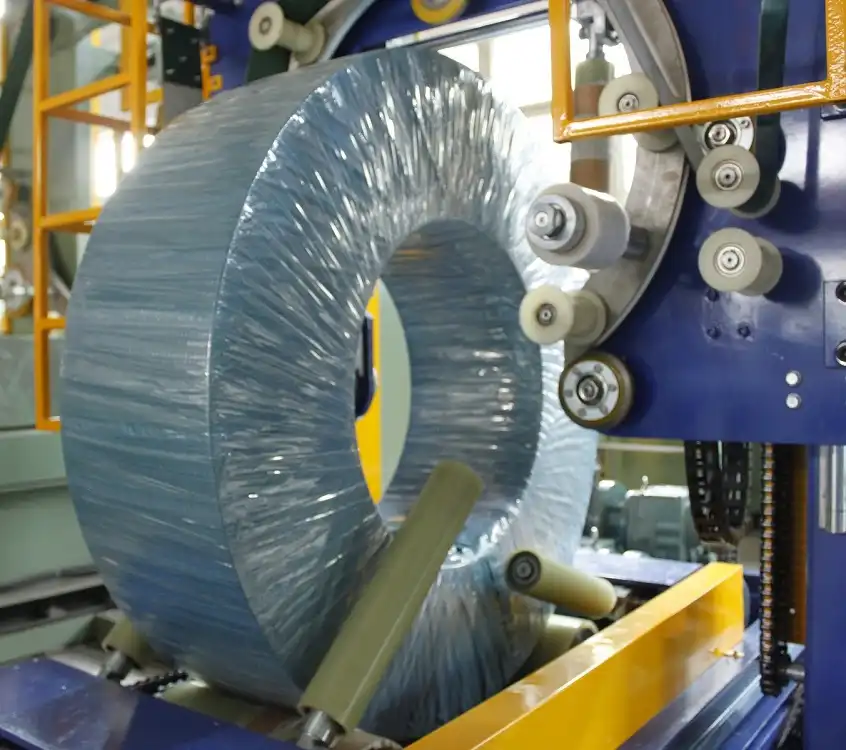
In addition to the environmental benefits, automated packaging systems offer significant economic advantages by lowering operational costs. Traditional manual processes require a large workforce to handle the repetitive tasks of coil packaging, including wrapping, strapping, and palletizing. These labor costs add up over time, especially when considering factors like overtime, employee benefits, and training.
Automation drastically reduces the need for manual labor, allowing companies to reallocate human resources to more skilled tasks that require judgment and decision-making. This shift not only improves operational efficiency but also reduces expenses related to labor. Moreover, since automated systems provide more consistent packaging, there’s less risk of product damage during transportation, which can lead to fewer returns and replacement shipments.
Automated machines are also more energy-efficient than their manual counterparts. By optimizing energy usage during packaging, companies can reduce their overall energy consumption, resulting in lower utility bills. Combining these cost-saving measures allows companies to boost profitability while simultaneously improving their sustainability credentials.
9. Sustainability in Packaging Materials
As the world continues to shift toward more environmentally conscious practices, the use of sustainable packaging materials is becoming increasingly important in steel coil packaging. Automated systems allow companies to make better use of biodegradable, recyclable, or renewable materials, further reducing their environmental impact.
For instance, many automated wrapping machines are designed to work with eco-friendly films that break down more quickly in landfills or can be easily recycled. By using less plastic and switching to biodegradable options, companies reduce their contribution to plastic pollution while still ensuring that the steel coils are protected during shipping.
Additionally, by using recyclable strapping materials such as PET (Polyethylene Terephthalate) instead of traditional metal straps, companies can reduce waste and promote a circular economy. Automated strapping machines are equipped with the technology to adjust to these materials without sacrificing the strength or integrity of the packaging, making this transition to sustainable materials seamless.
10. Compliance with Environmental Regulations
As governments and regulatory bodies worldwide continue to tighten restrictions on waste management and carbon emissions, companies in the steel industry must ensure that their packaging processes comply with these increasingly strict standards. Failing to adhere to environmental regulations can lead to hefty fines, legal penalties, and reputational damage.
Automated packaging systems make it easier for companies to comply with environmental regulations by reducing waste, minimizing energy consumption, and optimizing material usage. By investing in automation, companies can ensure that they are operating within the required legal frameworks and actively reducing their carbon footprint.
For example, many automated systems are designed with features that allow companies to track their resource usage and generate reports that demonstrate compliance with government mandates. These reports can be used to showcase a company’s commitment to sustainability and provide transparency to stakeholders, customers, and regulators.
11. Reducing Waste Throughout the Supply Chain
The benefits of automated packaging systems extend beyond the packaging process itself. By ensuring that steel coils are securely wrapped, efficiently stacked, and properly strapped, automated systems minimize the risk of damage during transportation. This reduction in damaged goods not only prevents waste in the form of unusable steel coils but also reduces the need for additional transportation to replace damaged products.
Moreover, by optimizing packaging to use less material and tightly secure coils, companies can reduce the overall volume of packaging. This leads to more efficient loading of trucks, trains, or ships, enabling businesses to transport more coils per shipment. Fewer shipments result in lower fuel consumption and reduced carbon emissions, making the entire supply chain more environmentally friendly.
12. Long-Term Sustainability Through Automation
While the immediate benefits of automated steel coil packaging systems are clear, it’s important to also consider the long-term sustainability that automation provides. Automated systems are designed to be durable and scalable, which means that they can grow with your business without needing frequent replacements or upgrades.
Because of their longevity and efficiency, these systems provide long-term cost savings and continued reductions in material and energy waste. Over time, the initial investment in automation pays off, not only in terms of financial ROI but also in terms of environmental impact.
Moreover, by adopting automated packaging systems, companies demonstrate their commitment to sustainability, which is increasingly important to both consumers and investors. Businesses that prioritize eco-friendly practices are more likely to build long-lasting relationships with customers, attract eco-conscious investors, and differentiate themselves in an increasingly competitive market.
13. Case Study: Real-World Impact of Automated Steel Coil Packaging
To illustrate the tangible benefits of automated coil packaging systems, let’s consider a real-world case study. A steel manufacturer implemented a fully automated steel coil packaging system, integrating automated wrapping, strapping, and palletizing machines.
Before automation, the company struggled with inconsistent packaging, leading to high material waste and frequent coil damage during shipping. By switching to an automated system, they reduced their plastic film usage by 25%, minimized strapping errors, and increased their packaging speed by 40%.
In addition to these material savings, the manufacturer also saw a significant decrease in transportation costs due to more efficient palletizing. By optimizing the packaging process, they could fit 15% more coils onto each truck, reducing the number of shipments required and lowering their overall carbon emissions.
This case study highlights the significant impact that automation can have, not only in terms of cost savings but also in reducing environmental impact and improving operational efficiency.
Conclusion
As the demand for sustainable practices continues to grow, the steel industry must adopt eco-friendly solutions in every aspect of its operations—including packaging. Automated packaging systems offer a clear path forward, providing numerous benefits that reduce resource waste, lower energy consumption, and improve packaging consistency.
From reducing plastic and strapping waste to optimizing energy use and transportation efficiency, automation is transforming the way steel coils are packaged. By investing in automation, companies not only contribute to a greener future but also improve their bottom line through cost savings and operational efficiency.
As we move forward, it’s clear that automation will continue to play a vital role in helping the steel industry achieve its sustainability goals while maintaining high-quality packaging standards. Businesses that embrace these innovations now will be well-positioned to lead in both environmental stewardship and competitive advantage.