Optimizing Load Stability: Understanding Horizontal Wrapping Machines with Timber Blockers
Horizontal wrapping machines, often referred to as orbital wrappers, play a vital role in packaging long or bulky products. When dealing with loads prone to shifting or requiring enhanced stabilization, integrating a timber blocker into the process becomes essential. This guide explores the function, application, and considerations surrounding horizontal wrapping machines equipped with timber blockers.
What is a Horizontal Wrapping Machine with a Timber Blocker?
These specialized packaging machines are designed to apply stretch film around products moving horizontally along a conveyor. Unlike traditional turntable or rotary arm wrappers primarily used for palletized loads, horizontal wrappers are ideal for items like lumber, pipes, extrusions, doors, windows, and bundled materials.
The addition of a timber blocker addresses a specific challenge: preventing lengthwise movement or shifting of the product within the wrapped package, particularly during handling, storage, and transit.
The Critical Role of the Timber Blocker
The timber blocker, typically a piece of wood or similarly sturdy material, serves as a crucial bracing element. Its primary functions include:
- Load Stabilization: It provides a fixed point against which the product rests, significantly reducing the risk of longitudinal shifting.
- Preventing Internal Movement: For bundled items or products with smooth surfaces, the blocker helps maintain the bundle's integrity and prevents individual pieces from sliding out.
- Enhanced Containment: The stretch film secures both the product and the blocker together, creating a more stable and unified package.
Without this component, loads might telescope, shift end-to-end, or become unstable, leading to potential product damage or creating safety hazards during handling.
How the Wrapping Process Works
The operation typically follows these steps:
- Infeed: The product is placed onto the infeed conveyor system.
- Blocker Placement: Depending on the system's automation level, the timber blocker is manually or automatically positioned against one end (or sometimes both ends) of the product or bundle.
- Wrapping Cycle: The product and blocker move horizontally through the machine's wrapping ring or rotating film carriage. Stretch film is dispensed and wraps orbitally around the length of the product, securing the timber blocker firmly in place against the load.
- Outfeed: The fully wrapped and stabilized package exits the machine via the outfeed conveyor.
Key components facilitating this process include the conveyor system, the film carriage assembly (which holds and dispenses the stretch film), the timber blocker placement mechanism (if automated), and the machine's control panel for managing settings like wrap parameters and conveyor speed.
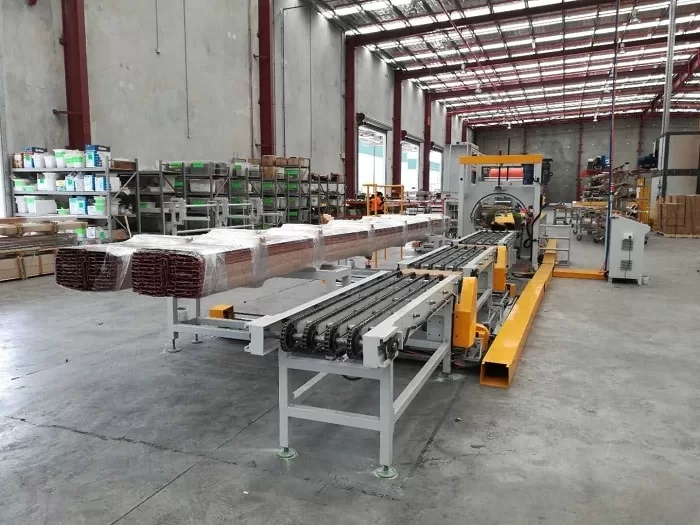
Common Applications and Suitable Products
Horizontal wrapping machines with timber blockers are frequently employed in industries such as:
- Lumber and Wood Products: Securing bundles of planks, beams, or engineered wood.
- Metal Extrusions: Wrapping aluminum or steel profiles, pipes, and tubing.
- Building Materials: Packaging doors, windows, panels, and siding.
- Textiles: Stabilizing large rolls or bolts of fabric.
- Furniture Components: Wrapping long sections or unassembled parts.
Benefits of Using Timber Blockers in Horizontal Wrapping
Integrating timber blockers offers tangible advantages:
- Enhanced Load Stability: Significantly reduces the risk of product shifting during transportation and handling.
- Reduced Product Damage: Minimizes impacts, abrasions, and deformations caused by internal movement within the wrap.
- Improved Handling Safety: Creates a more secure and predictable load, reducing risks for personnel and equipment during loading, unloading, and storage.
- Maintained Product Alignment: Keeps bundled items or components properly aligned within the package.
Considerations When Specifying a System
Choosing the right horizontal wrapping machine with a timber blocker requires careful evaluation of several factors:
- Load Dimensions and Weight: Ensure the machine's capacity and aperture size can accommodate the largest and heaviest products.
- Throughput Requirements: Match the machine's speed and automation level to production demands.
- Timber Blocker Integration: Determine the need for manual, semi-automatic, or fully automatic blocker placement. Consider the type, size, and material of the blocker required.
- Film Type and Specifications: Select a machine compatible with the desired stretch film characteristics (thickness, pre-stretch capabilities).
- Operating Environment: Consider space constraints, power requirements, and any harsh environmental conditions.
- Integration with Existing Lines: Assess compatibility if the wrapper needs to connect with upstream or downstream automation.
- Manufacturer Support and Reliability: Evaluate the supplier's reputation for service, parts availability, and technical expertise.
In summary, horizontal wrapping machines equipped with timber blockers provide a robust solution for stabilizing long, bulky, or shift-prone products. By effectively bracing the load before it's wrapped, these systems enhance package integrity, reduce damage, and improve safety throughout the supply chain. Careful consideration of application requirements and machine specifications is key to selecting the optimal system.