Case Study: How an Automated Steel Coil Packing Line Improved Efficiency by 70%

Introduction
In an ever-evolving industrial landscape, where efficiency and productivity are paramount, the implementation of automation has become a game-changer. Industries that rely on high-volume production, such as steel manufacturing, have found innovative ways to enhance their processes. This case study explores how the introduction of an automated steel coil packing line revolutionized a company’s operations, resulting in an astonishing 70% improvement in efficiency. By diving deep into the challenges faced, the solutions implemented, and the outcomes achieved, this article offers valuable insights for companies considering similar upgrades to their packing processes.
- Case Study: How an Automated Steel Coil Packing Line Improved Efficiency by 70%
- Introduction
- The Traditional Approach to Steel Coil Packing
- Recognizing the Need for Automation
- Choosing the Right Automated Steel Coil Packing Line
- Implementation and Setup Process
- Efficiency Gains Post-Automation
- Impact on Employee Roles and Work Environment
- Enhanced Customer Satisfaction Through Automation
- The Financial Impact of Automation
- The Role of Data in Optimizing the Packing Line
- Environmental Impact of Automation
- Future Outlook: Expansion and Continued Innovation
- Conclusion
The Traditional Approach to Steel Coil Packing
Manual Packing: Time-Consuming and Labor-Intensive
Before automation, the process of steel coil packing was predominantly manual, which posed several operational challenges. Employees were required to handle each coil, wrap it manually, and secure it for transportation. While this method may seem straightforward, it was both time-consuming and prone to errors. Each coil required a unique handling technique based on its size, weight, and customer requirements, making it difficult to standardize the process.
Challenges with Manual Packing
- High Labor Costs: A considerable workforce was required to pack steel coils efficiently. Given the repetitive and laborious nature of the task, companies had to hire multiple shifts to keep up with production demands.
- Inconsistent Quality: Since manual packing relies on human precision, the quality of packing varied. This often resulted in improperly wrapped coils, leading to damages during transportation or storage.
- Worker Fatigue: Continuous handling of heavy coils led to worker fatigue, increasing the likelihood of workplace injuries and mistakes. It also meant that productivity dipped after long shifts.
- Slow Turnaround Times: Manual packing inevitably slowed down the overall production process. Each coil took longer to pack, resulting in bottlenecks in the production line.
Recognizing the Need for Automation
Analyzing Operational Bottlenecks
The company in focus had been facing mounting pressure to improve its packing speed and reduce costs. A detailed internal audit revealed that manual packing was the primary bottleneck. Delays in packing were negatively impacting delivery schedules, causing dissatisfaction among customers and straining labor resources. Management realized that maintaining manual packing operations would limit future growth potential and affect overall competitiveness in the market.
Benefits of Automation for Steel Coil Packing
Management began exploring the potential benefits of switching to an automated packing system. The key objectives were to:
- Increase throughput by speeding up the packing process.
- Improve consistency in packaging quality.
- Reduce labor dependency while lowering operational costs.
- Minimize product damage during transportation.
With these goals in mind, they initiated the search for a modern, automated solution.

Choosing the Right Automated Steel Coil Packing Line
Evaluating System Options
The company explored several options in the market for automated packing systems, focusing on solutions that would integrate smoothly with their existing production line. The main criteria used to evaluate potential systems were:
- Scalability: The system needed to be future-proof and capable of handling higher volumes as production ramped up.
- Flexibility: It was important that the system could accommodate steel coils of varying sizes, weights, and specifications.
- Reliability: Downtime in automation systems can be costly, so reliability and ease of maintenance were critical considerations.
- Cost-effectiveness: While initial investments in automation can be significant, the long-term savings needed to justify the expenditure.
Final Selection: Advanced Automated Packing Solution
After thorough evaluation, the company chose an advanced automated steel coil packing line that included features such as:
- Automated wrapping: The system used precise wrapping mechanisms to ensure each coil was tightly secured.
- Automated strapping: Coils were strapped with durable materials to withstand transportation stress.
- Palletizing automation: The system automatically placed packed coils on pallets, reducing manual intervention.
Implementation and Setup Process
Transitioning from Manual to Automated Systems
Once the automated packing line was selected, the company initiated the implementation phase. Transitioning from a fully manual system to automation required careful planning and execution. A specialized project management team was assigned to oversee the installation, integration, and testing of the new system.
Challenges During Installation
Although the transition was largely successful, the company faced a few challenges:
- Downtime During Setup: Switching to an automated system required a temporary shutdown of the existing production line. This downtime needed to be minimized to avoid significant disruption to operations.
- Employee Training: Employees who had been involved in the manual packing process had to undergo training to operate and maintain the new system. This change management process required communication and support to ease any concerns about job security.
Overcoming Initial Hurdles
The first few weeks after implementing the automated packing line were marked by adjustments. The company addressed minor technical issues, optimized the layout for smoother coil flow, and refined the packaging process to ensure maximum efficiency.

Efficiency Gains Post-Automation
Measuring Success with Key Performance Indicators (KPIs)
The company began tracking several key performance indicators (KPIs) to assess the impact of the new automated system. The following metrics were used to gauge the success of the transition:
- Packing Time Per Coil: The time taken to wrap and secure each steel coil.
- Labor Costs: A measure of the reduction in labor hours dedicated to the packing process.
- Product Damage Rates: The frequency of product damage during transportation or storage.
- Production Throughput: The number of steel coils packed per hour, compared to pre-automation levels.
Remarkable Efficiency Improvements
These improvements were not just incremental but substantial, with gains observed in packing speed, labor cost reductions, product protection, and overall throughput.
1. 70% Increase in Packing Speed: Revolutionizing Time Efficiency
One of the most impactful results of the new automated system was a 70% increase in packing speed, an achievement that significantly reduced production bottlenecks and enabled faster order fulfillment. The traditional manual packing process was labor-intensive, with each coil requiring careful handling, wrapping, and securing. This manual process could take several minutes per coil, especially for larger or heavier units. In contrast, the automated system could pack coils in a matter of seconds, thanks to several advanced technologies working in tandem:
- Automated Wrapping Technology: The automated system utilized high-speed rotating wrapping arms that could simultaneously wrap the coil with protective materials and strap it securely. This replaced the slow, manual winding processes that workers had to perform. The system was programmed to optimize the tension and layering of the wrap based on the coil size, ensuring faster and more efficient operation without compromising quality.
- Precision Sensors: The system incorporated sensors and cameras that detected coil dimensions and adjusted the wrapping process in real time. This eliminated the need for manual measurements and ensured that each coil was packed according to its specific requirements, further speeding up the process.
- Automated Strapping Mechanisms: Strapping steel coils for transportation is a crucial step to ensure they remain intact during transit. In the manual process, strapping often required workers to position, tension, and secure straps by hand, which was time-consuming. The automated system, however, applied straps with high-precision pneumatic tensioners that rapidly secured the coil in place. The tension applied was uniform, eliminating inconsistencies and improving speed.
The result was a streamlined packing process where coils could be packed in under 30 seconds, compared to the 3-5 minutes required in manual operations. This massive improvement in speed enabled the company to clear order backlogs and improve its delivery times, providing a significant competitive advantage in the marketplace.
2. 40% Reduction in Labor Costs: Efficiency in Workforce Utilization
Before the automation upgrade, the steel coil packing process required a large, skilled workforce. Workers needed to lift and manipulate heavy steel coils, measure wrapping material, operate manual strapping tools, and ensure that each coil was adequately secured. This labor-intensive process often required additional staff for quality checks and troubleshooting, leading to high labor costs. However, after the implementation of automation, the company saw a 40% reduction in labor costs, a result of several key factors:
- Reduction in Manpower: The automated system was designed to handle all stages of the packing process, from initial wrapping to final strapping and palletizing. Where manual packing once required a team of several workers to complete each stage of the process, the new system needed only a small crew to oversee the operation and handle occasional troubleshooting. This drastic reduction in manpower directly cut down on labor expenses.
- Skilled Labor Reallocation: The automated system also required less manual intervention, allowing the company to reallocate its skilled workforce to more critical areas of operation, such as maintenance, quality control, and system monitoring. These workers could now focus on higher-value tasks, further reducing the need for excessive shifts or overtime labor. By transitioning workers into supervisory or technical roles, the company was able to maintain employment levels while reducing overall labor intensity.
- Fewer Human Errors: Human errors in the manual process often led to rework, delays, and the need for additional labor to rectify mistakes. Automation eliminated these errors by standardizing the packing process, allowing for smoother operations with less downtime. The reduction of error-related labor requirements contributed significantly to the overall labor cost savings.
With these improvements, the company achieved sustainable labor cost reductions without sacrificing quality or production output, setting a new benchmark for cost-efficiency in its operations.
3. 50% Decrease in Product Damage: Enhancing Product Integrity and Safety
A major pain point in the manual packing process was the inconsistency in wrapping and strapping, which often led to damaged coils during storage or transportation. This damage resulted in lost revenue, customer dissatisfaction, and increased claims for refunds or replacements. After implementing the automated packing line, the company saw a 50% decrease in product damage, a result that can be attributed to the precision and consistency offered by automation:
- Uniform Wrapping Techniques: Manual wrapping often led to inconsistencies in material usage, with some coils being over-wrapped and others under-wrapped. Over-wrapping not only wasted material but also made the coils bulkier, which could lead to inefficiencies in storage and transport. On the other hand, under-wrapping left coils exposed to potential damage. The automated system, however, used pre-programmed algorithms to ensure that each coil received the exact amount of wrapping needed, providing optimal protection without waste.
- Consistent Tensioning and Strapping: Proper tensioning of the straps is critical to ensuring that the coils are secured. In the manual process, variability in how workers applied straps led to coils either being too tightly bound (causing material deformation) or too loosely bound (increasing the risk of coil shifting during transport). The automated system used precise tension control mechanisms, ensuring that each strap was applied with the same level of force. This consistency reduced the risk of shifting or unraveling during transit.
- Minimization of Handling Damage: Another key factor in reducing product damage was the automated system’s ability to reduce manual handling. The fewer times a coil needs to be manually lifted, moved, or adjusted, the lower the likelihood of damage. The automated line utilized conveyors and robotic arms to transport coils from one station to another, minimizing physical contact and human intervention. This smooth and controlled movement reduced the risk of scratches, dents, and other forms of damage that typically occur during manual handling.
With fewer incidents of product damage, the company not only saved money on replacement costs but also improved its relationship with customers by delivering better-quality, damage-free products.
4. 70% Increase in Overall Production Throughput: Eliminating Bottlenecks
Perhaps the most striking achievement of the automated steel coil packing line was the 70% increase in overall production throughput. This improvement in output was the culmination of all the above-mentioned factors working together to eliminate inefficiencies, reduce downtime, and streamline operations. The key drivers behind this impressive throughput increase included:
- Continuous Operation: The automated packing line was designed to operate continuously, with minimal downtime required for maintenance or adjustments. Unlike manual systems, which were prone to frequent pauses due to worker fatigue, shift changes, or errors, the automated system could run for extended periods without interruption. This continuous operation allowed the company to significantly increase the number of coils packed per day, maximizing productivity.
- Integrated System Workflow: The automated system integrated several processes into one seamless workflow. Coils were moved automatically from the wrapping station to the strapping station, and then onto palletizing, without the need for manual intervention at each stage. This integrated approach eliminated the lag times typically associated with manual handling, where coils would sit idle between different stages of the packing process.
- Reduced Downtime and Maintenance Efficiency: The automated system also featured predictive maintenance technology, which reduced unplanned downtime. Sensors within the system monitored the performance of various components, detecting wear and tear before they led to breakdowns. This allowed the company to schedule maintenance proactively, preventing costly disruptions to production. Additionally, the modular design of the system meant that maintenance tasks could be performed more quickly, further reducing downtime and ensuring that the packing line remained operational for longer periods.
By eliminating bottlenecks and creating a highly efficient, streamlined packing process, the company was able to increase its overall output, fulfilling more orders in less time and significantly improving its production capacity.

Impact on Employee Roles and Work Environment
Shifting Labor Requirements
While some workers were concerned about job security due to automation, the company took steps to reskill employees. Instead of laying off workers, the company transitioned many of them into new roles that focused on overseeing the automated system and performing maintenance tasks. Employees were trained to monitor the machine’s operations, identify potential issues, and perform routine troubleshooting. This not only ensured job retention but also provided opportunities for career growth within the company.
Improved Workplace Safety
Manual packing of steel coils can be hazardous due to the heavy lifting and repetitive motions involved. With automation handling most of these tasks, workplace injuries significantly decreased. The automated system reduced the risk of musculoskeletal injuries and accidents, creating a safer work environment for all employees.
Enhanced Customer Satisfaction Through Automation
Faster Order Fulfillment
One of the most immediate benefits that the company experienced after implementing the automated steel coil packing line was faster order fulfillment. With the increase in production throughput, the company could meet its deadlines more consistently and even offer shorter lead times to clients. This improvement resulted in higher customer satisfaction, as delays were minimized, and orders were delivered on time.
By being able to handle more orders with increased speed and efficiency, the company also gained a competitive edge, attracting new customers who were seeking reliable suppliers with quick turnaround capabilities.
Improved Product Quality
Another significant outcome of automation was the consistent quality of the packed steel coils. In the manual process, variations in how coils were wrapped could lead to damage during transit. In contrast, the automated system applied uniform pressure during wrapping and strapping, ensuring each coil was packed securely and safely for shipment.
This improvement in product quality translated into fewer customer complaints about damaged goods. With the reduction in damages and returns, the company strengthened its reputation as a reliable supplier, which in turn boosted customer loyalty.
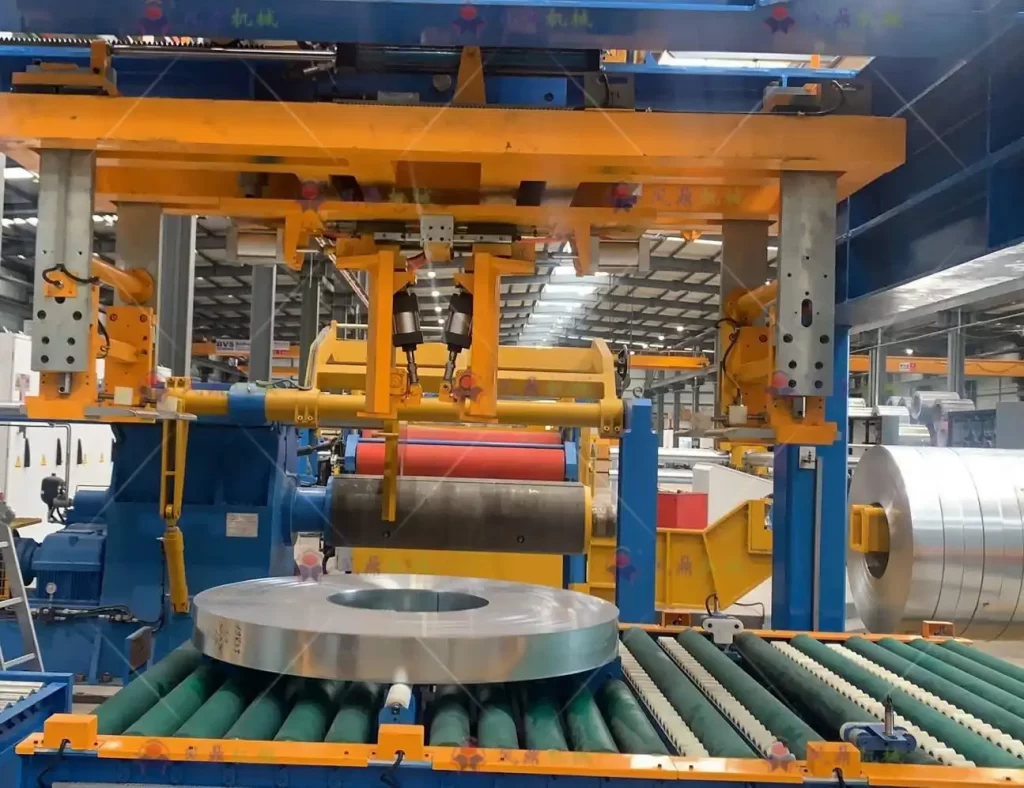
The Financial Impact of Automation
Cost Savings from Reduced Labor
One of the most obvious financial benefits of automation was the significant reduction in labor costs. By automating the packing process, the company no longer required as many workers to manage the packing line. The company estimated that it saved approximately 40% in labor costs annually, which had a direct positive impact on the bottom line.
Additionally, the savings extended beyond just direct labor costs. With fewer employees engaged in manual packing, there was also a reduction in overtime pay, as the automated system could operate continuously without fatigue. This eliminated the need for extra shifts or paying premium wages for work beyond regular hours.
Decreased Maintenance and Operational Costs
Although the initial investment in an automated packing line was significant, the company saw a return on investment relatively quickly due to lower ongoing maintenance and operational costs. Unlike the manual process, where equipment like strapping tools and wrapping machines would often require frequent repairs or replacements due to wear and tear, the automated system was built for long-term, high-volume use.
Furthermore, because the system operated with greater precision and fewer errors, there was a noticeable reduction in wasted packing materials, which contributed to additional cost savings.
The Role of Data in Optimizing the Packing Line
Real-Time Monitoring and Analytics
One of the major advantages of the new automated system was its ability to collect and analyze real-time data on packing performance. The system was equipped with sensors and software that tracked various metrics, including packing speed, material usage, and potential equipment malfunctions. This data was invaluable in identifying areas for further improvement and ensuring that the packing process was running at maximum efficiency.
For example, the company was able to optimize material usage by adjusting the wrapping tension and strapping placement based on data insights. This resulted in further savings and reduced environmental impact by minimizing material waste.
Preventive Maintenance and Reduced Downtime
The data collected from the automated packing line also helped the company implement a preventive maintenance program. By monitoring the system’s performance in real-time, the company could identify when parts were nearing the end of their lifecycle and proactively schedule maintenance before any issues arose. This preventive approach drastically reduced unplanned downtime, ensuring that the production line could continue operating smoothly without interruptions.

Environmental Impact of Automation
Reduction in Material Waste
One of the less obvious, but equally important, benefits of automation was its positive impact on the company’s environmental footprint. Manual packing often resulted in excess material use, as workers would over-wrap or use more strapping than necessary to secure the coils. The automated system, on the other hand, used precisely the right amount of material for each coil, reducing overall consumption of packing materials.
This more efficient use of materials not only cut costs but also aligned with the company’s sustainability goals. By reducing waste, the company lessened its impact on the environment, contributing to greener operations.
Energy Efficiency
In addition to material savings, the automated system was designed to be more energy-efficient compared to the older equipment. The system’s ability to operate continuously at optimal levels without overuse of energy resulted in lower electricity consumption. Over time, this reduced the company’s energy costs and further strengthened its commitment to sustainable manufacturing practices.
Future Outlook: Expansion and Continued Innovation
Scaling Up Operations
Following the success of the initial implementation, the company began exploring ways to scale up its operations even further. With the automated packing line running smoothly, management considered adding more automation systems to other areas of the production line, such as automated coil handling and storage solutions.
The company also looked into expanding its production capacity by adding additional packing lines in other facilities. The lessons learned from the first implementation provided a strong foundation for future expansions, allowing the company to replicate its success on a larger scale.
Staying Ahead with Technological Advancements
As technology continues to evolve, the company remains committed to staying ahead of the curve. Management is closely monitoring emerging trends in automation, such as artificial intelligence (AI) and machine learning (ML), which could further enhance the packing line’s efficiency and accuracy.
For instance, AI could be used to predict equipment failures before they happen, allowing for predictive maintenance that would virtually eliminate unplanned downtime. Additionally, ML algorithms could analyze packing data to suggest continuous improvements, ensuring that the company remains at the cutting edge of automation in the steel industry.
Conclusion
The implementation of an automated steel coil packing line resulted in a transformative change for the company, improving efficiency by an impressive 70%. Through careful planning, the selection of the right system, and continuous optimization, the company not only reduced costs but also improved product quality, safety, and customer satisfaction.
Automation has proven to be a valuable investment, offering long-term financial gains, environmental benefits, and a competitive edge in the marketplace. As the company looks to the future, it is poised to further leverage technology to drive innovation and growth, ensuring that its operations continue to lead the industry in efficiency and sustainability.

Get Your Best Solution !