How Automated Steel Coil Packing Reduces Downtime and Ensures Stability
- How Automated Steel Coil Packing Reduces Downtime and Ensures Stability
- 1. The Need for Automation in Steel Coil Packing
- 2. Downtime: A Major Challenge in Steel Manufacturing
- 3. How Automated Steel Coil Packing Reduces Downtime
- 4. Enhancing Stability in Steel Coil Packing
- 5. Key Components of Automated Steel Coil Packing Lines
- 6. How Automated Packing Systems Ensure Consistency and Quality
- 7. The Long-Term Benefits of Automated Steel Coil Packing
- Conclusion
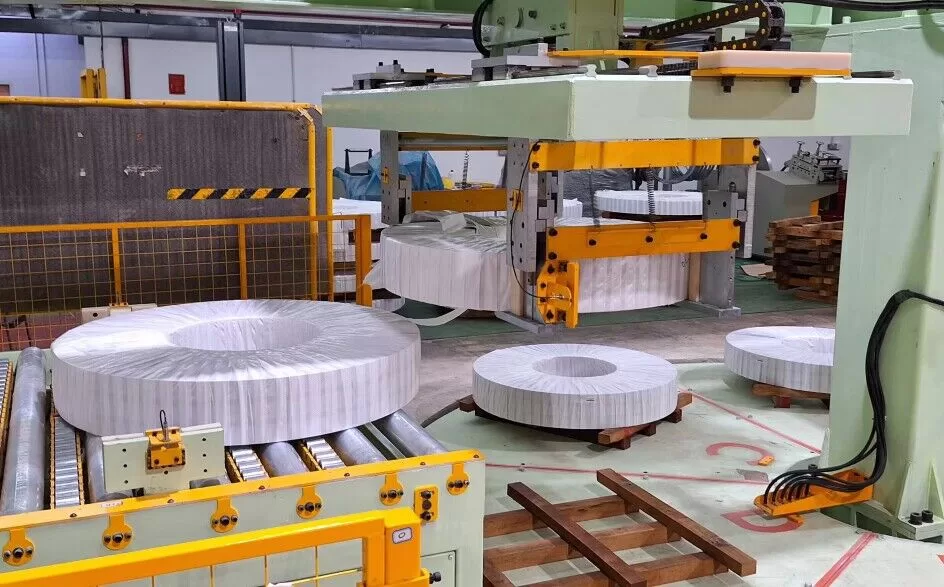
In the steel manufacturing industry, operational efficiency and stability are critical to maintaining high production levels and meeting customer demands. One of the most important aspects of maintaining this efficiency is the packaging process, specifically for steel coils. Downtime in this sector can be costly, and ensuring the stability of packed coils is essential to prevent damage during storage or transportation. This article explores how automated steel coil packing systems significantly reduce downtime, enhance production flow, and ensure the stability of packed coils, offering manufacturers a competitive edge in the market.
1. The Need for Automation in Steel Coil Packing
Steel coil packaging has traditionally been a manual, labor-intensive process that requires significant manpower and is prone to human error. Manual operations not only slow down the production process but also introduce inconsistencies in the quality of the packaging, which can lead to coil damage during handling and transportation.
Automation in steel coil packing addresses these challenges head-on. By automating the process, manufacturers can increase speed, reduce human error, and ensure that each coil is packed consistently and securely. Automated systems allow for continuous operation without the need for human intervention, which drastically reduces operational delays and ensures that production runs smoothly and efficiently.
2. Downtime: A Major Challenge in Steel Manufacturing
Downtime, whether planned or unplanned, is one of the most significant challenges faced by steel manufacturers. Unplanned downtime can occur due to machine breakdowns, human error, or inefficiencies in the packing process, leading to significant financial losses. Every minute of downtime equates to a reduction in overall productivity, delays in order fulfillment, and higher operational costs.
In manual packing systems, downtime is often caused by the need for breaks, manual adjustments, or errors that require repacking. Furthermore, the variability in worker skill levels can lead to inconsistencies, causing delays. Automated steel coil packing systems eliminate these issues by ensuring that the packing process runs continuously and efficiently, without the need for constant manual intervention. This leads to a significant reduction in downtime and increases overall production throughput.
3. How Automated Steel Coil Packing Reduces Downtime
Automated steel coil packing systems are designed to operate continuously, allowing for seamless integration with the rest of the production line. Here are the key ways automation reduces downtime:
- Continuous Operation: Unlike manual systems, which require frequent stops for rest or adjustments, automated systems can run 24/7 without interruption. This ensures that the packing process keeps pace with production, preventing bottlenecks.
- Quick Setup and Transitions: Automated systems are equipped with programmable settings that allow for quick adjustments to coil sizes and packing requirements. This reduces the time spent transitioning between different coil dimensions and ensures that the packing process flows smoothly.
- Real-Time Monitoring: Advanced automation systems include sensors and diagnostic tools that monitor the performance of the packing line in real-time. Any issues, such as misaligned coils or material shortages, are detected immediately, allowing for rapid resolution without prolonged downtime.
By automating these key processes, manufacturers can significantly reduce idle time, ensure higher throughput, and maintain consistent product quality.
4. Enhancing Stability in Steel Coil Packing
The stability of packed steel coils is critical to ensuring that they remain undamaged during storage and transportation. Improperly packed coils are prone to shifting, which can lead to deformations, scratches, or even breaks in the material. Automated steel coil packing systems ensure stability through precise, consistent packing techniques that eliminate these risks.
- Precision Wrapping: Automated wrapping machines apply stretch film or protective materials uniformly across the coil’s surface. The system controls the tension and overlap rate, ensuring that the material is applied securely, preventing movement within the packaging.
- Consistent Strapping: Automated strapping ensures that each strap is applied with the correct tension and in the right position. This consistency prevents the coil from loosening during transportation, maintaining its shape and integrity.
By maintaining uniformity in wrapping and strapping, automated systems help reduce the risk of damage to the coils, which in turn reduces the likelihood of product returns or reworks, both of which can add to downtime.
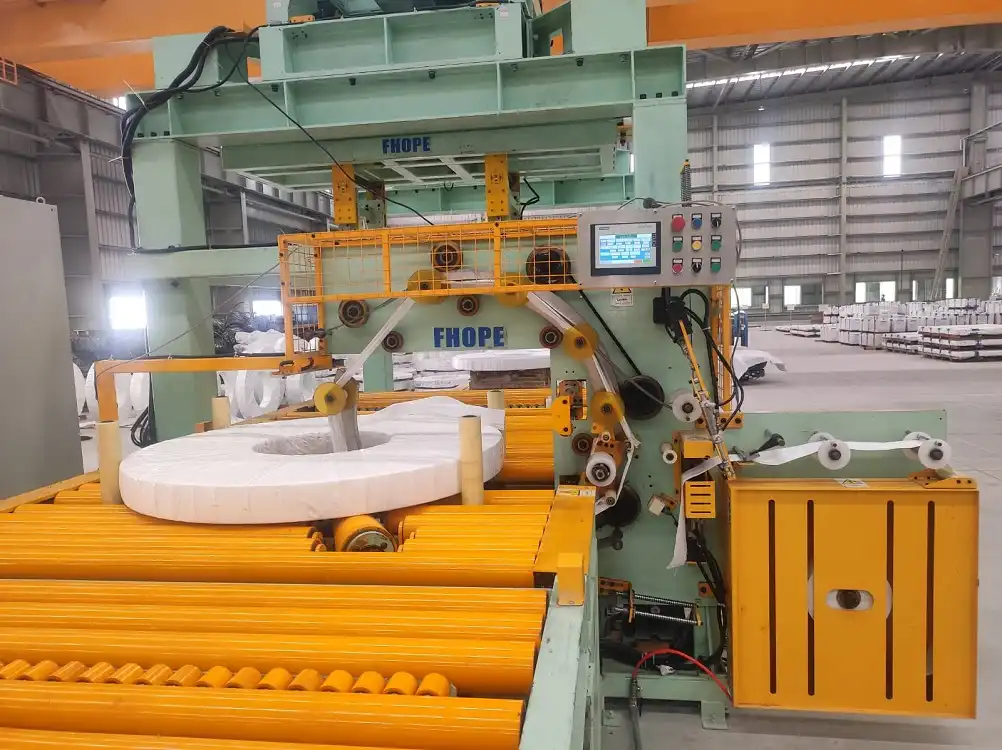
5. Key Components of Automated Steel Coil Packing Lines
Automated steel coil packing lines are composed of several essential components, each designed to contribute to reducing downtime and improving packing stability. These components work in tandem to streamline the packing process and ensure consistent, high-quality results:
- Turnstiles: These devices hold multiple coils, allowing for efficient loading and reducing the need for cranes to handle each coil individually. The turnstile can rotate to present the next coil in line for packing, speeding up the process.
- Coil Down-Enders: These machines lift and rotate the coil to the correct orientation for packing, ensuring that it is stable throughout the wrapping and strapping process.
- Conveyor Systems: Automated conveyors transport coils between different packing stages, reducing the need for manual handling and speeding up the movement of products through the packing line.
- Strapping Machines: Automated strapping systems apply steel or plastic straps to secure the coils, ensuring that each coil is tightly bound and stable during transport.
- Wrapping Machines: These systems wrap the coils with protective materials such as stretch film, ensuring that the coils are shielded from moisture, dust, and other environmental factors.
Together, these components form an integrated system that enhances the speed, accuracy, and stability of steel coil packing.
6. How Automated Packing Systems Ensure Consistency and Quality
One of the primary benefits of automation is the consistency it brings to the packing process. Manual packing is subject to human error, which can result in improperly secured coils. This inconsistency can lead to coils being damaged during transport or requiring rework, both of which can cause delays.
Automated systems eliminate this variability by using pre-programmed parameters to control the packing process. This ensures that each coil is wrapped and strapped with the same precision, regardless of size or weight. Automated systems also maintain consistent tension levels in strapping and wrapping, ensuring that every coil is packed to the same high standard.
By ensuring uniformity in the packing process, automation not only reduces the likelihood of coil damage but also enhances customer satisfaction by delivering consistently well-packed products.
7. The Long-Term Benefits of Automated Steel Coil Packing
While the initial investment in an automated steel coil packing system may seem substantial, the long-term benefits far outweigh the costs. Here are some of the key advantages:
- Increased Productivity: Automated systems run continuously and efficiently, allowing manufacturers to increase their production output without adding extra labor.
- Lower Labor Costs: By reducing the need for manual labor, manufacturers can lower their staffing costs while also minimizing the risk of injuries related to heavy lifting or repetitive tasks.
- Reduced Material Waste: Automated systems are programmed to use the exact amount of packing material needed for each coil, reducing waste and saving costs on materials.
- Improved Safety: Automation minimizes human interaction with heavy coils, reducing the risk of accidents and improving overall workplace safety.
Conclusion
In today’s competitive steel industry, reducing downtime and ensuring the stability of packed products are critical to maintaining high levels of productivity and customer satisfaction. Automated steel coil packing systems offer a solution that not only reduces downtime but also improves the quality and consistency of packing, ensuring that each coil is protected and stable during transportation.
By investing in automation, manufacturers can future-proof their operations, reduce costs, and maintain a competitive edge in the market. Automated systems are no longer just an option but a necessity for manufacturers looking to maximize efficiency, safety, and product quality in their steel coil packing processes.