How Automated Packing Lines Meet the Growing Demands of the Steel Industry
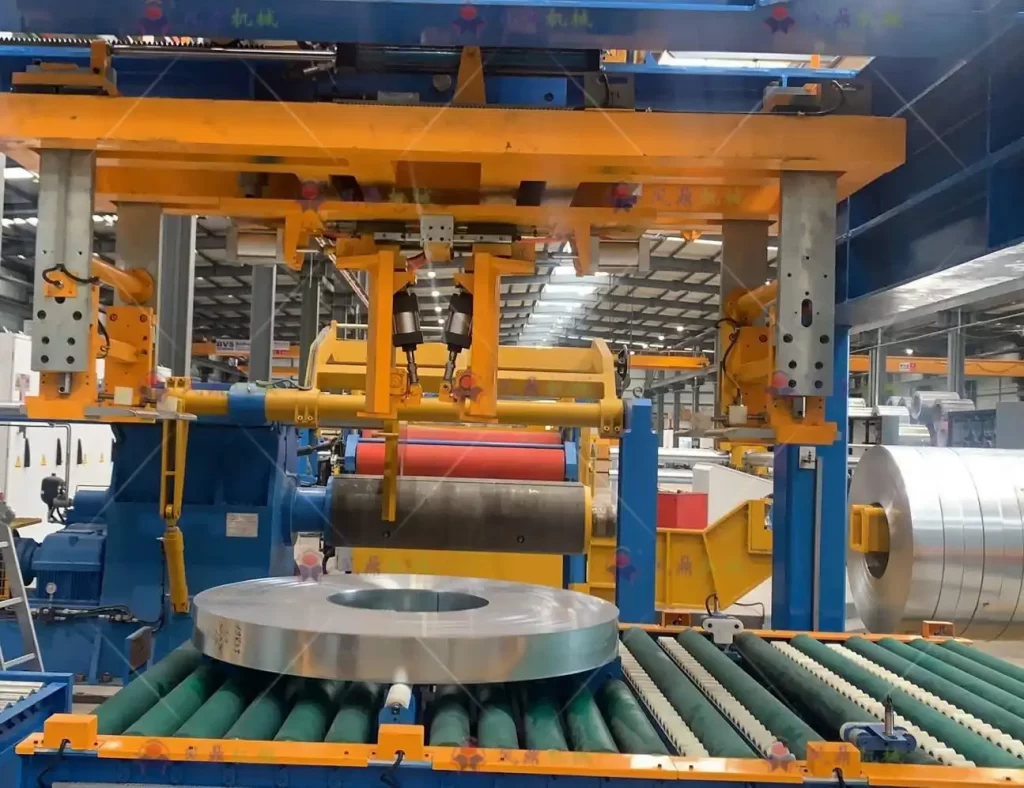
As the steel industry continues to expand and evolve, so do the demands placed on its operations. Efficiency, precision, and safety are now more critical than ever. One of the most significant advancements in recent years is the implementation of automated packing lines. These systems have revolutionized the way steel products, especially steel coils, are handled and packed, offering solutions that meet the increasing challenges of the industry. In this article, we’ll explore how automated packing lines help the steel industry cope with growing demands, reduce costs, and improve overall performance.
1. The Rising Demand for Efficiency in Steel Packing
The steel industry is a cornerstone of global infrastructure, producing millions of tons of steel every year. However, this growth comes with mounting pressure on manufacturers to increase productivity without sacrificing quality. Manual packing systems, once standard, are now seen as bottlenecks in production processes. With automated packing lines, steel manufacturers can meet demand more efficiently. These machines work continuously, ensuring the fast, precise packing of products, reducing downtime, and eliminating the human errors associated with manual packing.
Efficiency isn’t just about speed—it’s about maintaining consistent quality across all packaging operations. Automated systems guarantee uniform wrapping, strapping, and securing, which is crucial for steel products that are often heavy, bulky, and require specific handling techniques.
2. Meeting Stringent Safety Requirements
Safety in the workplace, especially in industries as hazardous as steel production, is non-negotiable. The process of packing steel coils, sheets, or bars manually can be dangerous, with risks ranging from cuts to more severe injuries caused by lifting heavy objects or improper handling. Automated packing lines drastically reduce the likelihood of accidents.
With robotic arms, conveyors, and other mechanized systems, these machines handle the heavy lifting, wrapping, and strapping of steel products, keeping workers at a safe distance from potentially harmful processes. This not only ensures compliance with Occupational Safety and Health Administration (OSHA) standards but also fosters a safer working environment, reducing the overall cost related to worker injuries and compensation claims.
3. Addressing the Challenge of Customization
One of the core strengths of automated packing lines is their ability to adapt to different product sizes and types. In the steel industry, products range from large steel coils to smaller, more delicate items like steel rods or bars. Manually adjusting packaging techniques for each type is inefficient and prone to errors.
Modern automated packing systems come equipped with smart sensors and programmable settings that allow manufacturers to adjust the machine for different products easily. Whether it’s wrapping a small diameter coil or a larger bundle, these systems can be tailored to ensure each product is packed securely and in accordance with customer specifications. This flexibility allows companies to scale operations as demand fluctuates, ensuring they’re always prepared to meet market needs.

Get Your Best Solution !
4. Reducing Labor Costs and Boosting Productivity
Labor costs are a significant concern for many steel manufacturers. Manual packing operations require a substantial workforce, which can be expensive and inefficient. Automated packing lines reduce the reliance on manual labor by handling repetitive tasks quickly and consistently. This allows businesses to reallocate human resources to more value-added tasks, such as quality control, machine maintenance, or customer service.
By automating the packing process, companies can also increase productivity. With faster packing times and 24/7 operational capability, automated systems can keep production lines running smoothly even during off-hours or high-demand periods. This level of productivity not only meets customer deadlines but also improves profitability by reducing labor-related overhead.
5. Improving Product Protection and Minimizing Damage
When it comes to steel products, especially coils and bars, protection during shipping and storage is critical. Improper packaging can lead to significant losses due to product damage, whether from rust, dents, or deformation during transit. Manual packing can sometimes result in inconsistent packaging, where products may not be securely wrapped or strapped.
Automated packing lines use precise tension control, ensuring that steel products are tightly wrapped and secured. This precision minimizes the risk of surface damage or scratches and reduces the chances of products shifting during transport. Furthermore, many automated systems come equipped with protective material feeders that automatically apply protective layers, such as plastic wraps or anti-rust coatings, adding an extra layer of defense against environmental factors.
6. Future-Proofing Steel Manufacturing Operations
As the steel industry continues to evolve, so too must its operations. Automation is not just a trend—it’s the future of manufacturing. By investing in automated packing lines, steel manufacturers are effectively future-proofing their operations. These systems are designed to be upgradable, meaning they can evolve alongside advancements in technology.
As Industry 4.0 technologies such as the Internet of Things (IoT), artificial intelligence (AI), and data analytics become more integrated into manufacturing processes, automated packing lines will be able to leverage these technologies to offer even greater efficiencies. For example, AI-driven systems can predict when maintenance is needed, reducing unplanned downtime. IoT-enabled sensors can provide real-time data on machine performance, allowing operators to make informed decisions quickly.
By embracing automation, steel manufacturers are positioning themselves to meet future demands, not only in terms of output but also in terms of environmental responsibility, as many automated systems are designed to reduce waste and energy consumption.
Conclusion
The demands of the steel industry are ever-growing, but with automated packing lines, manufacturers are better equipped to meet these challenges head-on. From improving efficiency and safety to reducing costs and enhancing product protection, automation offers a host of benefits that manual processes simply can’t match. As technology continues to evolve, automated packing systems will only become more integral to the steel industry’s success.
For manufacturers looking to stay competitive and future-proof their operations, investing in automated packing lines is not just an option—it’s a necessity. The transition to automation is the key to maintaining operational excellence, reducing waste, and ultimately meeting the growing demands of both the market and the industry.
By implementing these solutions, the steel industry will continue to thrive, delivering high-quality products while ensuring safety and efficiency across the board.

Get Your Best Solution !