Optimizing Coil Packaging: Selecting and Customizing Hose and Cable Wrapping Machines
Efficiently packaging hose and cable coils is critical for protecting products during transit and storage, optimizing material usage, and improving overall operational throughput. Manual wrapping methods are often inconsistent, labor-intensive, and can lead to product damage or excessive material consumption. Investing in a specialized coil wrapping machine, particularly one customized to your specific needs, offers a robust solution. This guide details the key considerations for selecting and tailoring an orbital wrapping machine for hose and cable coil applications, ensuring secure packaging and a strong return on investment.
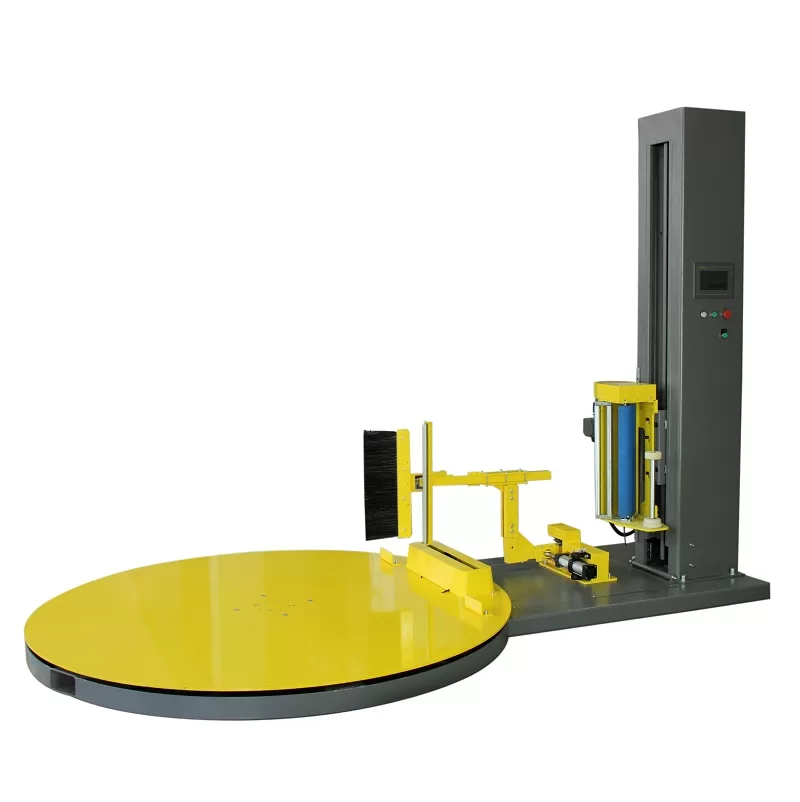
Why Specialized Wrapping is Essential
Automated coil wrapping machines, primarily orbital wrappers for these applications, offer significant advantages over manual methods:
- Consistency: Ensures uniform wrap tension and coverage for every coil.
- Speed: Dramatically increases packaging throughput compared to manual labor.
- Material Savings: Precise control and film pre-stretch capabilities reduce consumable usage.
- Product Protection: Provides superior protection against dust, moisture, and handling damage.
- Labor Optimization: Frees up personnel for higher-value tasks.
Defining Your Application Requirements: The Foundation for Customization
Before exploring machine options, a thorough assessment of your specific operational needs is paramount. This analysis forms the basis for effective customization:
Coil Specifications
Document the range of coils you need to wrap:
- Dimensions: Minimum and maximum Outer Diameter (OD), Inner Diameter (ID), and width/height.
- Weight: Minimum and maximum coil weight.
- Material & Form: Hose type (hydraulic, industrial), cable type (power, data), coil density, susceptibility to deformation.
- Stacking: Will coils be wrapped individually or in stacks?
Production Throughput Needs
Determine the required packaging rate:
- Volume: Coils per hour, per shift, or per day.
- Cycle Time: Target time to wrap a single coil or stack.
Operating Environment
Consider the machine's placement:
- Space: Available floor space, ceiling height constraints.
- Conditions: Temperature fluctuations, humidity levels, presence of dust or debris.
Packaging Goals
Define the desired outcome:
- Protection Level: Standard dust/moisture protection, heavy-duty protection for export, corrosion prevention (requiring VCI materials).
- Presentation: Requirements for retail display or branding.
- Unitization: Wrapping multiple coils together for stability.
pallet stretch wrap 3 Understanding Orbital Wrapping Technology
Orbital wrappers are ideal for coils as they pass a roll of packaging material (typically stretch film) through the center of the coil and around the outside as the coil is rotated or indexed. Key components influencing customization include:
- Wrapping Ring: Carries the film roll dispenser. Its diameter must accommodate your largest coil OD. Ring speed impacts throughput.
- Film Delivery System: Applies the wrapping material. This is a critical area for customization.
- Conveyor/Handling System: Moves coils into, through, and out of the wrapping station.
Key Machine Features for Customization
Tailoring the machine involves selecting and configuring specific components:
Ring Diameter and Speed
The ring must be sized appropriately for the largest coil diameter. Variable speed control allows adjustment for different coil sizes and desired wrap patterns, directly impacting cycle time.
Film Delivery System (Film Carriage)
- Pre-stretch: Crucial for maximizing film yield and load stability. Standard powered pre-stretch ratios (e.g., 150%, 200%, 250%) significantly reduce film costs. Adjustable pre-stretch offers flexibility.
- Tension Control: Ensures consistent film tension regardless of roll diameter, preventing coil deformation or loose wraps. Electronic tension control offers the most precision.
Automatic Film Cut and Clamp System
Automates the start and end of the wrap cycle, cutting the film tail and securing it. This boosts efficiency and enhances operator safety by eliminating manual intervention.
Conveyor and Handling Systems
- Type: Powered roller or belt conveyors are common. Consider options like V-rollers or specialized fixtures for unstable coils.
- Integration: Smooth transitions between existing lines and the wrapper are essential. Sensors for coil presence and positioning ensure proper wrapping initiation.
- Indexing/Rotation: Systems to automatically rotate the coil during wrapping for complete coverage.
pallet stretch wrap 4 Control Systems
- PLC/HMI: Programmable Logic Controllers (PLCs) with Human-Machine Interfaces (HMIs) offer flexibility and ease of use. Touch screens allow storing wrap recipes for different coil types, adjusting parameters (wrap counts, tension, speed), and accessing diagnostics.
Selecting the Right Wrapping Material
The choice of wrapping material directly impacts protection, cost, and sustainability:
Stretch Film Characteristics
- Gauge (Thickness): Determines puncture resistance and load containment.
- Cling: Ensures layers bond together. One-sided cling can prevent wrapped coils from sticking to each other.
- UV Resistance: Important if coils will be stored outdoors.
- Color/Opacity: Options for clear, opaque, or colored films for identification or security.
Alternative Materials
- VCI Film: Volatile Corrosion Inhibitor film protects ferrous and non-ferrous metals from rust during shipping and storage.
- Protective Paper/Foam: Can be applied concurrently with stretch film for surface protection against scratches or impacts.
Sustainable Options
Investigate films with recycled content or potentially biodegradable/compostable options, carefully verifying their performance characteristics and suitability for your application and disposal streams.
Integrating the Wrapper into Your Production Line
Seamless integration maximizes the benefits of automation:
Physical Integration
Ensure conveyor heights match upstream and downstream equipment. Plan for adequate infeed and outfeed accumulation space. Electrical and pneumatic connections must be properly planned.
Data and Automation
Consider integrating the wrapper with plant-level control systems (MES/SCADA) for:
- Performance Monitoring: Tracking throughput, film usage, and uptime.
- Remote Diagnostics: Facilitating troubleshooting and maintenance.
- Automated Recipe Selection: Linking production orders to specific wrapping parameters.
Safety and Compliance Standards
Operator safety is non-negotiable:
Operator Safety Features
- Guarding: Physical barriers and safety fencing to prevent access to moving parts during operation.
- Interlocking Doors: Automatically stop the machine if access gates are opened.
- Emergency Stops: Easily accessible E-stop buttons.
- Light Curtains: Safety devices that stop the machine if an operator breaks the light beam barrier.
Adhering to Standards
Ensure the machine complies with relevant safety standards, such as CE marking for Europe or adherence to OSHA guidelines concerning machine guarding in the United States. Reputable manufacturers will provide documentation of compliance.
Calculating the Return on Investment (ROI)
A customized wrapping machine is an investment. Justify it by calculating the potential ROI:
Quantifying Benefits
- Labor Savings: Reduced manual handling and wrapping time.
- Material Savings: Significant cost reduction through optimized film usage via pre-stretch.
- Reduced Product Damage: Consistent, secure wrapping minimizes damage during handling and transit.
- Increased Throughput: Faster packaging cycles meet higher production demands.
- Improved Safety: Reduced risk of repetitive strain injuries associated with manual wrapping.
Considering Total Cost of Ownership (TCO)
Factor in the initial purchase price, installation, training, ongoing maintenance, spare parts, and consumable costs for a complete financial picture. A well-customized, robust machine often yields a lower TCO over its lifespan despite potentially higher initial costs.
Conclusion: Strategic Investment for Optimal Packaging
Selecting and customizing a hose or cable coil wrapping machine requires careful consideration of your specific products, production environment, and packaging objectives. By thoroughly defining your requirements and working with experienced machine builders to tailor features like the film delivery system, controls, and handling components, you can implement an automated solution that delivers significant improvements in efficiency, product protection, and cost savings. This strategic investment enhances your packaging operation, ensuring coils are securely wrapped and ready for shipment or storage while contributing positively to your bottom line.